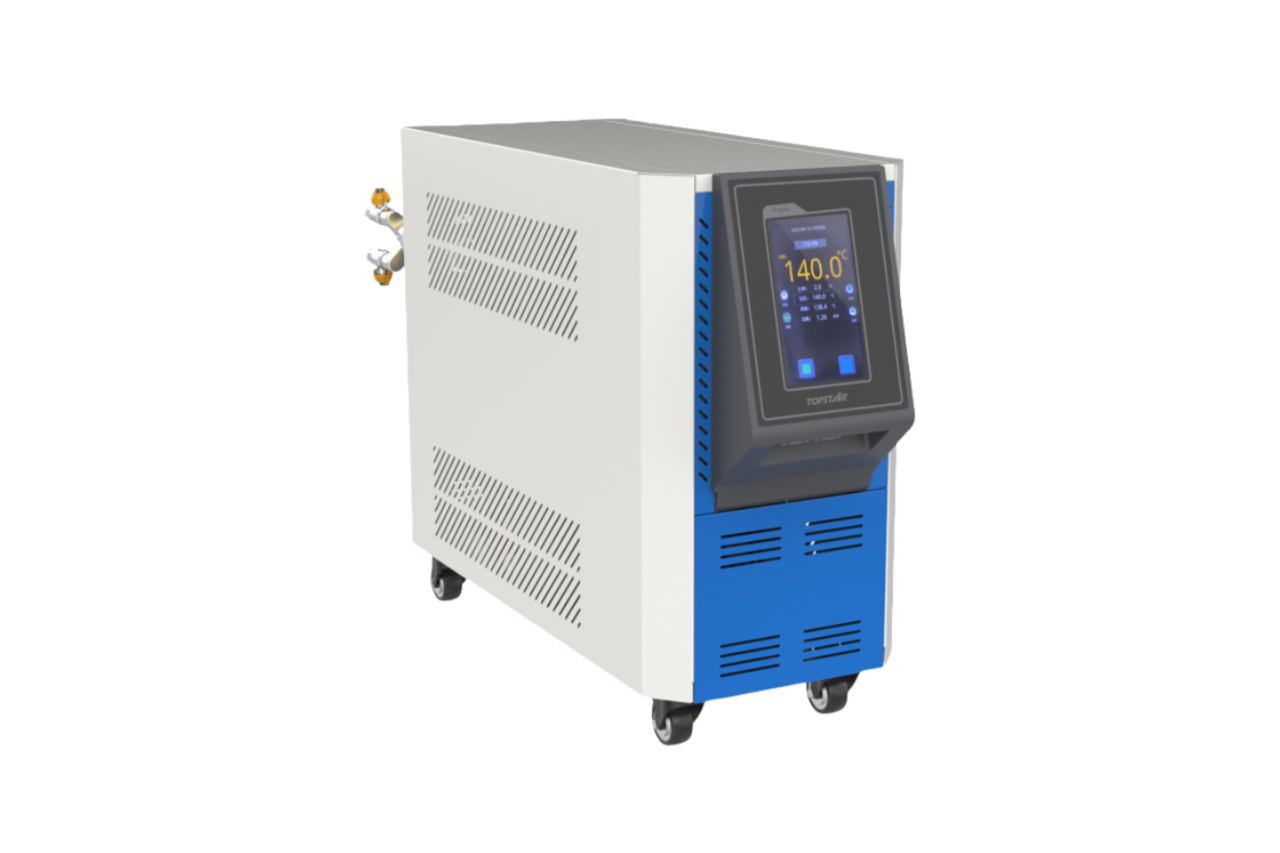
Injection molding is one of the most widespread manufacturing technologies today, and it is used to produce a wide variety of plastic products, ranging from small household products to large home appliances. When the injection molding process officially starts, the plastic temperature needs to be controlled, and the mould temperature controller can control the temperature well during the entire process. This temperature-controlled process begins with the melting of the plastic. Manufacturing takes place after the molten plastic cools. This guide will introduce you to the impact of mould temperature controllers on injection molding.
Effect of temperature on product quality
One factor that affects product quality during the entire injection molding process is mold temperature. As the surface temperature of the mold increases, the appearance quality of the product will also change. Generally speaking, improving the quality of injection-molded products requires increasing the mold temperature during the injection process to reduce the output thickness and insertion pressure. It’s essential to control the temperature effectively during the injection moulding process.
