The best Injection molding robotic arm for the rapid prototyping industry
2024/07/22 By Topstar
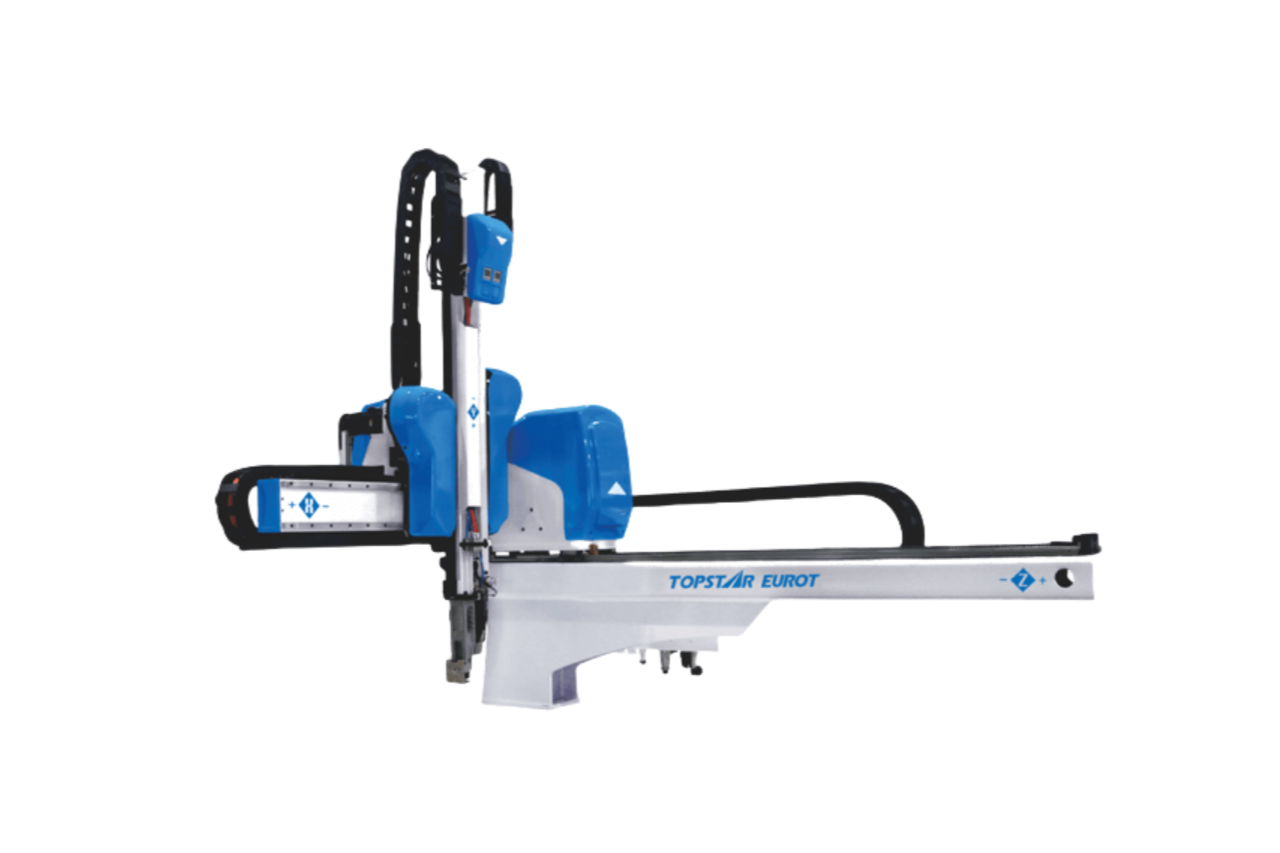
The rapid prototyping industry requires high precision, high efficiency and high flexibility to meet the needs of rapid product development and manufacturing. The Injection molding robotic arm can meet the high precision and high efficiency required in the rapid prototyping industry. This guide will share the features and advantages of the injection molding robotic arm, which is best designed for the rapid prototyping industry. Let you know how this technology can optimize and enhance your prototyping process, shorten cycle time and improve overall product quality.
