What factors can cause delays in the injection molding process of plastic molding machine?
2024/12/13 By Topstar
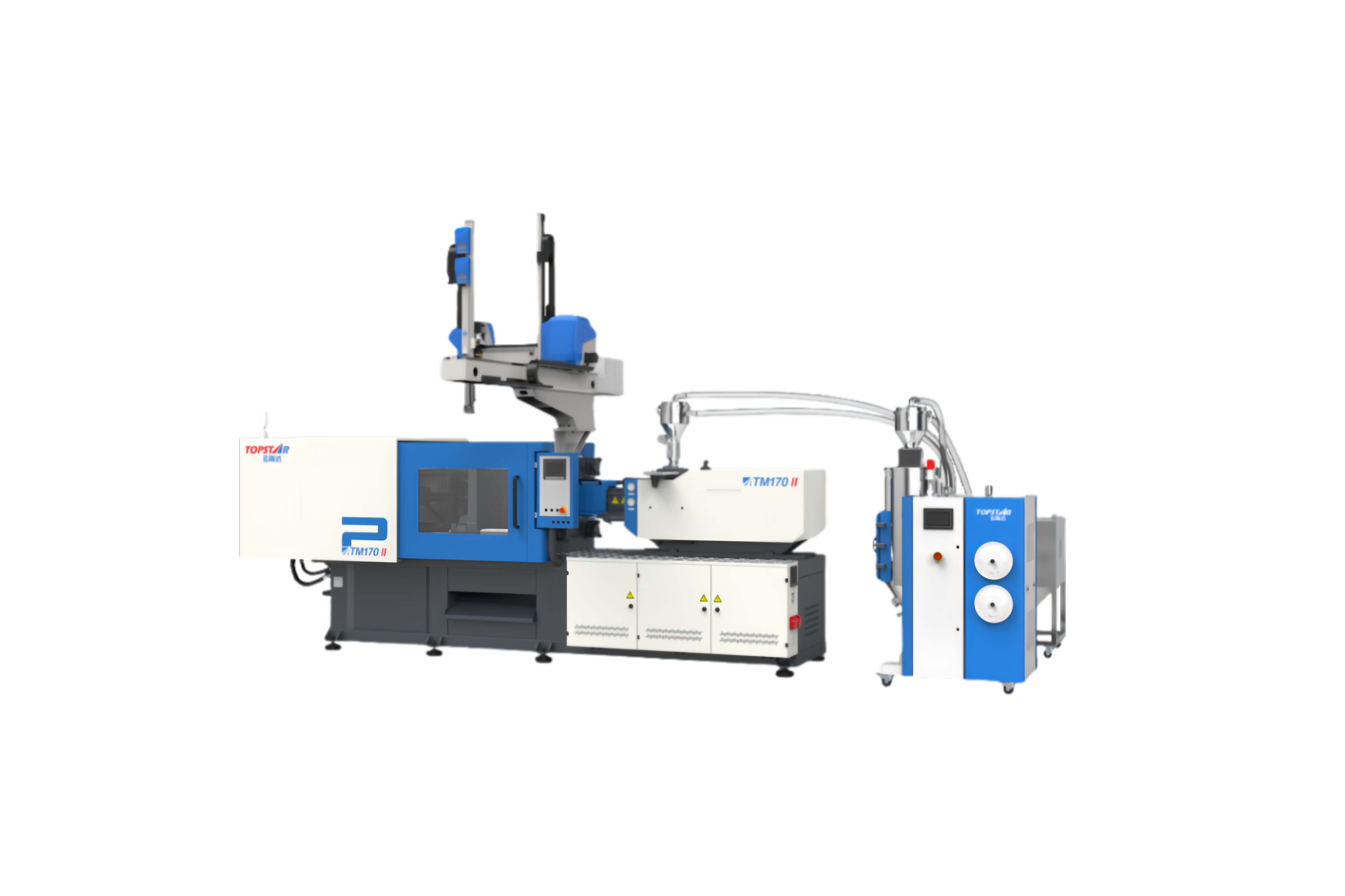
Injection molding is a fast, efficient, and economical manufacturing process for producing large quantities of complex plastic parts. Many factors can cause delays in plastic molding machines, affecting the efficiency of the entire production line. These factors include the machine’s insufficient intelligence, inadequate material handling, and more. Below, we will explore the various factors that cause delays in the injection molding process and how the plastic molding machine provided by Topstar can improve efficiency and prevent these delays.
