What are the most popular injection molding machine on the market?
2024/01/24 By Topstar
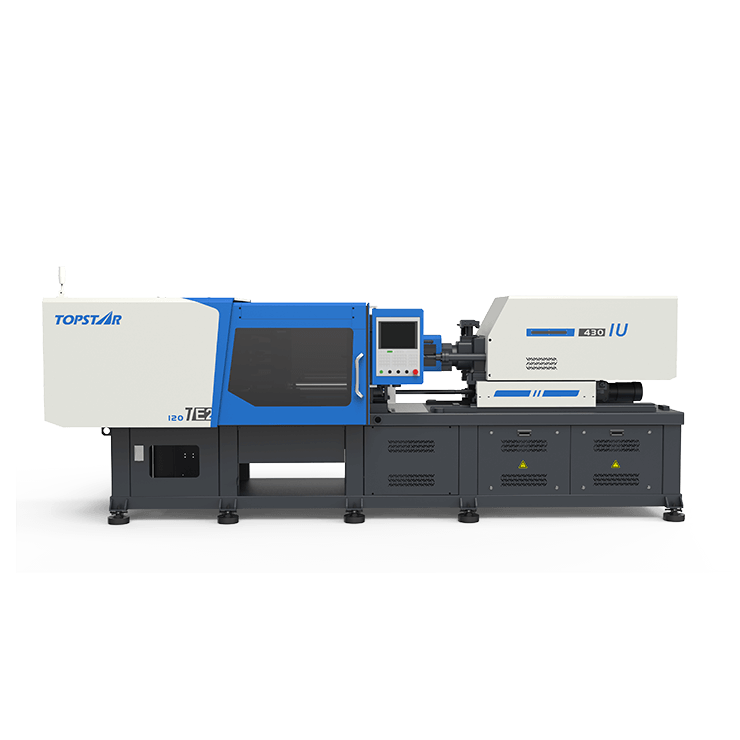
In this injection molding machine market, traditional injection molding machines all use electric-hydraulic servo control. In today’s market, users prefer injection molding machines that are highly clean and light in movement. Therefore, Topstar has developed a new high-quality electric injection molding machine. This series can be divided into two types: all-electric and hybrid. Below, we will explain why it is the most popular injection molding machine on the market.
The most Popular Injection Molding Machine Types
There is no doubt that electric injection molding machines are the most popular in the market today. We divide them into two types: an all-electric injection molding machine specially designed for high-clean application scenarios and a hybrid electric injection molding machine designed for all scenarios of hydraulic press manufacturing upgrades. Type injection molding machine. Their clamping force covers 60T-460T, B-screw covers 22~80mm, and injection speeds are available in low, medium, and high, with the highest optional 500mm/s.
The popularity of electric injection molding machines is due to their energy efficiency. Unlike hydraulic presses, the electric motor only consumes electricity during forming, resulting in significant energy savings. For any manufacturing plant, this efficiency can significantly reduce operating costs. And they don’t require using hydraulic oil to maintain a cleaner environment.
Clamping unit
The clamping unit of the electric injection molding machine has a popular modulus design to meet the mold installation needs. The comprehensive supporting feet make the dynamic support more stable, open and close the mold smoothly, and better protect the mold and machine. Using non-contact pull rods eliminates the need for lubrication and reduces strain on the Corinthian columns. The highly rigid template has sufficient stress analysis and more appropriate design strength, which can better protect the mold while ensuring the stability of the product. Their maintenance is generally more straightforward compared to hydraulic clamping units. Maintenance needs are minimized since there are fewer hydraulic components, and no hydraulic oil is required. This simplicity reduces maintenance downtime and creates a cleaner, greener manufacturing environment.
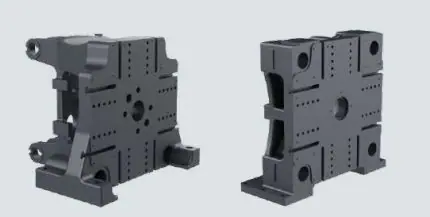
Injection unit
The injection unit of the electric injection molding machine uses an integrated injection seat, which has high rigidity, stable structure, and more precise control. A low-damping linear guide rail makes pressure detection more sensitive and pressure control more accurate. The support of the linear guide rail allows the minimum speed to be controlled at <1mm/s. These two core structures enable the motor to accurately manage the speed, pressure, and position of the screw when driving the injection process. This level of precision ensures consistent shot sizes and high-quality molded products, significantly reducing waste and improving overall efficiency.
