Troubleshooting of misaligned gripping issues with the injection manipulator robot
2025/04/25 By Topstar
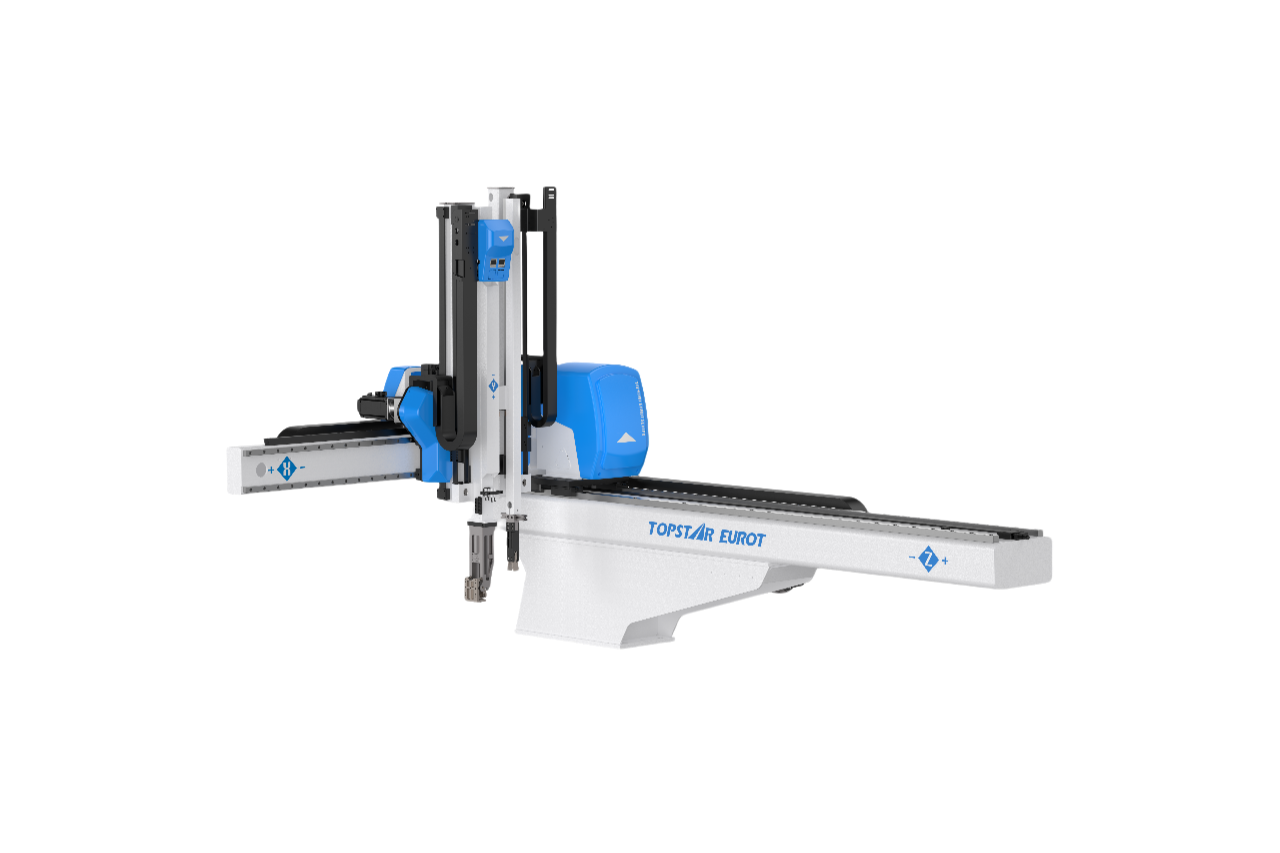
If the injection molding robot misaligns when accurately picking and placing molded parts in high-speed production lines, it can cause part defects, production delays, and even equipment damage. For the injection manipulator robot, grasping errors are usually caused by problems such as poor synchronization with the injection molding machine or insufficient positioning accuracy of the end effector. In this guide, we will share how Topstar solves such problems, what technologies are used, and popularize other situations that occur for injection molding manufacturers to help everyone better perform injection molding work.
How signal delays and system compatibility affect injection manipulator robots?
Signal delays and protocol mismatches are common in injection molding plants using equipment from different suppliers. If the injection manipulator robot receives delayed or misinterpreted signals, grasping errors may occur. These technical limitations lead to repeated mistakes, longer cycle times, and increased wear on mechanical parts due to repeated grasping errors.
To avoid this failure, Topstar uses the open architecture of the underlying control system to enable both the injection molding machine and the injection manipulator robot to have a native language of system integration. This makes the interconnection of injection molding equipment an extension of the system rather than just a communication connection. This enhances the robot’s compatibility with various injection molding machines.
