Why is the 5-in-1 servo-driven injection robot better than other injection robots?
2025/02/12 By Topstar
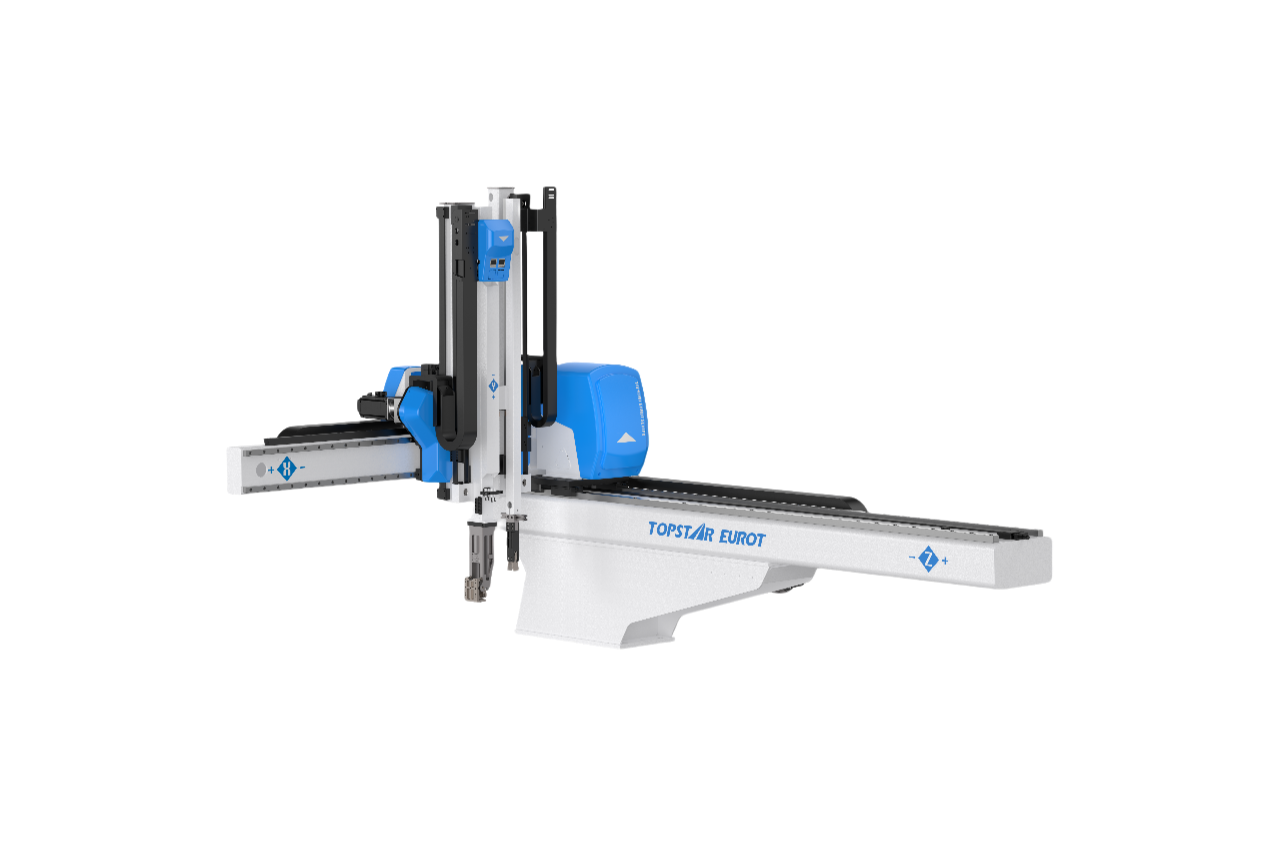
Injection robots simplify parts removal, sorting, and post-injection molding operations. However, not all injection molding robots are created equal. Traditional models often suffer from inefficiencies such as limited precision, high energy consumption, and rigid programming frameworks. Topstar’s 5-in-1 servo-driven injection robot is a breakthrough solution that redefines performance through advanced engineering and intelligent design. Integrating five servo motors into one servo drive and developing proprietary control algorithms provides unparalleled precision, energy efficiency, and adaptability. This article will analyze why this 5-in-1 servo-driven injection robot is superior to traditional injection robots, focusing on its technical advantages, operational flexibility, and practical impact on the production line.
