What is the role of proportional back pressure in Topstar’s plastic injection molding machines?
2024/09/23 By Topstar
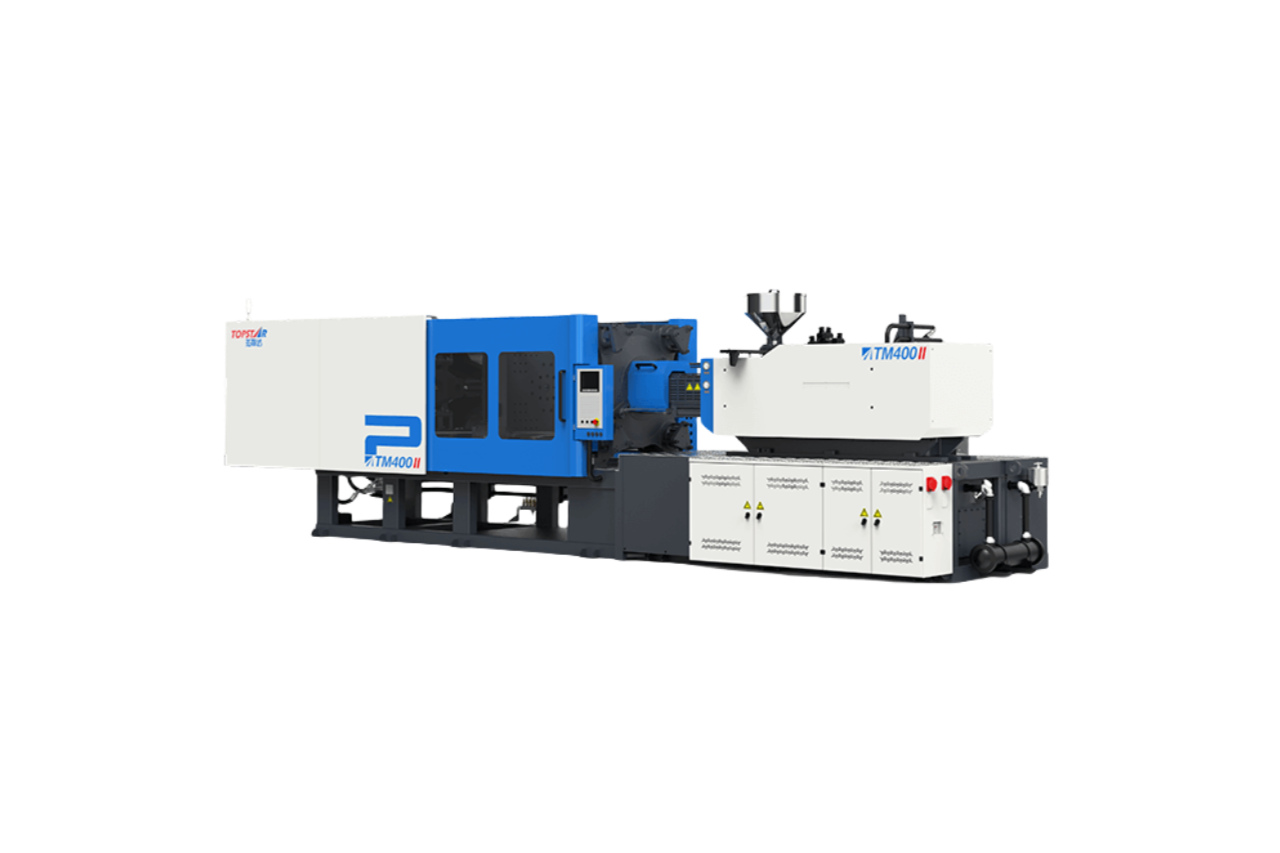
Managing the pressure applied during the injection molding process is one of the most critical factors in ensuring stable production. Automotive parts, medical, electronics, and other fields rely on the stability and flexibility provided by plastic injection molding machines to meet different production needs. A key feature of proportional back pressure is used in Topstar’s plastic injection molding machines, vital in controlling material flow and ensuring the best part quality. In this blog post, we will share the role of proportional back pressure in plastic injection molding machines and injection molding.
