Star Case | Topstar helps Santong upgrade its intelligent plant
2024/06/12 By topstar
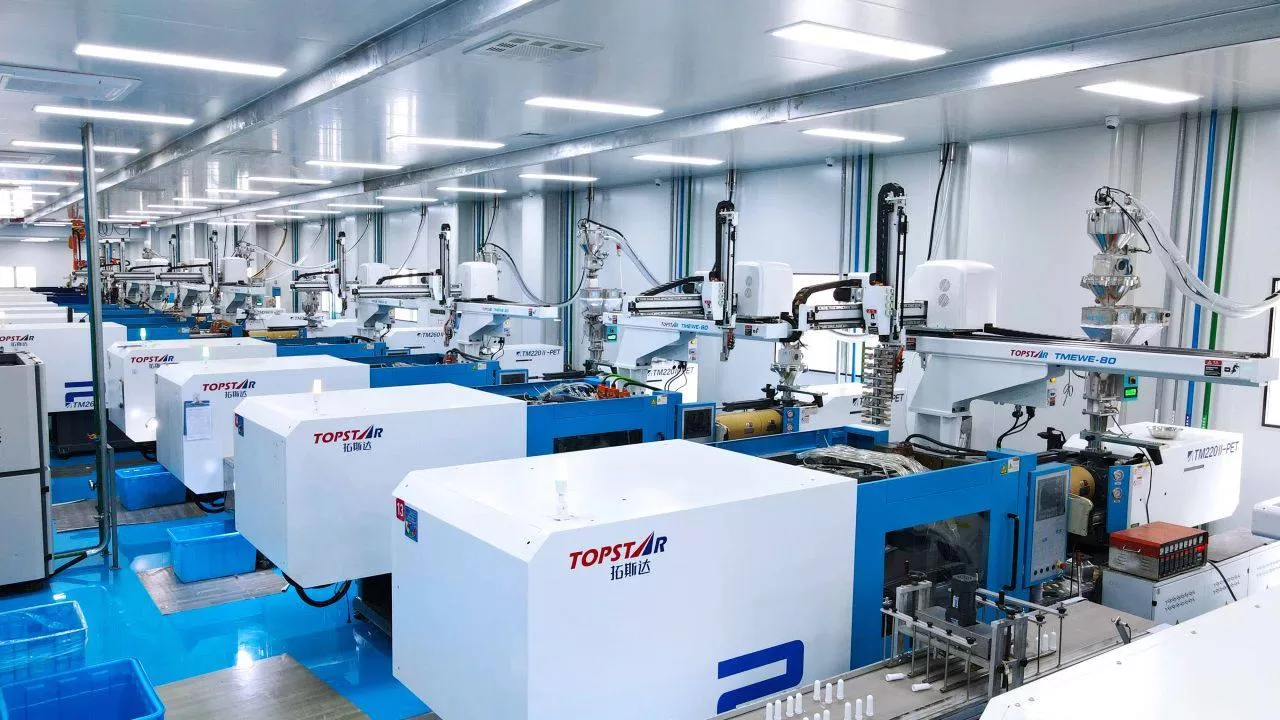
“I want to build an intelligent, modern, and digital plant” Miss Yan, General Manager of Zhejiang Santong Plastic Industry Co., Ltd. expressed her expectations of the new plant to us.
Zhejiang Santong Plastic Industry Co., Ltd. is located in Yuhuan City, Taizhou, Zhejiang. It is a professional plastic packaging manufacturer. There are more than 280 employees here, including R&D, production, manufacturing, and sales departments, which ensures Santong’s strong R&D and production capacity.
Santong’s packaging materials are mainly used in FMCG, medical devices, and food packaging. The European and American markets support 70% of its business, so the market has very high requirements for product quality. Facing the challenge of high production standards, Santong expects to introduce the Topstar Intelligent Whole Plant Solution to enhance the plant manufacturing level.
