What are the advantages of a large injection molding machine?
2022/12/02 By Topstar
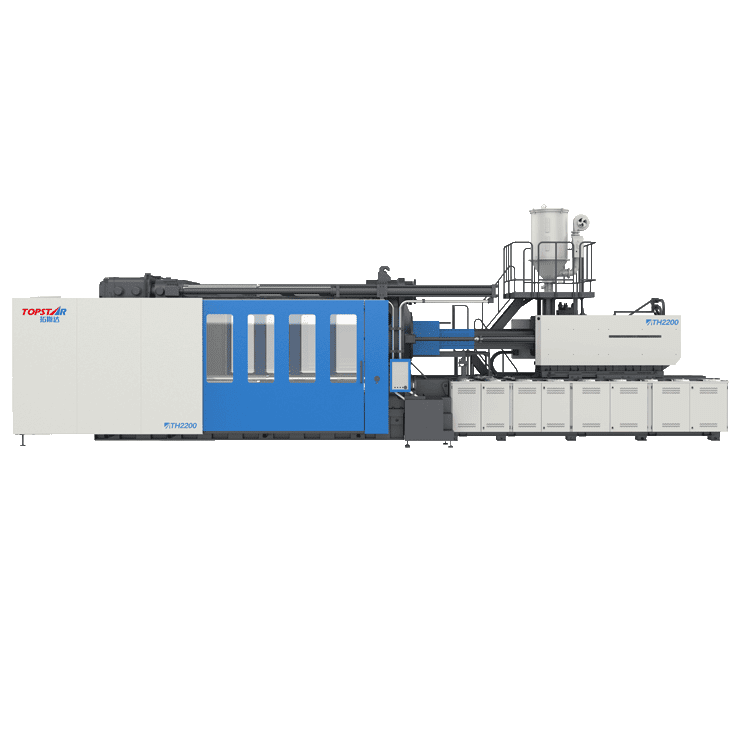
Injection molding is one of the most widely used manufacturing processes. Large injection molding machine is becoming increasingly popular for large-scale plastic products because they can produce more significant, complex parts with greater precision and consistency. This blog post will explore the significant advantages of large injection molding machines and how they can benefit plastic product manufacturers. Whether you are manufacturing heavy parts or complex designs, the features used in Topstar’s large injection molding machines can streamline production, improve quality, and increase overall efficiency.
Large injection molding machine use multi-cylinder direct-pressure clamping
One of the outstanding features of large injection molding machines is their use of a multi-cylinder direct pressure clamping system. This design minimizes the deformation of the machine’s platen, ensuring that the mold maintains parallel pressure across the entire surface. This is critical to ensuring high molding accuracy, especially for complex or large parts. The use of multiple cylinders allows for a more even distribution of force, helping to prevent defects such as warping, sink marks, or uneven molding.
Adopting a multi-cylinder direct pressure clamping system benefits manufacturers by increasing stability and uniformity in the injection process. This clamping method helps maintain precise alignment of the mold, and for manufacturers producing precision parts or large, complex designs, this feature can significantly improve overall product quality. In addition, the multi-cylinder design ensures that overall deformation is minimized even when tremendous forces are applied to the mold during the injection process.
Dual/Quad Injection: Operational Stability and Sensitivity
Another key advantage of the large injection molding machines offered by Topstar is the use of dual or even quad injection mechanisms. This setup offers various benefits, such as stable injection, sensitive movement, and high precision. These injection systems can more precisely control the flow of molten plastic into the mold, thereby reducing problems such as overfilling, underfilling, or inconsistent material distribution.
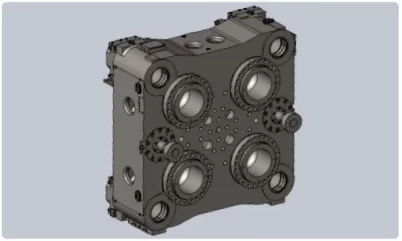
Dual or quad injection molding helps optimize the flow of plastic during the molding process, providing stable injection and preventing pressure or speed fluctuations. This means that the machine can achieve more consistent results with fewer defects, ensuring that the final product meets the design specifications with greater precision. In addition, the multi-cylinder injection system has a higher sensitivity during the injection process. This allows for finer adjustments during the injection process, which is critical when using advanced materials, thin-walled parts, or complex mold cavities.