The Power of 5-in-1 Servo Drives: Changing Injection Robot Precision
The heart of the Topstar injection robot is the 5-in-1 servo drive system. Unlike traditional robots that require separate servo drives for each axis, Topstar’s design integrates the control of five servo motors into a drive unit driven by only three CPU chips. This integration eliminates signal delays caused by communication between multiple drives, ensuring synchronized motion of all axes.
When removing parts, the end effector of the injection robot must move quickly and precisely to avoid damaging delicate molded parts. The 5-in-1 system can adjust speed, torque, and trajectory in real time to achieve positioning accuracy within ±0.1 mm. This level of accuracy is critical for industries such as medical device manufacturing, where minor deviations can render components unusable. In contrast, traditional robots with decentralized drives often experience lag or overshoot, resulting in higher scrap rates and downtime.
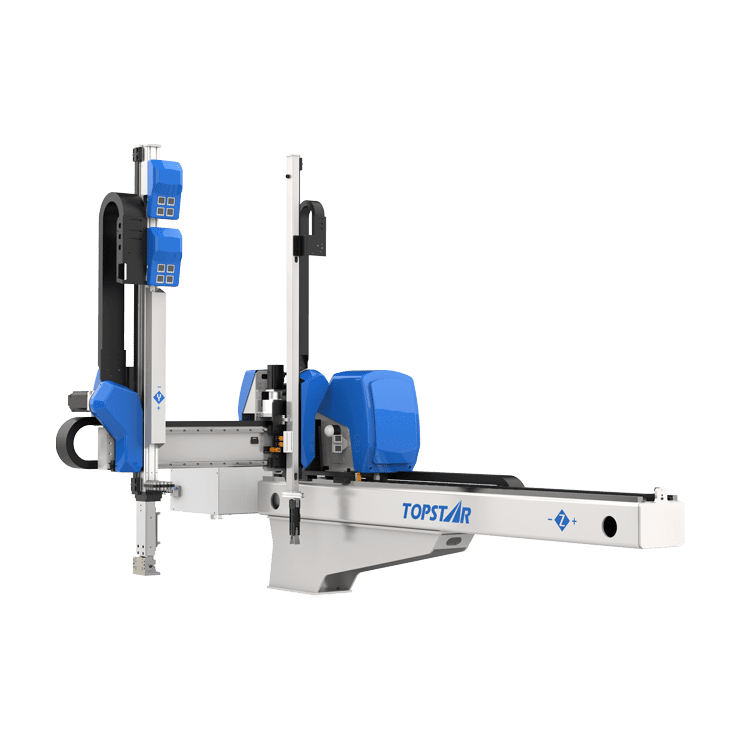
How does multi-axis standard bus design improve the energy efficiency of injection robot?
Energy consumption is the main pain point of injection robots when working, especially in large-scale production. Topstar solves this problem with its multi-axis standard bus design, which allows the regenerative energy of the decelerated axis to be redistributed to other motors in real-time. This approach can reduce total power consumption by up to 20% compared to traditional systems.
Imagine an injection robot executing a complex retrieval path: when one axis brakes, its kinetic energy is captured and reused to power another axis that accelerates in a different direction. This not only reduces electricity costs but also reduces heat generation and extends the life of servo components. For factories running multiple robots around the clock, the cumulative energy savings can save thousands of dollars annually, guaranteeing both environmental and cost-effectiveness.
Unlocking New Possibilities with Self-Developed Control Algorithms
Traditional injection robots often rely on preset, rigid programming, which limits adaptability. Topstar’s self-developed control system breaks this mold, providing an open architecture that enables operators to customize motion paths, servo parameters, and application logic. Using a handheld teach pendant, users can easily modify:
Trajectory: Create complex paths for challenging, complex part geometries such as arcs, diagonals, or irregular curves.
Speed Profile: Adjust acceleration/deceleration rates to prevent parts from deforming during high-speed retrieval.
Special Features: Program stacking, counting, or sampling without an external PLC.