Equipment Intelligence: custom injection molding machines improve production efficiency
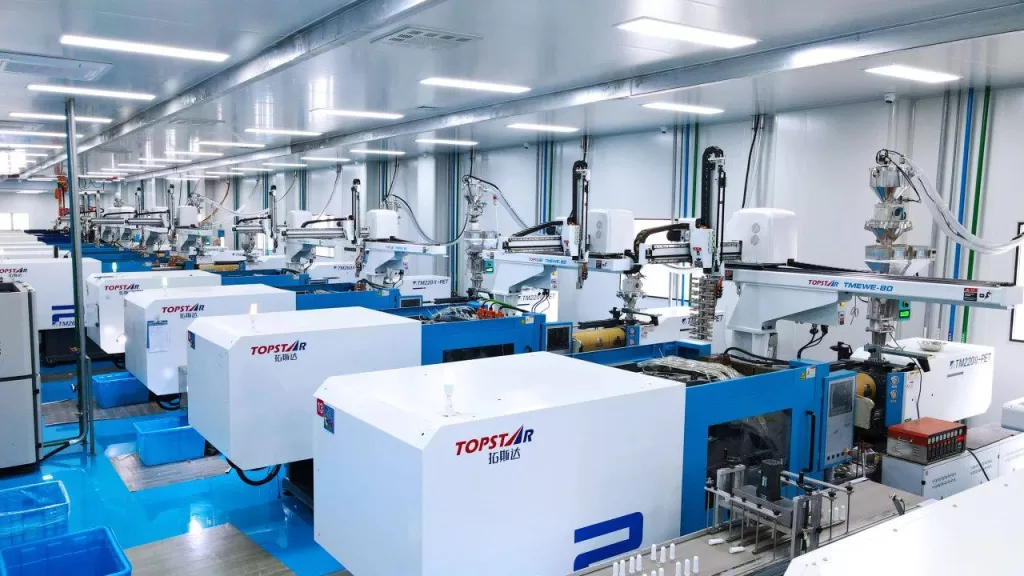
“Injection molding of preforms is very demanding. If the injection molding is not precise, a slight force can break the neck of the bottle”. Santong’s packaging preforms are made of PET material, which is highly viscous and temperature sensitive. Inappropriate temperature will lead to poor transparency and uneven thickness of the products, thus causing waste of raw materials.
Aiming at the PET raw material’s molding characteristics, Topstar provides a PET special injection molding machine for Santong. The injection molding machine uses a special screw for preforms, a high torque motor, and an enlarged power system, which improves the overall plasticizing efficiency by more than 20%. At the same time, precise temperature control can greatly reduce air bubbles, and impurity defects, to ensure the transparency of the preforms and yield rate.
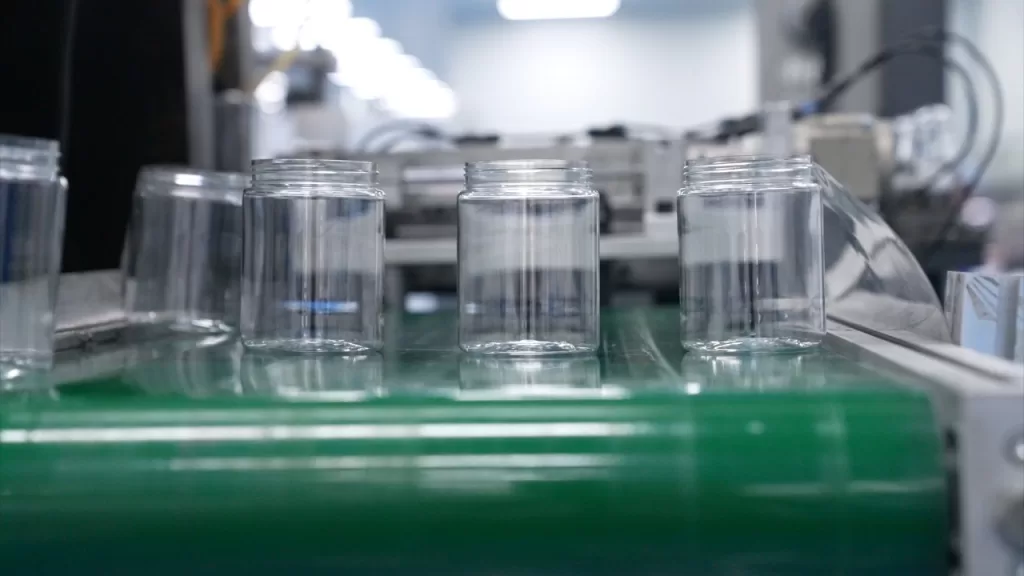
Santong wants to improve production efficiency and save production costs through integration. Topstar’s self-developed control system supports injection molding machine linkage of manipulator and auxiliary machines. The key parameters such as pressure, temperature, speed, etc. of the auxiliary machines can be interlocked by the IMM, which can greatly improve the response rate of the production process.