Injection molding robotic arm: improve precision and accuracy
Precision and accuracy are crucial in rapid prototyping. The reason why Injection molding robotic arms are suitable is that they use high-rigidity precision sliding guides. It is able to maintain precise linear motion, and the rigidity of the guide prevents any bending or bending, ensuring that the robot arm follows a precise path. At the same time, the high-rigidity slide rails will not affect performance when supporting large weight loads, which is very important for injection molding robot arms that handle heavy molds and parts. The enhanced stability provided by these guides ensures smooth and consistent movement, reduces the risk of mechanical failure and improves the overall reliability of the robot system.
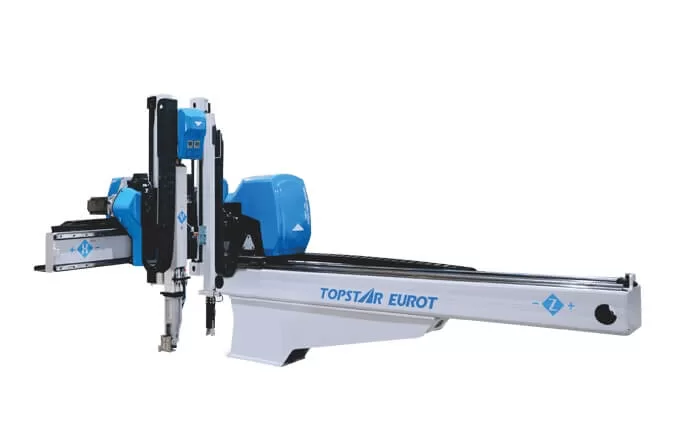
Speed up the injection molding process
Time is a very important factor for injection molding, and the ability to quickly produce and iterate prototypes can significantly affect the time of the entire product development. The main aim of the injection molding robot is made of lightweight and high-strength A6061 material, which reduces the weight by 20% and reduces 20 structural components. The servo motor drive increases the maximum speed by 10% and reduces the acceleration and deceleration time by 20%. While improving the overall operating performance, it also improves production efficiency. Through automated grasping, these robots greatly reduce the time required to produce each prototype. Advanced programming capabilities enable these robots to switch seamlessly to different tasks and configurations. This flexibility can be a good help for rapid prototyping because rapid prototyping production often requires multiple iterations and adjustments.
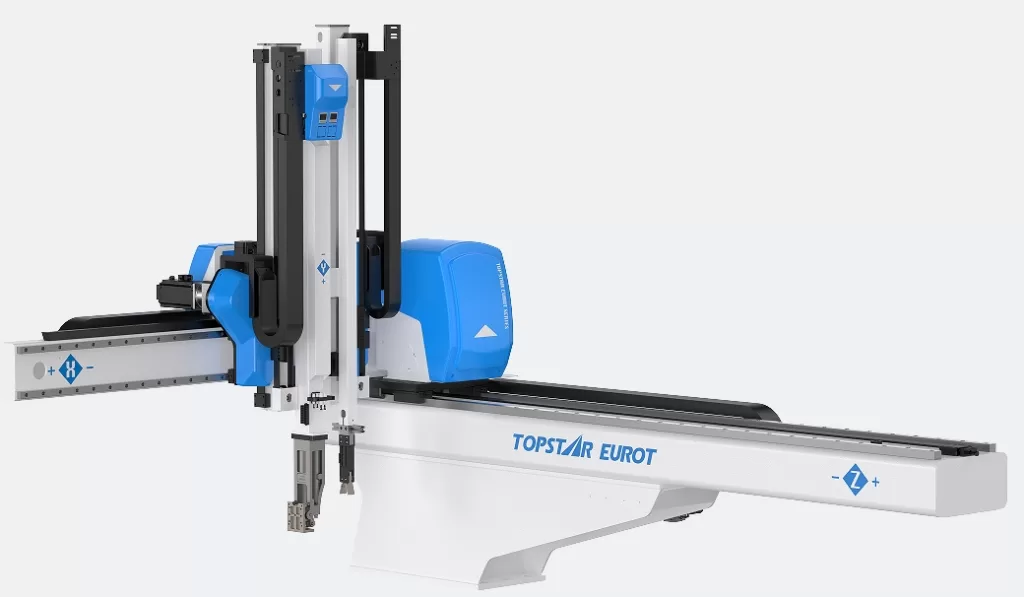
Higher performance of Injection molding robotic arm
The injection molding robot uses a built-in dual system, allowing customers to choose freely. It also has an RS485 communication interface and supports MODBUS RTU communication protocol. In addition, the large cylinder force cylinder used has a greater thrust, which increases the overall load-bearing capacity by 20% and can carry large parts. You can integrate them with the injection molding machine to synchronize the cycle and ensure smooth and efficient operation. This integration helps realise automated injection moulding workflow, reduce manual intervention and improve overall process control. The company independently developed the entire control system and can customize it according to customer needs.
