What is the production capacity of a toggle injection molding machine?
2024/05/15 By Topstar
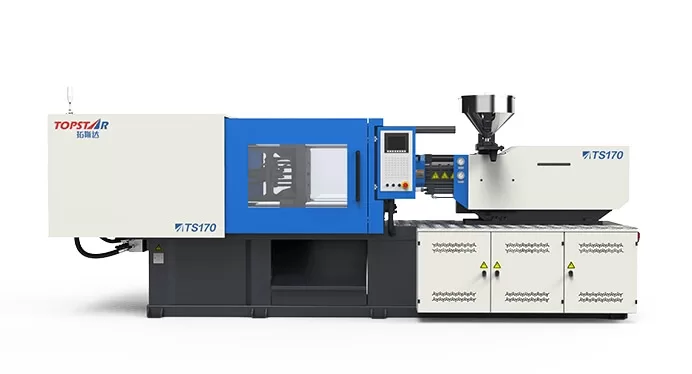
In the manufacturing industry, production capacity often reflects a manufacturer’s level of production capabilities. In the injection molding manufacturing process, you also need to understand the production capacity of the toggle injection molding machine. This comprehensive guide will take an in-depth look at every aspect of your toggle injection molding machine’s productivity, detailing its features, benefits, and impact on your productivity.
Toggle injection molding machine production capacity
The production capacity of a toggle injection molding machine is generally determined based on factors such as clamping force, process parameters, cycle time, etc. Normally, the production capacity of toggle injection molding machines ranges from 12 to 5,000 parts per cycle. An important factor in the production capabilities of these machines is their cycle time, which can be very short due to the efficiency of the mechanism of a toggle injection molding machine. The toggle mechanism provides fast mold opening and closing speeds, resulting in shorter overall cycle times. This cycle time efficiency translates directly into higher throughput.
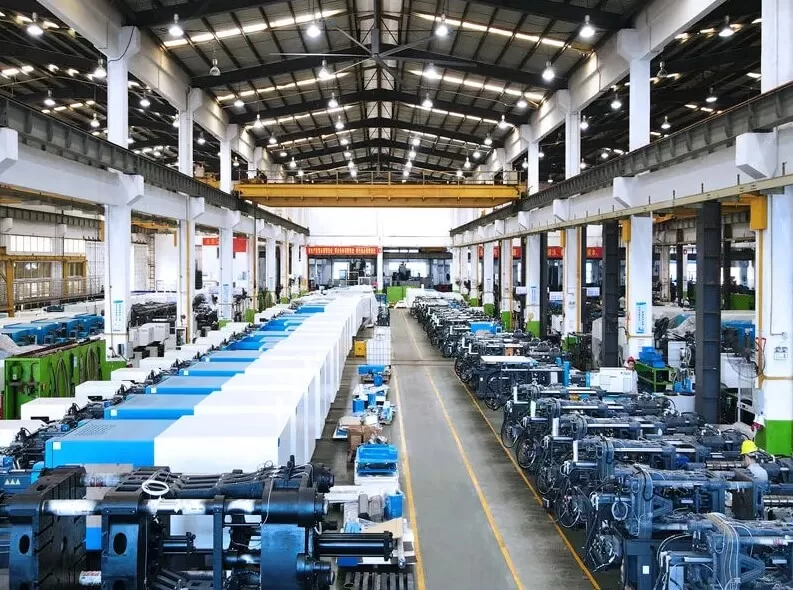
Factors affecting the production capacity of toggle injection molding machines
Several factors affect the production capacity of a toggle injection molding machine. The clamping force is usually the basis for determining the types of molds and parts that the machine can handle. Higher clamping forces can produce larger, more complex parts by ensuring a secure closure during injection. The size of the injection unit (including barrel and screw) determines the injection volume, the volume of material that can be injected in one cycle. The larger the size of the injection unit, the more material can be processed in each cycle. The cycle time encompasses the duration required to complete an injection molding cycle, including mold clamping, injection, cooling, and ejection stages. Shorter cycle times bring higher productivity.