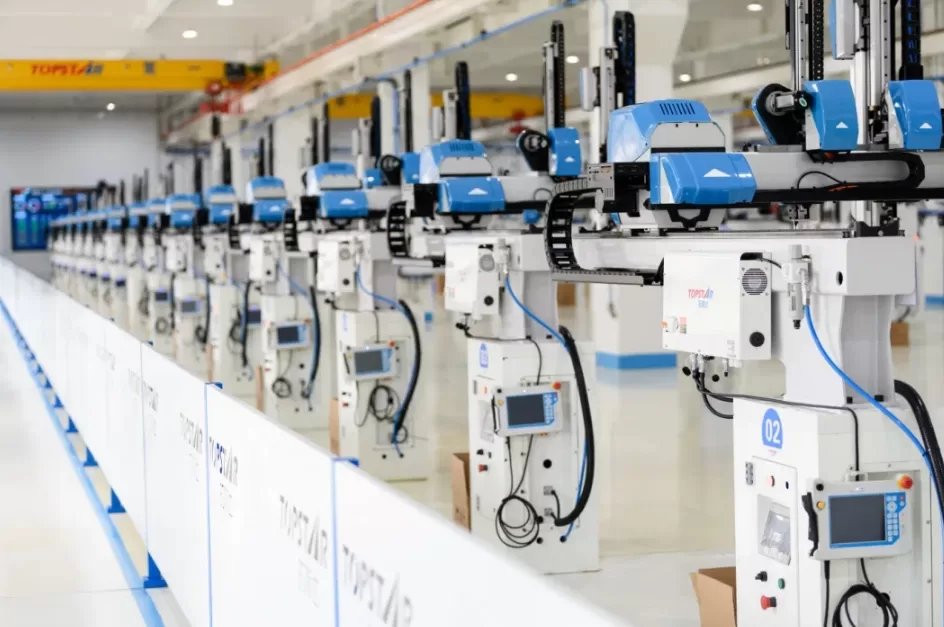
Why do Injection Robot excel at complex retrieval tasks?
Complex part geometries, such as threaded caps, multi-cavity molds, or components with sliding cores, require an injection molding robot capable of complex 3D motion. Topstar’s 5-in-1 servo system, combined with its motion algorithms, smoothly performs advanced operations such as:
Angled extraction: Retrieving parts at non-perpendicular angles to avoid interfering with mold features.
Contour following: Mirroring curved mold surfaces during ejection to minimize stress on delicate parts.
Multi-stage sorting: Combining pick, rotate, and place into one fluid motion.
One customer we work with, a toy manufacturer that makes figurines, has used these capabilities to implement a “zigzag” retrieval path, reducing cycle time by 15% while maintaining 99.9% part integrity.
Reduce downtime: The maintenance benefits of a simplified architecture.
Traditional injection robots have separate drives, cables, and controllers, creating multiple points of failure. Topstar’s 5-in-1 design reduces the number of components by 40%, resulting in fewer connections, and integrated wiring minimizes loose connectors or frayed cables. At the same time, unified diagnostics monitor all axes on a single interface to simplify troubleshooting. With a modular design, replacing a compact servo drive takes only minutes, while a multi-drive system takes hours. In addition, their predictive analytics function analyzes servo load trends and temperature data, and the system will flag potential problems weeks before failure. This proactive approach helps users reduce unplanned downtime by up to 30%.
