Plastic injection molding machine solutions specifically designed for PET materials
2025/01/08 By Topstar
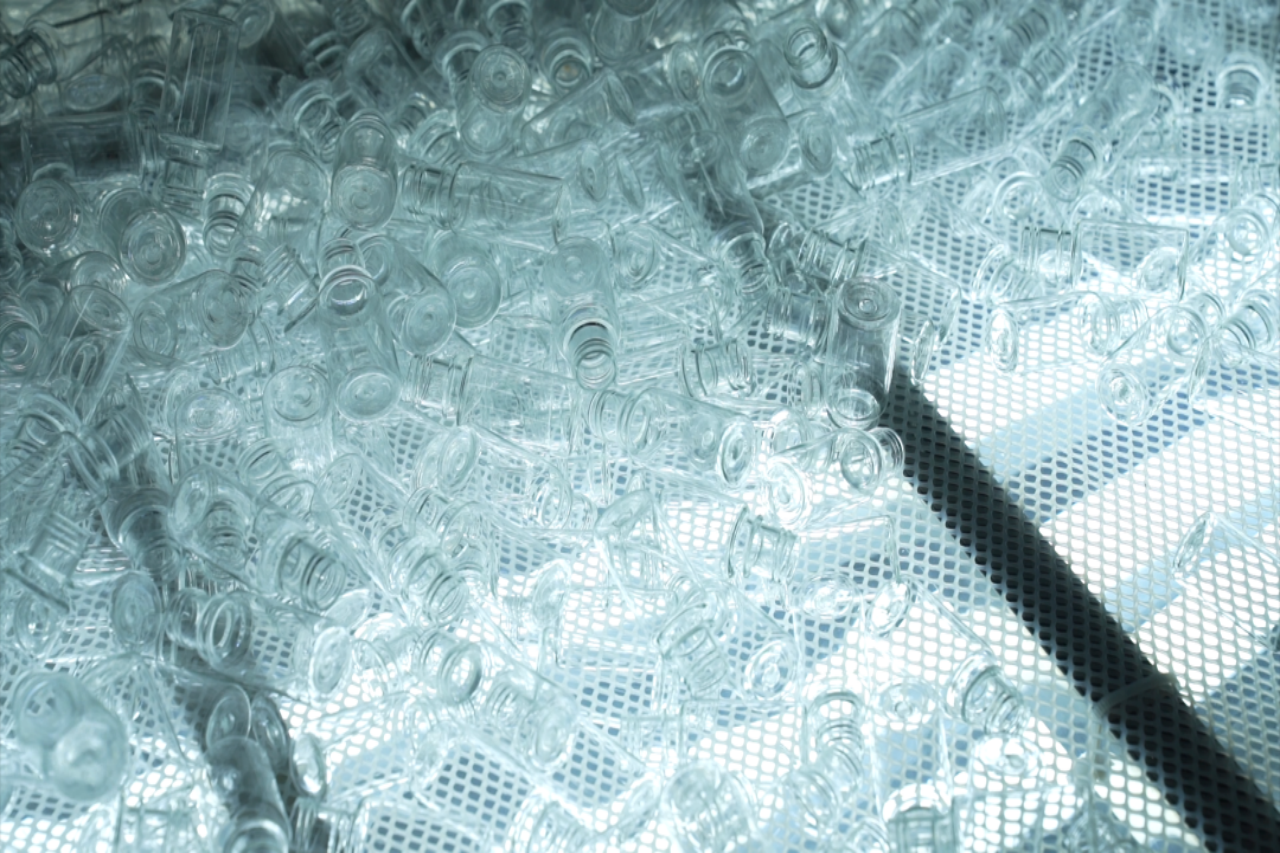
The packaging bottles commonly used in daily chemical products are mainly made of PET material. This material has high viscosity and is sensitive to temperature. Improper temperature can easily cause poor product permeability and uneven wall thickness, resulting in waste of raw materials and increased production costs. If the preform is not suitable during injection molding, only a slight external force can cause the bottleneck or bottle mouth to break. Given the molding difficulties of PET raw materials, Topstar provides PET-specific plastic injection molding machine, which use special screws, high-torque motors, and increased power systems to improve the overall plasticization efficiency by more than 20%. At the same time, it also dramatically reduces the defects such as bubbles and impurities that may occur during the molding process, ensuring the permeability and yield rate of the molded preforms.