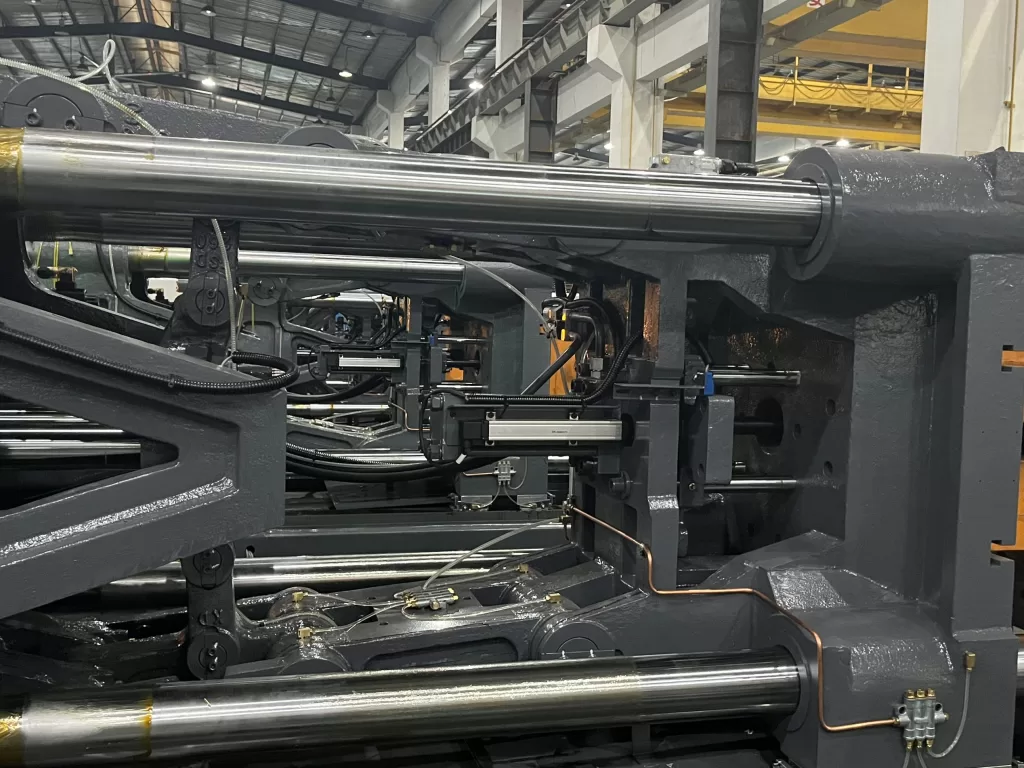
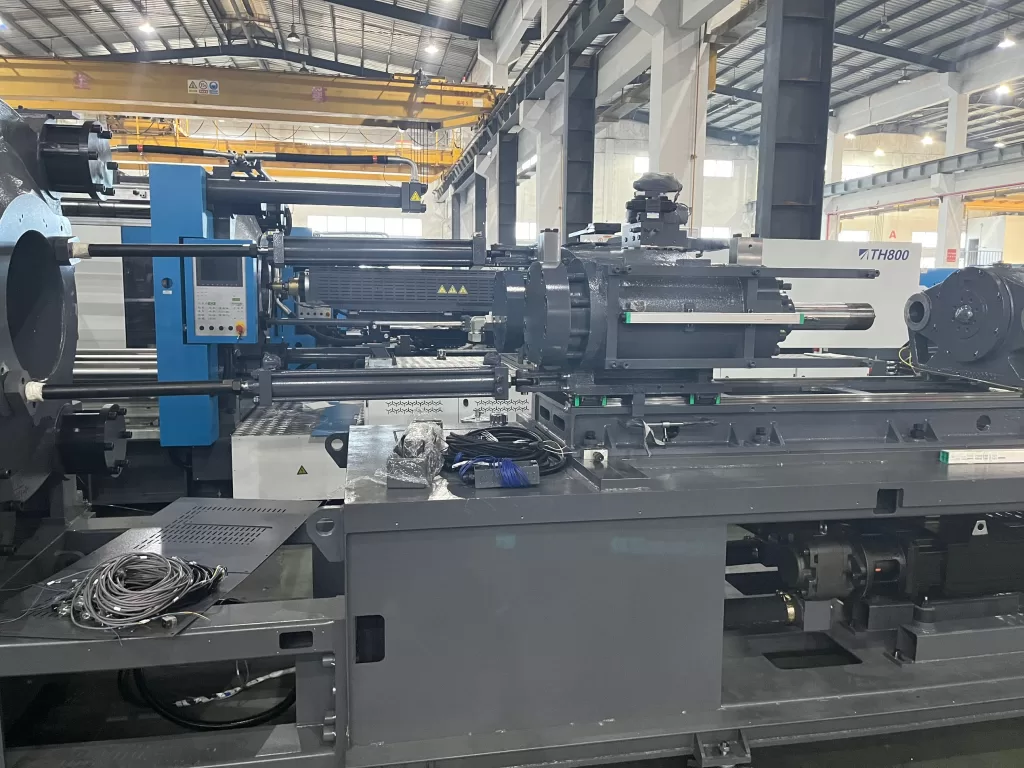
In addition, you need to perform regular maintenance and upkeep. Higher injection speeds can significantly reduce cycle times, thereby increasing overall throughput. Other factors include part size and shape complexity.
