What are the development and future prospects of injection molding machines?
2025/04/04 By Topstar
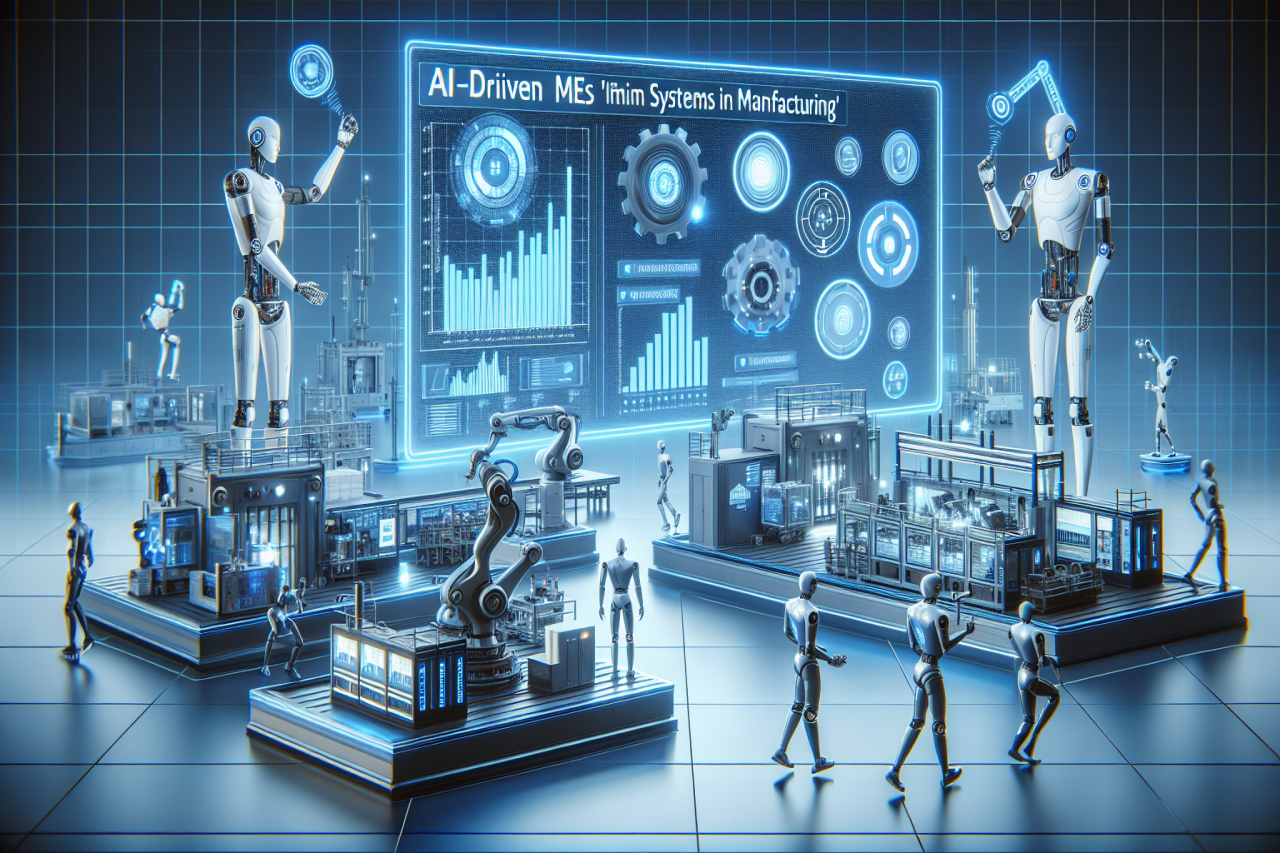
Injection molding machines are at the heart of mass injection molding production in automotive, consumer goods, electronics, and medical devices. The current state of intelligence in injection molding machines is driven by rapid technological advancement, digital integration, and evolving process control. Modern injection molding machines are no longer mechanical devices; they have evolved into equipment integrating diversified technologies, various injection molding processes, and real-time data analysis. This shift toward intelligence has significantly improved injection molding production’s overall efficiency and accuracy. The current state of injection molding machines reflects the broader trend of industrial intelligence and digital transformation. Many manufacturers are increasingly adopting MES and integrating it with machine control to improve process transparency and traceability. These digital systems provide a comprehensive view of production performance, helping companies identify bottlenecks and optimize operations.
