The overall solution for the injection molding machine of medicine bottle caps
2024/09/09 By Topstar
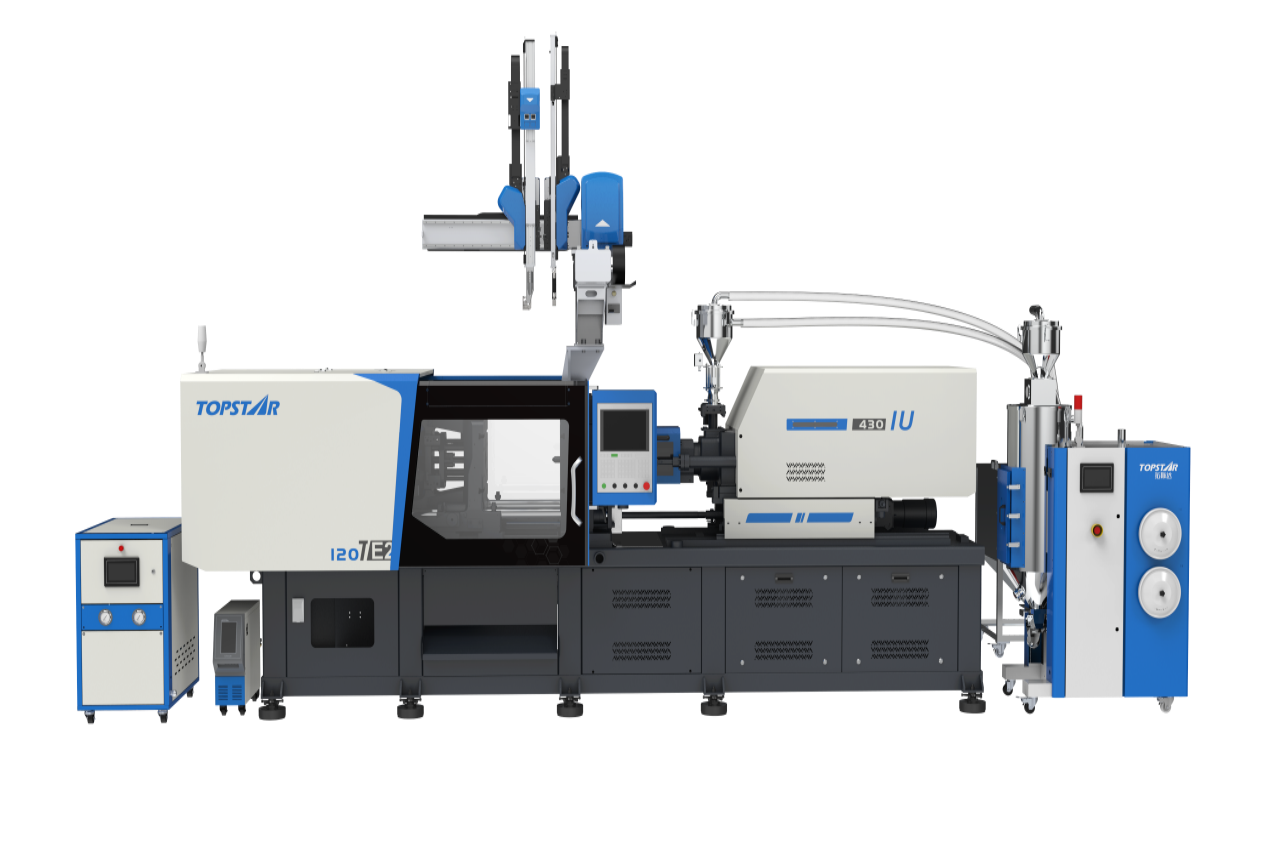
There are strict regulations and quality requirements for procuring medicine bottle caps in the pharmaceutical industry, so when producing medicine bottle caps, it is necessary to use a dedicated injection molding machine. These caps not only seal the medicine bottles but also ensure product safety, tamper-proof, and meet strict hygiene standards. At Topstar, we can provide comprehensive injection molding machine solutions designed specifically for medicine bottle cap manufacturers. The injection molding solution combines cutting-edge technology, central control, and automation to optimize production efficiency and ensure product quality. So, we will present you with our complete solution for manufacturing medicine bottle caps in this article.
Importance of dedicated injection molding machine for medicine bottle caps
The production of medicine bottle caps requires a dedicated injection molding machine that meets the high standards of the pharmaceutical industry. They are produced precisely to ensure a perfect fit on the bottle, maintain an airtight seal, and prevent contamination. Topstar’s TE160II electric injection molding machine is equipped with the latest technology and is the second generation of a new electric injection molding machine. Servo’s self-drive drive ensures that each medicine bottle cap is produced with unparalleled precision. High molding performance can make the bottle cap molding more stable, and the highly stable imported control system can produce consistent results with high output while complying with strict quality control standards. With Topstar’s overall injection molding solution, you can achieve faster production time, reduced waste, and higher product safety.