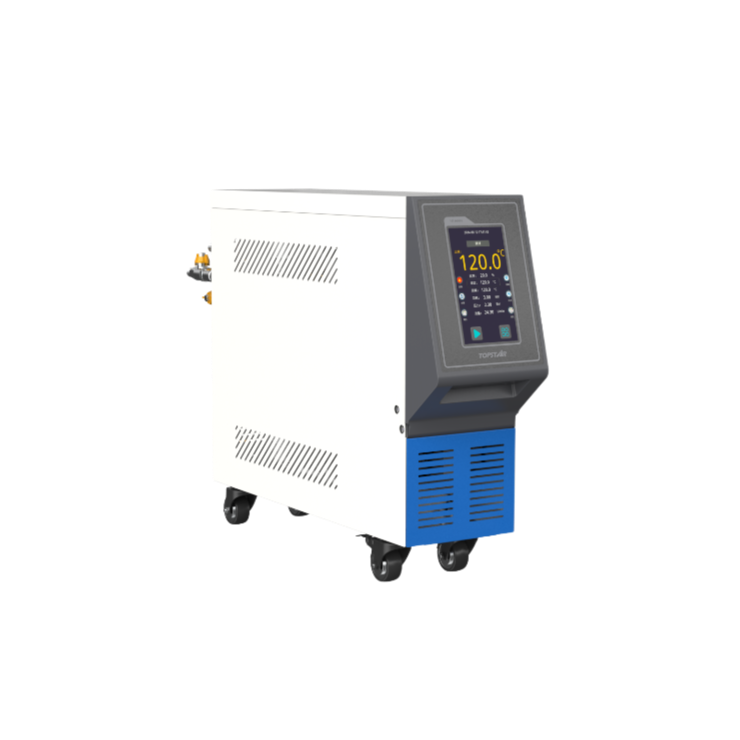
Temperature control via mould temperature controller
Mould temperature controllers work by circulating water through channels in or around the mold. Heating or cooling water to a specific temperature ensures consistent heating conditions during the molding process. At the same time, they can precisely control mold temperature and can quickly switch between heating and cooling, making them suitable for molds that require different temperature stages within a single cycle. Modern mould temperature controllers also function as automatic cooling during idle periods.
Why is a mould temperature controller necessary?
Precise mold temperature management can affect the quality and appearance of the final product, where the temperature of the mold can directly affect the viscosity of the plastic melt. A properly heated mould ensures that the plastic flows evenly and completely fills the mould cavity. If the mould is too cold, the material may solidify prematurely, resulting in short shots. Conversely, an overheated mold may result in excessive packing pressure or extended cooling times.
Uniform mold temperature is essential for reducing internal stress within molded parts. Differences in cooling can cause tension and compression within the plastic, leading to warping, shrinkage, or structural failure. They can also lead to other related problems, such as surface quality defects and short mold life.
Why use a Topstar mould temperature controller?
To meet the needs of industry customers for intelligent and digital upgrades, solve temperature control problems in injection moulding production, and improve product yield, Topstar launched the fourth-generation mould temperature controller. The new generation of mould temperature controllers uses a stainless steel frame structure to upgrade the copper heater because impurities in the water have a lower tendency to adhere to the copper surface and are not easy to scale. At the same time, copper’s ductility and thermal conductivity are superior. It increases the service life by 40% and the efficiency by 10%, and operators can use it effectively even with poor water quality.