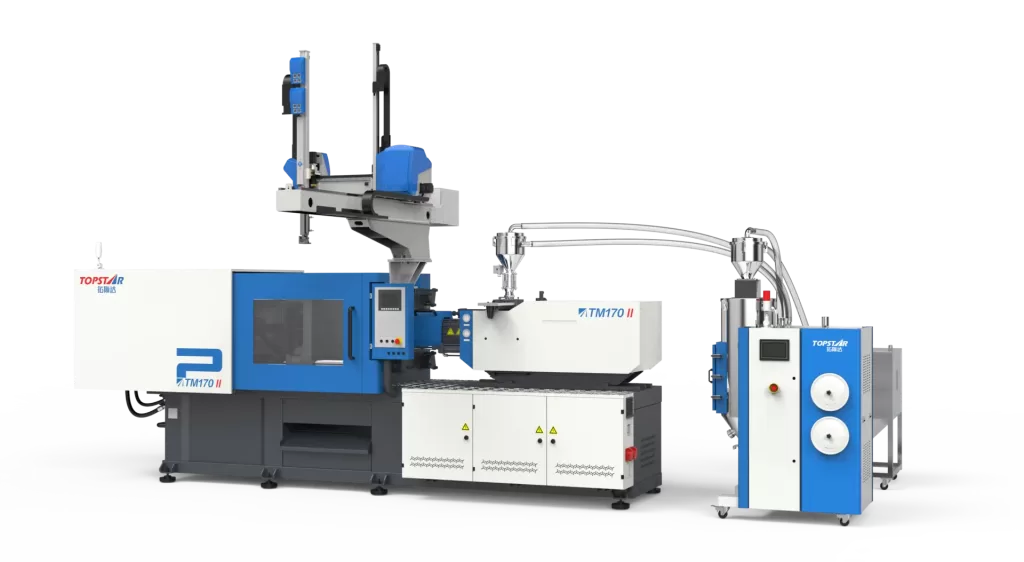
High energy-saving effect
The servo motor used in the injection molding robotic arm can accurately control and adjust power usage according to the load, thereby greatly reducing energy waste. The robot arm is made of lightweight and durable materials, which also helps to improve its energy-saving ability. By reducing the overall weight of the robot arm, less energy is required to move and operate. Advanced materials such as lightweight aluminium alloys provide the necessary durability while maintaining a low weight. This balance ensures that the robot arm can perform difficult tasks without consuming too much energy. In addition, the added servo automatic OFF function allows the servo motor to stop energizing when on standby, saving 10% of electricity.
Real-time remote monitoring
The injection molding robotic arm has advanced sensors and connection solutions to enable real-time remote monitoring.
Make rapid prototyping more flexible and efficient
Injection molding robots provide a comprehensive solution for the rapid prototyping industry and are the most suitable robots for the rapid prototyping industry. Through their high speed, high precision, and high-performance advantages, they improve the overall efficiency and quality of rapid prototyping in the production process, allowing them to remain competitive and responsive in the dynamic market of enterprises.