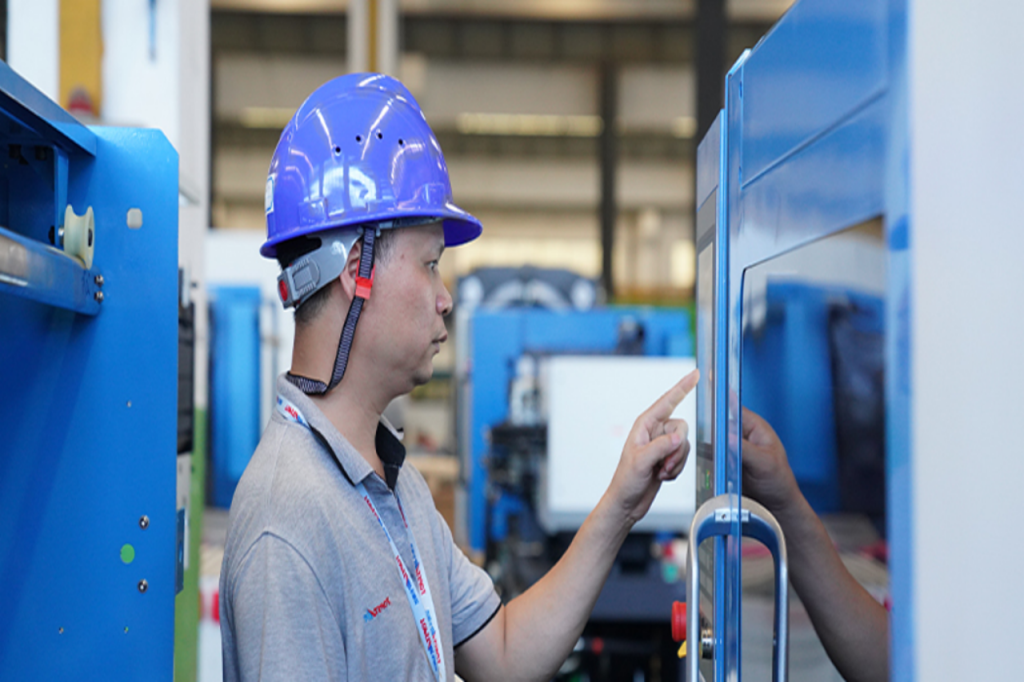
Redefining the precision and reliability of injection robots
Topstar’s 5-in-1 servo-driven injection robot is an incremental upgrade that solves traditional systems’ core challenges by combining precision engineering with intelligent control: energy waste, lack of flexibility, and high maintenance costs. Manufacturers who adopt this technology get more than just a robot; they need a versatile injection molding partner to unlock new efficiencies, adapt to design innovations, and cut operating expenses.
TRENDING POSTS
- What factors can cause delays in the injection molding process of plastic molding machine? 2025/02/12
- Exhibition Review| Topstar participates in InterPlas Thailand 2024 2025/02/12
- Star Case | Topstar helps Santong upgrade its intelligent plant 2025/02/12
- Topstar Special | National Science and Technology Workers Day 2025/02/12
HOT TOPIC
- 3 in 1 Compact Dehumidifying Dryer
- 5-axis CNC machine
- accuracy
- Air Chillers
- all electric injection molding machine
- all electric injection molding machines
- All-electric injection molding machines
- and overall production quality. Therefore
- AP-RubberPlas
- automated injection molding machine
- Automation changed engineering
- automation of injection molding robots
- auxiliary machine
- Bench Injection Molding Machine
- Cabinet dryer manufacturers
- Cabinet dryers
- chiller
- CNC Drilling Machine
- CNC Drilling Machines
- cnc engraving machine manufacturer
- cnc laser cutting machine manufacturer
- CNC machine
- CNC Machine Center
- CNC Machine for Sale
- CNC Machine Manufacturing
- CNC Machine Tool
- CNC machine tool product
- CNC Machining Center
- CNC wood carving machine
- Cooling system
- Cross-Walking Single Axis Servo Cylinder Robot
- Cross-Walking Single-Axis Servo Cylinder Robot
- Cross-Walking Three-Axis/Five-Axis Servo Driven Robot
- cross-walking three-axis/five-axis servo-driven robot
- Dehumidifier Dryer
- Dehumidifying Dryer
- delta parallel robot
- Desktop Injection Molding Machine
- Desktop injection molding machines
- Desktop Molding Machine
- desktop plastic injection machine
- Desktop Plastic Injection Molding Machine
- direct clamp injection molding machine
- Direct clamp injection molding machines
- Dosing & mixing system
- Drilling Centers
- Drying and dehumidification system
- drying and dehumidifying equipment
- Drying and Dehumidifying System
- drying system
- effective and efficient. Cabinet dryers are also used in other industries where large quantities of material need to be dried
- efficient injection molding machine
- elbow hydraulic injection molding machines
- electric injection molding machine
- electric injection molding machines
- energy-saving injection molding machine
- etc. Among injection molding robots
- exhibition
- features of CNC machine
- Feeding And Conveying System
- Five Axis Machine Center
- Fully automatic injection molding machine
- Gathering Topstar
- giant injection molding machine
- GMU-600 5-Axis Machining Center
- Granulating & Recycling System
- Heavy duty injection molding machine
- Honeycomb rotor dehumidifier
- horizontal injection molding machine
- Horizontal Injection Molding Machines
- Horizontal Injection Moulding Machine
- Horizontal Mixer manufacturer
- How The CNC Machine Works
- hybrid injection molding machine
- hydraulic injection molding machine
- Hydraulic Injection Molding Machines
- in this article
- Industrial robot
- Industrial Robot Chinese brand
- industrial robot parts
- industrial robot supplier
- Industrial robots
- Industry Chain
- Injection Manipulator
- injection mold machines
- Injection molding
- Injection molding automation
- Injection Molding Automation Solution
- injection molding dryer
- Injection molding equipment
- injection molding hopper dryer
- Injection molding machine
- injection molding machine brand
