What machines can be used for plastic bucket manufacturing?
2024/07/15 By Topstar
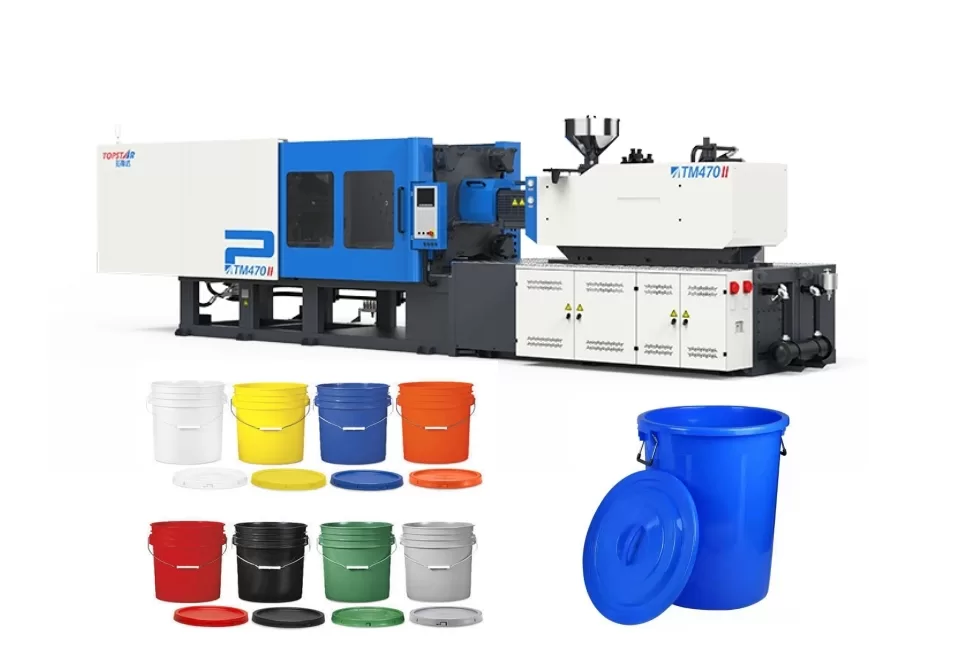
High-quality plastic barrels are often used in various industries, such as food storage and chemical transportation. For manufacturers of plastic barrels, the right equipment can ensure the durability, functionality and overall quality of the barrels produced. As an expert in the field of injection molding, in this guide, we will guide you through the different injection molding machines used in plastic bucket manufacturing. This will give you a comprehensive understanding of what to look for when looking for a plastic bucket manufacturing machine.
Injection molding machines for plastic bucket manufacturing
Injection molding machines are one of the most commonly used equipment for injection molding, and many plastic bucket manufacturers also use them for injection molding. They can mold complex, dimensional, or dense plastic products with metal inserts in one go. In plastic barrel manufacturing, these machines use a high-pressure injection process to mold plastic into the required bucket shape. They can be precise and efficient and produce large quantities of uniform products. Their key components include injection units, molds, clamping units and control systems. For plastic bucket manufacturing, machines with high clamping forces, fast cycle times and solid manufacturing quality can better handle the typical thick walls and large sizes of barrels.
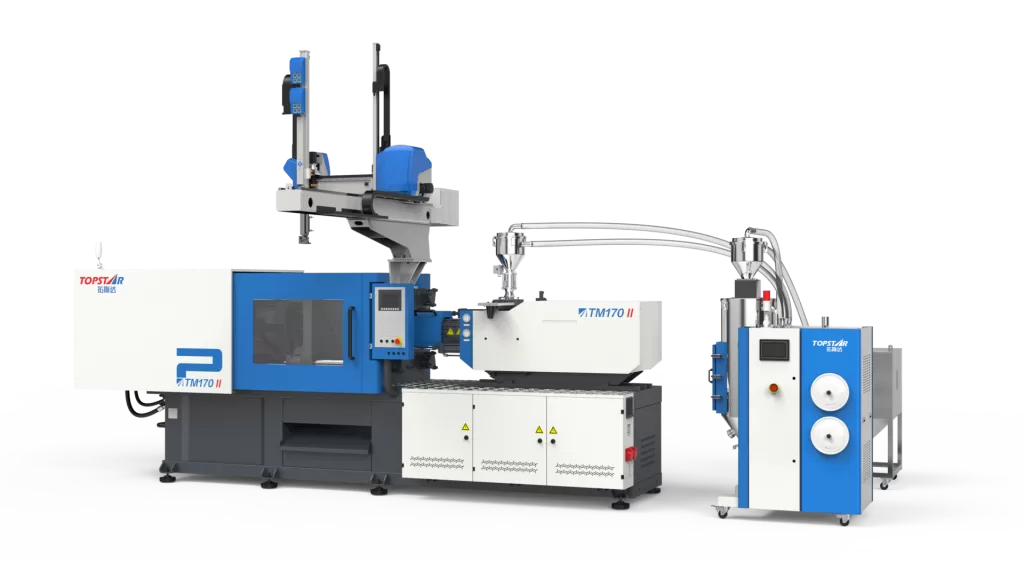
The role of blow molding machines in plastic bucket manufacturing
While injection molding is the most common method, some people also use blow molding machines for manufacturing. Blow molding is a process in which heated plastic is formed into a parison or preform and then inflated inside a mold to create the desired shape. It is divided into several types, including extrusion blow molding, injection blow molding, and stretch blow molding. For plastic buckets, extrusion blow molding is the most common method.