Demand for plastic injection molding machine for PET materials
The high viscosity characteristics of PET require specific molding solutions to maintain optimal production quality and efficiency. Generally speaking, traditional plastic injection molding machines may find it difficult to cope with the challenges brought by PET materials. They are prone to bubbles, impurities, or insufficient plasticization, which may cause defects in molded parts.
The plastic injection molding machine designed for PET materials provided by Topstar uses a dedicated screw, a high-torque motor, and a power system. All these functions work together to increase plasticizing efficiency by more than 20%. While ensuring product quality, Topstar also meets the needs of improving production efficiency and saving costs. Based on the integrated design concept of the injection molding process, the PET-specific plastic injection molding machine has a self-developed control system that supports the host-linked robot signal, the host-linked peripheral auxiliary pressure, temperature, and other key process parameters to improve production efficiency. In addition, the machine uses an infrared heating coil to save energy by about 20%, enhance thermal energy conversion efficiency, and reduce energy consumption during production.
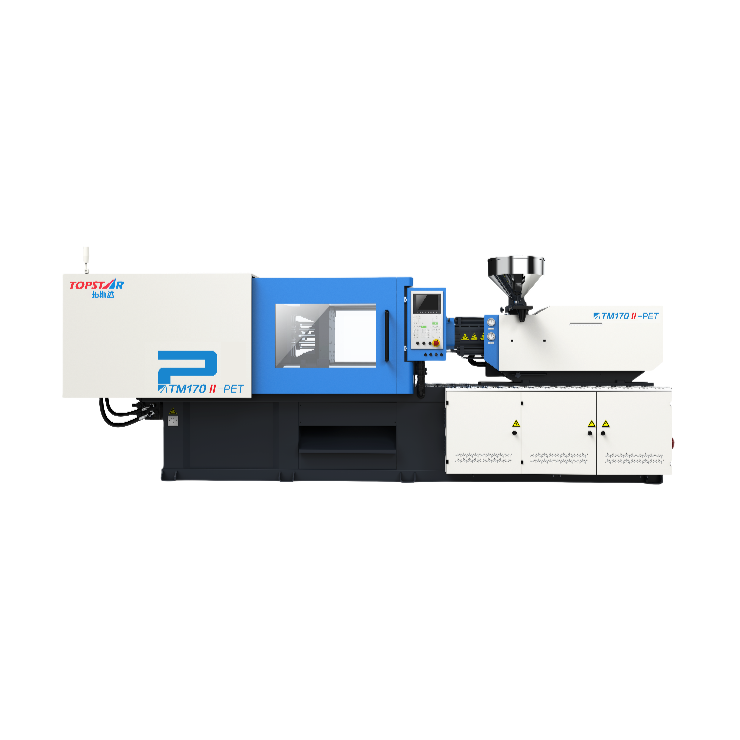
The plastic injection molding machine uses a dedicated screw to optimize PET material processing.
PET is a semi-crystalline material that requires precise control of its heating and cooling process to avoid problems such as uneven crystallization or bubbles. Topstar’s dedicated screw design improves the melting and mixing of PET materials, ensuring that the resin is evenly distributed and thoroughly heated. This produces a higher quality melt, essential for producing preforms with excellent transparency and strength. At the same time, the design of the screw optimizes the mixing zone to ensure the resin evenly distributes, allowing the PET material to mix and homogenize thoroughly before injection. Any inconsistency in the melt will cause changes in the mechanical properties of the final product, so this suitable mixing is essential. The high-quality melt produced by the dedicated screw can ensure that the preform molded parts have excellent optical properties and excellent structural integrity. This improves the durability of the final product.