Proportional Back Pressure in Topstar Plastic Injection Molding Machines
Proportional back pressure plays a crucial role in plastic injection molding machines, affecting how the machine handles molten plastic during injection and molding. In simple terms, back pressure refers to the backward thrust of the material on the screw when the injection molding machine is molten. Due to the rotation of the screw, the material is pushed to accumulate in the front section of the screw. The injection cylinder is used to control the pressure of the screw retreat. Proper back pressure control ensures that the material is evenly melted, mixed, and distributed during the injection molding. Proportional back pressure allows the machine to apply different pressure levels according to the specific requirements of the plastic material and part design.
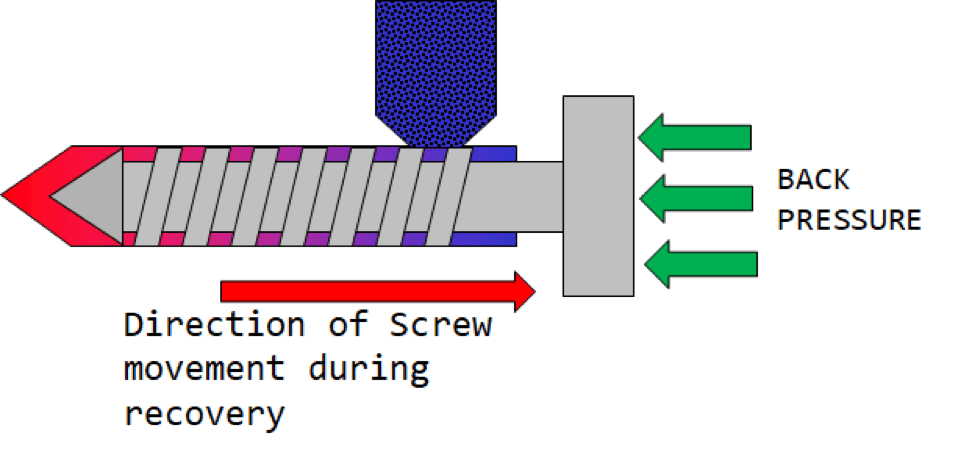
In Topstar’s injection molding machines, a servo system controls proportional back pressure, allowing precise adjustments at different stages of the injection cycle. This level of control can help manufacturers achieve more consistent product quality. Fine-tuning back pressure settings can improve the overall performance of the molding process and reduce waste.
Ensure Material Uniformity with Proportional Backpressure
One of the most critical roles proportional backpressure plays in a plastic injection molding machine is to ensure material uniformity. The machine must thoroughly mix the plastic pellets as they melt inside the barrel to achieve a consistent material composition.
Any inconsistencies in the material can result in defects in the final product. Proportional backpressure helps prevent these problems by maintaining a constant pressure on the molten plastic, forcing it to flow evenly through the screw and barrel. As the screw rotates, it melts the plastic and pushes it forward while mixing it. Proportional back pressure ensures the screw encounters resistance, thoroughly mixing the molten plastic. This results in a uniform material composition, ensuring that each part produced has the same structural and high-quality quality.
Improve Dimensional Accuracy with Proportional Backpressure on Plastic Injection Molding Machines
Whether manufacturing small parts for electronic devices or large parts for the automotive industry, you must ensure that each part meets precise dimensional specifications. Plastic injection molding machines with proportional backpressure allow manufacturers to control the flow and holding pressure of the molten material, which directly affects the part’s final dimensions. Proportional back pressure plays a vital role in maintaining the compression and holding of the plastic material within the mold. During the holding phase, as the molten plastic fills the mold cavity, the machine applies additional pressure to hold the material entirely and prevent it from shrinking or deforming as it cools. By maintaining consistent pressure throughout the entire phase, Topstar’s plastic injection molding machines help minimize variations in part dimensions, resulting in more accurate and consistent parts from one cycle to the next.
