Use mould temperature controller to improve injection molding yield
2024/07/19 By Topstar
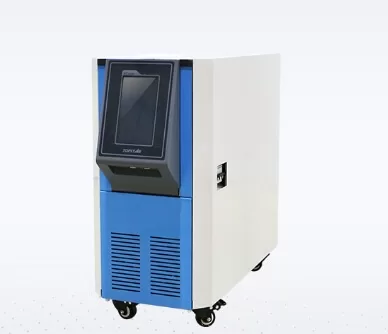
In the injection molding industry, the actual temperature delivered by the mould temperature controller of many users is different from the temperature displayed by the mold temperature controller. There is a significant deviation, resulting in a low yield rate. In communicating with users, we often encounter similar problems, and the yield rate is not high for various reasons. Therefore, we have sorted out the Topstar mould temperature controller functions to improve the yield rate and will share them with you in this guide.
Temperature control accuracy of mould temperature controller
Topstar’s mould temperature controller is based on the temperature PID algorithm, which allows the temperature control accuracy to reach ±0.1℃. It can ensure temperature uniformity and also has an over-temperature protection mechanism. By preventing temperature fluctuations, these controllers help minimize defects such as warping, dents and incomplete filling, thereby increasing the overall yield of the molding process. In addition, the machine’s system will automatically record the equipment operation status and alarm log to reduce the fault promotion response time. It not only guarantees productivity but also guarantees the yield rate.
Use mould temperature controller to optimize cycle time
In injection molding, cycle time is also a key factor that directly affects productivity and output. The mould temperature controller helps keep the mold at an ideal temperature, ensuring the material solidifies quickly without affecting quality. By shortening the cooling time, the enhanced cooling phase enables manufacturers to produce more parts faster. Faster cooling speeds up the solidification of the plastic, which reduces the overall cycle time. This increase in output can meet high production demands and ensure a good yield. In addition, shorter cycle times can reduce energy consumption.
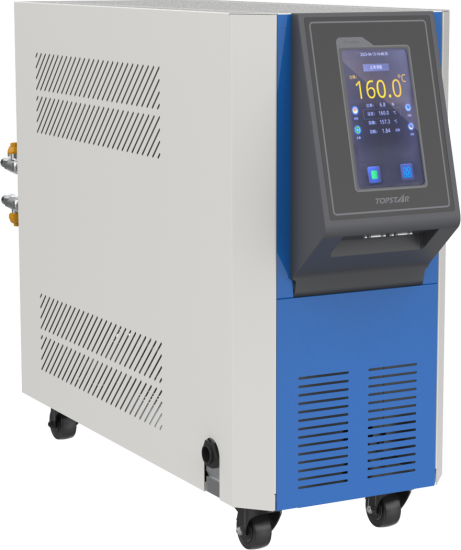
Blowing and water return function
The blowing function of the Topstar mould temperature controller helps to speed up mold cooling by introducing controlled airflow into the mold. By directing air to specific areas of the mould, blowing can supplement the cooling effect provided by traditional water-based systems. Achieve a more uniform and faster cooling process. The blowing function also greatly reduces cooling inconsistencies, directly translating into higher yields. The water return function ensures that the cooling water circulates efficiently and constantly throughout the mold. It helps to maintain a stable mold temperature, and constant temperature control minimizes thermal changes that may cause defects, thereby improving the yield rate. The two are combined with each other, using the targeted cooling enhancement provided by the blowing function, and the water return function ensures overall temperature stability to make parts more efficient and less defective.
Dual-circuit temperature detection
In mould temperature controllers, dual-circuit temperature detection uses two independent temperature sensors and control circuits to monitor and regulate the temperature of the mold. Enabling each circuit to operate independently allows for precise and continuous temperature measurement and control at different points within the mold. This ensures a more accurate and reliable thermal management system. By monitoring multiple points within the mold, they can detect and correct temperature deviations in a timely manner. This precise control can reduce temperature fluctuations that cause defects such as warping and shrinkage of moulded parts. Using dual-circuit temperature detection minimises temperature changes, resulting in more consistent product quality and better yields.
Wider temperature range
The mould temperature controller series is divided into water-type mold temperature controllers (120℃-180℃) and oil-type mold temperature controllers (200℃-320℃), with heating power ranging from 8-48KW and water pump power ranging from 1-5HP. Mold temperature controllers with a wide temperature range can meet the temperature requirements of different plastics such as PEEK, POM, PP or PE. Ensure that the appropriate temperature is maintained for each material type. This versatility reduces the risk of heat-related defects, thereby improving overall yields. Proper temperature control over a wide temperature range can improve the surface finish, dimensional stability, and strength of molded parts.