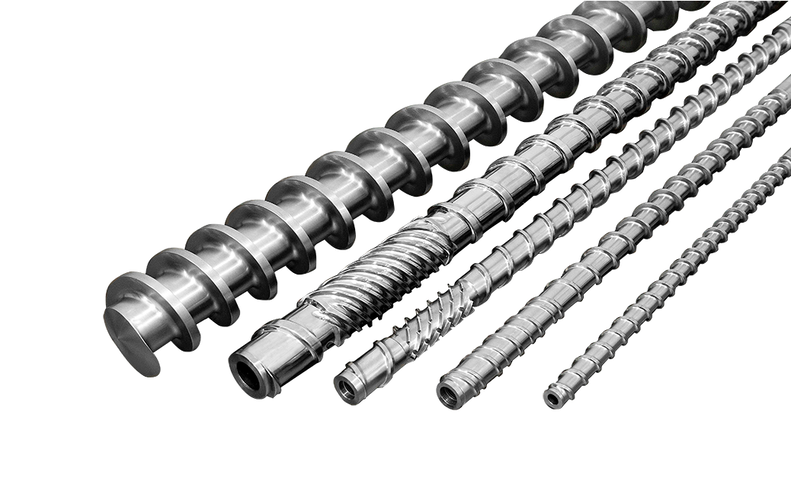
High-torque motors are used to increase the power system.
The high-torque motor used in the plastic injection molding machine specially built for PET increases the entire power system and improves the plasticization efficiency by more than 20%. Enable the system to melt and mix plastic resins faster and more efficiently. Unlike traditional motors, high-torque motors bring greater force and stability. This can shorten processing time and make it heat more evenly, ensuring that the plastic material reaches the required temperature and consistency in a shorter time. At the same time, it dramatically reduces defects such as bubbles and impurities that may occur during the molding process, ensuring the permeability and yield of the molded preforms. High-torque motors ensure more thorough and consistent plasticization, minimizing the risk of trapped air and contamination.
Improve production efficiency and save costs
The PET-specific plastic injection molding machine adopts the integrated injection molding process design concept. It is based on a self-developed control system and can support the host linkage robot signal. The host can adjust the key process parameters, such as the pressure and temperature of the peripheral auxiliary machines, to improve production efficiency. It can ensure that all injection molding equipment works in coordination to achieve the best production conditions. This integration can minimize downtime, reduce variability, and improve the overall efficiency of the production line.
The machine features an infrared heating coil that improves heat energy conversion efficiency and reduces energy consumption during production. Calculations show that the infrared heating coil saves energy by about 20%. Using infrared technology, the heating coil can directly heat the PET material more effectively than traditional methods, ensuring faster and more uniform heating of the entire molding area.
Open up blow molding automation
After the injection molding process is completed, the preform will enter the following key process: molding to form the final product. Based on software control capabilities, Topstar can open up the blow molding automation of the back end of injection molding. After the injection molding process shapes the PET raw materials, the conveyor belt smoothly carries the preforms into the blow molding process, optimizing manpower allocation and maximizing production efficiency. Such system design ensures the entire production line’s smooth and efficient production process.
By automating the transfer and handling steps between these two key stages, Topstar eliminates the need for manual handling and intervention. This speeds up the production process and ensures that each preform moves smoothly from one stage to the next without delays or bottlenecks. The automated system reduces human errors, improves precision, optimizes production throughput, and dramatically improves the overall efficiency of the production line.
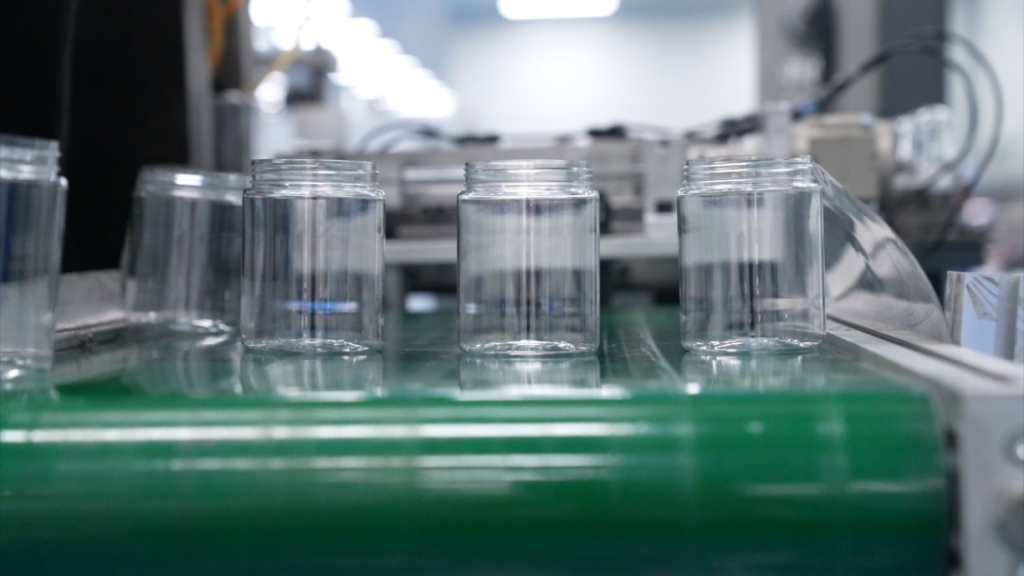
Optimizing PET material molding
Through a dedicated plastic injection molding machine combined with a dedicated screw, high-torque motor, and enhanced power system, the plasticization efficiency of PET materials can be optimized, defects can be reduced, and the permeability and yield of PET products can be improved. With faster cycle times, higher energy efficiency, and excellent processing capabilities, it provides a complete injection molding solution for companies seeking to optimize PET manufacturing processes.