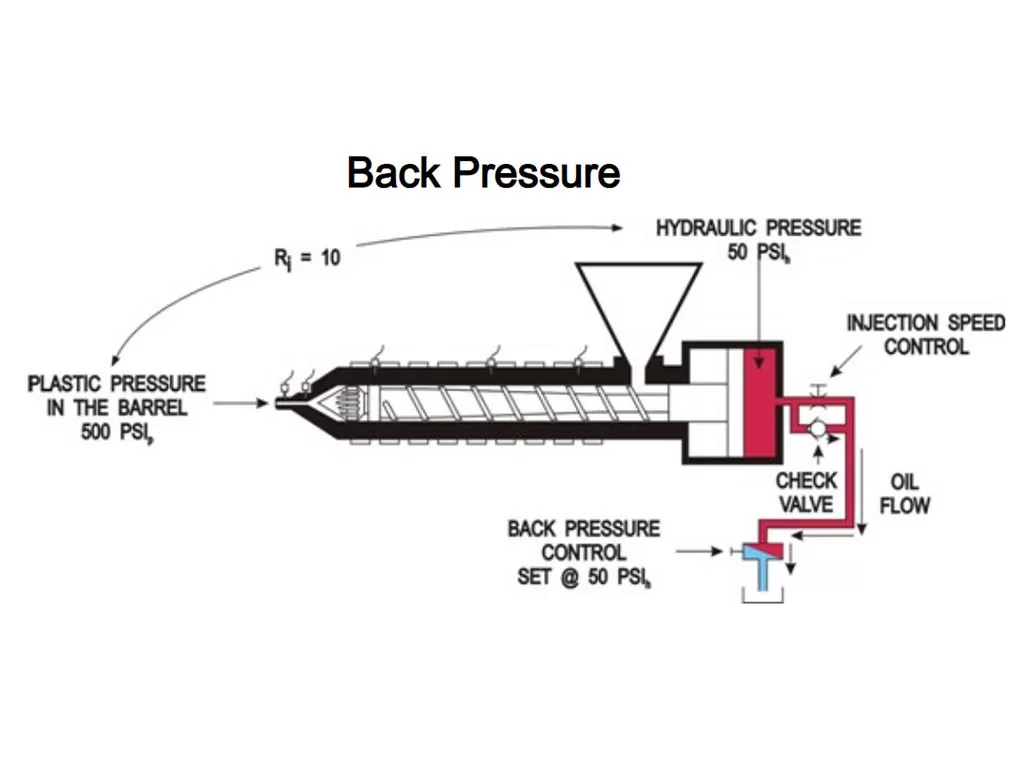
Improve Energy Efficiency
Energy efficiency has always been a critical concern for manufacturers of all types, especially those with extensive production facilities and multiple machines running simultaneously. Plastic injection molding machines equipped with proportional back pressure systems can improve energy efficiency by reducing overall energy consumption during the molding process. Unlike traditional systems that maintain constant pressure, proportional back pressure allows the machine to dynamically adjust the pressure, using only the necessary energy at each point in the cycle. Reducing unnecessary pressure helps minimize the power consumption of the hydraulic or servo system that controls the machine. In addition to saving energy costs, this also helps extend the life of machine components.
Improved Overall Production Efficiency
Proportional back pressure in plastic injection molding machines improves production efficiency by reducing cycle times, material waste, and defect occurrence. By maintaining precise control over the injection process, proportional back pressure enables manufacturers to optimize every cycle stage, from melting and mixing the plastic material to packing and cooling the final part.
One main way they increase efficiency is by fully preparing and evenly distributing the plastic material before it enters the mold.
This reduces the likelihood of incomplete fill, voids, or other defects that can slow production and produce expensive rework or scrap. Additionally, by maintaining consistent pressure during the packing and cooling stages, the machine can reduce cycle times, enabling manufacturers to produce more parts in less time without sacrificing quality.
