What are the most important specifications for a plastic injection molding machine?
2024/08/28 By Topstar
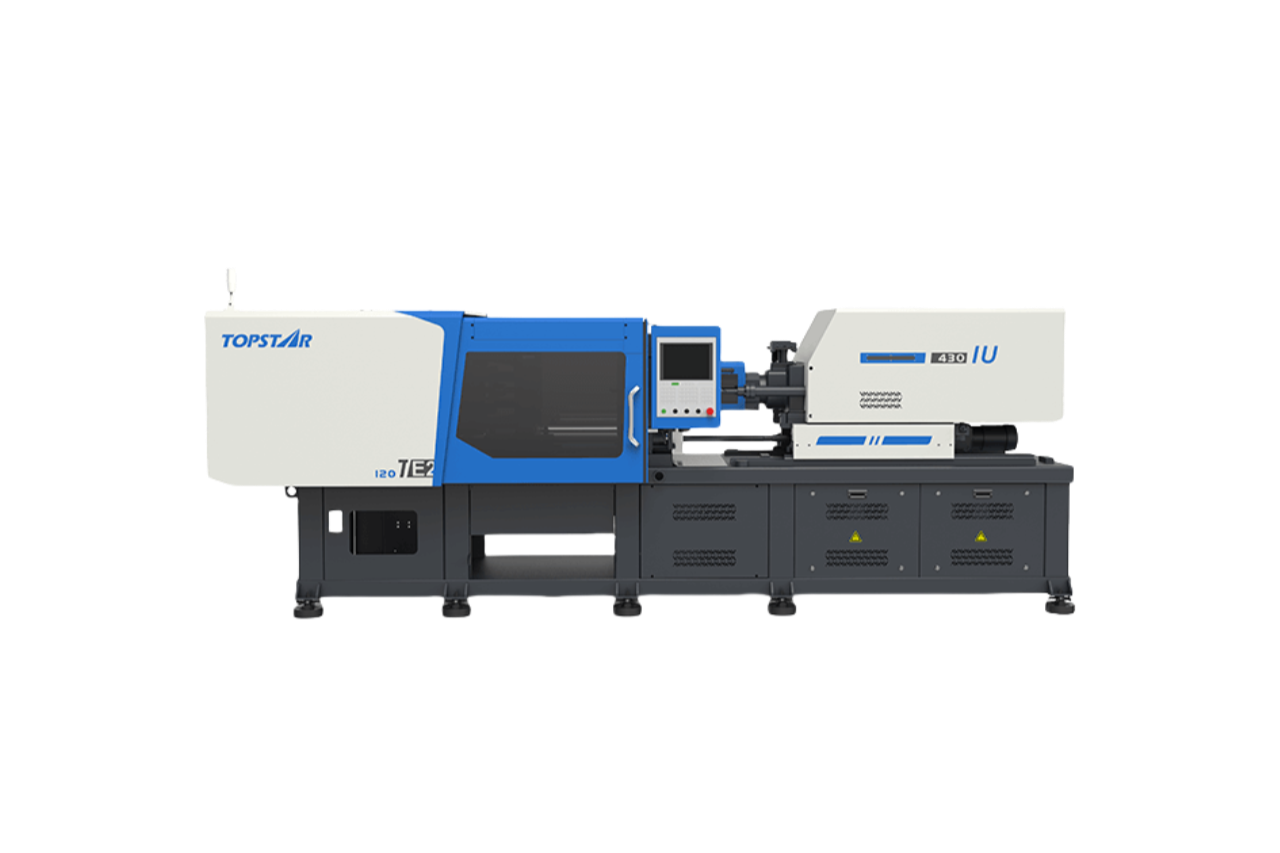
Injection molding is the core manufacturing process for making various plastic products involving multiple industries, such as automobiles, electronics, consumer products, and medical devices. The efficiency and precision of the plastic injection molding machine you choose will significantly impact the product’s quality, production speed, and cost. So, when you purchase a batch of plastic injection molding machines, you need to know their most critical specifications. Topstar will share the key specifications in this article based on its experience as a technical expert in plastic injection molding technology.
