What are the latest technological advances in mould temperature controller?
2024/06/07 By Topstar
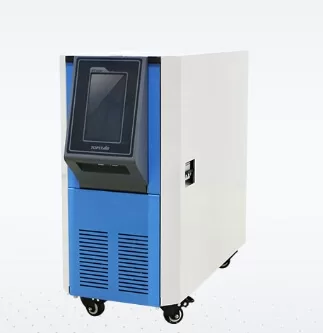
Injection molding requires precise and controllable temperature. Among the auxiliary equipment, the mould temperature controller plays a key role in regulating the mould temperature and ensuring the quality of the parts. With technology’s continuous advancement and iteration, Topstar has updated and upgraded them while maintaining the original technology. In this guide, we will discuss the latest technological advances with you so that different manufacturing industries can learn about the benefits they bring.
Touch screen controller for mould temperature controller
Unlike previous mould temperature controllers, we have added a dedicated touchscreen controller to provide highly accurate temperature management. Digital technology monitors and adjusts the temperature in real-time, and the intuitive interface allows users to adjust the settings easily. Compared with traditional temperature control systems, the outstanding advantage of the upgraded touchscreen controller is that it can save more than 35% of electricity. The entire touchscreen controller also includes an intelligent standby mode that reduces power consumption during idle periods. When the mold is not in use, the controller can reduce the temperature or shut down non-essential components, thereby further saving energy.
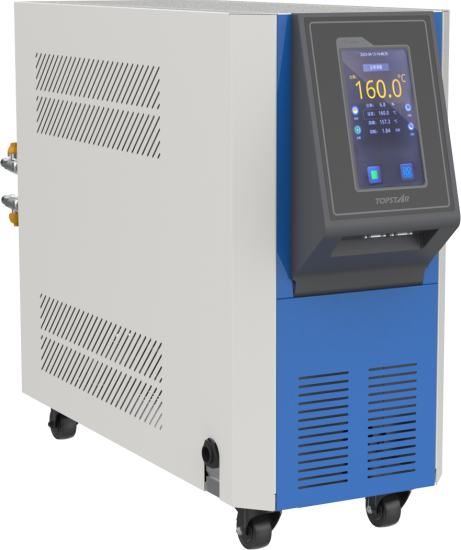
Unique heating design
In the heating design of the mould temperature controller, we use a multi-zone heating method. This design can accurately control different parts of the mold and ensure that the temperature distribution across the entire surface is uniform, which can minimize hot and cold spots. In addition, they are suitable for use in different temperature control places, whether it is for injection molding, blow molding, extrusion, or other industrial processes. The multi-zone heating design is particularly beneficial for complex molds with different thermal requirements. It allows precise temperature management in each zone, thereby optimizing the entire process and ensuring high-quality output. By using high-efficiency heating elements and multi-zone control, our systems ensure efficient use of energy and reduce the amount of electricity required to reach and maintain the required temperature.
Automatic exhaust function of mould temperature controller
The automatic exhaust function is a key component in maintaining the effectiveness of the mold temperature control system. In injection molding, the mold and its temperature control channels may trap air and other gases. This trapped air hinders heat transfer efficiency and causes inconsistent mold temperature. Our upgraded automatic exhaust function can achieve uniform and consistent temperature regulation by efficiently removing trapped air from the system. Removing trapped air ensures that the heat transfer fluid can flow freely and fully to the mold surface. Improve the heat exchange process, thereby achieving more precise and stable temperature control.
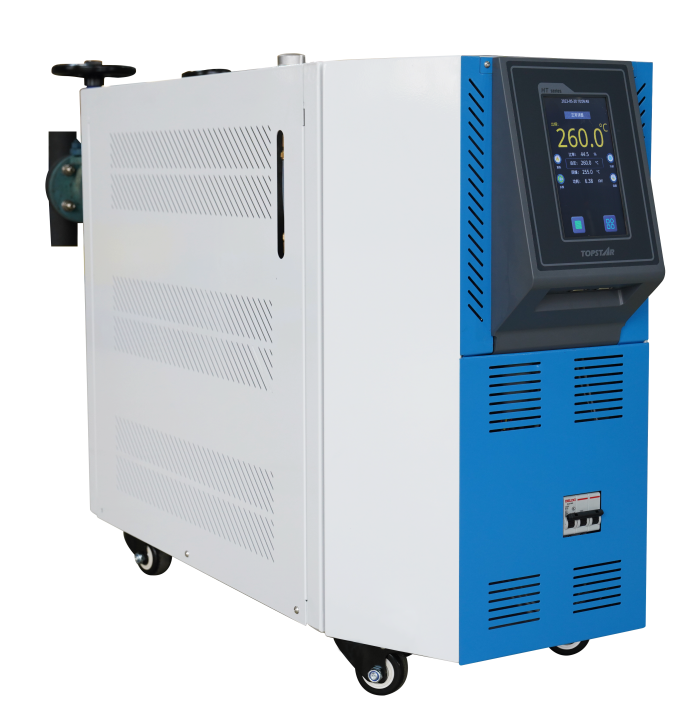
Isolation between the electrical control box and the fuselage
The isolation between the electrical control box and the fuselage is also an important upgrade in the design of our mould temperature controller. Traditionally, these components are located very close to each other, which causes heat to be transferred from the fuselage to the control box. This proximity can cause the electronic components in the control box to overheat, resulting in performance degradation and potential failure.