The Importance of Proportional Back Pressure
Proportional back pressure is a crucial feature of Topstar plastic injection molding machines that significantly improve the quality, consistency, and efficiency of the injection molding process. By precisely controlling the flow and holding pressure of the molten plastic, proportional back pressure helps manufacturers achieve better material uniformity, prevent defects, improve dimensional accuracy, and optimize the process for different materials. It also helps reduce operating costs and reduce environmental impact.
TRENDING POSTS
- What factors can cause delays in the injection molding process of plastic molding machine? 2024/09/23
- Exhibition Review| Topstar participates in InterPlas Thailand 2024 2024/09/23
- Star Case | Topstar helps Santong upgrade its intelligent plant 2024/09/23
- Topstar Special | National Science and Technology Workers Day 2024/09/23
HOT TOPIC
- .ervo motor-driven linear robots
- 3 axis robot
- 3 axis robots
- 3 in 1 Compact Dehumidifying Dryer
- 3-axis robot
- 3-axis robots
- 5-axis CNC machine
- accuracy
- Air Chillers
- all electric injection molding machine
- all electric injection molding machines
- All-electric injection molding machines
- and overall production quality. Therefore
- AP-RubberPlas
- automated injection molding machine
- Automation changed engineering
- automation of injection molding robots
- auxiliary machine
- Bench Injection Molding Machine
- Cabinet dryer manufacturers
- Cabinet dryers
- chiller
- CNC Drilling Machine
- CNC Drilling Machines
- cnc engraving machine manufacturer
- cnc laser cutting machine manufacturer
- CNC machine
- CNC Machine Center
- CNC Machine for Sale
- CNC Machine Manufacturing
- CNC Machine Tool
- CNC machine tool product
- CNC Machining Center
- CNC wood carving machine
- Cooling system
- Cross-Walking Single Axis Servo Cylinder Robot
- Cross-Walking Single-Axis Servo Cylinder Robot
- Cross-Walking Three-Axis/Five-Axis Servo Driven Robot
- cross-walking three-axis/five-axis servo-driven robot
- Dehumidifier Dryer
- Dehumidifying Dryer
- delta parallel robot
- Desktop Injection Molding Machine
- Desktop injection molding machines
- Desktop Molding Machine
- desktop plastic injection machine
- Desktop Plastic Injection Molding Machine
- direct clamp injection molding machine
- Direct clamp injection molding machines
- Dosing & mixing system
- Drilling Centers
- Drying and dehumidification system
- drying and dehumidifying equipment
- Drying and Dehumidifying System
- drying system
- effective and efficient. Cabinet dryers are also used in other industries where large quantities of material need to be dried
- efficient injection molding machine
- elbow hydraulic injection molding machines
- electric injection molding machine
- electric injection molding machines
- energy-efficient injection molding robot
- energy-saving injection molding machine
- etc. Among injection molding robots
- exhibition
- features of CNC machine
- Feeding And Conveying System
- Five Axis Machine Center
- Fully automatic injection molding machine
- Gathering Topstar
- giant injection molding machine
- GMU-600 5-Axis Machining Center
- Granulating & Recycling System
- Heavy duty injection molding machine
- High-precision electric molding machines
- high-precision plastic molding machines
- high-speed all electric injection molding machine
- Honeycomb rotor dehumidifier
- horizontal injection molding machine
- Horizontal Injection Molding Machines
- Horizontal Injection Moulding Machine
- Horizontal Mixer manufacturer
- How The CNC Machine Works
- hybrid injection molding machine
- hydraulic injection molding machine
- Hydraulic Injection Molding Machines
- in this article
- Industrial robot
- Industrial Robot Chinese brand
- industrial robot parts
- industrial robot supplier
- Industrial robots
- Industry Chain
- Injection Manipulator
- injection manipulator robot
- injection mold machines
- Injection molding
- Injection molding automation
- Injection Molding Automation Solution
- injection molding dryer
- Injection molding equipment
- injection molding hopper dryer
- Injection molding machine
- injection molding machine brand
- Injection Molding Machine Factory
- Injection Molding Machine Manufacture
- Injection molding machine manufacturer
- injection molding machine manufacturers