The PET-customized IMM is also fitted with an infrared heating coil, which reduces energy consumption in the production process by improving the efficiency of heat conversion. Experimental data measured the effective energy-saving rate of the infrared heating coil to be about 20%.
“You didn’t cut corners with the materials used in your injection molding machine, and the machine is stronger. The machine is stable when used.” Ms Yan, General Manager of Santong Plastic Industry, commented.
Based on the software control capability, Topstar helped Santong optimize the back-end automation process. After the preforms are formed, they are transferred to the blow molding process with the assistance of a conveyor belt. After the blow molding process, the preform is finally formed into a bottle. The whole process of automation uses intelligent control, saving labor costs and improving production efficiency.
Industrial modernization: smart plant solutions optimize production processes
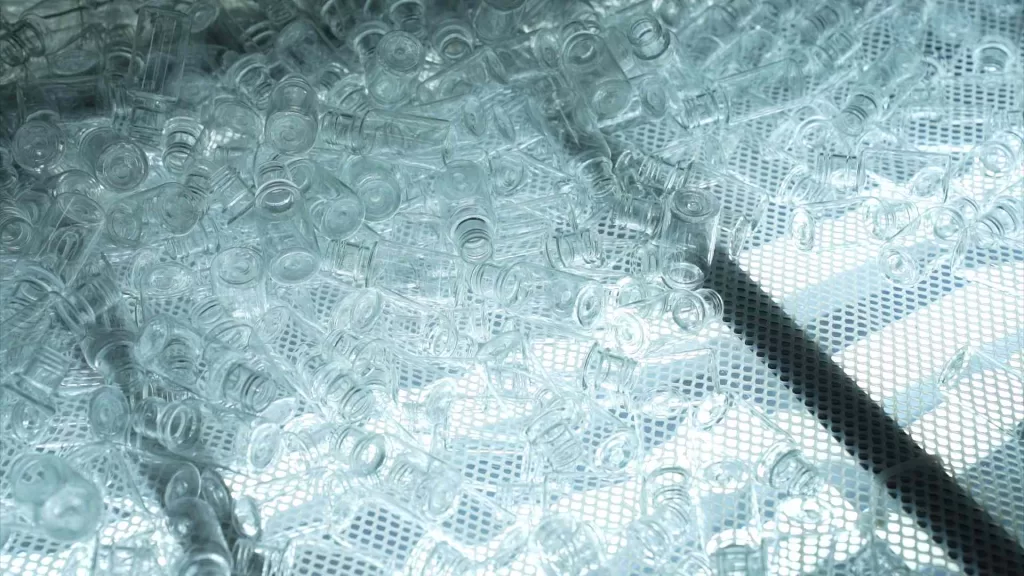
“In the beginning, I wanted to build an intelligent plant. After taking some detours and visits, I finally chose you (Topstar) as a supplier after inspection.” Miss Yan said.
Intelligent whole plant planning is a systematic project. Traditional plant planning relies on empiricism. With the development of the industry, intelligent whole plant planning in the program design subcontract mode and integrated turnkey mode.