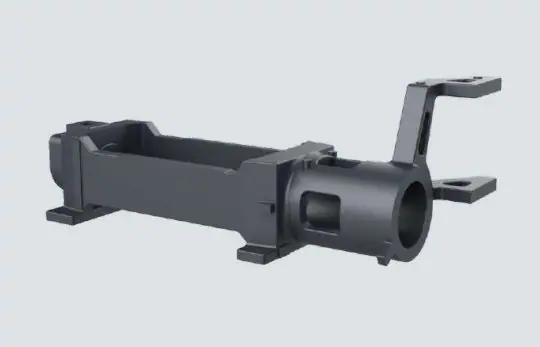
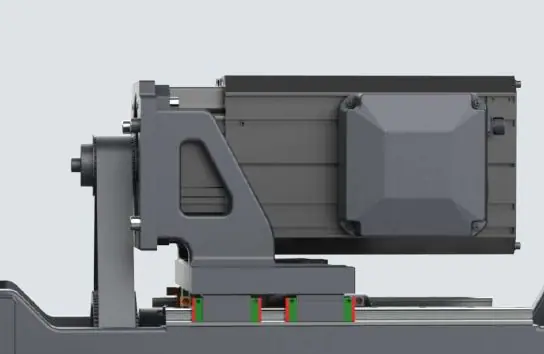
User interface for the most popular injection molding machines
To meet the industry’s and users’ needs, Topstar has interactive pages focusing on humanization. The interface is typically a touch screen, allowing the operator to interact with the machine through an intuitive touch screen. This touch-centric approach simplifies navigation, setup, and monitoring tasks, shortens the operator learning curve, and promotes a more streamlined production process. The user-friendly interface provides real-time information and feedback, allowing operators to monitor critical parameters such as temperature, pressure, and cycle time at a glance. The system displays alerts and notifications in a clear and easy-to-understand manner, enabling a quick response to any deviations or issues during the injection molding process.
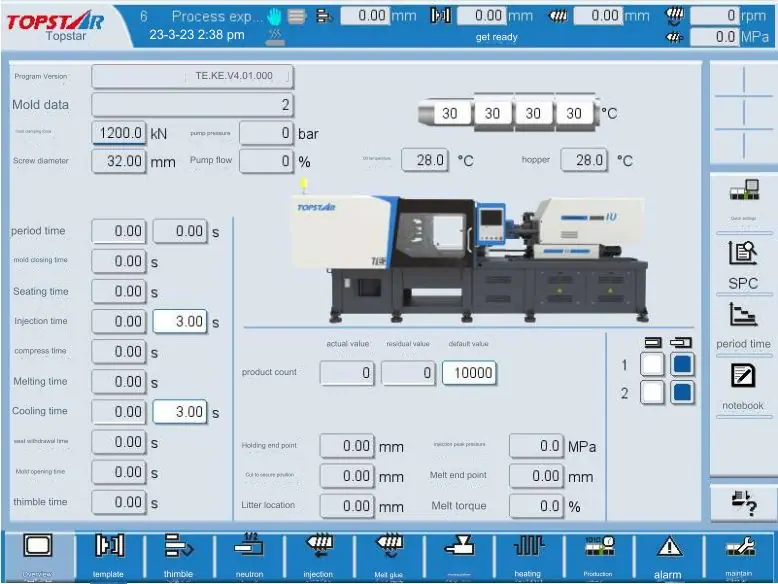
Innovative control methods
Topstar’s electric injection molding machine adopts our independently developed control method. This control principle solves the problem of product stability caused by communication delays in the control system. One core principle is sending the molding process data to the servo driver through the central controller of the upper controller, and the servo driver generates the operating curve by itself. This mode reduces the impact of communication delay on the high-speed operation of the servo motor, realizes real-time control of the servo motor, improves the accuracy of position, speed, and pressure control, and increases the response speed by 8-16 times.
By embedding the self-developed system, the servo driver can send synchronization signals containing the working status of the servo motor to the upper controller, which solves the problem of traditional hydraulic press operators being unable to understand the active status of the injection molding machine intuitively and improves human-computer interaction. This also makes them the most popular injection molding machines on the market.