Reduce costs through process optimization of injection molding machines
With the continuous optimization and refined control of the process, Topstar’s all-in-one injection molding process machine can further reduce production costs. By optimizing the production process, manufacturers can reduce production costs. The unified control system on the injection molding machine can accurately adjust the temperature, pressure, and injection speed. This enables the entire injection molding production line to operate closer to optimal conditions, reducing the risk of scrapping and rework caused by material degradation or defects in one link. In addition, with a unified and integrated control system, operators can quickly correct anomalies to ensure that each cycle meets high-quality standards. This design is not only an optimization of the injection molding machine process but also takes into account the seamless connection between peripheral equipment and the comprehensive factors of “man-machine-material-method-environment” and other links to improve overall production efficiency and management level.
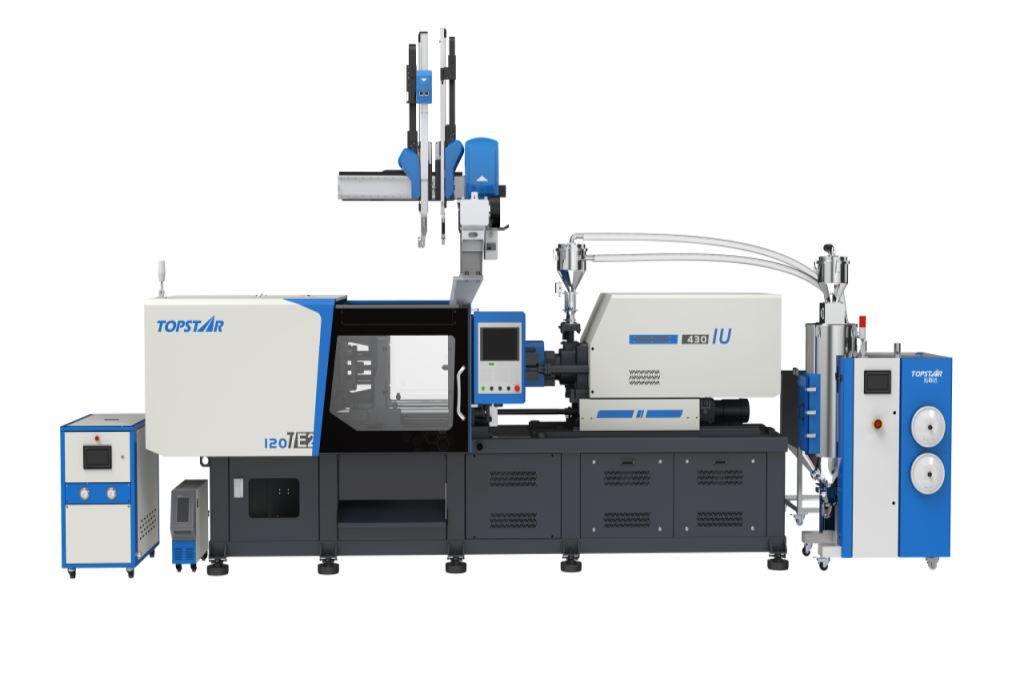
Intelligent injection molding machine: the combination of artificial intelligence and MES integration
Future injection molding machines will tend to be more intelligent and digital, combining artificial intelligence and Topstar’s MES system to achieve more efficient, precise and sustainable production. Integrate artificial intelligence with MES for end-to-end traceability and decision-making. MES systems can bridge the gap between production workshops and higher-level business analysis. They provide real-time insights into every stage of the injection molding process, enabling operators to monitor machine performance, detect anomalies and make data-driven decisions. When used with AI algorithms, these digital tools can predict maintenance needs, adjust process parameters in real-time, and even predict potential production problems before they occur.
This level of intelligence can significantly improve production efficiency and reliability while reducing downtime. For example, suppose the system detects a drop in the viscosity of recycled PET. In that case, the AI will cross-reference the MES data to immediately adjust the barrel temperature and screw speed to maintain part consistency.