TRENDING POSTS
- What factors can cause delays in the injection molding process of plastic molding machine? 2024/07/22
- Exhibition Review| Topstar participates in InterPlas Thailand 2024 2024/07/22
- Star Case | Topstar helps Santong upgrade its intelligent plant 2024/07/22
- Topstar Special | National Science and Technology Workers Day 2024/07/22
HOT TOPIC
- .ervo motor-driven linear robots
- 1.0 guangdong topstar technology co. ltd
- 1.0 topstar china
- 1.0 topstar robot
- 11
- 2
- 21
- 23
- 3 axis robot
- 3 axis robots
- 3 in 1 Compact Dehumidifying Dryer
- 3-axis robot
- 3-axis robots
- 39
- 41
- 5-axis CNC machine
- 62
- accuracy
- Air Chillers
- all electric injection molding machine
- all electric injection molding machines
- All-electric injection molding machines
- and overall production quality. Therefore
- AP-RubberPlas
- automated injection molding machine
- Automation changed engineering
- automation of injection molding robots
- auxiliary machine
- Bench Injection Molding Machine
- Cabinet dryer manufacturers
- Cabinet dryers
- chiller
- CNC Drilling Machine
- CNC Drilling Machines
- cnc engraving machine manufacturer
- cnc laser cutting machine manufacturer
- CNC machine
- CNC Machine Center
- CNC Machine for Sale
- CNC Machine Manufacturing
- CNC Machine Tool
- CNC machine tool product
- CNC Machining Center
- CNC wood carving machine
- Cooling system
- Cross-Walking Single Axis Servo Cylinder Robot
- Cross-Walking Single-Axis Servo Cylinder Robot
- Cross-Walking Three-Axis/Five-Axis Servo Driven Robot
- cross-walking three-axis/five-axis servo-driven robot
- Dehumidifier Dryer
- Dehumidifying Dryer
- delta parallel robot
- Desktop Injection Molding Machine
- Desktop injection molding machines
- Desktop Molding Machine
- desktop plastic injection machine
- Desktop Plastic Injection Molding Machine
- direct clamp injection molding machine
- Direct clamp injection molding machines
- Dosing & mixing system
- Drilling Centers
- Drying and dehumidification system
- drying and dehumidifying equipment
- Drying and Dehumidifying System
- drying system
- effective and efficient. Cabinet dryers are also used in other industries where large quantities of material need to be dried
- efficient injection molding machine
- elbow hydraulic injection molding machines
- electric injection molding machine
- electric injection molding machines
- energy-efficient injection molding robot
- energy-saving injection molding machine
- etc. Among injection molding robots
- exhibition
- features of CNC machine
- Feeding And Conveying System
- Five Axis Machine Center
- Fully automatic injection molding machine
- Gathering Topstar
- giant injection molding machine
- GMU-600 5-Axis Machining Center
- Granulating & Recycling System
- Heavy duty injection molding machine
- High-precision electric molding machines
- high-precision plastic molding machines
- high-speed all electric injection molding machine
- Honeycomb rotor dehumidifier
- horizontal injection molding machine
- Horizontal Injection Molding Machines
- Horizontal Injection Moulding Machine
- Horizontal Mixer manufacturer
- How The CNC Machine Works
- hybrid injection molding machine
- hydraulic injection molding machine
- Hydraulic Injection Molding Machines
- in this article
- Industrial robot
- Industrial Robot Chinese brand
- industrial robot parts
- industrial robot supplier
- Industrial robots
- Industry Chain
- Injection Manipulator
- injection manipulator robot
- injection mold machines
- Injection molding
- Injection molding automation
- Injection Molding Automation Solution
- injection molding dryer
- Injection molding equipment
- injection molding hopper dryer
- Injection molding machine
- injection molding machine brand
- Injection Molding Machine Factory
- Injection Molding Machine Manufacture
- Injection molding machine manufacturer
- injection molding machine manufacturers
- Injection molding machine procurement
- injection molding machine robotic arm
- injection molding machine with a robot
- Injection molding machines
- injection molding material dehumidifying
- injection molding plant
- Injection Molding Robot
- injection molding robot arm
- Injection molding robot automation
- Injection molding robotic arm
- injection molding robots
- Injection moulding machine
- Injection Moulding Robots
- Injection Robot
- Injection robot arm
- Injection robot manufacturer
- Injection robot wholesale
- injection robots
- intelligent injection molding machines
- Introducing Injection Robot
- It is the best choice for drying large quantities of material at once. Cabinetmakers use these machines because they are fast
- large injection molding machine
- large injection molding machines
- Learn what industrial automation and robotics is
- linear robot
- linear robots
- low speed sound-proof granulator
- machine plastic molding
- make sure to add some! Improvements (2) Keyphrase in introduction: Your keyphrase or its synonyms appear in the first paragraph of the copy
- manipulator machine
- manufacturing
- medical grade injection molding machines
- medical injection molding machine
- medical injection molding machines
- micro injection molding machine
- middle speed granulator
- Mini CNC machine manufacturers.