Inadequate material handling and quality issues in plastic molding machine
First, let’s start with the material. Changes in material properties such as viscosity, moisture content, or particle size can affect the injection molding process. When moisture in plastic particles causes poor flow, surface defects such as speckles or bubbles will appear on the finished part. If operators do not dry the material correctly before injection, they will cause delays in the molding cycle, require additional drying time, or create waste due to part defects. The temperature of the material also plays a vital role. Operators will achieve consistent flow if they preheat the material to the proper temperature before injection, slowing the entire cycle time. Topstar’s plastic molding machines can integrate a drying and dehumidifying System, in which the double-layer insulated drying barrel adopts a down-blowing air duct design to prevent heat loss. Improving material drying efficiency can ensure optimal processing conditions, reducing delays caused by improper material drying.
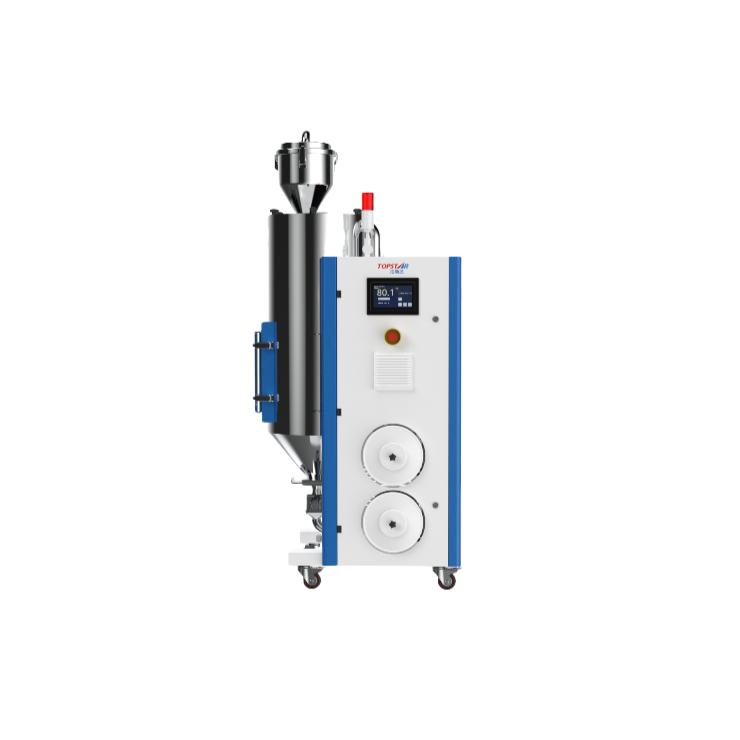
Plastic molding machine need more intelligence.
Intelligence is the key to reducing delays and improving production efficiency. Lack of intelligence in the injection molding process will lead to flexibility, slower cycles, increased labor costs, and unstable quality. Suppose the system does not integrate with the surrounding injection molding auxiliary equipment to improve intelligence and perform tasks such as part removal, material handling, and quality control. In that case, the equipment may experience repeated delays due to the inability to communicate between people and equipment. The automatic compensation function of the mold opening position is standard in Topstar’s plastic molding machine series. This function ensures that the robot can accurately grasp and place parts, solving problems such as delays in removal failure and equipment alarm shutdown due to ejection position deviation and inconsistent suction time.
