Why do South American manufacturers favor high-precision plastic molding machines?
- High-precision electric molding machines
- high-precision plastic molding machines
- precision injection molding
2025/04/27 By Topstar
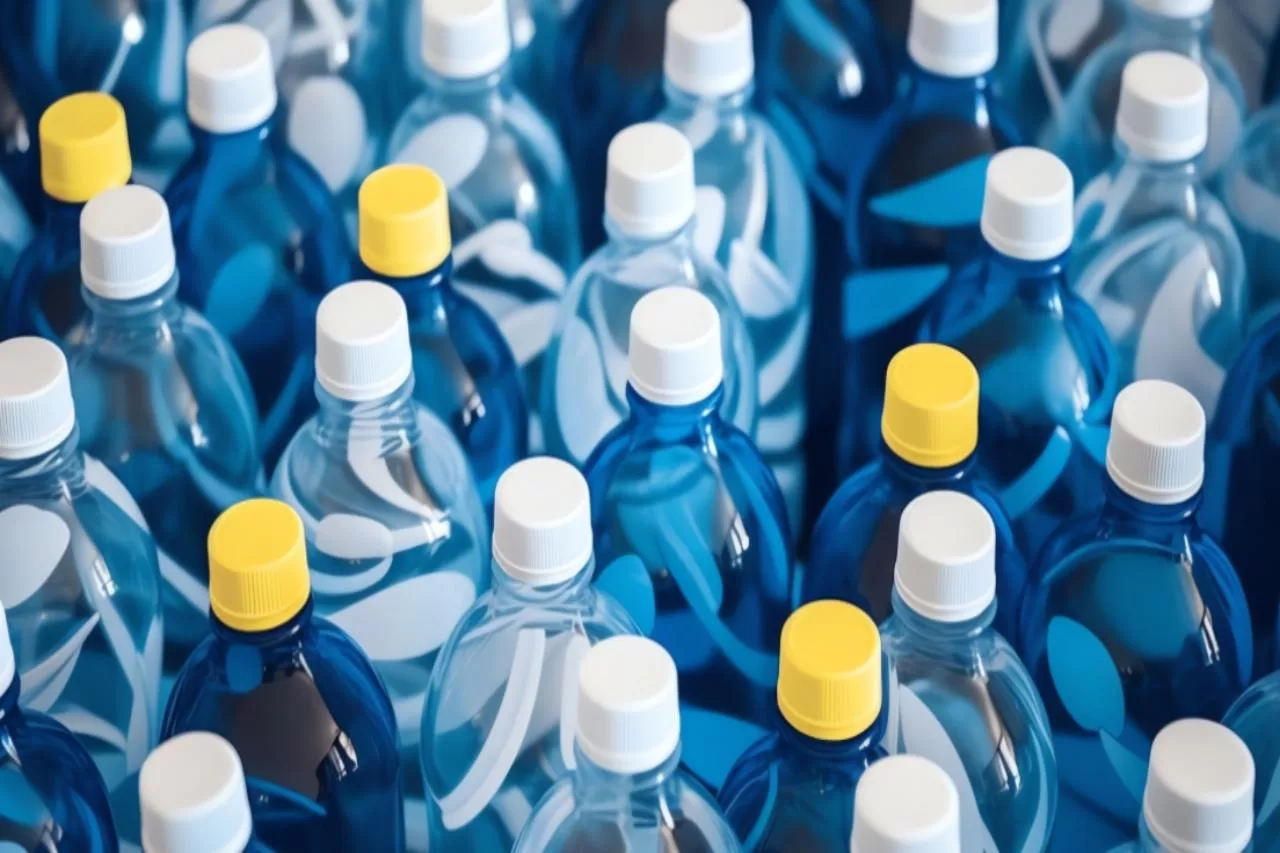
South America is experiencing a surge in demand for high-end consumer goods, from stylish electronics and home appliances to automotive interiors, medical devices and optics. These products require extremely high precision and perfect surface finish, which can only be reliably met by high-precision plastic molding machines. At the same time, local manufacturing companies are facing soaring labor, energy and raw material costs. To stay competitive, manufacturers are turning to advanced high-precision plastic molding machines to reduce waste, shorten production cycles and maximize uptime.