Benefits of High Productivity in Injection Molding
Higher throughput in injection molding also brings greater cost efficiencies, increasing a manufacturer’s market share and profitability by producing more parts in less time. In addition, high productivity reduces labor costs and energy consumption per part while catering to industries with mass production needs, such as automotive and consumer electronics. In addition, high production capacity increases the flexibility of production planning. Manufacturers can respond more quickly to changes in market demand, expanding or reducing production as needed.
How can we further increase production capacity?
Building upon the original foundation, we will integrate the toggle injection molding machine’s production capacity with various Internet of Things, big data analysis, and other technologies enabled by the emergence of Industry 4.0 technology. This integration aims to achieve real-time adjustment and predictive maintenance, enhancing efficiency, reducing downtime, and increasing production capacity. On the other hand, it is developing a more energy-saving injection molding machine, reducing energy consumption and improving accuracy by adding technologies such as servo-driven hydraulic systems and full motors.
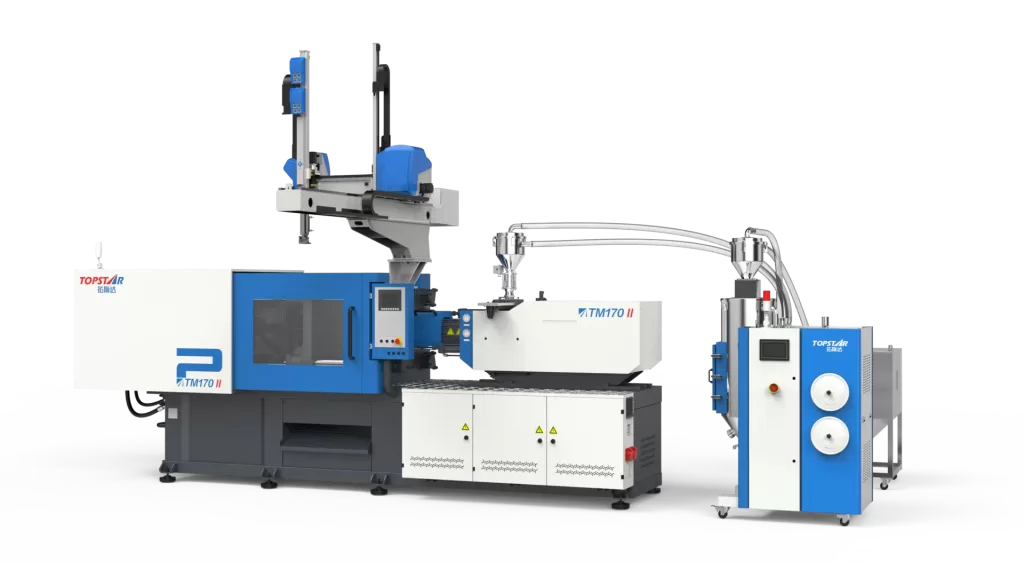
Various obstacles affecting production capacity
Earlier, we discussed how to increase your production capabilities, so in addition to this, you also need to carefully consider the various obstacles that may affect efficiency and productivity. The machine shutdown is the most important and will seriously affect the entire production plan, so our daily maintenance work and maintenance technology are very important. Worn, damaged, or improperly set up molds can also lead to defects, scrap, and reduced cycle times. Improper handling of materials can also result in inconsistent part quality and yield, necessitating proper storage, drying, and handling of materials.