Topstar provides integrated turnkey intelligent whole plant solutions. It is built on its core technology and supported by three major equipment as products. The solution integrates diversified product business lines, highly compatible equipment, and self-developed systems. Through the collaborative operation of an intelligent energy and environment management system, central feeding system, and injection molding integrated machine for the injection molding process, it reduces the problems of delayed and poor signal from equipment and system, thus making the operation and management of the plant easier.
“Currently, we moved into a new plant and all your systems have been running for a month, and they are very stable.” Miss Yan commented.
Whole-plant digitization: The MES system makes production management easier
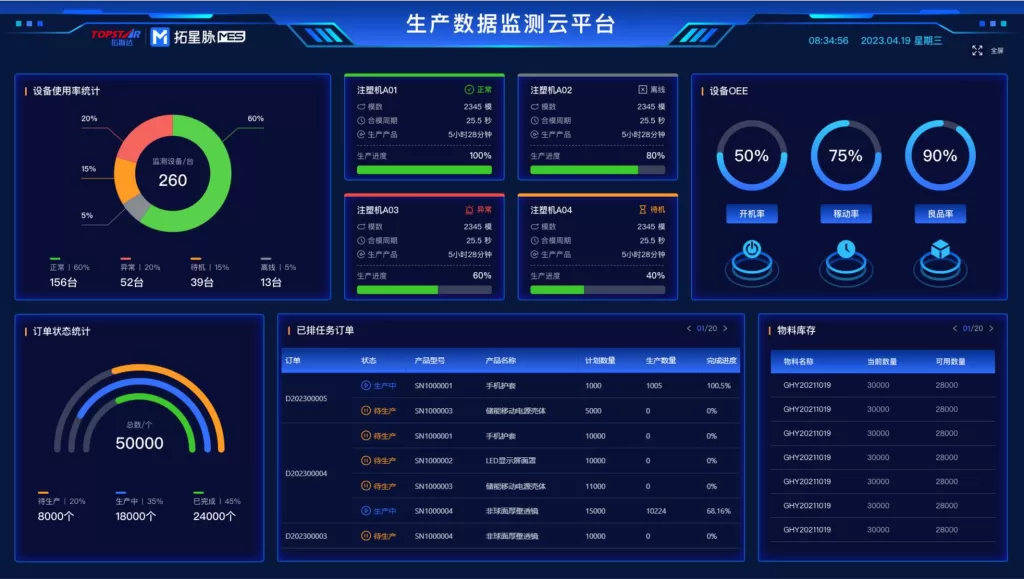
“We need to introduce the MES system next to facilitate the management of the plant’s production.” Miss Yan said.
Intelligence, modernization, and digitalization are the future directions of Santong’s manufacturing. After introducing an intelligent energy management system, central feeding system, PET custom IMM, and back-end blow molding automation, Santong will introduce the MES system.
Topstar MES system can realize the signal interface interconnection of multiple equipment. It can autonomously collect physical data from injection molding machines, auxiliary machines, material supply system, and energy management system so that managers can grasp the production situation of the workshop in real time.
“We will continue to plow deeper into the plastic products industry. We also hope that you (Topstar) will help Santong to become a truly intelligent, digital, and modern plant with the advantages of intelligence.” Miss Yan expressed her expectations for the future development of Santong.