Clamping force in plastic injection molding machine
One of the most critical specifications of plastic injection molding machines is the clamping force. The clamping force is the pressure the machine applies to keep the mold halves closed during the injection and cooling stages of the molding process. It is critical to determine whether the machine can continuously produce high-quality parts. Therefore, you must use a large enough clamping force to offset the pressure generated when injecting the molten plastic into the mold. If the clamping force is insufficient, the mold may open slightly, resulting in flashing. When choosing the clamping force, you must balance the size and complexity of the part produced and the material used. The clamping force range of Topstar’s plastic injection molding machine series is around 90T-2800T. You can calculate the required clamping force based on the part’s projected surface area and the material’s viscosity.
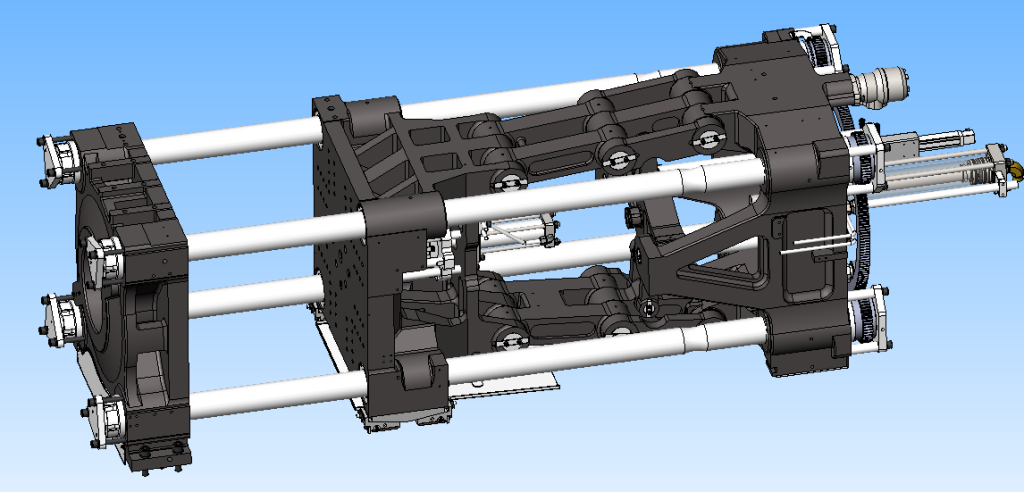
Injection Capacity of Plastic Injection Molding Machine
Another important specification is injection capacity, which refers to the maximum volume of molten plastic that the machine can inject into the mold during each cycle. Determining whether the machine can produce parts of the required size and complexity is critical. The injection capacity of a plastic injection molding machine must be consistent with the requirements of the part being produced. If the injection capacity is higher, the machine may be able to fill the mold, resulting in an incomplete or defective part. If it is too high, it will result in excessive material use and increased production costs.
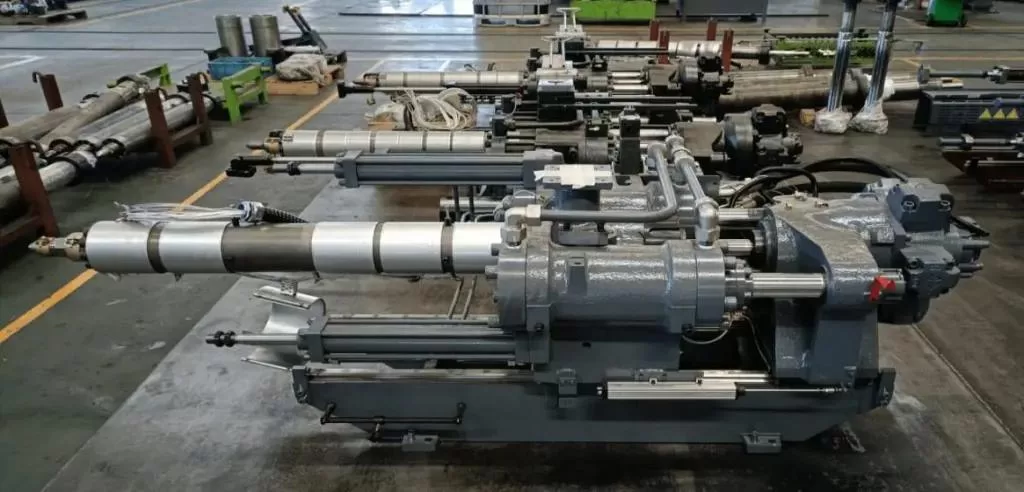
Manufacturers consider the part cavity’s volume and the material’s density to determine the appropriate injection capacity. You must also consider other features, such as gates, runners, and vents, which affect the total material required for each shot. In addition to the total injection capacity, you must carefully control injection pressure and speed to ensure the material fills the mold evenly and without defects.