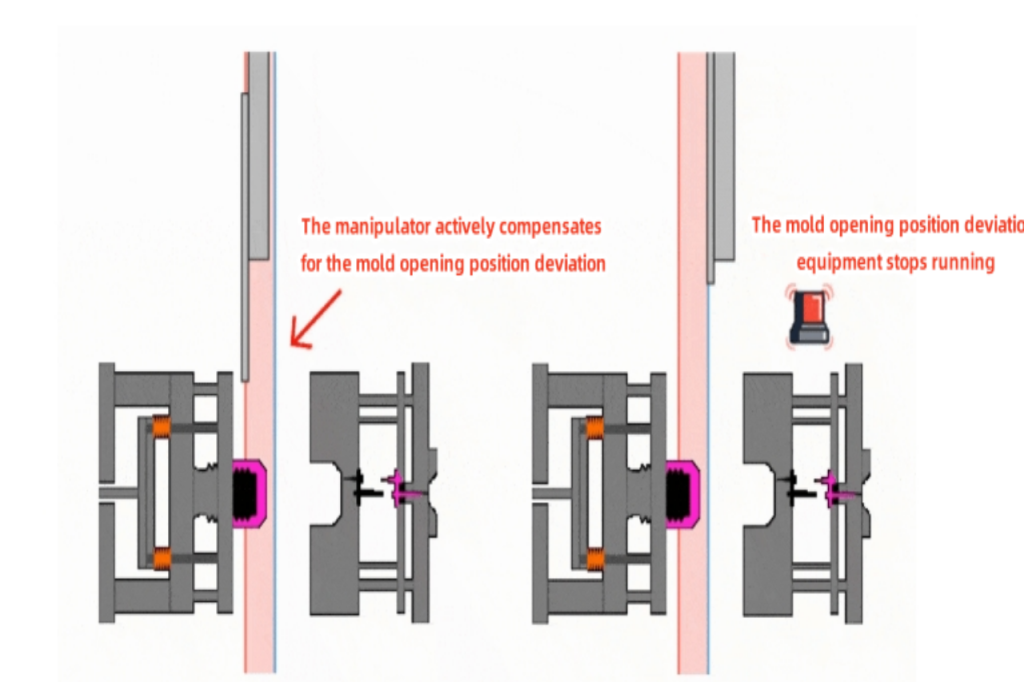
Robotic coordination between the injection manipulator robot and the injection molding machine
As mentioned above, the lack of real-time coordination between the injection molding robot and the injection molding machine will cause the problem of inaccurate grasping. Then, under a unified control system and communication protocol, the injection manipulator robot can have an automatic following function and respond to the movement of the injection molding machine in real-time. Ensuring that the robot arm’s precise position and time are consistent with the ejection process reduces the error margin when running at high speed or handling precision molds. Specifically, the injection molding robot and the mold opening process are synchronized, and the early arrival and “automatic following” functions reduce abnormal alarms and equipment maintenance times, further improving production efficiency. According to customer feedback, the robot with the “automatic following” function can increase the production efficiency of each injection molding intelligent unit by about 5%.

Mechanical reasons for inaccurate clamping
In addition to communication-related problems, mechanical factors can also cause grasping problems. Worn end effectors, misaligned guides, or vibrations during movement can affect the accuracy of the injection robot. In addition, improper installation or lack of calibration can cause minor errors that worsen over time. Topstar injection molding robots feature high-rigidity structures and precision-engineered components. Hardened steel guides, self-lubricating bearings, and vibration-resistant servo motors ensure mechanical stability over long-term use. In addition, the system includes an automatic calibration function that periodically recalibrates the robot’s position to prevent cumulative calibration errors.
