Plastic injection molding machine with safety protection function
2024/05/13 By Topstar
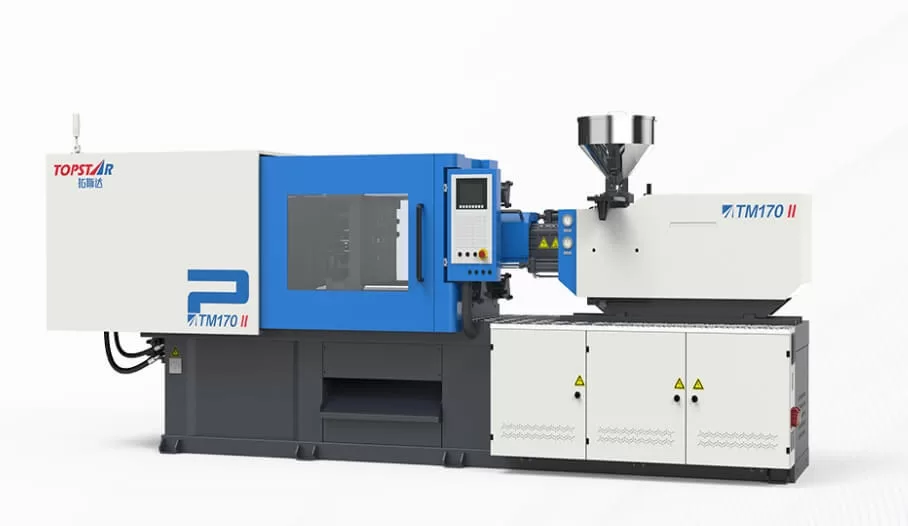
In addition to paying attention to the injection molding functional characteristics of plastic injection molding machine, we also need to pay attention to their safety protection functions to ensure that operators and workers can work safely. Topstar’s injection molding machine series has various safety protection functions to minimize risks and prevent accidents. This guide will explain how these safety features protect operator health while improving efficiency, productivity, and overall performance.
Automatic emergency stop system for plastic injection molding machines
One of the key safety protection features of plastic injection molding machines is the automatic emergency stop system. By automatically cutting power to the machine’s motors and hydraulic systems, they can immediately stop machine operation in case of a serious error, malfunction, or hazardous situation. Empowering operators to resolve issues and safely resume production quickly. The automatic emergency stop system has sensors distributed throughout the plastic injection molding machine. Various parameters, such as temperature, pressure, position, and motion, can be monitored. If an abnormality or security breach occurs, the sensor triggers an alarm signal, allowing immediate action to be taken.
Safety interlocking mechanism of plastic injection molding machine
Certain actions or operations can only be performed under specific conditions or sequences to minimize the risk of accident or damage. For example, interlocks may prevent a machine from operating if a safety door is open, a mold is not secured properly, or critical components are not in the correct position.
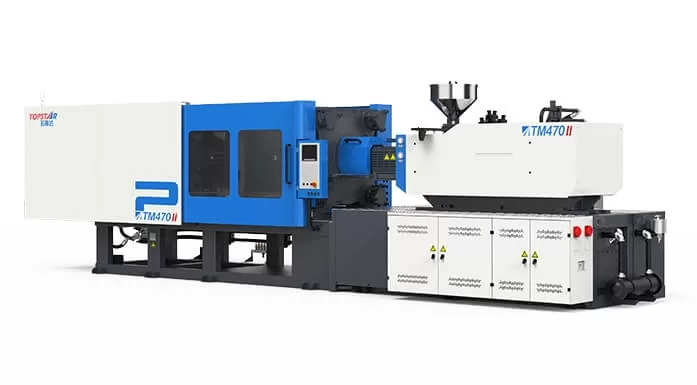
One of the main functions of safety interlocking mechanisms is preventing entry into hazardous areas while the plastic injection molding machine operates. This includes door interlocks, which are installed on access doors and panels. Install relevant safety protection devices around high-risk areas, such as injection units, mold areas, and door interlocks.