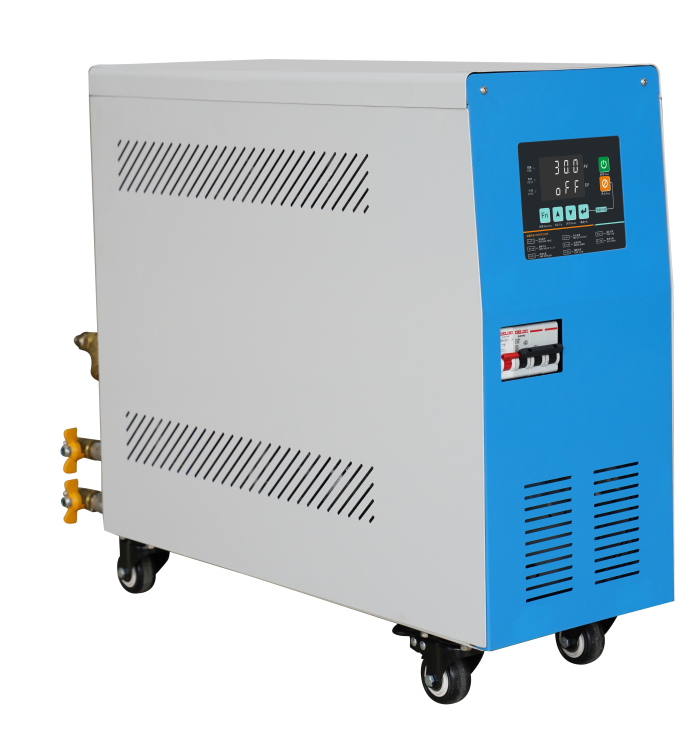
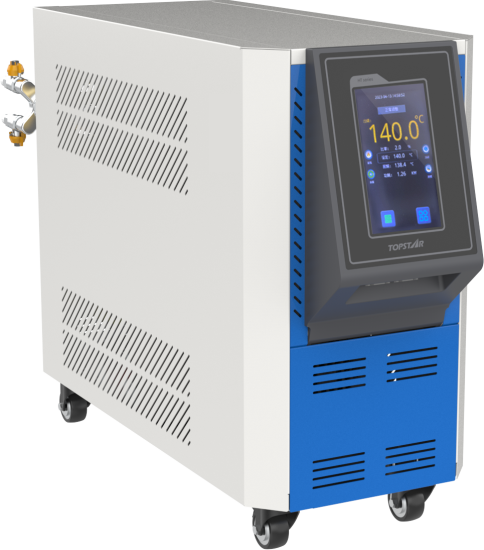
Impact on injection molding yield
Topstar’s mould temperature controllers can improve product quality, reduce energy consumption, and minimize downtime and maintenance by providing precise temperature control, optimizing cycle time, and optimizing air-blowing and water return functions. Their advanced features and best practices further enhance their ability to increase production and yield.
TRENDING POSTS
- What factors can cause delays in the injection molding process of plastic molding machine? 2024/07/19
- Exhibition Review| Topstar participates in InterPlas Thailand 2024 2024/07/19
- Star Case | Topstar helps Santong upgrade its intelligent plant 2024/07/19
- Topstar Special | National Science and Technology Workers Day 2024/07/19
HOT TOPIC
- 3 in 1 Compact Dehumidifying Dryer
- 5-axis CNC machine
- accuracy
- Air Chillers
- all electric injection molding machine
- all electric injection molding machines
- All-electric injection molding machines
- and overall production quality. Therefore
- AP-RubberPlas
- automated injection molding machine
- Automation changed engineering
- automation of injection molding robots
- auxiliary machine
- Bench Injection Molding Machine
- Cabinet dryer manufacturers
- Cabinet dryers
- chiller
- CNC Drilling Machine
- CNC Drilling Machines
- cnc engraving machine manufacturer
- cnc laser cutting machine manufacturer
- CNC machine
- CNC Machine Center
- CNC Machine for Sale
- CNC Machine Manufacturing
- CNC Machine Tool
- CNC machine tool product
- CNC Machining Center
- CNC wood carving machine
- Cooling system
- Cross-Walking Single Axis Servo Cylinder Robot
- Cross-Walking Single-Axis Servo Cylinder Robot
- Cross-Walking Three-Axis/Five-Axis Servo Driven Robot
- cross-walking three-axis/five-axis servo-driven robot
- Dehumidifier Dryer
- Dehumidifying Dryer
- delta parallel robot
- Desktop Injection Molding Machine
- Desktop injection molding machines
- Desktop Molding Machine
- desktop plastic injection machine
- Desktop Plastic Injection Molding Machine
- direct clamp injection molding machine
- Direct clamp injection molding machines
- Dosing & mixing system
- Drilling Centers
- Drying and dehumidification system
- drying and dehumidifying equipment
- Drying and Dehumidifying System
- drying system
- effective and efficient. Cabinet dryers are also used in other industries where large quantities of material need to be dried
- efficient injection molding machine
- elbow hydraulic injection molding machines
- electric injection molding machine
- electric injection molding machines
- energy-saving injection molding machine
- etc. Among injection molding robots
- exhibition
- features of CNC machine
- Feeding And Conveying System
- Five Axis Machine Center
- Fully automatic injection molding machine
- Gathering Topstar
- giant injection molding machine
- GMU-600 5-Axis Machining Center
- Granulating & Recycling System
- Heavy duty injection molding machine
- Honeycomb rotor dehumidifier
- horizontal injection molding machine
- Horizontal Injection Molding Machines
- Horizontal Injection Moulding Machine
- Horizontal Mixer manufacturer
- How The CNC Machine Works
- hybrid injection molding machine
- hydraulic injection molding machine
- Hydraulic Injection Molding Machines
- in this article
- Industrial robot
- Industrial Robot Chinese brand
- industrial robot parts
- industrial robot supplier
- Industrial robots
- Industry Chain
- Injection Manipulator
- injection mold machines
- Injection molding
- Injection molding automation
- Injection Molding Automation Solution
- injection molding dryer
- Injection molding equipment
- injection molding hopper dryer
- Injection molding machine
- injection molding machine brand
- Injection Molding Machine Factory