Let you achieve higher productivity
Toggle injection molding machines are key equipment in modern plastics manufacturing operations. Their speed, precision, and reliability allow them to provide higher productivity than traditional injection molding machines, allowing manufacturers to meet the demands of today’s fast-paced market.
TRENDING POSTS
- What factors can cause delays in the injection molding process of plastic molding machine? 2024/05/15
- Exhibition Review| Topstar participates in InterPlas Thailand 2024 2024/05/15
- Star Case | Topstar helps Santong upgrade its intelligent plant 2024/05/15
- Topstar Special | National Science and Technology Workers Day 2024/05/15
HOT TOPIC
- .ervo motor-driven linear robots
- 3 axis robot
- 3 axis robots
- 3 in 1 Compact Dehumidifying Dryer
- 3-axis robot
- 3-axis robots
- 5-axis CNC machine
- accuracy
- Air Chillers
- all electric injection molding machine
- all electric injection molding machines
- All-electric injection molding machines
- and overall production quality. Therefore
- AP-RubberPlas
- automated injection molding machine
- Automation changed engineering
- automation of injection molding robots
- auxiliary machine
- Bench Injection Molding Machine
- Cabinet dryer manufacturers
- Cabinet dryers
- chiller
- CNC Drilling Machine
- CNC Drilling Machines
- cnc engraving machine manufacturer
- cnc laser cutting machine manufacturer
- CNC machine
- CNC Machine Center
- CNC Machine for Sale
- CNC Machine Manufacturing
- CNC Machine Tool
- CNC machine tool product
- CNC Machining Center
- CNC wood carving machine
- Cooling system
- Cross-Walking Single Axis Servo Cylinder Robot
- Cross-Walking Single-Axis Servo Cylinder Robot
- Cross-Walking Three-Axis/Five-Axis Servo Driven Robot
- cross-walking three-axis/five-axis servo-driven robot
- Dehumidifier Dryer
- Dehumidifying Dryer
- delta parallel robot
- Desktop Injection Molding Machine
- Desktop injection molding machines
- Desktop Molding Machine
- desktop plastic injection machine
- Desktop Plastic Injection Molding Machine
- direct clamp injection molding machine
- Direct clamp injection molding machines
- Dosing & mixing system
- Drilling Centers
- Drying and dehumidification system
- drying and dehumidifying equipment
- Drying and Dehumidifying System
- drying system
- effective and efficient. Cabinet dryers are also used in other industries where large quantities of material need to be dried
- efficient injection molding machine
- elbow hydraulic injection molding machines
- electric injection molding machine
- electric injection molding machines
- energy-efficient injection molding robot
- energy-saving injection molding machine
- etc. Among injection molding robots
- exhibition
- features of CNC machine
- Feeding And Conveying System
- Five Axis Machine Center
- Fully automatic injection molding machine
- Gathering Topstar
- giant injection molding machine
- GMU-600 5-Axis Machining Center
- Granulating & Recycling System
- Heavy duty injection molding machine
- High-precision electric molding machines
- high-precision plastic molding machines
- high-speed all electric injection molding machine
- Honeycomb rotor dehumidifier
- horizontal injection molding machine
- Horizontal Injection Molding Machines
- Horizontal Injection Moulding Machine
- Horizontal Mixer manufacturer
- How The CNC Machine Works
- hybrid injection molding machine
- hydraulic injection molding machine
- Hydraulic Injection Molding Machines
- in this article
- Industrial robot
- Industrial Robot Chinese brand
- industrial robot parts
- industrial robot supplier
- Industrial robots
- Industry Chain
- Injection Manipulator
- injection manipulator robot
- injection mold machines
- Injection molding
- Injection molding automation
- Injection Molding Automation Solution
- injection molding dryer
- Injection molding equipment
- injection molding hopper dryer
- Injection molding machine
- injection molding machine brand
- Injection Molding Machine Factory
- Injection Molding Machine Manufacture
- Injection molding machine manufacturer
- injection molding machine manufacturers
- Injection molding machine procurement
- injection molding machine robotic arm
- injection molding machine with a robot
- Injection molding machines