Protecting mask
Topstar’s entire range of plastic injection molding machines are equipped with protective covers to protect operators from potential hazards such as flying debris or plastic parts. Install physical barriers around the machine’s work area to prevent accidental contact or hazard exposure. Additionally, transparent guards allow operators to monitor the molding process without compromising safety, providing an extra layer of protection without impeding visibility. In addition, protective covers protect critical machine components from dust, debris, and contaminants. Plastic injection molding machines produce a lot of noise during operation, and the protective cover also acts as a sound barrier, suppressing noise emissions and creating a quieter working environment.
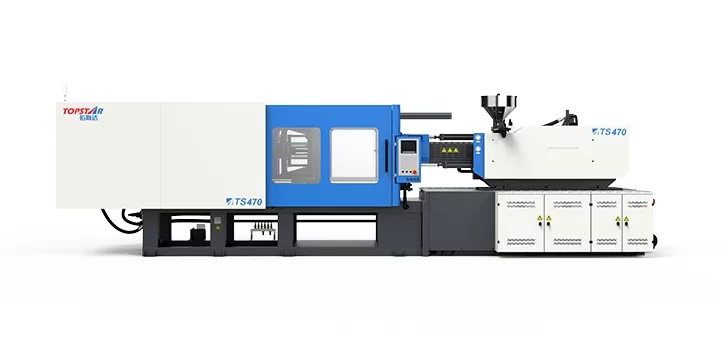
Security sensors and alarms
Safety sensors and alarms can alert operators to potential hazards during the operation of plastic injection molding machines. These sensors can detect a variety of conditions. Manufacturers deploy pressure sensors throughout the hydraulic system of plastic injection molding machines to monitor hydraulic levels. They provide real-time feedback on the pressure applied during the molding process’s injection, clamping, and ejection stages. Abnormal pressure readings, such as excessive or sudden drops in pressure, may indicate hydraulic system failure or mold issues.
Temperature sensors monitor temperature levels in critical areas, including barrels, nozzles, molds, and hydraulic systems. These sensors can detect deviations from preset temperature thresholds, signaling potential overheating, cooling system failure, or material degradation. Emergency stop buttons are prominently located on the control panel and throughout the work area, providing operators with a quick and convenient way to stop machine operation in an emergency.
Integrated safety PLC system
Topstar’s plastic injection molding machines have a safety programmable logic controller (PLC) system, which is a central control center for monitoring and managing safety functions. These advanced systems utilize complex algorithms and logic programming to coordinate safety interlocks, emergency stop sequences, and sensor feedback. The integrated safety PLC system continuously monitors various parameters and inputs from safety sensors installed throughout the injection molding machine. Integrated safety PLC systems provide configuration and programming flexibility to accommodate different machine configurations, process requirements, and safety standards. Use intuitive programming software to easily customize and configure safety features for seamless integration with existing control systems and equipment.