In extrusion blow molding, the plastic resin is melted and extruded into a hollow tube (parison). This parison is then enclosed in a split mold. Compressed air is blown into the parison, causing it to expand and conform to the internal shape of the mold. Once the plastic cools and solidifies, the mold opens, and the newly formed barrel is ejected. This method is suitable for larger barrels and can be completed with excellent strength and uniform wall thickness. On the other hand, injection blow molding is ideal for smaller, more complex barrel designs.
Advantages of using a hydraulic injection molding machine
Hydraulic injection molding machines usually have high clamping forces, which is essential for manufacturing large, thick-walled plastic barrels. Their sturdy clamping system ensures that the mold halves remain tightly closed during the injection process, preventing burrs and ensuring precise molding. This stability allows the production of plastic barrels that can withstand heavy loads and rough handling without compromising structural integrity. In addition, they are able to process a wide range of plastic materials. This versatility allows manufacturers to select the most suitable plastic barrel material based on the required characteristics, such as chemical resistance, strength and durability. The whole hydraulic injection molding machine also has a one-button automatic precision mold adjustment function.
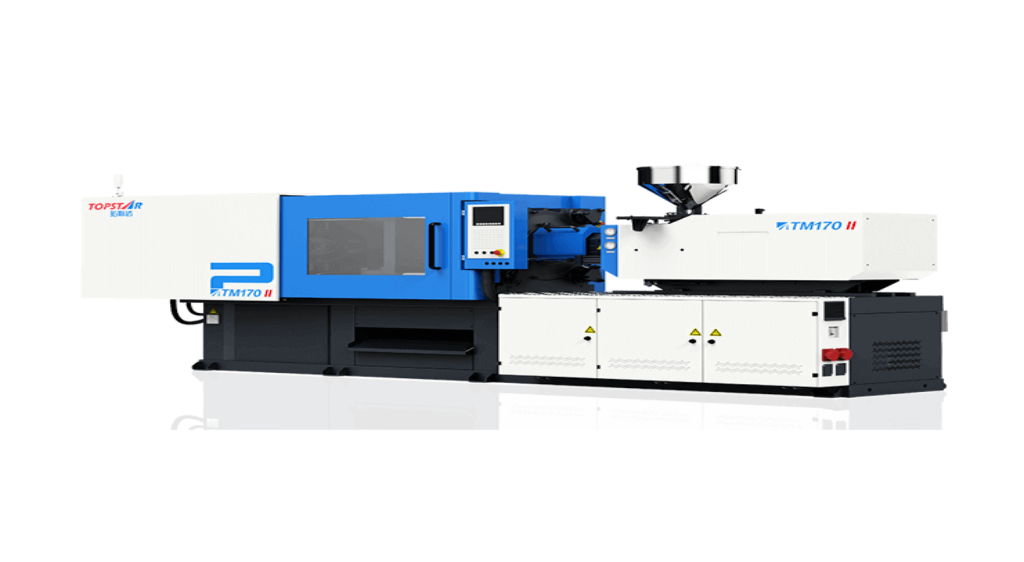
Advantages of using electric injection molding machines
Unlike hydraulic presses, electric injection molding machines use servo motors to drive the injection molding process and use intelligent electric mold opening and closing technology, which can more accurately control injection molding parameters, thereby improving accuracy and repeatability. They can provide faster cycle times and lower energy consumption. Unlike hydraulic presses that run continuously, they only consume energy when necessary. The use of servo motors dramatically reduces energy consumption, thereby reducing operating costs. At the same time, their cycle times are faster. Precise control of the injection, clamping and ejection processes enables faster and more efficient production cycles. For some plastic buckets used in specific environments, it can also ensure their cleanliness.