- Injection Molding Machine Factory
- Injection Molding Machine Manufacture
- Injection molding machine manufacturer
- injection molding machine manufacturers
- Injection molding machine procurement
- injection molding machine robotic arm
- injection molding machine with a robot
- Injection molding machines
- injection molding material dehumidifying
- injection molding plant
- Injection Molding Robot
- injection molding robot arm
- Injection molding robot automation
- Injection molding robotic arm
- injection molding robots
- Injection Moulding Robots
- Injection Robot
- Injection robot arm
- Injection robot manufacturer
- Injection robot wholesale
- injection robots
- intelligent injection molding machines
- Introducing Injection Robot
- It is the best choice for drying large quantities of material at once. Cabinetmakers use these machines because they are fast
- large injection molding machine
- Learn what industrial automation and robotics is
- low speed sound-proof granulator
- machine plastic molding
- make sure to add some! Improvements (2) Keyphrase in introduction: Your keyphrase or its synonyms appear in the first paragraph of the copy
- manipulator machine
- manufacturing
- micro injection molding machine
- middle speed granulator
- Mini CNC machine manufacturers.
- Mold Temperature Control System
- mold temperature controller
- molding material Dehumidifying System
- mould temperature controller
- mould temperature controllers
- New electric injection molding machine
- nitrogen dryer manufacturer
- nitrogen dryer system manufacturer
- Oil type mold temperature controller
- open day
- Outbound links: No outbound links appear in this page. Add some! Images: No images appear on this page. Add some! Internal links: No internal links appear in this page
- PET Preform injection molding
- phone case maker machine
- phone case making machine
- plastic bottle making machine
- plastic bottle manufacturing
- plastic bucket making machine
- plastic bucket manufacturing
- Plastic chair making machine
- plastic forming equipment
- plastic hopper dryer
- plastic injection machine
- plastic injection machines
- plastic injection molding
- Plastic injection molding equipment
- Plastic injection molding machine
- Plastic Injection Molding Machines
- plastic injection robot
- Plastic Molding machine
- Plastic Molding Machines
- plastic molding press
- plastic phone case making machine
- plastic-molding machine
- powerful granulator
- Powerful Type Sound-Proof Granulator
- production of plastic seats
- Robot injection molding
- robot injection molding machine
- robot manufacturing companies
- Robotic arm for injection molding machine
- robotic injection molding machines
- robotics in injection molding
- SCARA robot
- SCARA robots
- Service-oriented manufacturing
- Servo Cylinder Robot
- servo driven robot
- Servo Driven Robots
- servo injection robots
- Servo-Driven Robot
- Setup of injection machine
- Silicone Injection Molding Machine
- six-axis industrial robot
- Stainless Hopper Dryer
- Stainless Hopper Dryers
- star club
- swing arm robot
- the choice between servo-driven robots and hydraulic robots will have a certain impact on efficiency
- the most popular injection molding machine
- the type of injection molding robot
- toggle clamp injection molding machine
- Toggle Hydraulic Injection Molding Machines
- toggle injection molding machine
- Top 10 brands of injection robots
- Topstar
- Topstar Engineering
- Topstar Industrial Robots
- Topstar injection molding intelligent
- Topstar Scara Robots
- Useful Injection molding machine
- Vertical machining centers
- volumetric type blender
- water chiller
- water chillers
- water distributor
- Water Type MoldTemperature Controller
- We often face choices when performing injection molding. We will choose the type of injection molding machine
- wholesale of injection molding machines
- x carve CNC