Plastic injection molding machine intelligent whole factory case
2024/10/08 By Topstar
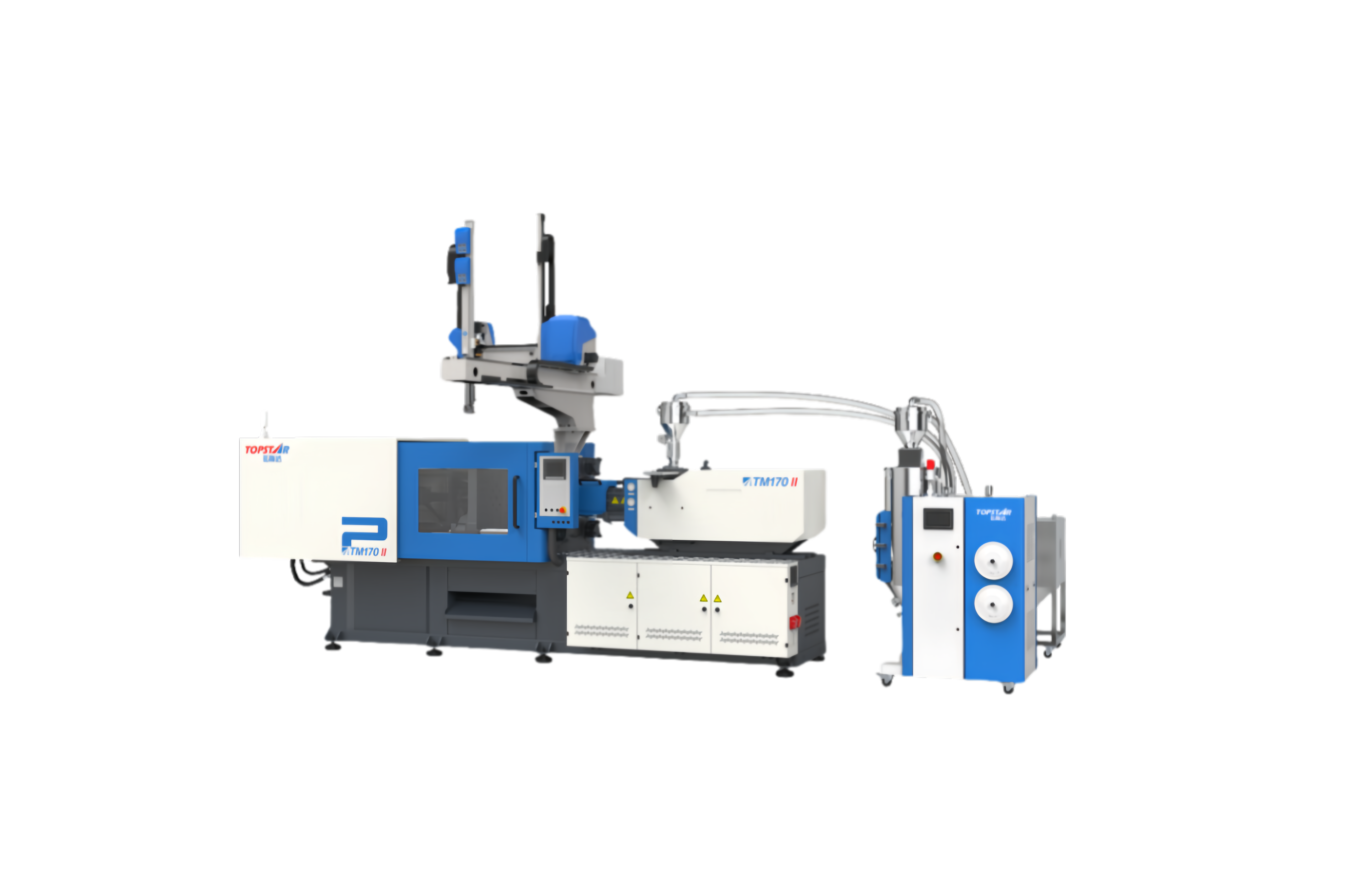
“We hope that the yield rate and aesthetics of the products will be professionally improved and enhanced, the cost of quality inspection will be reduced, and we hope to place more machines in a limited workshop.” Zhejiang DERXIN Connector Co., Ltd. (from now on referred to as DERXIN) is a professional company specializing in the production of various specifications of wire and cable connectors (cable connectors and their accessories). It is an experienced, comprehensive enterprise that integrates R&D and production.