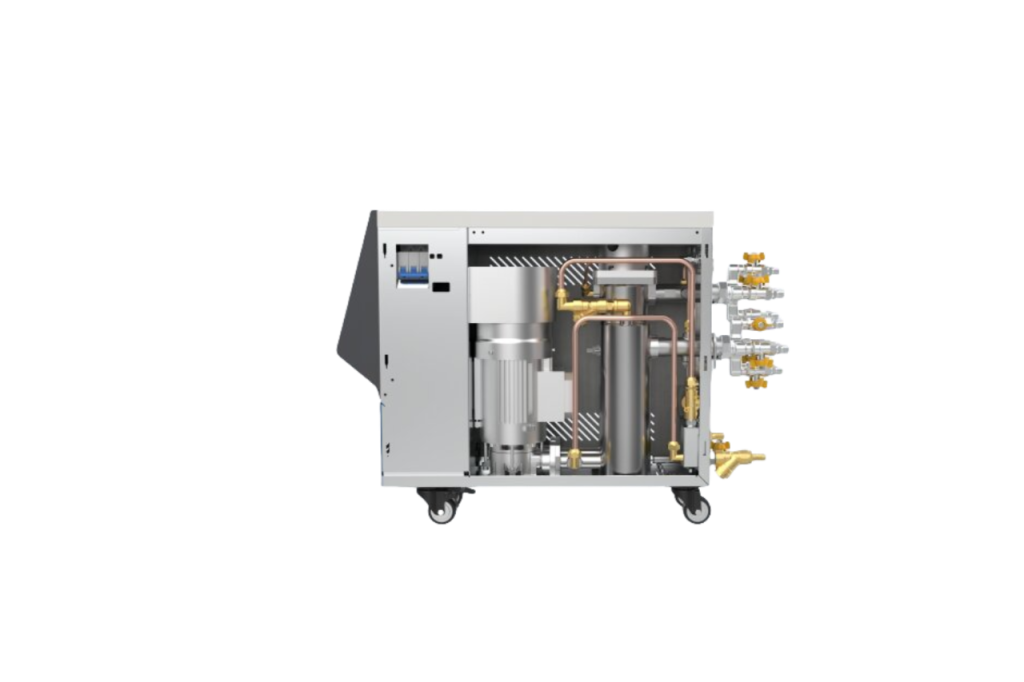
In the 120℃ standard water-type mould temperature controller, we have a standard pressure detector with a detection accuracy of 1%. The upper limit of the use temperature can be adjusted according to different water inlet pressures to ensure the mould temperature controller’s regular use when the water inlet pressure is low. This solves the problems of unstable inlet pressure and low water inlet pressure affecting the yield rate.
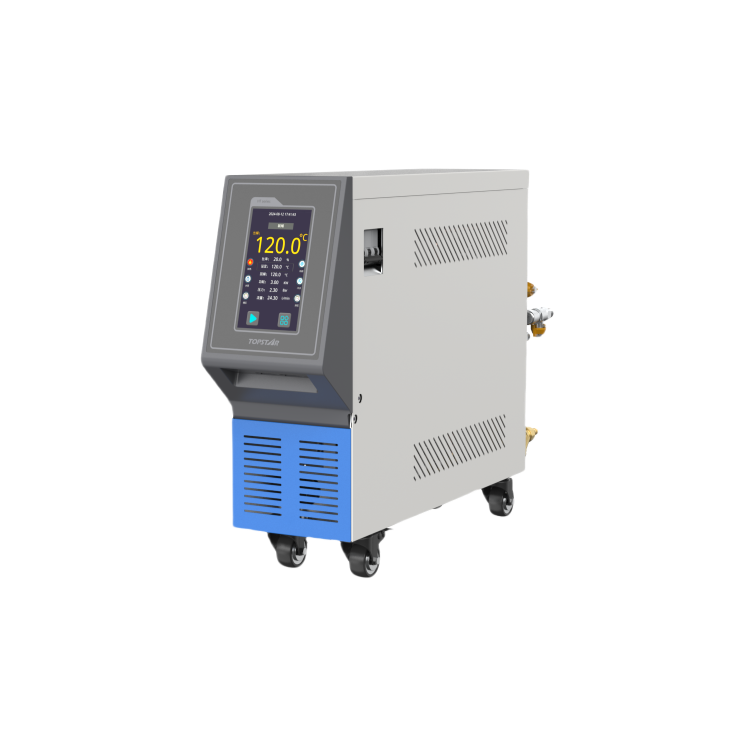
Intelligent algorithm makes temperature control more accurate.
In addition, the fourth-generation mould temperature controller also has forced cooling and timed appointment power on and off functions. Continuously opening the cooling solenoid valve reduces the mould temperature by about 10 minutes, increasing work efficiency by 10% and dramatically shortening the time required for a mould change. To better ensure that the mould has precise temperature control accuracy, Topstar uses the latest PID temperature control algorithm to improve the temperature control efficiency by 10% and ensure temperature uniformity. At the same time, the hardware part uses solid-state relays for temperature control, with a response time of 0.1s, to ensure that the temperature fluctuates within ±0.1℃ and ensures product yield.
Applications of Mould temperature controller
Mold temperature controllers are crucial in many manufacturing processes. They play a key role in plastic injection moulding, rubber moulding, composite moulding, die casting, and blow moulding.