What is the difference in price?
Compared to injection molding machines, blow molding machines are usually less expensive. This is because the blow molding process requires a more straightforward design with fewer moving parts. Injection molding machines are more costly due to their complexity and the high precision needed for the process. Factors that affect their prices include machine size, clamping force, precision, and additional features such as automation and control systems.
In terms of mold prices, blow molding molds are usually cheaper than injection molds. Injection molding requires more complex and expensive molds because the process requires high precision. It also depends on the complexity and size of the parts being produced. From the production side, blow molding is efficient for the mass production of hollow parts. Injection molding is an efficient method suitable for making large quantities of high-precision plastics.
Improve your plastic barrel manufacturing capabilities
The choice of equipment determines the success of plastic bucket manufacturing. Understanding the advantages and capabilities of injection molding machines, blow molding machines, hydraulics, and electric motors allows you to make informed decisions that meet your production goals. By selecting the right equipment and combining it with auxiliary equipment, you can improve the efficiency, quality, and cost-effectiveness of your manufacturing process.
TRENDING POSTS
- What factors can cause delays in the injection molding process of plastic molding machine? 2024/07/15
- Exhibition Review| Topstar participates in InterPlas Thailand 2024 2024/07/15
- Star Case | Topstar helps Santong upgrade its intelligent plant 2024/07/15
- Topstar Special | National Science and Technology Workers Day 2024/07/15
HOT TOPIC
- .ervo motor-driven linear robots
- 1.0 guangdong topstar technology co. ltd
- 1.0 topstar china
- 1.0 topstar robot
- 11
- 2
- 21
- 23
- 3 axis robot
- 3 axis robots
- 3 in 1 Compact Dehumidifying Dryer
- 3-axis robot
- 3-axis robots
- 39
- 41
- 5-axis CNC machine
- 62
- accuracy
- Air Chillers
- all electric injection molding machine
- all electric injection molding machines
- All-electric injection molding machines
- and overall production quality. Therefore
- AP-RubberPlas
- automated injection molding machine
- Automation changed engineering
- automation of injection molding robots
- auxiliary machine
- Bench Injection Molding Machine
- Cabinet dryer manufacturers
- Cabinet dryers
- chiller
- CNC Drilling Machine
- CNC Drilling Machines
- cnc engraving machine manufacturer
- cnc laser cutting machine manufacturer
- CNC machine
- CNC Machine Center
- CNC Machine for Sale
- CNC Machine Manufacturing
- CNC Machine Tool
- CNC machine tool product
- CNC Machining Center
- CNC wood carving machine
- Cooling system
- Cross-Walking Single Axis Servo Cylinder Robot
- Cross-Walking Single-Axis Servo Cylinder Robot
- Cross-Walking Three-Axis/Five-Axis Servo Driven Robot
- cross-walking three-axis/five-axis servo-driven robot
- Dehumidifier Dryer
- Dehumidifying Dryer
- delta parallel robot
- Desktop Injection Molding Machine
- Desktop injection molding machines
- Desktop Molding Machine
- desktop plastic injection machine
- Desktop Plastic Injection Molding Machine
- direct clamp injection molding machine
- Direct clamp injection molding machines
- Dosing & mixing system
- Drilling Centers
- Drying and dehumidification system
- drying and dehumidifying equipment
- Drying and Dehumidifying System
- drying system
- effective and efficient. Cabinet dryers are also used in other industries where large quantities of material need to be dried
- efficient injection molding machine
- elbow hydraulic injection molding machines
- electric injection molding machine
- electric injection molding machines
- energy-efficient injection molding robot
- energy-saving injection molding machine
- etc. Among injection molding robots
- exhibition
- features of CNC machine
- Feeding And Conveying System
- Five Axis Machine Center
- Fully automatic injection molding machine
- Gathering Topstar
- giant injection molding machine
- GMU-600 5-Axis Machining Center
- Granulating & Recycling System
- Heavy duty injection molding machine
- High-precision electric molding machines
- high-precision plastic molding machines
- high-speed all electric injection molding machine
- Honeycomb rotor dehumidifier
- horizontal injection molding machine
- Horizontal Injection Molding Machines
- Horizontal Injection Moulding Machine
- Horizontal Mixer manufacturer
- How The CNC Machine Works
- hybrid injection molding machine
- hydraulic injection molding machine
- Hydraulic Injection Molding Machines
- in this article
- Industrial robot
- Industrial Robot Chinese brand
- industrial robot parts
- industrial robot supplier
- Industrial robots
- Industry Chain
- Injection Manipulator