- Injection Molding Machine Manufacture
- Injection molding machine manufacturer
- injection molding machine manufacturers
- Injection molding machine procurement
- injection molding machine robotic arm
- injection molding machine with a robot
- Injection molding machines
- injection molding material dehumidifying
- injection molding plant
- Injection Molding Robot
- injection molding robot arm
- Injection molding robot automation
- Injection molding robotic arm
- injection molding robots
- Injection Moulding Robots
- Injection Robot
- Injection robot arm
- Injection robot manufacturer
- Injection robot wholesale
- injection robots
- intelligent injection molding machines
- Introducing Injection Robot
- It is the best choice for drying large quantities of material at once. Cabinetmakers use these machines because they are fast
- large injection molding machine
- Learn what industrial automation and robotics is
- low speed sound-proof granulator
- machine plastic molding
- make sure to add some! Improvements (2) Keyphrase in introduction: Your keyphrase or its synonyms appear in the first paragraph of the copy
- manipulator machine
- manufacturing
- micro injection molding machine
- middle speed granulator
- Mini CNC machine manufacturers.
- Mold Temperature Control System
- mold temperature controller
- molding material Dehumidifying System
- mould temperature controller
- mould temperature controllers
- New electric injection molding machine
- nitrogen dryer manufacturer
- nitrogen dryer system manufacturer
- Oil type mold temperature controller
- open day
- Outbound links: No outbound links appear in this page. Add some! Images: No images appear on this page. Add some! Internal links: No internal links appear in this page
- PET Preform injection molding
- phone case maker machine
- phone case making machine
- plastic bottle making machine
- plastic bottle manufacturing
- plastic bucket making machine
- plastic bucket manufacturing
- Plastic chair making machine
- plastic forming equipment
- plastic hopper dryer
- plastic injection machine
- plastic injection machines
- plastic injection molding
- Plastic injection molding equipment
- Plastic injection molding machine
- Plastic Injection Molding Machines
- plastic injection robot
- Plastic Molding machine
- Plastic Molding Machines
- plastic molding press
- plastic phone case making machine
- plastic-molding machine
- powerful granulator
- Powerful Type Sound-Proof Granulator
- production of plastic seats
- Robot injection molding
- robot injection molding machine
- robot manufacturing companies
- Robotic arm for injection molding machine
- robotic injection molding machines
- robotics in injection molding
- SCARA robot
- SCARA robots
- Service-oriented manufacturing
- Servo Cylinder Robot
- servo driven robot
- Servo Driven Robots
- servo injection robots
- Servo-Driven Robot
- Setup of injection machine
- Silicone Injection Molding Machine
- six-axis industrial robot
- Stainless Hopper Dryer
- Stainless Hopper Dryers
- star club
- swing arm robot
- the choice between servo-driven robots and hydraulic robots will have a certain impact on efficiency
- the most popular injection molding machine
- the type of injection molding robot
- toggle clamp injection molding machine
- Toggle Hydraulic Injection Molding Machines
- toggle injection molding machine
- Top 10 brands of injection robots
- Topstar
- Topstar Engineering
- Topstar Industrial Robots
- Topstar injection molding intelligent
- Topstar Scara Robots
- Useful Injection molding machine
- Vertical machining centers
- volumetric type blender
- water chiller
- water chillers
- water distributor
- Water Type MoldTemperature Controller
- We often face choices when performing injection molding. We will choose the type of injection molding machine
- wholesale of injection molding machines
- x carve CNC