High-rigidity and low-friction mechanical structure
One of the outstanding features of the TEII160 electric injection molding machine is its high-rigidity mechanical structure. This rigid frame withstands the powerful forces generated during the injection molding, providing unparalleled stability and accuracy. By reducing vibration and mechanical deformation, this structure ensures that the injection and clamping components remain aligned, allowing for accurate cavity filling and consistent part quality for medicine bottle caps.
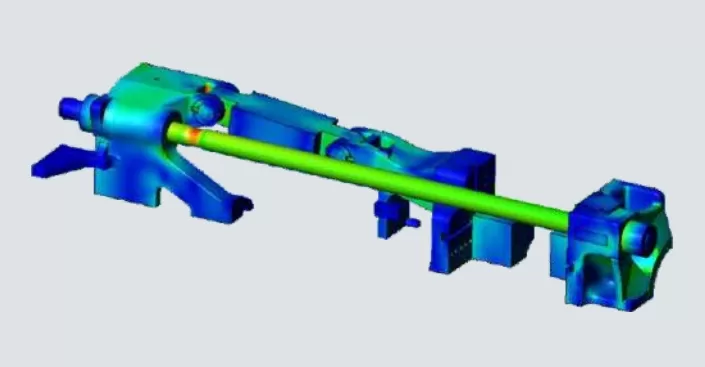
The low-friction mechanical design of the TEII160 is essential to reduce wear on machine components, especially in areas where movement is constant, such as the injection unit and screw mechanism. By reducing friction, the TEII160 ensures smoother and more controlled movement throughout the injection cycle, improving material flow and mold filling accuracy. At the same time, the low-friction design also helps improve the machine’s energy efficiency. Machines require less energy to overcome friction, which improves efficiency and reduces energy consumption.
User-friendly interface
The personalized interactive page is the most prominent feature of the central control system of the TEII160 electric injection molding machine. Operators can easily navigate the control panel, which provides real-time data and customizable settings for all aspects of the molding process. The clear and user-friendly touchscreen display lets operators quickly adjust parameters such as temperature, pressure, injection speed, and cycle time.
This ease of operation shortens the learning curve for new users while improving overall productivity. The central control system provides comprehensive real-time monitoring of all machine operations, including injection molding machines, injection molding machine robots, etc. Operators can continuously track key parameters such as material temperature, injection pressure, and clamping force to ensure the process stays within specified limits.
This real-time data collection capability enables quick adjustments during production, ensuring consistent product quality and reducing the likelihood of defects.
Non-contact tie rod and moving mold linear guide
Traditionally, tie rods in injection molding machines require regular lubrication to reduce friction between moving parts. This lubrication process, while necessary, often leads to environmental contamination, especially when oil or grease leaks onto the mold or final product. In fields such as medical, food, and electronics manufacturing, even small amounts of contamination can compromise the integrity of the product.
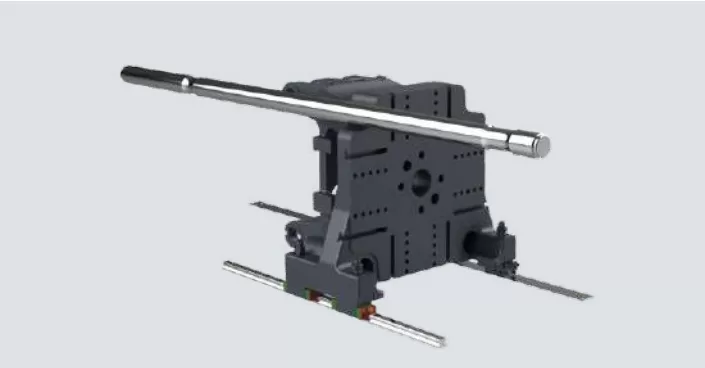
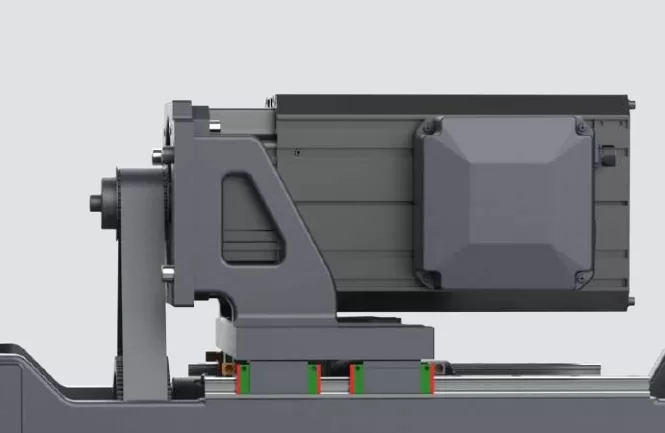
The TEII160 electric injection molding machine solves this problem with its non-contact tie-rod design. By eliminating direct contact between the tie rods and other moving parts, the machine removes the need for lubrication and reduces the risk of contamination. The movie mold linear guide ensures smooth and precise movement of the mold during the clamping and injection phases, reducing drag and providing enhanced stability during operation. The low-friction motion improves mold alignment accuracy and ensures even pressure distribution throughout the cavity. This improves part quality by reducing the likelihood of defects such as warped caps or uneven wall thickness.