Linear guide motion adopted by large injection molding machine
Another important feature of large injection molding machines is the use of linear guide motion. Linear guides are an important component in ensuring smooth and precise movement of the injection unit and mold carrier. These guides reduce friction, making the movement during the injection process more stable and sensitive.
Compared to traditional sliding guides, linear guides offer greater precision and control. The machine can move with greater precision and stability even under heavy loads, and the smoothness of the movement also minimizes wear on machine components, thereby extending service life and reducing maintenance requirements.
In addition, linear guide movement increases the overall speed of the injection molding process because it is more responsive and requires less force to start. This means that large injection molding machines equipped with linear guides are more precise and efficient, resulting in shorter cycle times and higher output. At the same time, being able to move the mold with precision allows for better control of the molding process, especially when sensitive or highly delicate parts are involved.
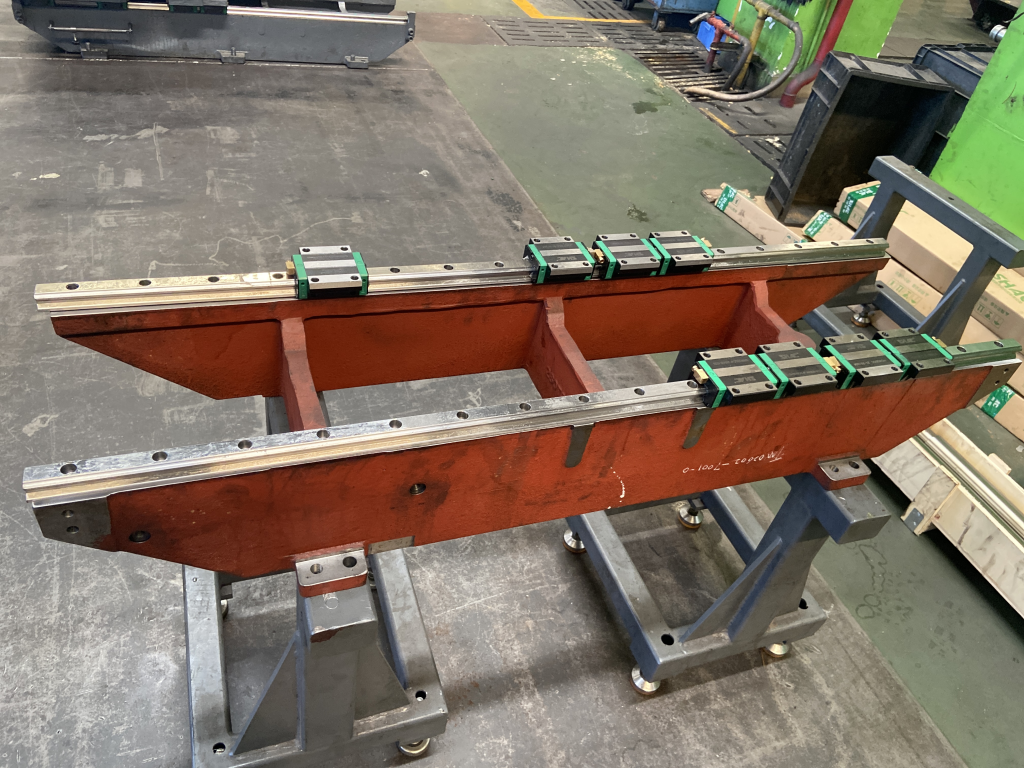
Patented seal ring structure
Sealing is one of the most critical aspects of any injection molding machine, and large injection molding machines have a unique advantage in this regard due to their patented seal ring structure. These seal rings are designed to ensure high sealing reliability and prevent leakage of molten plastic during the injection molding process. This is particularly important for large-scale production because the amount of material injected is large, and the pressure applied is also high.