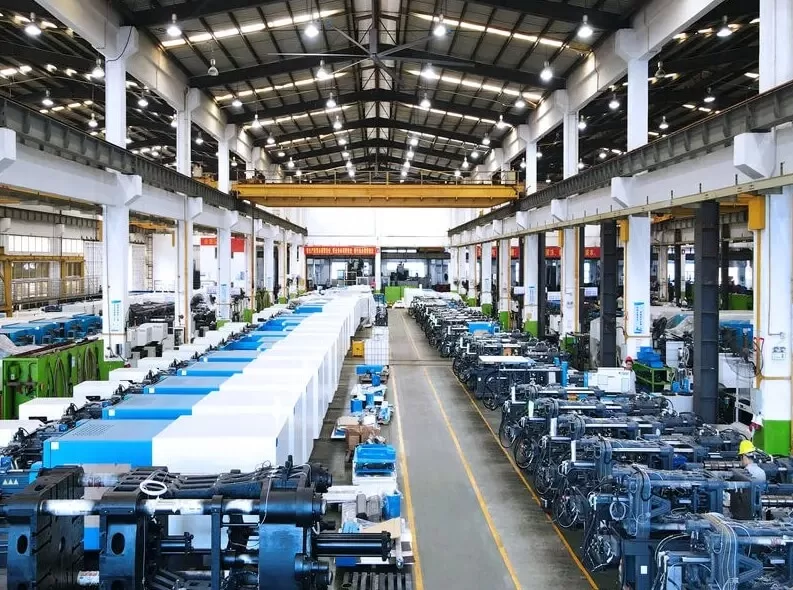
In the future, Topstar will continue to increase investment in research and development to promote open innovation. Guided by market demand, we will provide customers with smarter products and solutions, and continue encouraging the industry’s sustainable development.
Topstar’s corporate mission is to “make industrial manufacturing better”. Topstar adheres to the vision of “to be the world’s leading smart equipment supplier” and creates an intelligent hardware platform driven by core technologies through intelligent equipment centered on industrial robots, injection molding machines, and five-axis CNC machines, as well as three core technologies of control, servo, and vision, to provide manufacturing enterprises with an overall intelligent plant solution.
TRENDING POSTS
- What factors can cause delays in the injection molding process of plastic molding machine? 2024/06/12
- Exhibition Review| Topstar participates in InterPlas Thailand 2024 2024/06/12
- Star Case | Topstar helps Santong upgrade its intelligent plant 2024/06/12
- Topstar Special | National Science and Technology Workers Day 2024/06/12
HOT TOPIC
- 3 in 1 Compact Dehumidifying Dryer
- 5-axis CNC machine
- accuracy
- Air Chillers
- all electric injection molding machine
- All-electric injection molding machines
- and overall production quality. Therefore
- AP-RubberPlas
- automated injection molding machine
- Automation changed engineering
- automation of injection molding robots
- auxiliary machine
- Bench Injection Molding Machine
- Cabinet dryer manufacturers
- Cabinet dryers
- chiller
- CNC Drilling Machine
- CNC Drilling Machines
- cnc engraving machine manufacturer
- cnc laser cutting machine manufacturer
- CNC machine
- CNC Machine Center
- CNC Machine for Sale
- CNC Machine Manufacturing
- CNC Machine Tool
- CNC machine tool product
- CNC Machining Center
- CNC wood carving machine
- Cooling system
- Cross-Walking Single Axis Servo Cylinder Robot
- Cross-Walking Single-Axis Servo Cylinder Robot
- Cross-Walking Three-Axis/Five-Axis Servo Driven Robot
- cross-walking three-axis/five-axis servo-driven robot
- Dehumidifier Dryer
- Dehumidifying Dryer
- delta parallel robot
- Desktop Injection Molding Machine
- Desktop injection molding machines
- Desktop Molding Machine
- desktop plastic injection machine
- Desktop Plastic Injection Molding Machine
- direct clamp injection molding machine
- Direct clamp injection molding machines
- Dosing & mixing system
- Drilling Centers
- Drying and dehumidification system
- drying and dehumidifying equipment
- Drying and Dehumidifying System
- drying system
- effective and efficient. Cabinet dryers are also used in other industries where large quantities of material need to be dried
- efficient injection molding machine
- elbow hydraulic injection molding machines
- electric injection molding machine
- electric injection molding machines
- etc. Among injection molding robots
- exhibition
- features of CNC machine
- Feeding And Conveying System
- Five Axis Machine Center
- Fully automatic injection molding machine
- Gathering Topstar
- giant injection molding machine
- GMU-600 5-Axis Machining Center
- Granulating & Recycling System
- Heavy duty injection molding machine
- Honeycomb rotor dehumidifier
- horizontal injection molding machine
- Horizontal Injection Molding Machines
- Horizontal Injection Moulding Machine
- Horizontal Mixer manufacturer
- How The CNC Machine Works
- hybrid injection molding machine
- hydraulic injection molding machine
- Hydraulic Injection Molding Machines
- in this article
- Industrial robot
- Industrial Robot Chinese brand
- industrial robot parts
- industrial robot supplier
- Industrial robots
- Industry Chain
- Injection Manipulator
- injection mold machines
- Injection molding
- Injection molding automation
- Injection Molding Automation Solution
- injection molding dryer
- Injection molding equipment
- injection molding hopper dryer