TRENDING POSTS
- What factors can cause delays in the injection molding process of plastic molding machine? 2025/01/08
- Exhibition Review| Topstar participates in InterPlas Thailand 2024 2025/01/08
- Star Case | Topstar helps Santong upgrade its intelligent plant 2025/01/08
- Topstar Special | National Science and Technology Workers Day 2025/01/08
HOT TOPIC
- .ervo motor-driven linear robots
- 3 axis robot
- 3 axis robots
- 3 in 1 Compact Dehumidifying Dryer
- 3-axis robot
- 3-axis robots
- 5-axis CNC machine
- accuracy
- Air Chillers
- all electric injection molding machine
- all electric injection molding machines
- All-electric injection molding machines
- and overall production quality. Therefore
- AP-RubberPlas
- automated injection molding machine
- Automation changed engineering
- automation of injection molding robots
- auxiliary machine
- Bench Injection Molding Machine
- Cabinet dryer manufacturers
- Cabinet dryers
- chiller
- CNC Drilling Machine
- CNC Drilling Machines
- cnc engraving machine manufacturer
- cnc laser cutting machine manufacturer
- CNC machine
- CNC Machine Center
- CNC Machine for Sale
- CNC Machine Manufacturing
- CNC Machine Tool
- CNC machine tool product
- CNC Machining Center
- CNC wood carving machine
- Cooling system
- Cross-Walking Single Axis Servo Cylinder Robot
- Cross-Walking Single-Axis Servo Cylinder Robot
- Cross-Walking Three-Axis/Five-Axis Servo Driven Robot
- cross-walking three-axis/five-axis servo-driven robot
- Dehumidifier Dryer
- Dehumidifying Dryer
- delta parallel robot
- Desktop Injection Molding Machine
- Desktop injection molding machines
- Desktop Molding Machine
- desktop plastic injection machine
- Desktop Plastic Injection Molding Machine
- direct clamp injection molding machine
- Direct clamp injection molding machines
- Dosing & mixing system
- Drilling Centers
- Drying and dehumidification system
- drying and dehumidifying equipment
- Drying and Dehumidifying System
- drying system
- effective and efficient. Cabinet dryers are also used in other industries where large quantities of material need to be dried
- efficient injection molding machine
- elbow hydraulic injection molding machines
- electric injection molding machine
- electric injection molding machines
- energy-efficient injection molding robot
- energy-saving injection molding machine
- etc. Among injection molding robots
- exhibition
- features of CNC machine
- Feeding And Conveying System
- Five Axis Machine Center
- Fully automatic injection molding machine
- Gathering Topstar
- giant injection molding machine
- GMU-600 5-Axis Machining Center
- Granulating & Recycling System
- Heavy duty injection molding machine
- High-precision electric molding machines
- high-precision plastic molding machines
- high-speed all electric injection molding machine
- Honeycomb rotor dehumidifier
- horizontal injection molding machine
- Horizontal Injection Molding Machines
- Horizontal Injection Moulding Machine
- Horizontal Mixer manufacturer
- How The CNC Machine Works
- hybrid injection molding machine
- hydraulic injection molding machine
- Hydraulic Injection Molding Machines
- in this article
- Industrial robot
- Industrial Robot Chinese brand
- industrial robot parts
- industrial robot supplier
- Industrial robots
- Industry Chain
- Injection Manipulator
- injection manipulator robot
- injection mold machines
- Injection molding
- Injection molding automation
- Injection Molding Automation Solution
- injection molding dryer
- Injection molding equipment
- injection molding hopper dryer
- Injection molding machine
- injection molding machine brand
- Injection Molding Machine Factory
- Injection Molding Machine Manufacture
- Injection molding machine manufacturer
- injection molding machine manufacturers
- Injection molding machine procurement
- injection molding machine robotic arm
- injection molding machine with a robot
- Injection molding machines
- injection molding material dehumidifying
- injection molding plant
- Injection Molding Robot
- injection molding robot arm
- Injection molding robot automation