Meet consumer product quality expectations with high-precision plastic molding machines
Whether it is a smartphone casing or a shiny home appliance panel, the surface finish, dimensional accuracy and durability of plastic parts are now key purchasing factors. High-precision plastic molding machines, especially all-electric precision plastic molding machines, can provide repeatable consistency of each shot, creating a perfect surface without dents, warps or flow marks.
These machines use servo drives, discrete intelligent drives, and precise mold temperature control technology to maintain injection speed and pressure within one thousandth of a second. In precision molding presses, the injection speed profile can be dynamically adjusted to ensure that complex geometries are filled evenly without stress concentration. This feature reduces the scrap rate of parts from 8-10% in traditional presses to less than 1%, significantly saving materials and improving profitability.
Driving innovation in automotive parts
Major manufacturing centers in Brazil and Argentina support the South American automotive industry by producing not only economy cars but also mid-range and luxury models for export. These vehicles contain hundreds of plastic parts: headlight bezels, dashboards, door panels, and parts under the hood. The tolerances of these “invisible” plastic components are typically within ±0.01 mm.
To meet these stringent standards, Topstar equips high-precision plastic molding machine with discrete intelligent drives, independent injection units, low-damping shooting tables, and dynamic mold linear guides. Operators can adjust these machines in real time under a unified control system to compensate for changes in thermoplastic viscosity caused by batch-to-batch material differences or fluctuations in workshop ambient temperature. In addition, the integrated chiller and mold temperature controller can shorten the production cycle (usually by 15-20%) without sacrificing precision, thus creating a strong production line of high-quality automotive plastic parts that meet strict durability, aesthetics and safety requirements.
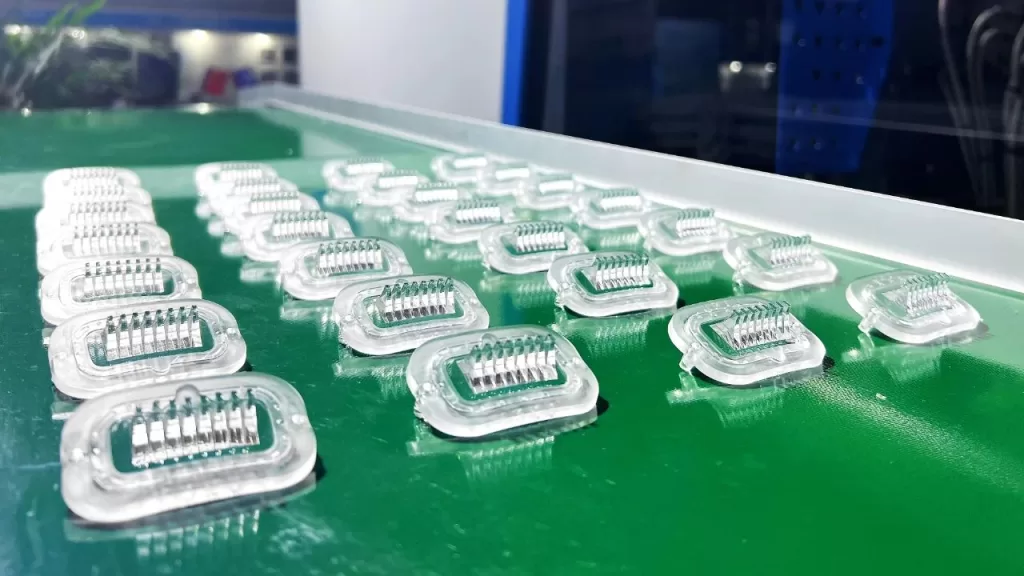
Empowering medical device manufacturing
In South America’s expanding medical industry, driven by increased healthcare investment and local equipment assembly, manufacturers must be able to produce complex microfluidic channels or ultra-clear lens arrays without burrs, particle contamination or structural defects. Due to the special characteristics of medical products being sterile and clean, the production environment must be a dust-free workshop. To adapt to the requirements of the dust-free workshop, South American manufacturers use high-precision electric molding machines that allow configuring minimum hydraulic pressure, reducing the risk of oil leakage. They also use special grease lubrication, which remains pollution-free to the environment. Additionally, they design the second plate and guide column to be contactless, eliminating the need for separate lubrication and ensuring the cleanliness of the mold area.