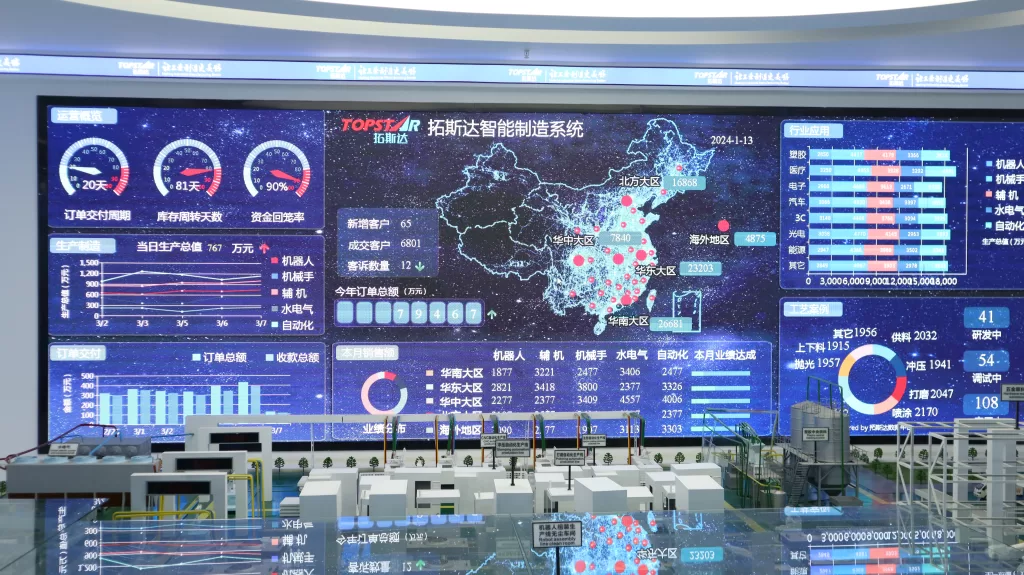
Modular design: Customization to meet various needs
Injection molding machines will be modular and customized according to customer needs. Because it is not difficult to find that each industry and application field has different requirements for injection molding machines, customized design can meet customer-specific production needs and provide more flexible and scalable solutions.
Compared with traditional fixed systems, modularity can break down injection molding machines into standardized modules, and manufacturers can easily upgrade or replace individual components. In addition, manufacturers can customize modular systems to meet the unique needs of different industries. They can fine-tune customizable injection molding machines to achieve the precise performance characteristics required for a specific production process. This includes adjusting cycle time, temperature control and pressure settings, which are key to maintaining product quality. In addition, manufacturers can integrate modular and customized systems with digital control systems, making it easier to monitor and adjust operations in real time.
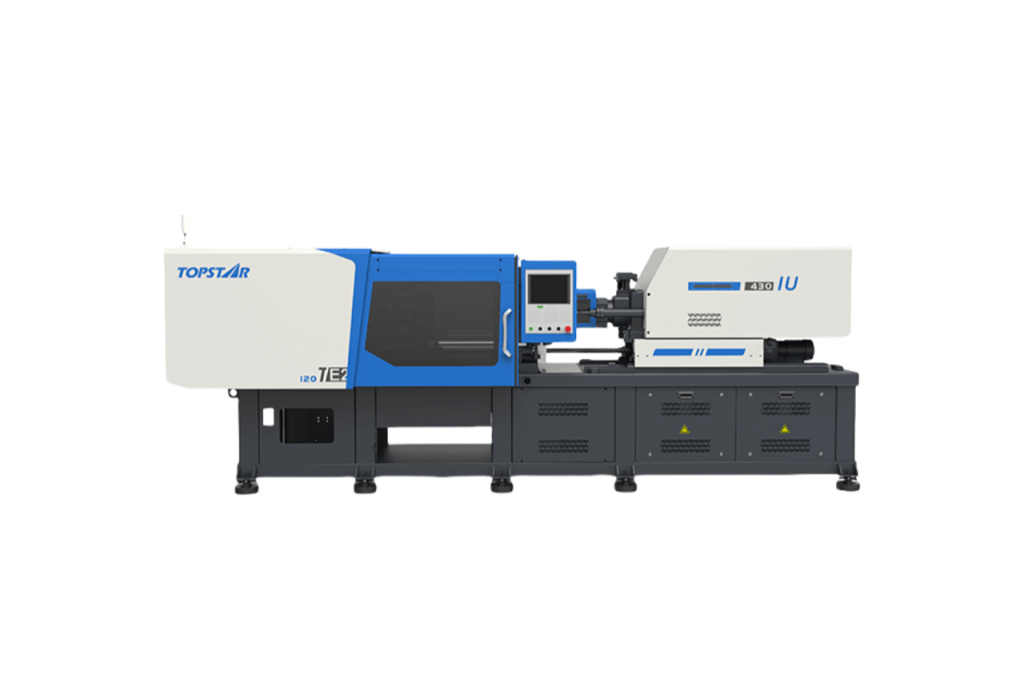
Achieve more reliable and efficient energy-saving production.