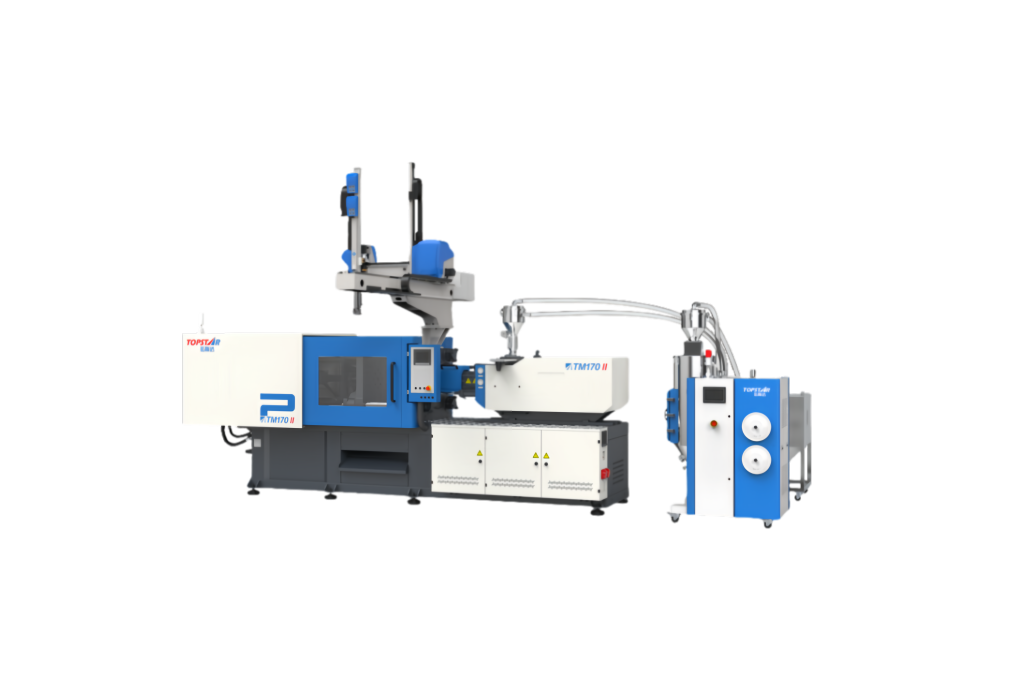
Cooling System Problems and Extended Cycle Times
Cooling time accounts for a large portion of the total cycle time. If the cooling system is not operating correctly, it may result in extended cycle times, delayed part production, and affected part quality. In some cases, problems such as inefficient cooling or insufficient coolant flow may cause uneven cooling, which may cause part warping or cracking. In addition, if the cooling system cannot handle the required heat dissipation, it will cause excessive cycle times, slowing overall production.
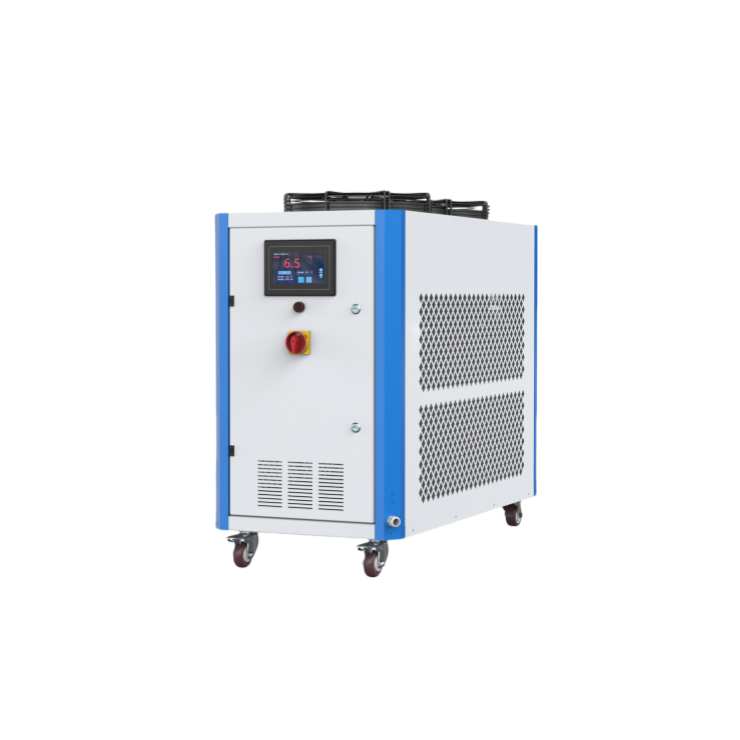
Topstar’s plastic molding machines use an automatic cooling system. The entire machine uses a fully computerized temperature controller, which is simple to operate and can accurately control the water temperature between 5-35°C. At the same time, current overload protection, high and low voltage control, and electronic time delay safety devices are also used. When a fault occurs, an alarm will be issued in time to display the cause of the fault, reducing the possibility of delays caused by inefficient cooling systems.
Inaccurate machine settings and calibration issues
Inaccurate machine settings can cause severe delays in the injection molding process. Operators must carefully calibrate injection pressure, speed, mold temperature, and cooling time to achieve the best results. If they set any of these parameters incorrectly, they can cause defects in the molded part, such as warpage, flash, or poor surface finish.