High-precision electric molding machines not only take into account the hard indicators of the dust-free workshop and the needs of South American manufacturers for precision injection molding of products, but also have significant effects in energy saving and cost reduction. In terms of improving efficiency, they have high precision, stable equipment, and production efficiency has increased by about 10% compared with the past. In terms of technical operation, high intelligence, a simple operation interface, and easy operation by workshop technicians effectively reduce the labor cost of the enterprise.
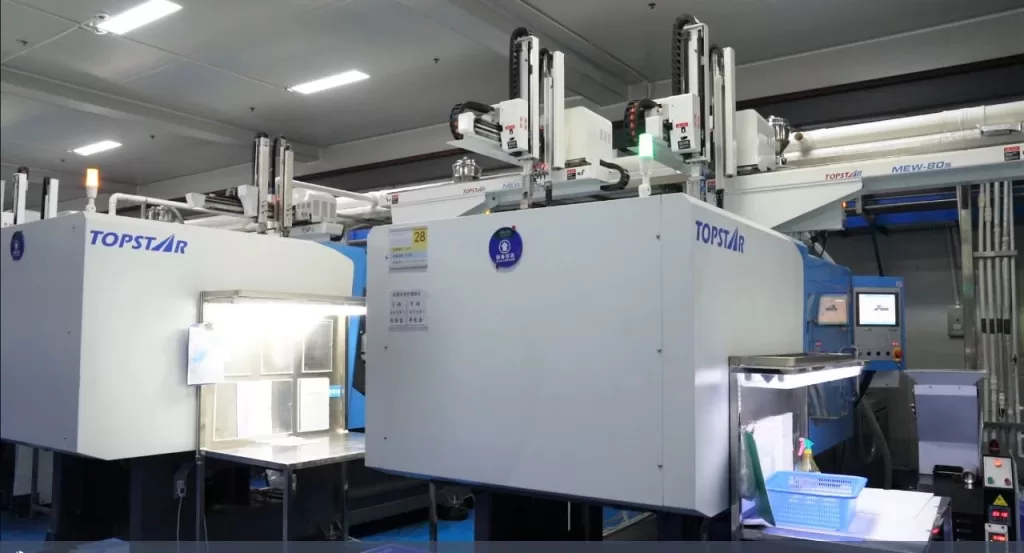
Improve efficiency and reduce operating costs through high-precision plastic molding machines
High precision not only means higher quality, but also lower unit cost. In South America, electricity and labor costs can be quite high, and optimizing machine efficiency is critical for them. On Topstar’s all-electric injection molding machine, the integration of auxiliary machines and automated control can be achieved through discrete intelligent drive and integrated control under a unified control system, thereby greatly improving the efficiency of the production cycle. Precise control of screw speed, back pressure, and mold opening and closing sequence can minimize molding cycles and reduce material waste. By achieving faster injection to ejection cycles, South American manufacturers can increase annual production by 30% to 50% on the same floor space. At the same time, excellent injection consistency reduces the scrap rate, saves thousands of dollars in raw material costs each month, and extends maintenance intervals.