Efficiency not only means faster cycles but also means doing more with fewer resources. In the past, the controller on the traditional electric injection molding machine would have a communication delay of several milliseconds, which would cause uneven quality control when precision injection molding products were formed. Now, we generate the operation curve by ourselves through the control method of discrete intelligent drive, which reduces the impact of communication delay on the high-speed operation of the servo motor, realizes real-time control of the servo motor, and improves the accuracy of position, speed and pressure control. In the future, electric drive injection molding will become more flexible, and manufacturers will achieve more precise control of the injection molding process, providing customers with more stable, safe, and reliable energy-saving injection molding machines.
We will build an ecosystem of “intelligent hardware platform driven by core technology” to make enterprise operators more worry-free, managers more relaxed, and operations and production faster to improve customer enterprises.
Make injection molding production simpler, more intelligent and more efficient.
In the future, several key pillars will be involved in injection molding machines. First, we will improve and optimize the injection molding machine process to reduce production costs further. By combining real-time monitoring, predictive maintenance, and artificial intelligence-driven process optimization, we can achieve operational efficiency and bring considerable economic benefits to customers. At the same time, we will also combine our proprietary MES system with cutting-edge technologies such as AI and IoT to develop equipment that can learn from its operating environment, automatically adjust parameters and optimize performance in real-time. Modularization and customization are used to meet the specific production needs of each industry, making injection molding production simpler, intelligent and more efficient.
TRENDING POSTS
- What factors can cause delays in the injection molding process of plastic molding machine? 2025/04/04
- Exhibition Review| Topstar participates in InterPlas Thailand 2024 2025/04/04
- Star Case | Topstar helps Santong upgrade its intelligent plant 2025/04/04
- Topstar Special | National Science and Technology Workers Day 2025/04/04
HOT TOPIC
- 3 in 1 Compact Dehumidifying Dryer
- 5-axis CNC machine
- accuracy
- Air Chillers
- all electric injection molding machine
- all electric injection molding machines
- All-electric injection molding machines
- and overall production quality. Therefore
- AP-RubberPlas
- automated injection molding machine
- Automation changed engineering
- automation of injection molding robots
- auxiliary machine
- Bench Injection Molding Machine
- Cabinet dryer manufacturers
- Cabinet dryers
- chiller
- CNC Drilling Machine
- CNC Drilling Machines
- cnc engraving machine manufacturer
- cnc laser cutting machine manufacturer
- CNC machine
- CNC Machine Center
- CNC Machine for Sale
- CNC Machine Manufacturing
- CNC Machine Tool
- CNC machine tool product
- CNC Machining Center
- CNC wood carving machine
- Cooling system
- Cross-Walking Single Axis Servo Cylinder Robot
- Cross-Walking Single-Axis Servo Cylinder Robot
- Cross-Walking Three-Axis/Five-Axis Servo Driven Robot
- cross-walking three-axis/five-axis servo-driven robot
- Dehumidifier Dryer
- Dehumidifying Dryer
- delta parallel robot
- Desktop Injection Molding Machine
- Desktop injection molding machines
- Desktop Molding Machine
- desktop plastic injection machine
- Desktop Plastic Injection Molding Machine
- direct clamp injection molding machine
- Direct clamp injection molding machines
- Dosing & mixing system
- Drilling Centers
- Drying and dehumidification system
- drying and dehumidifying equipment
- Drying and Dehumidifying System
- drying system
- effective and efficient. Cabinet dryers are also used in other industries where large quantities of material need to be dried
- efficient injection molding machine
- elbow hydraulic injection molding machines
- electric injection molding machine
- electric injection molding machines
- energy-saving injection molding machine
- etc. Among injection molding robots
- exhibition
- features of CNC machine
- Feeding And Conveying System
- Five Axis Machine Center
- Fully automatic injection molding machine
- Gathering Topstar
- giant injection molding machine
- GMU-600 5-Axis Machining Center
- Granulating & Recycling System
- Heavy duty injection molding machine
- Honeycomb rotor dehumidifier
- horizontal injection molding machine