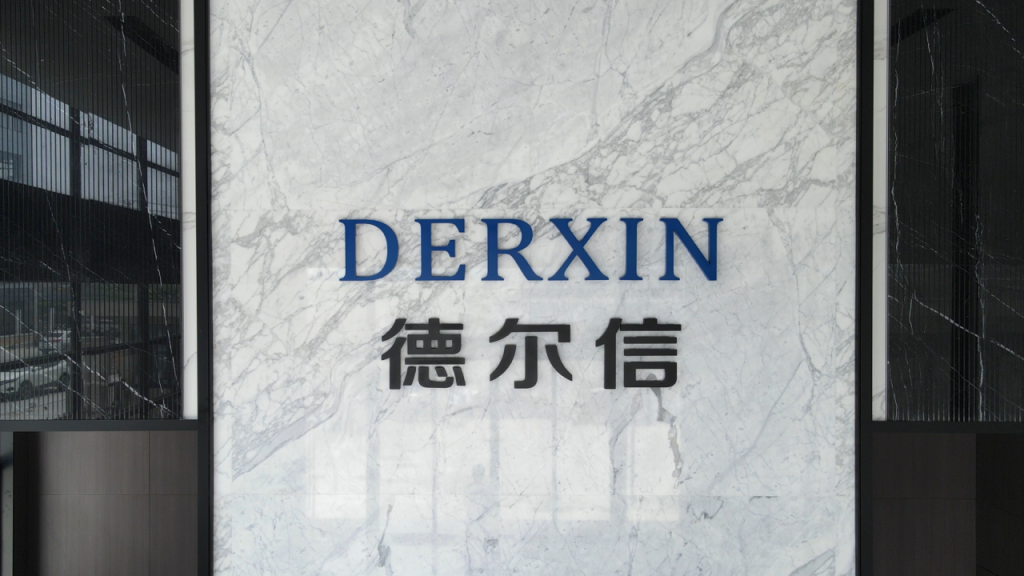
In the past five years, DERXIN’s sales have increased by 25%, and it has reached cooperation with many Fortune 500 companies. To further enhance product competitiveness and optimize the factory environment. DERXIN solves product precision and space problems by adopting Topstar’s intelligent whole-plant solution with injection molding machines as the core.
Plastic injection molding machine whole-plant planning
“We used to produce in an old factory building. The lack of standardization and professional design in the workshop layout resulted in low yield and affected appearance. The old equipment does not operate systematically, which easily causes after-sales service problems. Additionally, the workshop’s aesthetics and space utilization require improvement. This is what the head of DERXIN’s marketing department told us about the company’s problems during its expansion.
Injection molding whole plant solution
After a detailed survey of the old and new factories, Topstar equipped DERXIN with an intelligent energy management system, a central feeding management system, TM II injection molding machines and an MES digital management system based on the integration of the control system communication interface. These measures, from intelligent environment to digital management, have comprehensively improved the efficiency of DERXIN’s entire plant workshop, making it more efficient and tidy.
Therefore, through systematic and standardized design and transformation, the workshop space utilization rate has increased by nearly 30%, effectively solving the production environment problems caused by poor space management and chaotic raw material management.
-1024x551.webp)
Intelligent equipment such as plastic injection molding machines has increased the yield rate by about 25%
For the quality of products, Topstar not only requires the functionality of the products but also has strict requirements for the aesthetics of the product molding appearance. Production must guarantee the accuracy of the size and surface. According to the characteristics of raw materials, Topstar configures the TM II injection molding machine for DERXIN, and the main machine coordinates the peripheral injection molding robot, mold temperature controller and other auxiliary machines to dry the process parameters such as time, temperature and pressure. We thoroughly dry the raw materials before production to reduce defects such as bubbles, silver streaks, and splashes during the molding process.