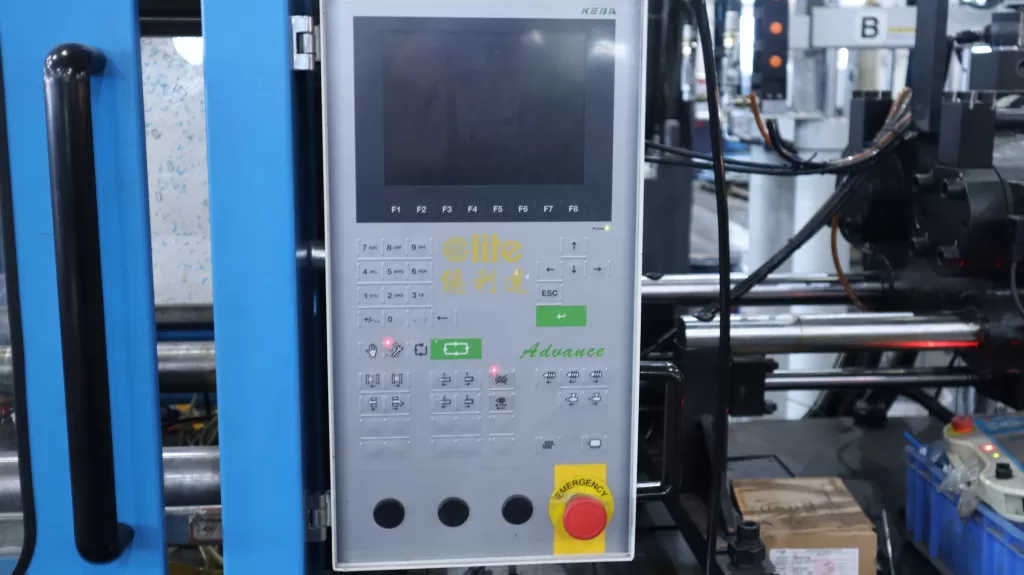
Security first
Plastic injection molding machines equipped with safety features are critical in ensuring safety for operators and manufacturing workers. These features, from automatic emergency stop systems and safety interlocks to protective shields, work together to reduce risk, prevent accidents, and promote a safe working environment.
TRENDING POSTS
- What factors can cause delays in the injection molding process of plastic molding machine? 2024/05/13
- Exhibition Review| Topstar participates in InterPlas Thailand 2024 2024/05/13
- Star Case | Topstar helps Santong upgrade its intelligent plant 2024/05/13
- Topstar Special | National Science and Technology Workers Day 2024/05/13
HOT TOPIC
- 3 in 1 Compact Dehumidifying Dryer
- 5-axis CNC machine
- accuracy
- Air Chillers
- all electric injection molding machine
- All-electric injection molding machines
- and overall production quality. Therefore
- AP-RubberPlas
- automated injection molding machine
- Automation changed engineering
- automation of injection molding robots
- auxiliary machine
- Bench Injection Molding Machine
- Cabinet dryer manufacturers
- Cabinet dryers
- chiller
- CNC Drilling Machine
- CNC Drilling Machines
- cnc engraving machine manufacturer
- cnc laser cutting machine manufacturer
- CNC machine
- CNC Machine Center
- CNC Machine for Sale
- CNC Machine Manufacturing
- CNC Machine Tool
- CNC machine tool product
- CNC Machining Center
- CNC wood carving machine
- Cooling system
- Cross-Walking Single Axis Servo Cylinder Robot
- Cross-Walking Single-Axis Servo Cylinder Robot
- Cross-Walking Three-Axis/Five-Axis Servo Driven Robot
- cross-walking three-axis/five-axis servo-driven robot
- Dehumidifier Dryer
- Dehumidifying Dryer
- delta parallel robot
- Desktop Injection Molding Machine
- Desktop injection molding machines
- Desktop Molding Machine
- desktop plastic injection machine
- Desktop Plastic Injection Molding Machine
- direct clamp injection molding machine
- Direct clamp injection molding machines
- Dosing & mixing system
- Drilling Centers
- Drying and dehumidification system
- drying and dehumidifying equipment
- Drying and Dehumidifying System
- drying system
- effective and efficient. Cabinet dryers are also used in other industries where large quantities of material need to be dried
- efficient injection molding machine
- elbow hydraulic injection molding machines
- electric injection molding machine
- electric injection molding machines
- etc. Among injection molding robots
- exhibition
- features of CNC machine
- Feeding And Conveying System
- Five Axis Machine Center
- Fully automatic injection molding machine
- Gathering Topstar
- giant injection molding machine
- GMU-600 5-Axis Machining Center
- Granulating & Recycling System
- Heavy duty injection molding machine
- Honeycomb rotor dehumidifier
- horizontal injection molding machine
- Horizontal Injection Molding Machines
- Horizontal Injection Moulding Machine
- Horizontal Mixer manufacturer
- How The CNC Machine Works
- hybrid injection molding machine
- hydraulic injection molding machine
- Hydraulic Injection Molding Machines
- in this article
- Industrial robot
- Industrial Robot Chinese brand
- industrial robot parts
- industrial robot supplier
- Industrial robots
- Industry Chain
- Injection Manipulator
- injection mold machines
- Injection molding
- Injection molding automation
- Injection Molding Automation Solution
- injection molding dryer
- Injection molding equipment
- injection molding hopper dryer
- Injection molding machine
- injection molding machine brand
- Injection Molding Machine Factory
- Injection Molding Machine Manufacture
- Injection molding machine manufacturer
- injection molding machine manufacturers