- injection molding material dehumidifying
- injection molding plant
- Injection Molding Robot
- injection molding robot arm
- Injection molding robot automation
- Injection molding robotic arm
- injection molding robots
- Injection moulding machine
- Injection Moulding Robots
- Injection Robot
- Injection robot arm
- Injection robot manufacturer
- Injection robot wholesale
- injection robots
- intelligent injection molding machines
- Introducing Injection Robot
- It is the best choice for drying large quantities of material at once. Cabinetmakers use these machines because they are fast
- large injection molding machine
- large injection molding machines
- Learn what industrial automation and robotics is
- linear robot
- linear robots
- low speed sound-proof granulator
- machine plastic molding
- make sure to add some! Improvements (2) Keyphrase in introduction: Your keyphrase or its synonyms appear in the first paragraph of the copy
- manipulator machine
- manufacturing
- medical grade injection molding machines
- medical injection molding machine
- medical injection molding machines
- micro injection molding machine
- middle speed granulator
- Mini CNC machine manufacturers.
- Mold Temperature Control System
- mold temperature controller
- mold temperature controllers
- molding material Dehumidifying System
- mould temperature control system
- mould temperature controller
- mould temperature controllers
- New electric injection molding machine
- nitrogen dryer manufacturer
- nitrogen dryer system manufacturer
- Oil type mold temperature controller
- Oil type mold temperature controllers
- open day
- Outbound links: No outbound links appear in this page. Add some! Images: No images appear on this page. Add some! Internal links: No internal links appear in this page
- PET Preform injection molding
- phone case maker machine
- phone case making machine
- plastic bottle making machine
- plastic bottle manufacturing
- plastic bucket making machine
- plastic bucket manufacturing
- Plastic chair making machine
- plastic forming equipment
- plastic hopper dryer
- plastic injection machine
- plastic injection machines
- plastic injection molding
- Plastic injection molding equipment
- Plastic injection molding machine
- Plastic Injection Molding Machines
- plastic injection moulding machine
- plastic injection robot
- Plastic Molding machine
- Plastic Molding Machines
- plastic molding press
- plastic moulding machine
- plastic phone case making machine
- plastic-molding machine
- powerful granulator
- Powerful Type Sound-Proof Granulator
- precision injection molding
- precision injection molding machines
- production of plastic seats
- pure water mould temperature controller
- Robot injection molding
- robot injection molding machine
- robot manufacturing companies
- Robotic arm for injection molding machine
- robotic injection molding machines
- robotics in injection molding
- SCARA robot
- SCARA robots
- Service-oriented manufacturing
- Servo Cylinder Robot
- servo driven robot
- Servo Driven Robots
- servo injection robots
- servo motor-driven linear robots
- servo-driven 3-axis robot
- Servo-Driven Robot
- Setup of injection machine
- Silicone Injection Molding Machine
- six-axis industrial robot
- Stainless Hopper Dryer
- Stainless Hopper Dryers
- star club
- swing arm robot
- take-out robots
- the choice between servo-driven robots and hydraulic robots will have a certain impact on efficiency
- the most popular injection molding machine
- the type of injection molding robot
- toggle clamp injection molding machine
- Toggle Hydraulic Injection Molding Machines
- toggle injection molding machine
- Top 10 brands of injection robots
- Topstar
- Topstar Engineering
- Topstar Industrial Robots
- Topstar injection molding intelligent
- Topstar Scara Robots
- Useful Injection molding machine
- Vertical machining centers
- volumetric type blender
- water chiller
- water chillers
- water distributor
- water type mold temperature controller
- Water Type MoldTemperature Controller
- Water-Type Mould Temperature Controllers
- We often face choices when performing injection molding. We will choose the type of injection molding machine
- wholesale of injection molding machines
- x carve CNC