- Injection molding machine procurement
- injection molding machine robotic arm
- injection molding machine with a robot
- Injection molding machines
- injection molding material dehumidifying
- injection molding plant
- Injection Molding Robot
- injection molding robot arm
- Injection molding robot automation
- Injection molding robotic arm
- injection molding robots
- Injection moulding machine
- Injection Moulding Robots
- Injection Robot
- Injection robot arm
- Injection robot manufacturer
- Injection robot wholesale
- injection robots
- intelligent injection molding machines
- Introducing Injection Robot
- It is the best choice for drying large quantities of material at once. Cabinetmakers use these machines because they are fast
- large injection molding machine
- Learn what industrial automation and robotics is
- linear robot
- linear robots
- low speed sound-proof granulator
- machine plastic molding
- make sure to add some! Improvements (2) Keyphrase in introduction: Your keyphrase or its synonyms appear in the first paragraph of the copy
- manipulator machine
- manufacturing
- medical grade injection molding machines
- medical injection molding machine
- medical injection molding machines
- micro injection molding machine
- middle speed granulator
- Mini CNC machine manufacturers.
- Mold Temperature Control System
- mold temperature controller
- mold temperature controllers
- molding material Dehumidifying System
- mould temperature control system
- mould temperature controller
- mould temperature controllers
- New electric injection molding machine
- nitrogen dryer manufacturer
- nitrogen dryer system manufacturer
- Oil type mold temperature controller
- Oil type mold temperature controllers
- open day
- Outbound links: No outbound links appear in this page. Add some! Images: No images appear on this page. Add some! Internal links: No internal links appear in this page
- PET Preform injection molding
- phone case maker machine
- phone case making machine
- plastic bottle making machine
- plastic bottle manufacturing
- plastic bucket making machine
- plastic bucket manufacturing
- Plastic chair making machine
- plastic forming equipment
- plastic hopper dryer
- plastic injection machine
- plastic injection machines
- plastic injection molding
- Plastic injection molding equipment
- Plastic injection molding machine
- Plastic Injection Molding Machines
- plastic injection moulding machine
- plastic injection robot
- Plastic Molding machine
- Plastic Molding Machines
- plastic molding press
- plastic moulding machine
- plastic phone case making machine
- plastic-molding machine
- powerful granulator
- Powerful Type Sound-Proof Granulator
- precision injection molding
- production of plastic seats
- pure water mould temperature controller
- Robot injection molding
- robot injection molding machine
- robot manufacturing companies
- Robotic arm for injection molding machine
- robotic injection molding machines
- robotics in injection molding
- SCARA robot
- SCARA robots
- Service-oriented manufacturing
- Servo Cylinder Robot
- servo driven robot
- Servo Driven Robots
- servo injection robots
- servo motor-driven linear robots
- servo-driven 3-axis robot
- Servo-Driven Robot
- Setup of injection machine
- Silicone Injection Molding Machine
- six-axis industrial robot
- Stainless Hopper Dryer
- Stainless Hopper Dryers
- star club
- swing arm robot
- take-out robots
- the choice between servo-driven robots and hydraulic robots will have a certain impact on efficiency
- the most popular injection molding machine
- the type of injection molding robot
- toggle clamp injection molding machine
- Toggle Hydraulic Injection Molding Machines
- toggle injection molding machine
- Top 10 brands of injection robots
- Topstar
- Topstar Engineering
- Topstar Industrial Robots
- Topstar injection molding intelligent
- Topstar Scara Robots
- Useful Injection molding machine
- Vertical machining centers
- volumetric type blender
- water chiller
- water chillers
- water distributor
- water type mold temperature controller
- Water Type MoldTemperature Controller
- Water-Type Mould Temperature Controllers
- We often face choices when performing injection molding. We will choose the type of injection molding machine
- wholesale of injection molding machines
- x carve CNC