In addition, incorrect calibration can cause machine inefficiencies, such as uneven injection pressure, inconsistent part quality, or extended cycle times. The in-house control system used in our plastic molding machine series enables manufacturers to fine-tune all necessary parameters through a computer screen, ensuring that each injection cycle is optimized for speed and accuracy. Real-time monitoring and automatic adjustments can help prevent delays caused by incorrect machine settings, ensuring smooth and efficient production.
Delays caused by maintenance and repair issues
Planned and unplanned maintenance and repair downtime is another significant factor that causes delays in the injection molding process. Plastic molding machines are complex systems that require regular maintenance to keep them running smoothly. In addition, unforeseen repair issues can be even more detrimental, resulting in extended downtime between ordering parts and completing repairs. Topstar designs its plastic molding machines with reliability in mind, using high-quality components and durable systems to minimize the need for repairs. In addition, Topstar’s machines feature automatic diagnostics and preventive maintenance alerts to help identify potential issues before they cause unplanned downtime, reducing the risk of delays due to repair and maintenance issues.
Increase Efficiency and Reduce Delays
Delays in the injection molding can lead to lost time, increased costs, and reduced product quality. However, with features such as automatic mold compensation, state-of-the-art cooling systems, and automated control systems, Topstar’s injection molding machines are designed to reduce downtime, prevent delays, and increase the overall efficiency of the molding process.
TRENDING POSTS
- What factors can cause delays in the injection molding process of plastic molding machine? 2024/12/13
- Exhibition Review| Topstar participates in InterPlas Thailand 2024 2024/12/13
- Star Case | Topstar helps Santong upgrade its intelligent plant 2024/12/13
- Topstar Special | National Science and Technology Workers Day 2024/12/13
HOT TOPIC
- .ervo motor-driven linear robots
- 3 axis robot
- 3 axis robots
- 3 in 1 Compact Dehumidifying Dryer
- 3-axis robot
- 3-axis robots
- 5-axis CNC machine
- accuracy
- Air Chillers
- all electric injection molding machine
- all electric injection molding machines
- All-electric injection molding machines
- and overall production quality. Therefore
- AP-RubberPlas
- automated injection molding machine
- Automation changed engineering
- automation of injection molding robots
- auxiliary machine
- Bench Injection Molding Machine
- Cabinet dryer manufacturers
- Cabinet dryers
- chiller
- CNC Drilling Machine
- CNC Drilling Machines
- cnc engraving machine manufacturer
- cnc laser cutting machine manufacturer
- CNC machine
- CNC Machine Center
- CNC Machine for Sale
- CNC Machine Manufacturing
- CNC Machine Tool
- CNC machine tool product
- CNC Machining Center
- CNC wood carving machine
- Cooling system
- Cross-Walking Single Axis Servo Cylinder Robot
- Cross-Walking Single-Axis Servo Cylinder Robot
- Cross-Walking Three-Axis/Five-Axis Servo Driven Robot
- cross-walking three-axis/five-axis servo-driven robot
- Dehumidifier Dryer
- Dehumidifying Dryer
- delta parallel robot
- Desktop Injection Molding Machine
- Desktop injection molding machines
- Desktop Molding Machine
- desktop plastic injection machine
- Desktop Plastic Injection Molding Machine
- direct clamp injection molding machine
- Direct clamp injection molding machines
- Dosing & mixing system
- Drilling Centers
- Drying and dehumidification system
- drying and dehumidifying equipment
- Drying and Dehumidifying System
- drying system
- effective and efficient. Cabinet dryers are also used in other industries where large quantities of material need to be dried
- efficient injection molding machine
- elbow hydraulic injection molding machines
- electric injection molding machine
- electric injection molding machines
- energy-efficient injection molding robot
- energy-saving injection molding machine
- etc. Among injection molding robots
- exhibition
- features of CNC machine
- Feeding And Conveying System
- Five Axis Machine Center
- Fully automatic injection molding machine
- Gathering Topstar
- giant injection molding machine
- GMU-600 5-Axis Machining Center
- Granulating & Recycling System
- Heavy duty injection molding machine
- High-precision electric molding machines
- high-precision plastic molding machines
- high-speed all electric injection molding machine
- Honeycomb rotor dehumidifier
- horizontal injection molding machine
- Horizontal Injection Molding Machines
- Horizontal Injection Moulding Machine
- Horizontal Mixer manufacturer
- How The CNC Machine Works
- hybrid injection molding machine
- hydraulic injection molding machine
- Hydraulic Injection Molding Machines
- in this article