The upgraded mould temperature controller adopts an isolated design, using innovative technology to form a thermal barrier between the electronic control box and the fuselage. Heat transfer is reduced, providing better protection for sensitive electronic components in the control box. Through some high-performance insulating materials, heat transfer can be effectively blocked. It can ensure that the heat generated by the fuselage does not reach the control box. After the upgrade, the service life of the electronic components in the control box is extended, and the reliability of the mould temperature controller is improved.
Blowing and water return function
We have upgraded and added the blowing and water return functions to the mould temperature controller technology. The blowing function improves the cooling efficiency and control within the mould temperature controller. Directing a stream of air into the mold cavity helps promote rapid heat dissipation and accelerates the cooling process. The blowing function provides a more controlled and uniform cooling process. This helps prevent local overheating or uneven cooling, which can cause defects such as warping or shrinkage in molded parts.
The water return function is important for maintaining efficient and consistent temperature control within the mold. It ensures the effective circulation and management of cooling water used in the temperature control process. This continuous flow helps maintain a stable, consistent temperature within the mold, preventing overheating and ensuring even cooling. By maintaining a steady flow of water, the return water function optimizes the heat exchange process and maintains an optimal mold temperature.
Allowing you to get higher-quality products
The latest technology in mould temperature controllers allows you to reduce failures in injection molding. Different manufacturers can achieve higher precision, reliability, and efficiency in injection molding work through these innovations.
TRENDING POSTS
- What factors can cause delays in the injection molding process of plastic molding machine? 2024/06/07
- Exhibition Review| Topstar participates in InterPlas Thailand 2024 2024/06/07
- Star Case | Topstar helps Santong upgrade its intelligent plant 2024/06/07
- Topstar Special | National Science and Technology Workers Day 2024/06/07
HOT TOPIC
- 3 in 1 Compact Dehumidifying Dryer
- 5-axis CNC machine
- accuracy
- Air Chillers
- all electric injection molding machine
- all electric injection molding machines
- All-electric injection molding machines
- and overall production quality. Therefore
- AP-RubberPlas
- automated injection molding machine
- Automation changed engineering
- automation of injection molding robots
- auxiliary machine
- Bench Injection Molding Machine
- Cabinet dryer manufacturers
- Cabinet dryers
- chiller
- CNC Drilling Machine
- CNC Drilling Machines
- cnc engraving machine manufacturer
- cnc laser cutting machine manufacturer
- CNC machine
- CNC Machine Center
- CNC Machine for Sale
- CNC Machine Manufacturing
- CNC Machine Tool
- CNC machine tool product
- CNC Machining Center
- CNC wood carving machine
- Cooling system
- Cross-Walking Single Axis Servo Cylinder Robot
- Cross-Walking Single-Axis Servo Cylinder Robot
- Cross-Walking Three-Axis/Five-Axis Servo Driven Robot
- cross-walking three-axis/five-axis servo-driven robot
- Dehumidifier Dryer
- Dehumidifying Dryer
- delta parallel robot
- Desktop Injection Molding Machine
- Desktop injection molding machines
- Desktop Molding Machine
- desktop plastic injection machine
- Desktop Plastic Injection Molding Machine
- direct clamp injection molding machine
- Direct clamp injection molding machines
- Dosing & mixing system
- Drilling Centers
- Drying and dehumidification system
- drying and dehumidifying equipment
- Drying and Dehumidifying System
- drying system
- effective and efficient. Cabinet dryers are also used in other industries where large quantities of material need to be dried
- efficient injection molding machine
- elbow hydraulic injection molding machines
- electric injection molding machine
- electric injection molding machines
- energy-saving injection molding machine
- etc. Among injection molding robots
- exhibition
- features of CNC machine
- Feeding And Conveying System
- Five Axis Machine Center
- Fully automatic injection molding machine
- Gathering Topstar
- giant injection molding machine
- GMU-600 5-Axis Machining Center
- Granulating & Recycling System
- Heavy duty injection molding machine
- Honeycomb rotor dehumidifier
- horizontal injection molding machine