For die-casting processes, Topstar’s 320° oil-type mould temperature controller has the characteristics of precise temperature control, rapid heating and cooling, and easy maintenance and operation. At the same time, the design separates the electric box to protect electrical components more effectively and ensure safe use. In addition, the magnetic drive pump used solves the problem of natural wear and leakage of the shaft seal, and an over-temperature protection switch is also standard in the motor coil to prevent the motor from overheating and burning, reduce the failure rate, and reduce the risk of accidental touch by personnel.
Faced with the 120℃ large-flow water mould temperature machine featuring high flow and head in the automotive industry, operators select a cooling solenoid valve with a diameter of 20mm.
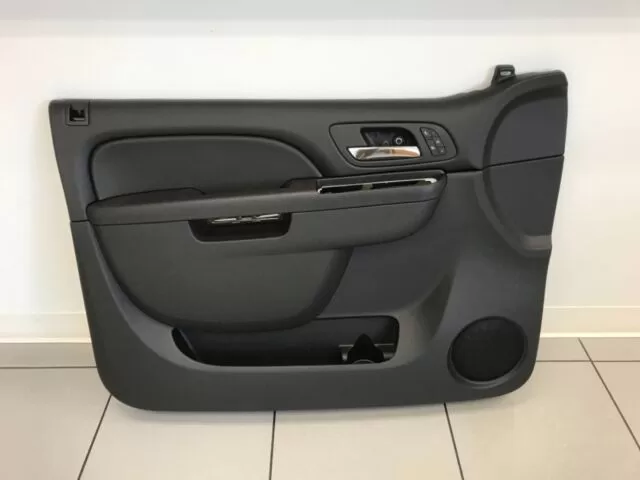
Obtain optimal mold temperature
Topstar designs its mold temperature controllers to provide precise temperature management during the injection molding process. In addition to managing temperature, our temperature controller also features a newly designed stainless steel frame structure, which is more convenient to move and can be widely used in manufacturing processes across various industries.
TRENDING POSTS
- What factors can cause delays in the injection molding process of plastic molding machine? 2022/07/22
- Exhibition Review| Topstar participates in InterPlas Thailand 2024 2022/07/22
- Star Case | Topstar helps Santong upgrade its intelligent plant 2022/07/22
- Topstar Special | National Science and Technology Workers Day 2022/07/22
HOT TOPIC
- 3 in 1 Compact Dehumidifying Dryer
- 5-axis CNC machine
- accuracy
- Air Chillers
- all electric injection molding machine
- All-electric injection molding machines
- and overall production quality. Therefore
- AP-RubberPlas
- automated injection molding machine
- Automation changed engineering
- automation of injection molding robots
- auxiliary machine
- Bench Injection Molding Machine
- Cabinet dryer manufacturers
- Cabinet dryers
- chiller
- CNC Drilling Machine
- CNC Drilling Machines
- cnc engraving machine manufacturer
- cnc laser cutting machine manufacturer
- CNC machine
- CNC Machine Center
- CNC Machine for Sale
- CNC Machine Manufacturing
- CNC Machine Tool
- CNC machine tool product
- CNC Machining Center
- CNC wood carving machine
- Cooling system
- Cross-Walking Single Axis Servo Cylinder Robot
- Cross-Walking Single-Axis Servo Cylinder Robot
- Cross-Walking Three-Axis/Five-Axis Servo Driven Robot
- cross-walking three-axis/five-axis servo-driven robot
- Dehumidifier Dryer
- Dehumidifying Dryer
- delta parallel robot
- Desktop Injection Molding Machine
- Desktop injection molding machines
- Desktop Molding Machine
- desktop plastic injection machine
- Desktop Plastic Injection Molding Machine
- direct clamp injection molding machine
- Direct clamp injection molding machines
- Dosing & mixing system
- Drilling Centers
- Drying and dehumidification system
- drying and dehumidifying equipment
- Drying and Dehumidifying System
- drying system
- effective and efficient. Cabinet dryers are also used in other industries where large quantities of material need to be dried
- efficient injection molding machine
- elbow hydraulic injection molding machines
- electric injection molding machine
- electric injection molding machines
- etc. Among injection molding robots
- exhibition
- features of CNC machine
- Feeding And Conveying System
- Five Axis Machine Center
- Fully automatic injection molding machine
- Gathering Topstar
- giant injection molding machine
- GMU-600 5-Axis Machining Center
- Granulating & Recycling System
- Heavy duty injection molding machine
- Honeycomb rotor dehumidifier
- horizontal injection molding machine
- Horizontal Injection Molding Machines
- Horizontal Injection Moulding Machine
- Horizontal Mixer manufacturer
- How The CNC Machine Works
- hybrid injection molding machine
- hydraulic injection molding machine
- Hydraulic Injection Molding Machines
- in this article
- Industrial robot
- Industrial Robot Chinese brand
- industrial robot parts
- industrial robot supplier
- Industrial robots
- Industry Chain