- Injection molding machine procurement
- injection molding machine robotic arm
- injection molding machine with a robot
- Injection molding machines
- injection molding material dehumidifying
- injection molding plant
- Injection Molding Robot
- injection molding robot arm
- Injection molding robot automation
- Injection molding robotic arm
- injection molding robots
- Injection Moulding Robots
- Injection Robot
- Injection robot arm
- Injection robot manufacturer
- Injection robot wholesale
- injection robots
- intelligent injection molding machines
- Introducing Injection Robot
- It is the best choice for drying large quantities of material at once. Cabinetmakers use these machines because they are fast
- large injection molding machine
- Learn what industrial automation and robotics is
- low speed sound-proof granulator
- machine plastic molding
- make sure to add some! Improvements (2) Keyphrase in introduction: Your keyphrase or its synonyms appear in the first paragraph of the copy
- manipulator machine
- manufacturing
- micro injection molding machine
- middle speed granulator
- Mini CNC machine manufacturers.
- Mold Temperature Control System
- mold temperature controller
- molding material Dehumidifying System
- mould temperature controller
- mould temperature controllers
- New electric injection molding machine
- nitrogen dryer manufacturer
- nitrogen dryer system manufacturer
- Oil type mold temperature controller
- open day
- Outbound links: No outbound links appear in this page. Add some! Images: No images appear on this page. Add some! Internal links: No internal links appear in this page
- PET Preform injection molding
- phone case maker machine
- phone case making machine
- plastic bottle making machine
- plastic bottle manufacturing
- plastic bucket making machine
- plastic bucket manufacturing
- Plastic chair making machine
- plastic forming equipment
- plastic hopper dryer
- plastic injection machine
- plastic injection machines
- plastic injection molding
- Plastic injection molding equipment
- Plastic injection molding machine
- Plastic Injection Molding Machines
- plastic injection robot
- Plastic Molding machine
- Plastic Molding Machines
- plastic molding press
- plastic phone case making machine
- plastic-molding machine
- powerful granulator
- Powerful Type Sound-Proof Granulator
- production of plastic seats
- Robot injection molding
- robot injection molding machine
- robot manufacturing companies
- Robotic arm for injection molding machine
- robotic injection molding machines
- robotics in injection molding
- SCARA robot
- SCARA robots
- Service-oriented manufacturing
- Servo Cylinder Robot
- servo driven robot
- Servo Driven Robots
- servo injection robots
- Servo-Driven Robot
- Setup of injection machine
- Silicone Injection Molding Machine
- six-axis industrial robot
- Stainless Hopper Dryer
- Stainless Hopper Dryers
- star club
- swing arm robot
- the choice between servo-driven robots and hydraulic robots will have a certain impact on efficiency
- the most popular injection molding machine
- the type of injection molding robot
- toggle clamp injection molding machine
- Toggle Hydraulic Injection Molding Machines
- toggle injection molding machine
- Top 10 brands of injection robots
- Topstar
- Topstar Engineering
- Topstar Industrial Robots
- Topstar injection molding intelligent
- Topstar Scara Robots
- Useful Injection molding machine
- Vertical machining centers
- volumetric type blender
- water chiller
- water chillers
- water distributor
- Water Type MoldTemperature Controller
- We often face choices when performing injection molding. We will choose the type of injection molding machine
- wholesale of injection molding machines
- x carve CNC