Using specialized seal rings helps extend the machine’s service life and reduce wear on sealing components. In addition to improving the reliability of the sealing process, these patented seals also help reduce maintenance costs and downtime, ensuring that the machine can run for a long time. The reliable seal provided by these structures ensures that manufacturers can achieve consistent, high-quality results while minimizing the risk of material loss or contamination. The patented seal structure keeps the mold cavity intact and allows the plastic injection process to occur under optimal conditions in applications that require high precision.
Large plate spacing and high plate rigidity
Another significant advantage of large injection molding machines is their large plate spacing and high rigidity. This design feature enables the machine to handle deep cavity molds, which is critical for producing large or complex parts requiring deeper mold cavities. The increased plate spacing also facilitates the use of larger and heavier molds, making it easier to produce oversized products that standard injection molding machines cannot handle.
High plate rigidity ensures that the mold remains secure during the injection process, preventing deformation and maintaining the part’s dimensional accuracy. This rigidity is significant when molding large, heavy parts requiring high clamping force to hold the mold in place. For manufacturers producing large products or complex designs with different thicknesses, the ability to accommodate deep cavity molds with constant pressure and minimal deformation is a key advantage.
Transforming Injection Molding Production of Large Products
Large injection molding machines offer various advantages to manufacturers seeking to produce high-quality plastic parts with precision, speed, and efficiency. From improved molding accuracy and stable injection to increased productivity and improved sealing reliability, these machines can transform your production line.
TRENDING POSTS
- What factors can cause delays in the injection molding process of plastic molding machine? 2022/12/02
- Exhibition Review| Topstar participates in InterPlas Thailand 2024 2022/12/02
- Star Case | Topstar helps Santong upgrade its intelligent plant 2022/12/02
- Topstar Special | National Science and Technology Workers Day 2022/12/02
HOT TOPIC
- 3 in 1 Compact Dehumidifying Dryer
- 5-axis CNC machine
- accuracy
- Air Chillers
- all electric injection molding machine
- All-electric injection molding machines
- and overall production quality. Therefore
- AP-RubberPlas
- automated injection molding machine
- Automation changed engineering
- automation of injection molding robots
- auxiliary machine
- Bench Injection Molding Machine
- Cabinet dryer manufacturers
- Cabinet dryers
- CNC Drilling Machine
- CNC Drilling Machines
- cnc engraving machine manufacturer
- cnc laser cutting machine manufacturer
- CNC machine
- CNC Machine Center
- CNC Machine for Sale
- CNC Machine Manufacturing
- CNC Machine Tool
- CNC machine tool product
- CNC Machining Center
- CNC wood carving machine
- Cooling system
- Cross-Walking Single Axis Servo Cylinder Robot
- Cross-Walking Single-Axis Servo Cylinder Robot
- Cross-Walking Three-Axis/Five-Axis Servo Driven Robot
- cross-walking three-axis/five-axis servo-driven robot
- Dehumidifier Dryer
- delta parallel robot
- Desktop Injection Molding Machine
- Desktop injection molding machines
- Desktop Molding Machine
- desktop plastic injection machine
- Desktop Plastic Injection Molding Machine
- direct clamp injection molding machine
- Direct clamp injection molding machines
- Dosing & mixing system
- Drilling Centers
- Drying and dehumidification system
- drying and dehumidifying equipment
- Drying and Dehumidifying System
- drying system
- effective and efficient. Cabinet dryers are also used in other industries where large quantities of material need to be dried
- efficient injection molding machine
- elbow hydraulic injection molding machines
- electric injection molding machine
- electric injection molding machines
- etc. Among injection molding robots
- exhibition
- features of CNC machine
- Feeding And Conveying System
- Five Axis Machine Center
- Fully automatic injection molding machine
- Gathering Topstar
- giant injection molding machine
- GMU-600 5-Axis Machining Center
- Granulating & Recycling System
- Heavy duty injection molding machine
- Honeycomb rotor dehumidifier
- horizontal injection molding machine