- Injection Manipulator
- injection mold machines
- Injection molding
- Injection molding automation
- Injection Molding Automation Solution
- injection molding dryer
- Injection molding equipment
- injection molding hopper dryer
- Injection molding machine
- injection molding machine brand
- Injection Molding Machine Factory
- Injection Molding Machine Manufacture
- Injection molding machine manufacturer
- injection molding machine manufacturers
- Injection molding machine procurement
- injection molding machine robotic arm
- injection molding machine with a robot
- Injection molding machines
- injection molding material dehumidifying
- injection molding plant
- Injection Molding Robot
- injection molding robot arm
- Injection molding robot automation
- Injection molding robotic arm
- injection molding robots
- Injection Moulding Robots
- Injection Robot
- Injection robot arm
- Injection robot manufacturer
- Injection robot wholesale
- injection robots
- intelligent injection molding machines
- Introducing Injection Robot
- It is the best choice for drying large quantities of material at once. Cabinetmakers use these machines because they are fast
- large injection molding machine
- Learn what industrial automation and robotics is
- low speed sound-proof granulator
- machine plastic molding
- make sure to add some! Improvements (2) Keyphrase in introduction: Your keyphrase or its synonyms appear in the first paragraph of the copy
- manipulator machine
- manufacturing
- micro injection molding machine
- middle speed granulator
- Mini CNC machine manufacturers.
- Mold Temperature Control System
- mold temperature controller
- molding material Dehumidifying System
- mould temperature controller
- mould temperature controllers
- New electric injection molding machine
- nitrogen dryer manufacturer
- nitrogen dryer system manufacturer
- Oil type mold temperature controller
- open day
- Outbound links: No outbound links appear in this page. Add some! Images: No images appear on this page. Add some! Internal links: No internal links appear in this page
- PET Preform injection molding
- phone case maker machine
- phone case making machine
- plastic bottle making machine
- plastic bottle manufacturing
- plastic bucket making machine
- plastic bucket manufacturing
- Plastic chair making machine
- plastic forming equipment
- plastic hopper dryer
- plastic injection machine
- plastic injection machines
- plastic injection molding
- Plastic injection molding equipment
- Plastic injection molding machine
- Plastic Injection Molding Machines
- plastic injection robot
- Plastic Molding machine
- Plastic Molding Machines
- plastic molding press
- plastic phone case making machine
- plastic-molding machine
- powerful granulator
- Powerful Type Sound-Proof Granulator
- production of plastic seats
- Robot injection molding
- robot injection molding machine
- robot manufacturing companies
- Robotic arm for injection molding machine
- robotic injection molding machines
- robotics in injection molding
- SCARA robot
- SCARA robots
- Service-oriented manufacturing
- Servo Cylinder Robot
- servo driven robot
- Servo Driven Robots
- servo injection robots
- Servo-Driven Robot
- Setup of injection machine
- Silicone Injection Molding Machine
- six-axis industrial robot
- Stainless Hopper Dryer
- Stainless Hopper Dryers
- star club
- swing arm robot
- the choice between servo-driven robots and hydraulic robots will have a certain impact on efficiency
- the most popular injection molding machine
- the type of injection molding robot
- toggle clamp injection molding machine
- Toggle Hydraulic Injection Molding Machines
- toggle injection molding machine
- Top 10 brands of injection robots
- Topstar
- Topstar Engineering
- Topstar Industrial Robots
- Topstar injection molding intelligent
- Topstar Scara Robots
- Useful Injection molding machine
- Vertical machining centers
- volumetric type blender
- water chiller
- water chillers
- water distributor
- Water Type MoldTemperature Controller
- We often face choices when performing injection molding. We will choose the type of injection molding machine
- wholesale of injection molding machines
- x carve CNC