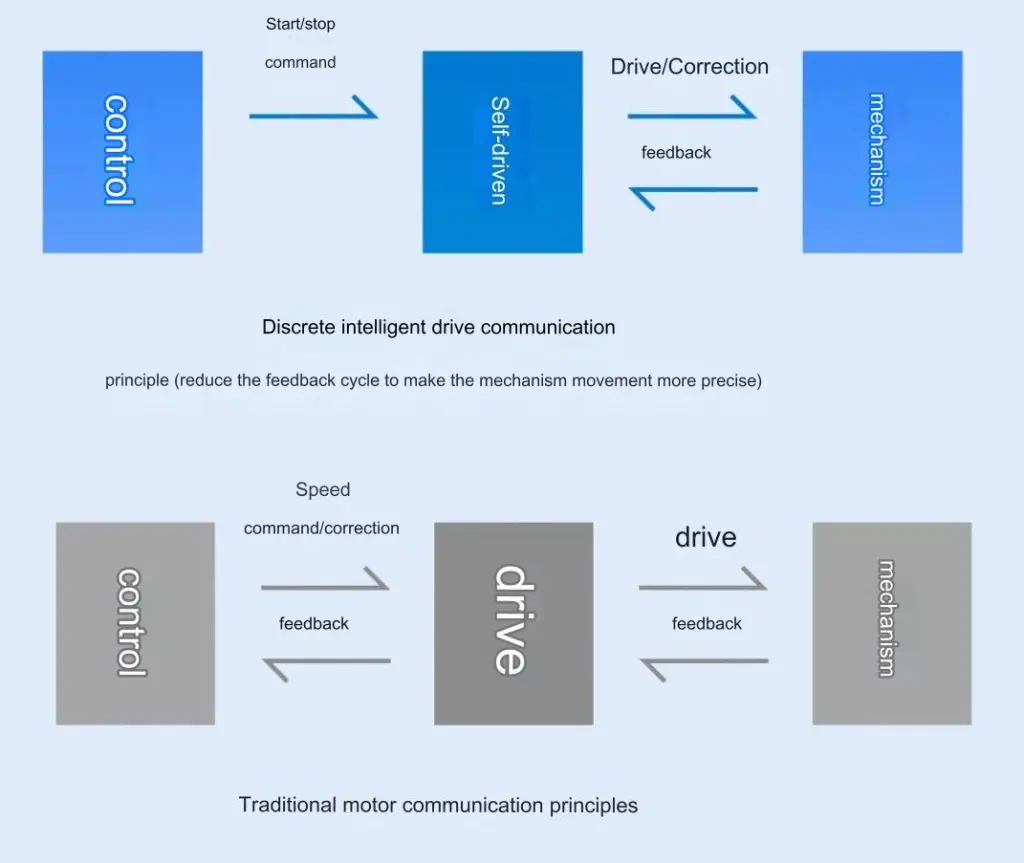
Application scenarios continue to improve!
In terms of application, electric injection molding machines have a wealth of cases. For example, in the medical industry, the use of electric injection molding machines saves at least 50% of electricity costs and increases the production efficiency of the production line by about 10%. We will continue to provide customers with precision-controlled, stable, safe, and reliable injection molding machines.
TRENDING POSTS
- What factors can cause delays in the injection molding process of plastic molding machine? 2024/01/24
- Exhibition Review| Topstar participates in InterPlas Thailand 2024 2024/01/24
- Star Case | Topstar helps Santong upgrade its intelligent plant 2024/01/24
- Topstar Special | National Science and Technology Workers Day 2024/01/24
HOT TOPIC
- 3 in 1 Compact Dehumidifying Dryer
- 5-axis CNC machine
- accuracy
- Air Chillers
- all electric injection molding machine
- All-electric injection molding machines
- and overall production quality. Therefore
- AP-RubberPlas
- automated injection molding machine
- Automation changed engineering
- automation of injection molding robots
- auxiliary machine
- Bench Injection Molding Machine
- Cabinet dryer manufacturers
- Cabinet dryers
- chiller
- CNC Drilling Machine
- CNC Drilling Machines
- cnc engraving machine manufacturer
- cnc laser cutting machine manufacturer
- CNC machine
- CNC Machine Center
- CNC Machine for Sale
- CNC Machine Manufacturing
- CNC Machine Tool
- CNC machine tool product
- CNC Machining Center
- CNC wood carving machine
- Cooling system
- Cross-Walking Single Axis Servo Cylinder Robot
- Cross-Walking Single-Axis Servo Cylinder Robot
- Cross-Walking Three-Axis/Five-Axis Servo Driven Robot
- cross-walking three-axis/five-axis servo-driven robot
- Dehumidifier Dryer
- Dehumidifying Dryer
- delta parallel robot
- Desktop Injection Molding Machine
- Desktop injection molding machines
- Desktop Molding Machine
- desktop plastic injection machine
- Desktop Plastic Injection Molding Machine
- direct clamp injection molding machine
- Direct clamp injection molding machines
- Dosing & mixing system
- Drilling Centers
- Drying and dehumidification system
- drying and dehumidifying equipment
- Drying and Dehumidifying System
- drying system
- effective and efficient. Cabinet dryers are also used in other industries where large quantities of material need to be dried
- efficient injection molding machine
- elbow hydraulic injection molding machines
- electric injection molding machine
- electric injection molding machines
- etc. Among injection molding robots
- exhibition
- features of CNC machine
- Feeding And Conveying System
- Five Axis Machine Center
- Fully automatic injection molding machine
- Gathering Topstar
- giant injection molding machine
- GMU-600 5-Axis Machining Center
- Granulating & Recycling System
- Heavy duty injection molding machine
- Honeycomb rotor dehumidifier
- horizontal injection molding machine
- Horizontal Injection Molding Machines
- Horizontal Injection Moulding Machine
- Horizontal Mixer manufacturer
- How The CNC Machine Works
- hybrid injection molding machine
- hydraulic injection molding machine
- Hydraulic Injection Molding Machines
- in this article
- Industrial robot
- Industrial Robot Chinese brand
- industrial robot parts
- industrial robot supplier
- Industrial robots
- Industry Chain
- Injection Manipulator
- injection mold machines
- Injection molding
- Injection molding automation
- Injection Molding Automation Solution
- injection molding dryer
- Injection molding equipment
- injection molding hopper dryer
- Injection molding machine
- injection molding machine brand
- Injection Molding Machine Factory
- Injection Molding Machine Manufacture