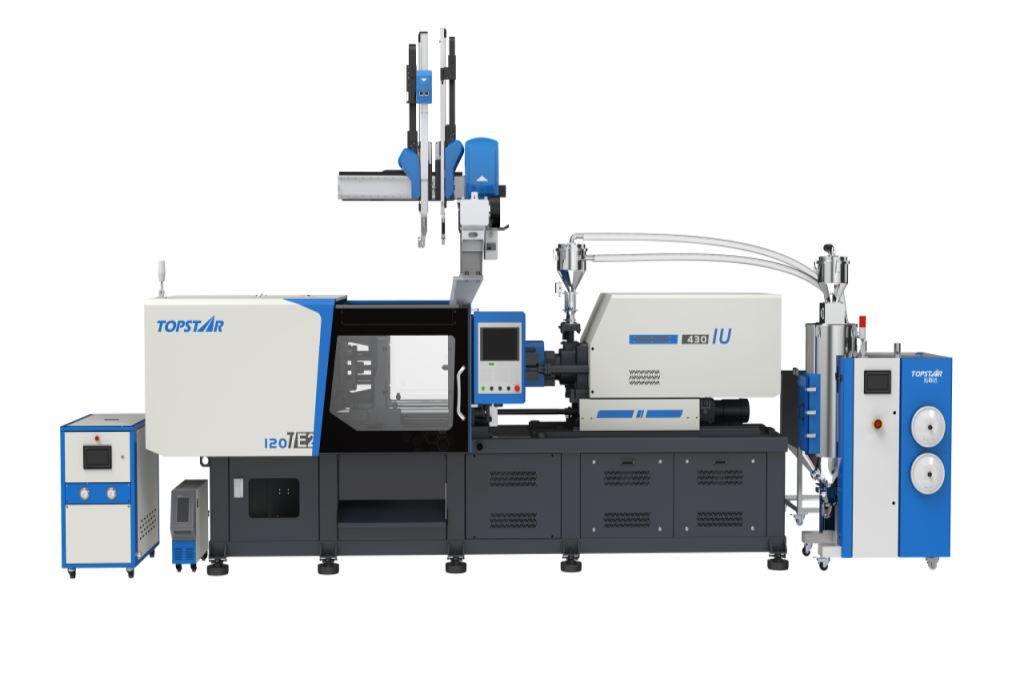
Maintaining a competitive advantage
The growing demand for high-precision plastic molding machines among South American manufacturers is mainly due to strict product quality requirements, the expanding automotive and medical industries, and rising operating costs. From intelligent servo-driven precision plastic molding machines to electric drive integrated platforms, these technologies enable local producers to meet global standards – reducing scrap, lowering energy consumption and increasing output to meet high-precision needs.
TRENDING POSTS
- What factors can cause delays in the injection molding process of plastic molding machine? 2025/04/27
- Exhibition Review| Topstar participates in InterPlas Thailand 2024 2025/04/27
- Star Case | Topstar helps Santong upgrade its intelligent plant 2025/04/27
- Topstar Special | National Science and Technology Workers Day 2025/04/27
HOT TOPIC
- 3 in 1 Compact Dehumidifying Dryer
- 5-axis CNC machine
- accuracy
- Air Chillers
- all electric injection molding machine
- all electric injection molding machines
- All-electric injection molding machines
- and overall production quality. Therefore
- AP-RubberPlas
- automated injection molding machine
- Automation changed engineering
- automation of injection molding robots
- auxiliary machine
- Bench Injection Molding Machine
- Cabinet dryer manufacturers
- Cabinet dryers
- chiller
- CNC Drilling Machine
- CNC Drilling Machines
- cnc engraving machine manufacturer
- cnc laser cutting machine manufacturer
- CNC machine
- CNC Machine Center
- CNC Machine for Sale
- CNC Machine Manufacturing
- CNC Machine Tool
- CNC machine tool product
- CNC Machining Center
- CNC wood carving machine
- Cooling system
- Cross-Walking Single Axis Servo Cylinder Robot
- Cross-Walking Single-Axis Servo Cylinder Robot
- Cross-Walking Three-Axis/Five-Axis Servo Driven Robot
- cross-walking three-axis/five-axis servo-driven robot
- Dehumidifier Dryer
- Dehumidifying Dryer
- delta parallel robot
- Desktop Injection Molding Machine
- Desktop injection molding machines
- Desktop Molding Machine
- desktop plastic injection machine
- Desktop Plastic Injection Molding Machine
- direct clamp injection molding machine
- Direct clamp injection molding machines
- Dosing & mixing system
- Drilling Centers
- Drying and dehumidification system
- drying and dehumidifying equipment
- Drying and Dehumidifying System
- drying system
- effective and efficient. Cabinet dryers are also used in other industries where large quantities of material need to be dried
- efficient injection molding machine
- elbow hydraulic injection molding machines
- electric injection molding machine
- electric injection molding machines
- energy-saving injection molding machine
- etc. Among injection molding robots
- exhibition
- features of CNC machine
- Feeding And Conveying System
- Five Axis Machine Center
- Fully automatic injection molding machine
- Gathering Topstar
- giant injection molding machine
- GMU-600 5-Axis Machining Center
- Granulating & Recycling System
- Heavy duty injection molding machine
- High-precision electric molding machines
- high-precision plastic molding machines
- Honeycomb rotor dehumidifier
- horizontal injection molding machine
- Horizontal Injection Molding Machines
- Horizontal Injection Moulding Machine
- Horizontal Mixer manufacturer
- How The CNC Machine Works
- hybrid injection molding machine
- hydraulic injection molding machine
- Hydraulic Injection Molding Machines
- in this article
- Industrial robot
- Industrial Robot Chinese brand
- industrial robot parts
- industrial robot supplier
- Industrial robots
- Industry Chain
- Injection Manipulator
- injection manipulator robot
- injection mold machines
- Injection molding
- Injection molding automation
- Injection Molding Automation Solution
- injection molding dryer
- Injection molding equipment
- injection molding hopper dryer
- Injection molding machine