The screw diameter and stroke length throughout the injection unit affect the injection capacity and the machine’s ability to handle different materials. As you increase the screw diameter, the injection capacity grows, while the stroke length determines how much material you can inject in a single cycle. Selecting the right combination of these factors is critical to optimizing the injection molding process and achieving consistent, high-quality results.
Mold Size and Compatibility
Mold Size and Compatibility They determine the range of parts a machine can produce. The platen size and tie-bar spacing usually define the mold sizes a plastic injection molding machine can accommodate. Platen size refers to the size of the mounting plate where you mount the mold. If the platen is too small, the mold will fit, making the machine usable for your application. Conversely, a platen much larger than the mold may result in inefficient use of space and resources.
Tie-bar spacing refers to the distance between the vertical bars that support the mold. This spacing must be broad enough to accommodate the mold without interference for smooth operation. If the tie-bar spacing is too narrow, the mold may not fit, or friction and wear may occur during operation, resulting in potential damage to the mold and the machine.
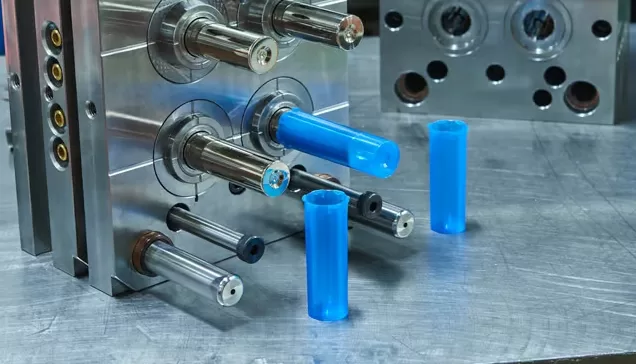
In addition to the physical size of the mold, the weight of the mold and the handling capacity of the machine need to be considered. The mold weight specification ensures the machine can safely support the mold without excessive stress on the moving parts. Finally, compatibility with existing molds is a critical factor for manufacturers with a stock of molds. When upgrading or purchasing a new plastic injection molding machine, it is essential to ensure the new machine is compatible with existing molds to avoid expensive modifications or replacements.
Cycle Time
Cycle time is one of the most critical performance indicators in plastic injection molding because it directly affects production speed, efficiency, and total output. For manufacturers, reducing cycle time without compromising part quality is critical to achieving higher productivity and maximizing profitability.
Various factors affect the cycle time of a plastic injection molding machine, including injection speed, cooling time, and the efficiency of the ejection system. Optimize the injection speed, the rate at which you inject molten plastic into the mold, to ensure quick and even filling. While faster injection speeds can reduce cycle time, you must carefully manage them to prevent defects such as flow lines, air pockets, or incomplete filling.
Cooling time is another critical component of cycle time. After the molten plastic is injected into the mold, it must cool and solidify before the part can be ejected. Reducing cooling time can significantly improve overall cycle time, and advanced cooling systems can help reduce cooling time while maintaining part quality. While reducing cycle time is vital for enhancing productivity, balancing speed and part quality is also essential. In Topstar’s injection molding machine series, cycle time can be carefully monitored and adjusted through the core control panel to achieve the best balance between speed and quality.
Energy efficiency of plastic injection molding machines
Energy consumption directly affects operating costs and the environmental impact of the production process and is an issue that every manufacturer will pay attention to.
One of the main factors affecting the energy efficiency of plastic injection molding machines is the type of drive system used. There are three main types of drive systems: hydraulic, electric, and hybrid. Hydraulic machines are the most traditional type and consume more energy because the hydraulic pump runs continuously, even when you do not require active movement. On the other hand, electric machines use servo motors that only run when needed, reducing energy consumption and, more precisely, controlling the molding process. Hybrid machines combine the advantages of hydraulic and electric systems to balance power and efficiency.