- Injection molding machine manufacturer
- injection molding machine manufacturers
- Injection molding machine procurement
- injection molding machine robotic arm
- injection molding machine with a robot
- Injection molding machines
- injection molding material dehumidifying
- injection molding plant
- Injection Molding Robot
- injection molding robot arm
- Injection molding robot automation
- Injection molding robotic arm
- injection molding robots
- Injection Moulding Robots
- Injection Robot
- Injection robot arm
- Injection robot manufacturer
- Injection robot wholesale
- injection robots
- intelligent injection molding machines
- Introducing Injection Robot
- It is the best choice for drying large quantities of material at once. Cabinetmakers use these machines because they are fast
- large injection molding machine
- Learn what industrial automation and robotics is
- low speed sound-proof granulator
- machine plastic molding
- make sure to add some! Improvements (2) Keyphrase in introduction: Your keyphrase or its synonyms appear in the first paragraph of the copy
- manipulator machine
- manufacturing
- micro injection molding machine
- middle speed granulator
- Mini CNC machine manufacturers.
- Mold Temperature Control System
- mold temperature controller
- molding material Dehumidifying System
- mould temperature controller
- mould temperature controllers
- New electric injection molding machine
- nitrogen dryer manufacturer
- nitrogen dryer system manufacturer
- Oil type mold temperature controller
- open day
- Outbound links: No outbound links appear in this page. Add some! Images: No images appear on this page. Add some! Internal links: No internal links appear in this page
- PET Preform injection molding
- phone case maker machine
- phone case making machine
- plastic bottle making machine
- plastic bottle manufacturing
- plastic bucket making machine
- plastic bucket manufacturing
- Plastic chair making machine
- plastic forming equipment
- plastic hopper dryer
- plastic injection machine
- plastic injection machines
- plastic injection molding
- Plastic injection molding equipment
- Plastic injection molding machine
- Plastic Injection Molding Machines
- plastic injection robot
- Plastic Molding machine
- Plastic Molding Machines
- plastic molding press
- plastic phone case making machine
- plastic-molding machine
- powerful granulator
- Powerful Type Sound-Proof Granulator
- production of plastic seats
- Robot injection molding
- robot injection molding machine
- robot manufacturing companies
- Robotic arm for injection molding machine
- robotic injection molding machines
- robotics in injection molding
- SCARA robot
- SCARA robots
- Service-oriented manufacturing
- Servo Cylinder Robot
- servo driven robot
- Servo Driven Robots
- servo injection robots
- Servo-Driven Robot
- Setup of injection machine
- Silicone Injection Molding Machine
- six-axis industrial robot
- Stainless Hopper Dryer
- Stainless Hopper Dryers
- star club
- swing arm robot
- the choice between servo-driven robots and hydraulic robots will have a certain impact on efficiency
- the most popular injection molding machine
- the type of injection molding robot
- toggle clamp injection molding machine
- Toggle Hydraulic Injection Molding Machines
- toggle injection molding machine
- Top 10 brands of injection robots
- Topstar
- Topstar Engineering
- Topstar Industrial Robots
- Topstar injection molding intelligent
- Topstar Scara Robots
- Useful Injection molding machine
- Vertical machining centers
- volumetric type blender
- water chiller
- water chillers
- water distributor
- Water Type MoldTemperature Controller
- We often face choices when performing injection molding. We will choose the type of injection molding machine
- wholesale of injection molding machines
- x carve CNC