- Industrial robot
- Industrial Robot Chinese brand
- industrial robot parts
- industrial robot supplier
- Industrial robots
- Industry Chain
- Injection Manipulator
- injection manipulator robot
- injection mold machines
- Injection molding
- Injection molding automation
- Injection Molding Automation Solution
- injection molding dryer
- Injection molding equipment
- injection molding hopper dryer
- Injection molding machine
- injection molding machine brand
- Injection Molding Machine Factory
- Injection Molding Machine Manufacture
- Injection molding machine manufacturer
- injection molding machine manufacturers
- Injection molding machine procurement
- injection molding machine robotic arm
- injection molding machine with a robot
- Injection molding machines
- injection molding material dehumidifying
- injection molding plant
- Injection Molding Robot
- injection molding robot arm
- Injection molding robot automation
- Injection molding robotic arm
- injection molding robots
- Injection moulding machine
- Injection Moulding Robots
- Injection Robot
- Injection robot arm
- Injection robot manufacturer
- Injection robot wholesale
- injection robots
- intelligent injection molding machines
- Introducing Injection Robot
- It is the best choice for drying large quantities of material at once. Cabinetmakers use these machines because they are fast
- large injection molding machine
- Learn what industrial automation and robotics is
- linear robot
- linear robots
- low speed sound-proof granulator
- machine plastic molding
- make sure to add some! Improvements (2) Keyphrase in introduction: Your keyphrase or its synonyms appear in the first paragraph of the copy
- manipulator machine
- manufacturing
- medical grade injection molding machines
- medical injection molding machine
- medical injection molding machines
- micro injection molding machine
- middle speed granulator
- Mini CNC machine manufacturers.
- Mold Temperature Control System
- mold temperature controller
- mold temperature controllers
- molding material Dehumidifying System
- mould temperature control system
- mould temperature controller
- mould temperature controllers
- New electric injection molding machine
- nitrogen dryer manufacturer
- nitrogen dryer system manufacturer
- Oil type mold temperature controller
- Oil type mold temperature controllers
- open day
- Outbound links: No outbound links appear in this page. Add some! Images: No images appear on this page. Add some! Internal links: No internal links appear in this page
- PET Preform injection molding
- phone case maker machine
- phone case making machine
- plastic bottle making machine
- plastic bottle manufacturing
- plastic bucket making machine
- plastic bucket manufacturing
- Plastic chair making machine
- plastic forming equipment
- plastic hopper dryer
- plastic injection machine
- plastic injection machines
- plastic injection molding
- Plastic injection molding equipment
- Plastic injection molding machine
- Plastic Injection Molding Machines
- plastic injection moulding machine
- plastic injection robot
- Plastic Molding machine
- Plastic Molding Machines
- plastic molding press
- plastic moulding machine
- plastic phone case making machine
- plastic-molding machine
- powerful granulator
- Powerful Type Sound-Proof Granulator
- precision injection molding
- production of plastic seats
- pure water mould temperature controller
- Robot injection molding
- robot injection molding machine
- robot manufacturing companies
- Robotic arm for injection molding machine
- robotic injection molding machines
- robotics in injection molding
- SCARA robot
- SCARA robots
- Service-oriented manufacturing
- Servo Cylinder Robot
- servo driven robot
- Servo Driven Robots
- servo injection robots
- servo motor-driven linear robots
- servo-driven 3-axis robot
- Servo-Driven Robot
- Setup of injection machine
- Silicone Injection Molding Machine
- six-axis industrial robot
- Stainless Hopper Dryer
- Stainless Hopper Dryers
- star club
- swing arm robot
- take-out robots
- the choice between servo-driven robots and hydraulic robots will have a certain impact on efficiency
- the most popular injection molding machine
- the type of injection molding robot
- toggle clamp injection molding machine
- Toggle Hydraulic Injection Molding Machines
- toggle injection molding machine
- Top 10 brands of injection robots
- Topstar
- Topstar Engineering
- Topstar Industrial Robots
- Topstar injection molding intelligent
- Topstar Scara Robots
- Useful Injection molding machine
- Vertical machining centers
- volumetric type blender
- water chiller
- water chillers
- water distributor
- water type mold temperature controller
- Water Type MoldTemperature Controller
- Water-Type Mould Temperature Controllers
- We often face choices when performing injection molding. We will choose the type of injection molding machine
- wholesale of injection molding machines
- x carve CNC