- Mold Temperature Control System
- mold temperature controller
- mold temperature controllers
- molding material Dehumidifying System
- mould temperature control system
- mould temperature controller
- mould temperature controllers
- New electric injection molding machine
- nitrogen dryer manufacturer
- nitrogen dryer system manufacturer
- Oil type mold temperature controller
- Oil type mold temperature controllers
- open day
- Outbound links: No outbound links appear in this page. Add some! Images: No images appear on this page. Add some! Internal links: No internal links appear in this page
- PET Preform injection molding
- phone case maker machine
- phone case making machine
- plastic bottle making machine
- plastic bottle manufacturing
- plastic bucket making machine
- plastic bucket manufacturing
- Plastic chair making machine
- plastic forming equipment
- plastic hopper dryer
- plastic injection machine
- plastic injection machines
- plastic injection molding
- Plastic injection molding equipment
- Plastic injection molding machine
- Plastic Injection Molding Machines
- plastic injection moulding machine
- plastic injection robot
- Plastic Molding machine
- Plastic Molding Machines
- plastic molding press
- plastic moulding machine
- plastic phone case making machine
- plastic-molding machine
- powerful granulator
- Powerful Type Sound-Proof Granulator
- precision injection molding
- precision injection molding machines
- production of plastic seats
- pure water mould temperature controller
- Robot injection molding
- robot injection molding machine
- robot manufacturing companies
- Robotic arm for injection molding machine
- robotic injection molding machines
- robotics in injection molding
- SCARA robot
- SCARA robots
- Service-oriented manufacturing
- Servo Cylinder Robot
- servo driven robot
- Servo Driven Robots
- servo injection robots
- servo motor-driven linear robots
- servo-driven 3-axis robot
- Servo-Driven Robot
- Setup of injection machine
- Silicone Injection Molding Machine
- six-axis industrial robot
- Stainless Hopper Dryer
- Stainless Hopper Dryers
- star club
- swing arm robot
- take-out robots
- the choice between servo-driven robots and hydraulic robots will have a certain impact on efficiency
- the most popular injection molding machine
- the type of injection molding robot
- toggle clamp injection molding machine
- Toggle Hydraulic Injection Molding Machines
- toggle injection molding machine
- Top 10 brands of injection robots
- Topstar
- Topstar Engineering
- Topstar Industrial Robots
- Topstar injection molding intelligent
- Topstar Scara Robots
- Useful Injection molding machine
- Vertical machining centers
- volumetric type blender
- water chiller
- water chillers
- water distributor
- water type mold temperature controller
- Water Type MoldTemperature Controller
- Water-Type Mould Temperature Controllers
- We often face choices when performing injection molding. We will choose the type of injection molding machine
- wholesale of injection molding machines
- x carve CNC
- 热门查询 点击次数 展示 排名 topstar