- Injection molding machine
- injection molding machine brand
- Injection Molding Machine Factory
- Injection Molding Machine Manufacture
- Injection molding machine manufacturer
- injection molding machine manufacturers
- Injection molding machine procurement
- injection molding machine robotic arm
- injection molding machine with a robot
- Injection molding machines
- injection molding material dehumidifying
- injection molding plant
- Injection Molding Robot
- injection molding robot arm
- Injection molding robot automation
- Injection molding robotic arm
- injection molding robots
- Injection Moulding Robots
- Injection Robot
- Injection robot arm
- Injection robot manufacturer
- Injection robot wholesale
- injection robots
- intelligent injection molding machines
- Introducing Injection Robot
- It is the best choice for drying large quantities of material at once. Cabinetmakers use these machines because they are fast
- large injection molding machine
- Learn what industrial automation and robotics is
- low speed sound-proof granulator
- machine plastic molding
- make sure to add some! Improvements (2) Keyphrase in introduction: Your keyphrase or its synonyms appear in the first paragraph of the copy
- manipulator machine
- manufacturing
- micro injection molding machine
- middle speed granulator
- Mini CNC machine manufacturers.
- Mold Temperature Control System
- mold temperature controller
- molding material Dehumidifying System
- mould temperature controller
- mould temperature controllers
- New electric injection molding machine
- nitrogen dryer manufacturer
- nitrogen dryer system manufacturer
- Oil type mold temperature controller
- open day
- Outbound links: No outbound links appear in this page. Add some! Images: No images appear on this page. Add some! Internal links: No internal links appear in this page
- PET Preform injection molding
- phone case maker machine
- phone case making machine
- plastic bottle making machine
- plastic bottle manufacturing
- plastic bucket making machine
- plastic bucket manufacturing
- Plastic chair making machine
- plastic forming equipment
- plastic hopper dryer
- plastic injection machine
- plastic injection machines
- plastic injection molding
- Plastic injection molding equipment
- Plastic injection molding machine
- Plastic Injection Molding Machines
- plastic injection robot
- Plastic Molding machine
- Plastic Molding Machines
- plastic molding press
- plastic phone case making machine
- plastic-molding machine
- powerful granulator
- Powerful Type Sound-Proof Granulator
- production of plastic seats
- Robot injection molding
- robot injection molding machine
- robot manufacturing companies
- Robotic arm for injection molding machine
- robotic injection molding machines
- robotics in injection molding
- SCARA robot
- SCARA robots
- Service-oriented manufacturing
- Servo Cylinder Robot
- servo driven robot
- Servo Driven Robots
- servo injection robots
- Servo-Driven Robot
- Setup of injection machine
- Silicone Injection Molding Machine
- six-axis industrial robot
- Stainless Hopper Dryer
- Stainless Hopper Dryers
- star club
- swing arm robot
- the choice between servo-driven robots and hydraulic robots will have a certain impact on efficiency
- the most popular injection molding machine
- the type of injection molding robot
- toggle clamp injection molding machine
- Toggle Hydraulic Injection Molding Machines
- toggle injection molding machine
- Top 10 brands of injection robots
- Topstar
- Topstar Engineering
- Topstar Industrial Robots
- Topstar injection molding intelligent
- Topstar Scara Robots
- Useful Injection molding machine
- Vertical machining centers
- volumetric type blender
- water chiller
- water chillers
- water distributor
- Water Type MoldTemperature Controller
- We often face choices when performing injection molding. We will choose the type of injection molding machine
- wholesale of injection molding machines
- x carve CNC