- injection manipulator robot
- injection mold machines
- Injection molding
- Injection molding automation
- Injection Molding Automation Solution
- injection molding dryer
- Injection molding equipment
- injection molding hopper dryer
- Injection molding machine
- injection molding machine brand
- Injection Molding Machine Factory
- Injection Molding Machine Manufacture
- Injection molding machine manufacturer
- injection molding machine manufacturers
- Injection molding machine procurement
- injection molding machine robotic arm
- injection molding machine with a robot
- Injection molding machines
- injection molding material dehumidifying
- injection molding plant
- Injection Molding Robot
- injection molding robot arm
- Injection molding robot automation
- Injection molding robotic arm
- injection molding robots
- Injection moulding machine
- Injection Moulding Robots
- Injection Robot
- Injection robot arm
- Injection robot manufacturer
- Injection robot wholesale
- injection robots
- intelligent injection molding machines
- Introducing Injection Robot
- It is the best choice for drying large quantities of material at once. Cabinetmakers use these machines because they are fast
- large injection molding machine
- large injection molding machines
- Learn what industrial automation and robotics is
- linear robot
- linear robots
- low speed sound-proof granulator
- machine plastic molding
- make sure to add some! Improvements (2) Keyphrase in introduction: Your keyphrase or its synonyms appear in the first paragraph of the copy
- manipulator machine
- manufacturing
- medical grade injection molding machines
- medical injection molding machine
- medical injection molding machines
- micro injection molding machine
- middle speed granulator
- Mini CNC machine manufacturers.
- Mold Temperature Control System
- mold temperature controller
- mold temperature controllers
- molding material Dehumidifying System
- mould temperature control system
- mould temperature controller
- mould temperature controllers
- New electric injection molding machine
- nitrogen dryer manufacturer
- nitrogen dryer system manufacturer
- Oil type mold temperature controller
- Oil type mold temperature controllers
- open day
- Outbound links: No outbound links appear in this page. Add some! Images: No images appear on this page. Add some! Internal links: No internal links appear in this page
- PET Preform injection molding
- phone case maker machine
- phone case making machine
- plastic bottle making machine
- plastic bottle manufacturing
- plastic bucket making machine
- plastic bucket manufacturing
- Plastic chair making machine
- plastic forming equipment
- plastic hopper dryer
- plastic injection machine
- plastic injection machines
- plastic injection molding
- Plastic injection molding equipment
- Plastic injection molding machine
- Plastic Injection Molding Machines
- plastic injection moulding machine
- plastic injection robot
- Plastic Molding machine
- Plastic Molding Machines
- plastic molding press
- plastic moulding machine
- plastic phone case making machine
- plastic-molding machine
- powerful granulator
- Powerful Type Sound-Proof Granulator
- precision injection molding
- precision injection molding machines
- production of plastic seats
- pure water mould temperature controller
- Robot injection molding
- robot injection molding machine
- robot manufacturing companies
- Robotic arm for injection molding machine
- robotic injection molding machines
- robotics in injection molding
- SCARA robot
- SCARA robots
- Service-oriented manufacturing
- Servo Cylinder Robot
- servo driven robot
- Servo Driven Robots
- servo injection robots
- servo motor-driven linear robots
- servo-driven 3-axis robot
- Servo-Driven Robot
- Setup of injection machine
- Silicone Injection Molding Machine
- six-axis industrial robot
- Stainless Hopper Dryer
- Stainless Hopper Dryers
- star club
- swing arm robot
- take-out robots
- the choice between servo-driven robots and hydraulic robots will have a certain impact on efficiency
- the most popular injection molding machine
- the type of injection molding robot
- toggle clamp injection molding machine
- Toggle Hydraulic Injection Molding Machines
- toggle injection molding machine
- Top 10 brands of injection robots
- Topstar
- Topstar Engineering
- Topstar Industrial Robots
- Topstar injection molding intelligent
- Topstar Scara Robots
- Useful Injection molding machine
- Vertical machining centers
- volumetric type blender
- water chiller
- water chillers
- water distributor
- water type mold temperature controller
- Water Type MoldTemperature Controller
- Water-Type Mould Temperature Controllers
- We often face choices when performing injection molding. We will choose the type of injection molding machine
- wholesale of injection molding machines
- x carve CNC
- 热门查询 点击次数 展示 排名 topstar