Electric injection molding machines are generally more energy-efficient than hydraulic injection molding machines because they require less power and generate less heat, reducing the need for cooling. In addition, electric machines have faster response times and higher precision, which can shorten cycle times and improve part quality. The machine’s control system also helps to improve energy efficiency. Topstar’s plastic injection molding machines use a self-developed control system that adjusts the machine’s parameters in real time according to the specific requirements of each cycle, thereby optimizing energy use. These systems can monitor and adjust motor speed, hydraulic pressure, and cooling rates to ensure energy is used efficiently.
Make the right decision.
There are many specifications to consider in a plastic injection molding machine, so it is essential to focus on the factors that impact your production needs and goals most. Clamping force, shot capacity, mold size and compatibility, cycle time, energy efficiency, control systems, and automation. Each of these factors determines the performance of the machine and its suitability for a specific application.
TRENDING POSTS
- What factors can cause delays in the injection molding process of plastic molding machine? 2024/08/28
- Exhibition Review| Topstar participates in InterPlas Thailand 2024 2024/08/28
- Star Case | Topstar helps Santong upgrade its intelligent plant 2024/08/28
- Topstar Special | National Science and Technology Workers Day 2024/08/28
HOT TOPIC
- .ervo motor-driven linear robots
- 1.0 guangdong topstar technology co. ltd
- 1.0 topstar china
- 1.0 topstar robot
- 11
- 2
- 21
- 23
- 3 axis robot
- 3 axis robots
- 3 in 1 Compact Dehumidifying Dryer
- 3-axis robot
- 3-axis robots
- 39
- 41
- 5-axis CNC machine
- 62
- accuracy
- Air Chillers
- all electric injection molding machine
- all electric injection molding machines
- All-electric injection molding machines
- and overall production quality. Therefore
- AP-RubberPlas
- automated injection molding machine
- Automation changed engineering
- automation of injection molding robots
- auxiliary machine
- Bench Injection Molding Machine
- Cabinet dryer manufacturers
- Cabinet dryers
- chiller
- CNC Drilling Machine
- CNC Drilling Machines
- cnc engraving machine manufacturer
- cnc laser cutting machine manufacturer
- CNC machine
- CNC Machine Center
- CNC Machine for Sale
- CNC Machine Manufacturing
- CNC Machine Tool
- CNC machine tool product
- CNC Machining Center
- CNC wood carving machine
- Cooling system
- Cross-Walking Single Axis Servo Cylinder Robot
- Cross-Walking Single-Axis Servo Cylinder Robot
- Cross-Walking Three-Axis/Five-Axis Servo Driven Robot
- cross-walking three-axis/five-axis servo-driven robot
- Dehumidifier Dryer
- Dehumidifying Dryer
- delta parallel robot
- Desktop Injection Molding Machine
- Desktop injection molding machines
- Desktop Molding Machine
- desktop plastic injection machine
- Desktop Plastic Injection Molding Machine
- direct clamp injection molding machine
- Direct clamp injection molding machines
- Dosing & mixing system
- Drilling Centers
- Drying and dehumidification system
- drying and dehumidifying equipment
- Drying and Dehumidifying System
- drying system
- effective and efficient. Cabinet dryers are also used in other industries where large quantities of material need to be dried
- efficient injection molding machine
- elbow hydraulic injection molding machines
- electric injection molding machine
- electric injection molding machines
- energy-efficient injection molding robot
- energy-saving injection molding machine
- etc. Among injection molding robots
- exhibition
- features of CNC machine
- Feeding And Conveying System
- Five Axis Machine Center
- Fully automatic injection molding machine
- Gathering Topstar
- giant injection molding machine
- GMU-600 5-Axis Machining Center
- Granulating & Recycling System
- Heavy duty injection molding machine
- High-precision electric molding machines
- high-precision plastic molding machines
- high-speed all electric injection molding machine
- Honeycomb rotor dehumidifier
- horizontal injection molding machine
- Horizontal Injection Molding Machines
- Horizontal Injection Moulding Machine
- Horizontal Mixer manufacturer
- How The CNC Machine Works
- hybrid injection molding machine
- hydraulic injection molding machine
- Hydraulic Injection Molding Machines
- in this article
- Industrial robot
- Industrial Robot Chinese brand
- industrial robot parts
- industrial robot supplier
- Industrial robots
- Industry Chain
- Injection Manipulator
- injection manipulator robot
- injection mold machines
- Injection molding
- Injection molding automation