- Injection molding robotic arm
- injection molding robots
- Injection moulding machine
- Injection Moulding Robots
- Injection Robot
- Injection robot arm
- Injection robot manufacturer
- Injection robot wholesale
- injection robots
- intelligent injection molding machines
- Introducing Injection Robot
- It is the best choice for drying large quantities of material at once. Cabinetmakers use these machines because they are fast
- large injection molding machine
- large injection molding machines
- Learn what industrial automation and robotics is
- linear robot
- linear robots
- low speed sound-proof granulator
- machine plastic molding
- make sure to add some! Improvements (2) Keyphrase in introduction: Your keyphrase or its synonyms appear in the first paragraph of the copy
- manipulator machine
- manufacturing
- medical grade injection molding machines
- medical injection molding machine
- medical injection molding machines
- micro injection molding machine
- middle speed granulator
- Mini CNC machine manufacturers.
- Mold Temperature Control System
- mold temperature controller
- mold temperature controllers
- molding material Dehumidifying System
- mould temperature control system
- mould temperature controller
- mould temperature controllers
- New electric injection molding machine
- nitrogen dryer manufacturer
- nitrogen dryer system manufacturer
- Oil type mold temperature controller
- Oil type mold temperature controllers
- open day
- Outbound links: No outbound links appear in this page. Add some! Images: No images appear on this page. Add some! Internal links: No internal links appear in this page
- PET Preform injection molding
- phone case maker machine
- phone case making machine
- plastic bottle making machine
- plastic bottle manufacturing
- plastic bucket making machine
- plastic bucket manufacturing
- Plastic chair making machine
- plastic forming equipment
- plastic hopper dryer
- plastic injection machine
- plastic injection machines
- plastic injection molding
- Plastic injection molding equipment
- Plastic injection molding machine
- Plastic Injection Molding Machines
- plastic injection moulding machine
- plastic injection robot
- Plastic Molding machine
- Plastic Molding Machines
- plastic molding press
- plastic moulding machine
- plastic phone case making machine
- plastic-molding machine
- powerful granulator
- Powerful Type Sound-Proof Granulator
- precision injection molding
- precision injection molding machines
- production of plastic seats
- pure water mould temperature controller
- Robot injection molding
- robot injection molding machine
- robot manufacturing companies
- Robotic arm for injection molding machine
- robotic injection molding machines
- robotics in injection molding
- SCARA robot
- SCARA robots
- Service-oriented manufacturing
- Servo Cylinder Robot
- servo driven robot
- Servo Driven Robots
- servo injection robots
- servo motor-driven linear robots
- servo-driven 3-axis robot
- Servo-Driven Robot
- Setup of injection machine
- Silicone Injection Molding Machine
- six-axis industrial robot
- Stainless Hopper Dryer
- Stainless Hopper Dryers
- star club
- swing arm robot
- take-out robots
- the choice between servo-driven robots and hydraulic robots will have a certain impact on efficiency
- the most popular injection molding machine
- the type of injection molding robot
- toggle clamp injection molding machine
- Toggle Hydraulic Injection Molding Machines
- toggle injection molding machine
- Top 10 brands of injection robots
- Topstar
- Topstar Engineering
- Topstar Industrial Robots
- Topstar injection molding intelligent
- Topstar Scara Robots
- Useful Injection molding machine
- Vertical machining centers
- volumetric type blender
- water chiller
- water chillers
- water distributor
- water type mold temperature controller
- Water Type MoldTemperature Controller
- Water-Type Mould Temperature Controllers
- We often face choices when performing injection molding. We will choose the type of injection molding machine
- wholesale of injection molding machines
- x carve CNC