- Horizontal Injection Molding Machines
- Horizontal Injection Moulding Machine
- Horizontal Mixer manufacturer
- How The CNC Machine Works
- hybrid injection molding machine
- hydraulic injection molding machine
- Hydraulic Injection Molding Machines
- in this article
- Industrial robot
- Industrial Robot Chinese brand
- industrial robot parts
- industrial robot supplier
- Industrial robots
- Industry Chain
- Injection Manipulator
- Injection molding
- Injection molding automation
- Injection Molding Automation Solution
- injection molding dryer
- Injection molding equipment
- injection molding hopper dryer
- Injection molding machine
- injection molding machine brand
- Injection Molding Machine Factory
- Injection Molding Machine Manufacture
- Injection molding machine manufacturer
- injection molding machine manufacturers
- Injection molding machine procurement
- injection molding machine robotic arm
- injection molding machine with a robot
- Injection molding machines
- injection molding material dehumidifying
- injection molding plant
- Injection Molding Robot
- injection molding robot arm
- Injection molding robot automation
- Injection molding robotic arm
- injection molding robots
- Injection Moulding Robots
- Injection Robot
- Injection robot arm
- Injection robot manufacturer
- Injection robot wholesale
- injection robots
- Introducing Injection Robot
- It is the best choice for drying large quantities of material at once. Cabinetmakers use these machines because they are fast
- large injection molding machine
- Learn what industrial automation and robotics is
- low speed sound-proof granulator
- machine plastic molding
- make sure to add some! Improvements (2) Keyphrase in introduction: Your keyphrase or its synonyms appear in the first paragraph of the copy
- manipulator machine
- manufacturing
- micro injection molding machine
- middle speed granulator
- Mini CNC machine manufacturers.
- Mold Temperature Control System
- mold temperature controller
- molding material Dehumidifying System
- mould temperature controller
- mould temperature controllers
- New electric injection molding machine
- nitrogen dryer manufacturer
- nitrogen dryer system manufacturer
- Oil type mold temperature controller
- open day
- Outbound links: No outbound links appear in this page. Add some! Images: No images appear on this page. Add some! Internal links: No internal links appear in this page
- PET Preform injection molding
- phone case maker machine
- phone case making machine
- plastic bottle making machine
- plastic bottle manufacturing
- plastic bucket making machine
- plastic bucket manufacturing
- Plastic chair making machine
- plastic forming equipment
- plastic hopper dryer
- plastic injection machine
- plastic injection machines
- plastic injection molding
- Plastic injection molding equipment
- Plastic injection molding machine
- Plastic Injection Molding Machines
- plastic injection robot
- Plastic Molding machine
- Plastic Molding Machines
- plastic molding press
- plastic phone case making machine
- plastic-molding machine
- powerful granulator
- Powerful Type Sound-Proof Granulator
- production of plastic seats
- Robot injection molding
- robot injection molding machine
- robot manufacturing companies
- Robotic arm for injection molding machine
- robotic injection molding machines
- robotics in injection molding
- SCARA robot
- Service-oriented manufacturing
- Servo Cylinder Robot
- servo driven robot
- Servo Driven Robots
- servo injection robots
- Servo-Driven Robot
- Setup of injection machine
- Silicone Injection Molding Machine
- six-axis industrial robot
- Stainless Hopper Dryer
- Stainless Hopper Dryers
- star club
- swing arm robot
- the choice between servo-driven robots and hydraulic robots will have a certain impact on efficiency
- the most popular injection molding machine
- the type of injection molding robot
- toggle clamp injection molding machine
- Toggle Hydraulic Injection Molding Machines
- toggle injection molding machine
- Top 10 brands of injection robots
- Topstar
- Topstar Engineering
- Topstar Industrial Robots
- Topstar injection molding intelligent
- Topstar Scara Robots
- Useful Injection molding machine
- Vertical machining centers
- volumetric type blender
- water distributor
- Water Type MoldTemperature Controller
- We often face choices when performing injection molding. We will choose the type of injection molding machine
- wholesale of injection molding machines
- x carve CNC