- Injection Molding Automation Solution
- injection molding dryer
- Injection molding equipment
- injection molding hopper dryer
- Injection molding machine
- injection molding machine brand
- Injection Molding Machine Factory
- Injection Molding Machine Manufacture
- Injection molding machine manufacturer
- injection molding machine manufacturers
- Injection molding machine procurement
- injection molding machine robotic arm
- injection molding machine with a robot
- Injection molding machines
- injection molding material dehumidifying
- injection molding plant
- Injection Molding Robot
- injection molding robot arm
- Injection molding robot automation
- Injection molding robotic arm
- injection molding robots
- Injection moulding machine
- Injection Moulding Robots
- Injection Robot
- Injection robot arm
- Injection robot manufacturer
- Injection robot wholesale
- injection robots
- intelligent injection molding machines
- Introducing Injection Robot
- It is the best choice for drying large quantities of material at once. Cabinetmakers use these machines because they are fast
- large injection molding machine
- large injection molding machines
- Learn what industrial automation and robotics is
- linear robot
- linear robots
- low speed sound-proof granulator
- machine plastic molding
- make sure to add some! Improvements (2) Keyphrase in introduction: Your keyphrase or its synonyms appear in the first paragraph of the copy
- manipulator machine
- manufacturing
- medical grade injection molding machines
- medical injection molding machine
- medical injection molding machines
- micro injection molding machine
- middle speed granulator
- Mini CNC machine manufacturers.
- Mold Temperature Control System
- mold temperature controller
- mold temperature controllers
- molding material Dehumidifying System
- mould temperature control system
- mould temperature controller
- mould temperature controllers
- New electric injection molding machine
- nitrogen dryer manufacturer
- nitrogen dryer system manufacturer
- Oil type mold temperature controller
- Oil type mold temperature controllers
- open day
- Outbound links: No outbound links appear in this page. Add some! Images: No images appear on this page. Add some! Internal links: No internal links appear in this page
- PET Preform injection molding
- phone case maker machine
- phone case making machine
- plastic bottle making machine
- plastic bottle manufacturing
- plastic bucket making machine
- plastic bucket manufacturing
- Plastic chair making machine
- plastic forming equipment
- plastic hopper dryer
- plastic injection machine
- plastic injection machines
- plastic injection molding
- Plastic injection molding equipment
- Plastic injection molding machine
- Plastic Injection Molding Machines
- plastic injection moulding machine
- plastic injection robot
- Plastic Molding machine
- Plastic Molding Machines
- plastic molding press
- plastic moulding machine
- plastic phone case making machine
- plastic-molding machine
- powerful granulator
- Powerful Type Sound-Proof Granulator
- precision injection molding
- precision injection molding machines
- production of plastic seats
- pure water mould temperature controller
- Robot injection molding
- robot injection molding machine
- robot manufacturing companies
- Robotic arm for injection molding machine
- robotic injection molding machines
- robotics in injection molding
- SCARA robot
- SCARA robots
- Service-oriented manufacturing
- Servo Cylinder Robot
- servo driven robot
- Servo Driven Robots
- servo injection robots
- servo motor-driven linear robots
- servo-driven 3-axis robot
- Servo-Driven Robot
- Setup of injection machine
- Silicone Injection Molding Machine
- six-axis industrial robot
- Stainless Hopper Dryer
- Stainless Hopper Dryers
- star club
- swing arm robot
- take-out robots
- the choice between servo-driven robots and hydraulic robots will have a certain impact on efficiency
- the most popular injection molding machine
- the type of injection molding robot
- toggle clamp injection molding machine
- Toggle Hydraulic Injection Molding Machines
- toggle injection molding machine
- Top 10 brands of injection robots
- Topstar
- Topstar Engineering
- Topstar Industrial Robots
- Topstar injection molding intelligent
- Topstar Scara Robots
- Useful Injection molding machine
- Vertical machining centers
- volumetric type blender
- water chiller
- water chillers
- water distributor
- water type mold temperature controller
- Water Type MoldTemperature Controller
- Water-Type Mould Temperature Controllers
- We often face choices when performing injection molding. We will choose the type of injection molding machine
- wholesale of injection molding machines
- x carve CNC
- 热门查询 点击次数 展示 排名 topstar