- injection molding machine brand
- Injection Molding Machine Factory
- Injection Molding Machine Manufacture
- Injection molding machine manufacturer
- injection molding machine manufacturers
- Injection molding machine procurement
- injection molding machine robotic arm
- injection molding machine with a robot
- Injection molding machines
- injection molding material dehumidifying
- injection molding plant
- Injection Molding Robot
- injection molding robot arm
- Injection molding robot automation
- Injection molding robotic arm
- injection molding robots
- Injection Moulding Robots
- Injection Robot
- Injection robot arm
- Injection robot manufacturer
- Injection robot wholesale
- injection robots
- intelligent injection molding machines
- Introducing Injection Robot
- It is the best choice for drying large quantities of material at once. Cabinetmakers use these machines because they are fast
- large injection molding machine
- Learn what industrial automation and robotics is
- linear robot
- low speed sound-proof granulator
- machine plastic molding
- make sure to add some! Improvements (2) Keyphrase in introduction: Your keyphrase or its synonyms appear in the first paragraph of the copy
- manipulator machine
- manufacturing
- micro injection molding machine
- middle speed granulator
- Mini CNC machine manufacturers.
- Mold Temperature Control System
- mold temperature controller
- molding material Dehumidifying System
- mould temperature controller
- mould temperature controllers
- New electric injection molding machine
- nitrogen dryer manufacturer
- nitrogen dryer system manufacturer
- Oil type mold temperature controller
- open day
- Outbound links: No outbound links appear in this page. Add some! Images: No images appear on this page. Add some! Internal links: No internal links appear in this page
- PET Preform injection molding
- phone case maker machine
- phone case making machine
- plastic bottle making machine
- plastic bottle manufacturing
- plastic bucket making machine
- plastic bucket manufacturing
- Plastic chair making machine
- plastic forming equipment
- plastic hopper dryer
- plastic injection machine
- plastic injection machines
- plastic injection molding
- Plastic injection molding equipment
- Plastic injection molding machine
- Plastic Injection Molding Machines
- plastic injection robot
- Plastic Molding machine
- Plastic Molding Machines
- plastic molding press
- plastic phone case making machine
- plastic-molding machine
- powerful granulator
- Powerful Type Sound-Proof Granulator
- precision injection molding
- production of plastic seats
- Robot injection molding
- robot injection molding machine
- robot manufacturing companies
- Robotic arm for injection molding machine
- robotic injection molding machines
- robotics in injection molding
- SCARA robot
- SCARA robots
- Service-oriented manufacturing
- Servo Cylinder Robot
- servo driven robot
- Servo Driven Robots
- servo injection robots
- Servo-Driven Robot
- Setup of injection machine
- Silicone Injection Molding Machine
- six-axis industrial robot
- Stainless Hopper Dryer
- Stainless Hopper Dryers
- star club
- swing arm robot
- the choice between servo-driven robots and hydraulic robots will have a certain impact on efficiency
- the most popular injection molding machine
- the type of injection molding robot
- toggle clamp injection molding machine
- Toggle Hydraulic Injection Molding Machines
- toggle injection molding machine
- Top 10 brands of injection robots
- Topstar
- Topstar Engineering
- Topstar Industrial Robots
- Topstar injection molding intelligent
- Topstar Scara Robots
- Useful Injection molding machine
- Vertical machining centers
- volumetric type blender
- water chiller
- water chillers
- water distributor
- Water Type MoldTemperature Controller
- We often face choices when performing injection molding. We will choose the type of injection molding machine
- wholesale of injection molding machines
- x carve CNC