Injection molding machine overall solution
The injection molding overall solution provides injection molding machines and includes related auxiliary equipment. TEII160 is designed to be easily integrated with peripheral auxiliary machines, such as injection molding robots, conveyor belts, material handling systems, and mold temperature controllers. This integration allows automation of all stages of the injection molding process, from material feeding to part removal. Integrating with auxiliary equipment, TEII160 supports fully automatic production lines, improves overall efficiency, and achieves continuous, uninterrupted operation.
To facilitate smooth communication between TEII160 and auxiliary equipment, Topstar uses standardized communication protocols, such as the MODBUS RTU communication protocol. This universal language ensures real-time data exchange and synchronization between the molding machine and peripheral equipment, achieving precise control and monitoring of the production line.
Complete injection molding solutions for medicine bottle caps
Topstar’s total injection molding machine solution can meet the specific needs of manufacturers producing medicine bottle caps. From precise control and energy efficiency improvement, the TEII160 electric injection molding machine provides you with everything you need to deliver high-quality, safe, and cost-effective medicine industry caps. At the same time, Topstar can offer tailor-made injection molding solutions for different industries, bringing continuous support and innovation.
TRENDING POSTS
- What factors can cause delays in the injection molding process of plastic molding machine? 2024/09/09
- Exhibition Review| Topstar participates in InterPlas Thailand 2024 2024/09/09
- Star Case | Topstar helps Santong upgrade its intelligent plant 2024/09/09
- Topstar Special | National Science and Technology Workers Day 2024/09/09
HOT TOPIC
- .ervo motor-driven linear robots
- 3 axis robot
- 3 axis robots
- 3 in 1 Compact Dehumidifying Dryer
- 3-axis robot
- 3-axis robots
- 5-axis CNC machine
- accuracy
- Air Chillers
- all electric injection molding machine
- all electric injection molding machines
- All-electric injection molding machines
- and overall production quality. Therefore
- AP-RubberPlas
- automated injection molding machine
- Automation changed engineering
- automation of injection molding robots
- auxiliary machine
- Bench Injection Molding Machine
- Cabinet dryer manufacturers
- Cabinet dryers
- chiller
- CNC Drilling Machine
- CNC Drilling Machines
- cnc engraving machine manufacturer
- cnc laser cutting machine manufacturer
- CNC machine
- CNC Machine Center
- CNC Machine for Sale
- CNC Machine Manufacturing
- CNC Machine Tool
- CNC machine tool product
- CNC Machining Center
- CNC wood carving machine
- Cooling system
- Cross-Walking Single Axis Servo Cylinder Robot
- Cross-Walking Single-Axis Servo Cylinder Robot
- Cross-Walking Three-Axis/Five-Axis Servo Driven Robot
- cross-walking three-axis/five-axis servo-driven robot
- Dehumidifier Dryer
- Dehumidifying Dryer
- delta parallel robot
- Desktop Injection Molding Machine
- Desktop injection molding machines
- Desktop Molding Machine
- desktop plastic injection machine
- Desktop Plastic Injection Molding Machine
- direct clamp injection molding machine
- Direct clamp injection molding machines
- Dosing & mixing system
- Drilling Centers
- Drying and dehumidification system
- drying and dehumidifying equipment
- Drying and Dehumidifying System
- drying system
- effective and efficient. Cabinet dryers are also used in other industries where large quantities of material need to be dried
- efficient injection molding machine
- elbow hydraulic injection molding machines
- electric injection molding machine
- electric injection molding machines
- energy-efficient injection molding robot
- energy-saving injection molding machine
- etc. Among injection molding robots
- exhibition
- features of CNC machine
- Feeding And Conveying System
- Five Axis Machine Center
- Fully automatic injection molding machine
- Gathering Topstar
- giant injection molding machine
- GMU-600 5-Axis Machining Center
- Granulating & Recycling System
- Heavy duty injection molding machine
- High-precision electric molding machines
- high-precision plastic molding machines
- high-speed all electric injection molding machine
- Honeycomb rotor dehumidifier
- horizontal injection molding machine
- Horizontal Injection Molding Machines
- Horizontal Injection Moulding Machine
- Horizontal Mixer manufacturer
- How The CNC Machine Works
- hybrid injection molding machine
- hydraulic injection molding machine
- Hydraulic Injection Molding Machines
- in this article
- Industrial robot
- Industrial Robot Chinese brand
- industrial robot parts
- industrial robot supplier
- Industrial robots