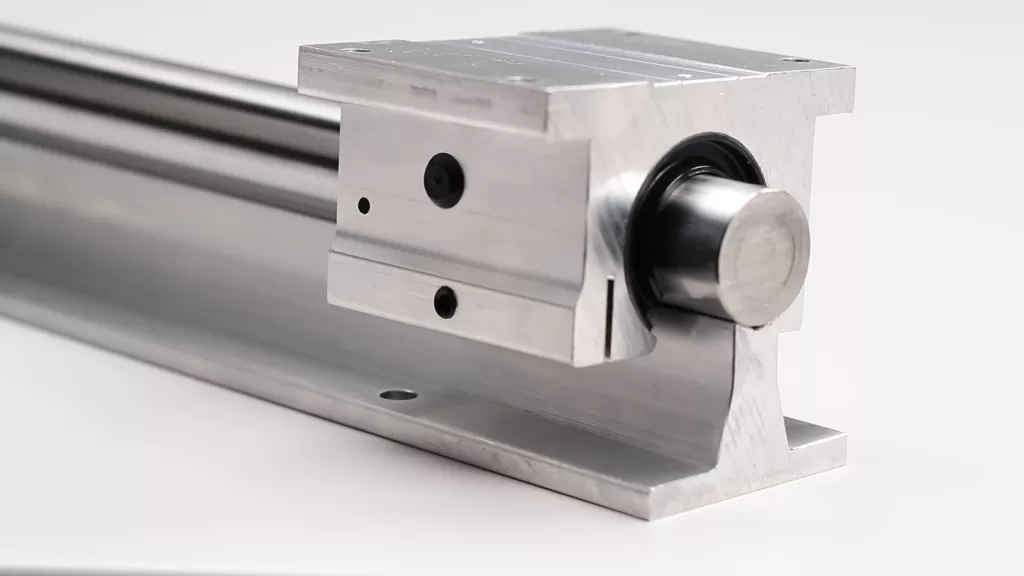
Optimization of gripping mechanisms
The design and function of the gripper (also known as the end effector) are also key to ensuring the successful handling of injection-molded parts. Some special industries require engineers to customize the gripper according to the shape, size, and material of the part. Because universal or improperly installed grippers may cause slippage, part rotation, or incomplete gripping. Operators can make real-time adjustments through a user-friendly HMI interface using tools designed for specific mold outputs, such as gripping tools, vacuum suction cups, mechanical claws, and hybrid grippers. In combination, Topstar’s “fast pick up, gentle placement” motion algorithm uses high-speed descent to grab the parts inside the mold quickly. It moves slowly during placement to avoid impact or damage, significantly improving precision and product safety.
The role of the control system in improving grasping performance
The robot’s control system is the key to solving the grasping misalignment problem. Outdated or limited-function controllers cannot meet the dynamic needs of modern injection molding. Topstar continuously equips its injection molding robot series with iterative control systems that evolve through firmware updates and AI-based learning.
The system enables injection manipulator robots to learn from previous tasks, adjust performance based on operator feedback, and fine-tune their movements to better adapt to each unique mold and cycle time. What’s more, Topstar’s controllers integrate seamlessly with MES, allowing centralized monitoring, real-time adjustments, and predictive maintenance alerts. This approach makes the injection molding robot an innovative, reliable, and adaptive production partner.
Precision grasping starts with intelligent control.
Injection molding robot grasping misalignment will hurt precision and speed. Topstar’s overall solution – combining advanced mechanical technology and intelligent control, solving signal delay problems through an automatic following system, improving mechanical durability, using special fixtures, and equipping the robot with control software with learning functions, can ensure that each product can be processed accurately and meticulously.
TRENDING POSTS
- What factors can cause delays in the injection molding process of plastic molding machine? 2025/04/25
- Exhibition Review| Topstar participates in InterPlas Thailand 2024 2025/04/25
- Star Case | Topstar helps Santong upgrade its intelligent plant 2025/04/25
- Topstar Special | National Science and Technology Workers Day 2025/04/25
HOT TOPIC
- 3 in 1 Compact Dehumidifying Dryer
- 5-axis CNC machine
- accuracy
- Air Chillers
- all electric injection molding machine
- all electric injection molding machines
- All-electric injection molding machines
- and overall production quality. Therefore
- AP-RubberPlas
- automated injection molding machine
- Automation changed engineering
- automation of injection molding robots
- auxiliary machine
- Bench Injection Molding Machine
- Cabinet dryer manufacturers
- Cabinet dryers
- chiller
- CNC Drilling Machine
- CNC Drilling Machines
- cnc engraving machine manufacturer
- cnc laser cutting machine manufacturer
- CNC machine
- CNC Machine Center
- CNC Machine for Sale
- CNC Machine Manufacturing
- CNC Machine Tool
- CNC machine tool product
- CNC Machining Center
- CNC wood carving machine
- Cooling system
- Cross-Walking Single Axis Servo Cylinder Robot
- Cross-Walking Single-Axis Servo Cylinder Robot
- Cross-Walking Three-Axis/Five-Axis Servo Driven Robot
- cross-walking three-axis/five-axis servo-driven robot
- Dehumidifier Dryer
- Dehumidifying Dryer
- delta parallel robot
- Desktop Injection Molding Machine
- Desktop injection molding machines
- Desktop Molding Machine
- desktop plastic injection machine
- Desktop Plastic Injection Molding Machine
- direct clamp injection molding machine
- Direct clamp injection molding machines
- Dosing & mixing system
- Drilling Centers
- Drying and dehumidification system
- drying and dehumidifying equipment
- Drying and Dehumidifying System
- drying system
- effective and efficient. Cabinet dryers are also used in other industries where large quantities of material need to be dried
- efficient injection molding machine
- elbow hydraulic injection molding machines
- electric injection molding machine
- electric injection molding machines
- energy-saving injection molding machine
- etc. Among injection molding robots
- exhibition
- features of CNC machine
- Feeding And Conveying System
- Five Axis Machine Center
- Fully automatic injection molding machine
- Gathering Topstar
- giant injection molding machine
- GMU-600 5-Axis Machining Center