- Horizontal Injection Molding Machines
- Horizontal Injection Moulding Machine
- Horizontal Mixer manufacturer
- How The CNC Machine Works
- hybrid injection molding machine
- hydraulic injection molding machine
- Hydraulic Injection Molding Machines
- in this article
- Industrial robot
- Industrial Robot Chinese brand
- industrial robot parts
- industrial robot supplier
- Industrial robots
- Industry Chain
- Injection Manipulator
- injection mold machines
- Injection molding
- Injection molding automation
- Injection Molding Automation Solution
- injection molding dryer
- Injection molding equipment
- injection molding hopper dryer
- Injection molding machine
- injection molding machine brand
- Injection Molding Machine Factory
- Injection Molding Machine Manufacture
- Injection molding machine manufacturer
- injection molding machine manufacturers
- Injection molding machine procurement
- injection molding machine robotic arm
- injection molding machine with a robot
- Injection molding machines
- injection molding material dehumidifying
- injection molding plant
- Injection Molding Robot
- injection molding robot arm
- Injection molding robot automation
- Injection molding robotic arm
- injection molding robots
- Injection Moulding Robots
- Injection Robot
- Injection robot arm
- Injection robot manufacturer
- Injection robot wholesale
- injection robots
- intelligent injection molding machines
- Introducing Injection Robot
- It is the best choice for drying large quantities of material at once. Cabinetmakers use these machines because they are fast
- large injection molding machine
- Learn what industrial automation and robotics is
- low speed sound-proof granulator
- machine plastic molding
- make sure to add some! Improvements (2) Keyphrase in introduction: Your keyphrase or its synonyms appear in the first paragraph of the copy
- manipulator machine
- manufacturing
- micro injection molding machine
- middle speed granulator
- Mini CNC machine manufacturers.
- Mold Temperature Control System
- mold temperature controller
- molding material Dehumidifying System
- mould temperature controller
- mould temperature controllers
- New electric injection molding machine
- nitrogen dryer manufacturer
- nitrogen dryer system manufacturer
- Oil type mold temperature controller
- open day
- Outbound links: No outbound links appear in this page. Add some! Images: No images appear on this page. Add some! Internal links: No internal links appear in this page
- PET Preform injection molding
- phone case maker machine
- phone case making machine
- plastic bottle making machine
- plastic bottle manufacturing
- plastic bucket making machine
- plastic bucket manufacturing
- Plastic chair making machine
- plastic forming equipment
- plastic hopper dryer
- plastic injection machine
- plastic injection machines
- plastic injection molding
- Plastic injection molding equipment
- Plastic injection molding machine
- Plastic Injection Molding Machines
- plastic injection robot
- Plastic Molding machine
- Plastic Molding Machines
- plastic molding press
- plastic phone case making machine
- plastic-molding machine
- powerful granulator
- Powerful Type Sound-Proof Granulator
- production of plastic seats
- Robot injection molding
- robot injection molding machine
- robot manufacturing companies
- Robotic arm for injection molding machine
- robotic injection molding machines
- robotics in injection molding
- SCARA robot
- SCARA robots
- Service-oriented manufacturing
- Servo Cylinder Robot
- servo driven robot
- Servo Driven Robots
- servo injection robots
- Servo-Driven Robot
- Setup of injection machine
- Silicone Injection Molding Machine
- six-axis industrial robot
- Stainless Hopper Dryer
- Stainless Hopper Dryers
- star club
- swing arm robot
- the choice between servo-driven robots and hydraulic robots will have a certain impact on efficiency
- the most popular injection molding machine
- the type of injection molding robot
- toggle clamp injection molding machine
- Toggle Hydraulic Injection Molding Machines
- toggle injection molding machine
- Top 10 brands of injection robots
- Topstar
- Topstar Engineering
- Topstar Industrial Robots
- Topstar injection molding intelligent
- Topstar Scara Robots
- Useful Injection molding machine
- Vertical machining centers
- volumetric type blender
- water chiller
- water chillers
- water distributor
- Water Type MoldTemperature Controller
- We often face choices when performing injection molding. We will choose the type of injection molding machine
- wholesale of injection molding machines
- x carve CNC