- Horizontal Injection Molding Machines
- Horizontal Injection Moulding Machine
- Horizontal Mixer manufacturer
- How The CNC Machine Works
- hybrid injection molding machine
- hydraulic injection molding machine
- Hydraulic Injection Molding Machines
- in this article
- Industrial robot
- Industrial Robot Chinese brand
- industrial robot parts
- industrial robot supplier
- Industrial robots
- Industry Chain
- Injection Manipulator
- injection manipulator robot
- injection mold machines
- Injection molding
- Injection molding automation
- Injection Molding Automation Solution
- injection molding dryer
- Injection molding equipment
- injection molding hopper dryer
- Injection molding machine
- injection molding machine brand
- Injection Molding Machine Factory
- Injection Molding Machine Manufacture
- Injection molding machine manufacturer
- injection molding machine manufacturers
- Injection molding machine procurement
- injection molding machine robotic arm
- injection molding machine with a robot
- Injection molding machines
- injection molding material dehumidifying
- injection molding plant
- Injection Molding Robot
- injection molding robot arm
- Injection molding robot automation
- Injection molding robotic arm
- injection molding robots
- Injection Moulding Robots
- Injection Robot
- Injection robot arm
- Injection robot manufacturer
- Injection robot wholesale
- injection robots
- intelligent injection molding machines
- Introducing Injection Robot
- It is the best choice for drying large quantities of material at once. Cabinetmakers use these machines because they are fast
- large injection molding machine
- Learn what industrial automation and robotics is
- linear robot
- low speed sound-proof granulator
- machine plastic molding
- make sure to add some! Improvements (2) Keyphrase in introduction: Your keyphrase or its synonyms appear in the first paragraph of the copy
- manipulator machine
- manufacturing
- micro injection molding machine
- middle speed granulator
- Mini CNC machine manufacturers.
- Mold Temperature Control System
- mold temperature controller
- molding material Dehumidifying System
- mould temperature controller
- mould temperature controllers
- New electric injection molding machine
- nitrogen dryer manufacturer
- nitrogen dryer system manufacturer
- Oil type mold temperature controller
- open day
- Outbound links: No outbound links appear in this page. Add some! Images: No images appear on this page. Add some! Internal links: No internal links appear in this page
- PET Preform injection molding
- phone case maker machine
- phone case making machine
- plastic bottle making machine
- plastic bottle manufacturing
- plastic bucket making machine
- plastic bucket manufacturing
- Plastic chair making machine
- plastic forming equipment
- plastic hopper dryer
- plastic injection machine
- plastic injection machines
- plastic injection molding
- Plastic injection molding equipment
- Plastic injection molding machine
- Plastic Injection Molding Machines
- plastic injection robot
- Plastic Molding machine
- Plastic Molding Machines
- plastic molding press
- plastic phone case making machine
- plastic-molding machine
- powerful granulator
- Powerful Type Sound-Proof Granulator
- production of plastic seats
- Robot injection molding
- robot injection molding machine
- robot manufacturing companies
- Robotic arm for injection molding machine
- robotic injection molding machines
- robotics in injection molding
- SCARA robot
- SCARA robots
- Service-oriented manufacturing
- Servo Cylinder Robot
- servo driven robot
- Servo Driven Robots
- servo injection robots
- Servo-Driven Robot
- Setup of injection machine
- Silicone Injection Molding Machine
- six-axis industrial robot
- Stainless Hopper Dryer
- Stainless Hopper Dryers
- star club
- swing arm robot
- the choice between servo-driven robots and hydraulic robots will have a certain impact on efficiency
- the most popular injection molding machine
- the type of injection molding robot
- toggle clamp injection molding machine
- Toggle Hydraulic Injection Molding Machines
- toggle injection molding machine
- Top 10 brands of injection robots
- Topstar
- Topstar Engineering
- Topstar Industrial Robots
- Topstar injection molding intelligent
- Topstar Scara Robots
- Useful Injection molding machine
- Vertical machining centers
- volumetric type blender
- water chiller
- water chillers
- water distributor
- Water Type MoldTemperature Controller
- We often face choices when performing injection molding. We will choose the type of injection molding machine
- wholesale of injection molding machines
- x carve CNC