- Industry Chain
- Injection Manipulator
- injection manipulator robot
- injection mold machines
- Injection molding
- Injection molding automation
- Injection Molding Automation Solution
- injection molding dryer
- Injection molding equipment
- injection molding hopper dryer
- Injection molding machine
- injection molding machine brand
- Injection Molding Machine Factory
- Injection Molding Machine Manufacture
- Injection molding machine manufacturer
- injection molding machine manufacturers
- Injection molding machine procurement
- injection molding machine robotic arm
- injection molding machine with a robot
- Injection molding machines
- injection molding material dehumidifying
- injection molding plant
- Injection Molding Robot
- injection molding robot arm
- Injection molding robot automation
- Injection molding robotic arm
- injection molding robots
- Injection moulding machine
- Injection Moulding Robots
- Injection Robot
- Injection robot arm
- Injection robot manufacturer
- Injection robot wholesale
- injection robots
- intelligent injection molding machines
- Introducing Injection Robot
- It is the best choice for drying large quantities of material at once. Cabinetmakers use these machines because they are fast
- large injection molding machine
- Learn what industrial automation and robotics is
- linear robot
- linear robots
- low speed sound-proof granulator
- machine plastic molding
- make sure to add some! Improvements (2) Keyphrase in introduction: Your keyphrase or its synonyms appear in the first paragraph of the copy
- manipulator machine
- manufacturing
- medical grade injection molding machines
- medical injection molding machine
- medical injection molding machines
- micro injection molding machine
- middle speed granulator
- Mini CNC machine manufacturers.
- Mold Temperature Control System
- mold temperature controller
- mold temperature controllers
- molding material Dehumidifying System
- mould temperature control system
- mould temperature controller
- mould temperature controllers
- New electric injection molding machine
- nitrogen dryer manufacturer
- nitrogen dryer system manufacturer
- Oil type mold temperature controller
- Oil type mold temperature controllers
- open day
- Outbound links: No outbound links appear in this page. Add some! Images: No images appear on this page. Add some! Internal links: No internal links appear in this page
- PET Preform injection molding
- phone case maker machine
- phone case making machine
- plastic bottle making machine
- plastic bottle manufacturing
- plastic bucket making machine
- plastic bucket manufacturing
- Plastic chair making machine
- plastic forming equipment
- plastic hopper dryer
- plastic injection machine
- plastic injection machines
- plastic injection molding
- Plastic injection molding equipment
- Plastic injection molding machine
- Plastic Injection Molding Machines
- plastic injection moulding machine
- plastic injection robot
- Plastic Molding machine
- Plastic Molding Machines
- plastic molding press
- plastic moulding machine
- plastic phone case making machine
- plastic-molding machine
- powerful granulator
- Powerful Type Sound-Proof Granulator
- precision injection molding
- precision injection molding machines
- production of plastic seats
- pure water mould temperature controller
- Robot injection molding
- robot injection molding machine
- robot manufacturing companies
- Robotic arm for injection molding machine
- robotic injection molding machines
- robotics in injection molding
- SCARA robot
- SCARA robots
- Service-oriented manufacturing
- Servo Cylinder Robot
- servo driven robot
- Servo Driven Robots
- servo injection robots
- servo motor-driven linear robots
- servo-driven 3-axis robot
- Servo-Driven Robot
- Setup of injection machine
- Silicone Injection Molding Machine
- six-axis industrial robot
- Stainless Hopper Dryer
- Stainless Hopper Dryers
- star club
- swing arm robot
- take-out robots
- the choice between servo-driven robots and hydraulic robots will have a certain impact on efficiency
- the most popular injection molding machine
- the type of injection molding robot
- toggle clamp injection molding machine
- Toggle Hydraulic Injection Molding Machines
- toggle injection molding machine
- Top 10 brands of injection robots
- Topstar
- Topstar Engineering
- Topstar Industrial Robots
- Topstar injection molding intelligent
- Topstar Scara Robots
- Useful Injection molding machine
- Vertical machining centers
- volumetric type blender
- water chiller
- water chillers
- water distributor
- water type mold temperature controller
- Water Type MoldTemperature Controller
- Water-Type Mould Temperature Controllers
- We often face choices when performing injection molding. We will choose the type of injection molding machine
- wholesale of injection molding machines
- x carve CNC