- Granulating & Recycling System
- Heavy duty injection molding machine
- Honeycomb rotor dehumidifier
- horizontal injection molding machine
- Horizontal Injection Molding Machines
- Horizontal Injection Moulding Machine
- Horizontal Mixer manufacturer
- How The CNC Machine Works
- hybrid injection molding machine
- hydraulic injection molding machine
- Hydraulic Injection Molding Machines
- in this article
- Industrial robot
- Industrial Robot Chinese brand
- industrial robot parts
- industrial robot supplier
- Industrial robots
- Industry Chain
- Injection Manipulator
- injection manipulator robot
- injection mold machines
- Injection molding
- Injection molding automation
- Injection Molding Automation Solution
- injection molding dryer
- Injection molding equipment
- injection molding hopper dryer
- Injection molding machine
- injection molding machine brand
- Injection Molding Machine Factory
- Injection Molding Machine Manufacture
- Injection molding machine manufacturer
- injection molding machine manufacturers
- Injection molding machine procurement
- injection molding machine robotic arm
- injection molding machine with a robot
- Injection molding machines
- injection molding material dehumidifying
- injection molding plant
- Injection Molding Robot
- injection molding robot arm
- Injection molding robot automation
- Injection molding robotic arm
- injection molding robots
- Injection Moulding Robots
- Injection Robot
- Injection robot arm
- Injection robot manufacturer
- Injection robot wholesale
- injection robots
- intelligent injection molding machines
- Introducing Injection Robot
- It is the best choice for drying large quantities of material at once. Cabinetmakers use these machines because they are fast
- large injection molding machine
- Learn what industrial automation and robotics is
- linear robot
- low speed sound-proof granulator
- machine plastic molding
- make sure to add some! Improvements (2) Keyphrase in introduction: Your keyphrase or its synonyms appear in the first paragraph of the copy
- manipulator machine
- manufacturing
- micro injection molding machine
- middle speed granulator
- Mini CNC machine manufacturers.
- Mold Temperature Control System
- mold temperature controller
- molding material Dehumidifying System
- mould temperature controller
- mould temperature controllers
- New electric injection molding machine
- nitrogen dryer manufacturer
- nitrogen dryer system manufacturer
- Oil type mold temperature controller
- open day
- Outbound links: No outbound links appear in this page. Add some! Images: No images appear on this page. Add some! Internal links: No internal links appear in this page
- PET Preform injection molding
- phone case maker machine
- phone case making machine
- plastic bottle making machine
- plastic bottle manufacturing
- plastic bucket making machine
- plastic bucket manufacturing
- Plastic chair making machine
- plastic forming equipment
- plastic hopper dryer
- plastic injection machine
- plastic injection machines
- plastic injection molding
- Plastic injection molding equipment
- Plastic injection molding machine
- Plastic Injection Molding Machines
- plastic injection robot
- Plastic Molding machine
- Plastic Molding Machines
- plastic molding press
- plastic phone case making machine
- plastic-molding machine
- powerful granulator
- Powerful Type Sound-Proof Granulator
- production of plastic seats
- Robot injection molding
- robot injection molding machine
- robot manufacturing companies
- Robotic arm for injection molding machine
- robotic injection molding machines
- robotics in injection molding
- SCARA robot
- SCARA robots
- Service-oriented manufacturing
- Servo Cylinder Robot
- servo driven robot
- Servo Driven Robots
- servo injection robots
- Servo-Driven Robot
- Setup of injection machine
- Silicone Injection Molding Machine
- six-axis industrial robot
- Stainless Hopper Dryer
- Stainless Hopper Dryers
- star club
- swing arm robot
- the choice between servo-driven robots and hydraulic robots will have a certain impact on efficiency
- the most popular injection molding machine
- the type of injection molding robot
- toggle clamp injection molding machine
- Toggle Hydraulic Injection Molding Machines
- toggle injection molding machine
- Top 10 brands of injection robots
- Topstar
- Topstar Engineering
- Topstar Industrial Robots
- Topstar injection molding intelligent
- Topstar Scara Robots
- Useful Injection molding machine
- Vertical machining centers
- volumetric type blender
- water chiller
- water chillers
- water distributor
- Water Type MoldTemperature Controller
- We often face choices when performing injection molding. We will choose the type of injection molding machine
- wholesale of injection molding machines
- x carve CNC