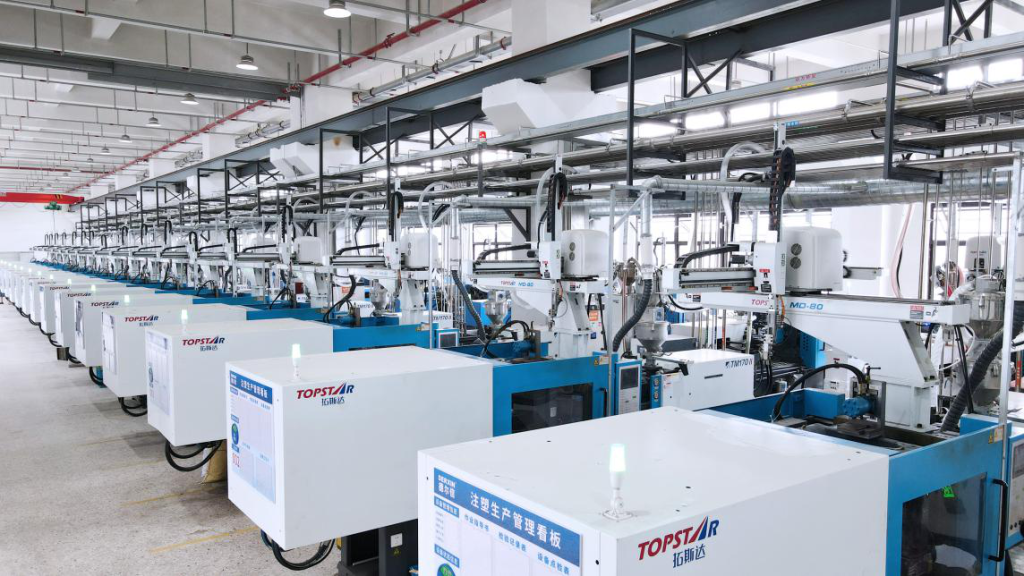
Topstar has equipped the machine with a new generation of plastic injection molding machine control solutions, which adopt a distributed control method and reasonably distribute the equipment according to the production process to achieve local control and monitoring. This can shorten the data transmission distance, thereby increasing the data transmission speed, making the communication speed fast and having strong anti-interference ability. Simple wiring can reduce line failure points and maintenance difficulty, reduce failure rate, and thus improve equipment utilization to increase production capacity.
Features of TM ll series injection molding machine
The TM ll series plastic injection molding machine, equipped with a Topstar injection molding robot, automatically compensates for the mold opening position. In the high-speed mold opening operation, it can realize accurate grasping and placement, and the production is more stable and efficient.
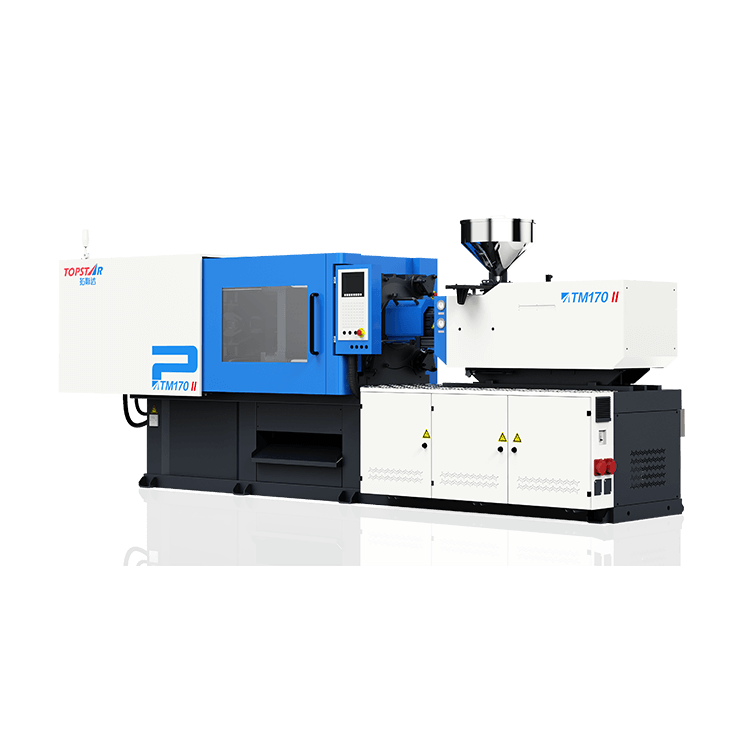
New oblique hinge layout: can realize ultra-long stroke mold opening, mold opening position accuracy <±1mm, and template movement is fast and stable.
The oil circuit system is fully upgraded: safe, stable, full-featured, differential clamping and fast operation speed.
New mold adjustment structure: Automatic and precise mold adjustment can be achieved with one click, thus reducing manual intervention.
The overall servo power is increased by 20%, the shooting speed is increased by 20%, the melt speed is increased by 10%, and the overall efficiency is increased by 15%.
Fourth-generation mold temperature controller
The fourth generation of mold temperature controllers is suitable for whole-plant solutions. The newly upgraded copper heater is not easy to scale. The copper material offers excellent ductility and thermal conductivity, increasing life by 40% and efficiency by 10% while allowing the mold temperature controller to function effectively even with poor water quality.
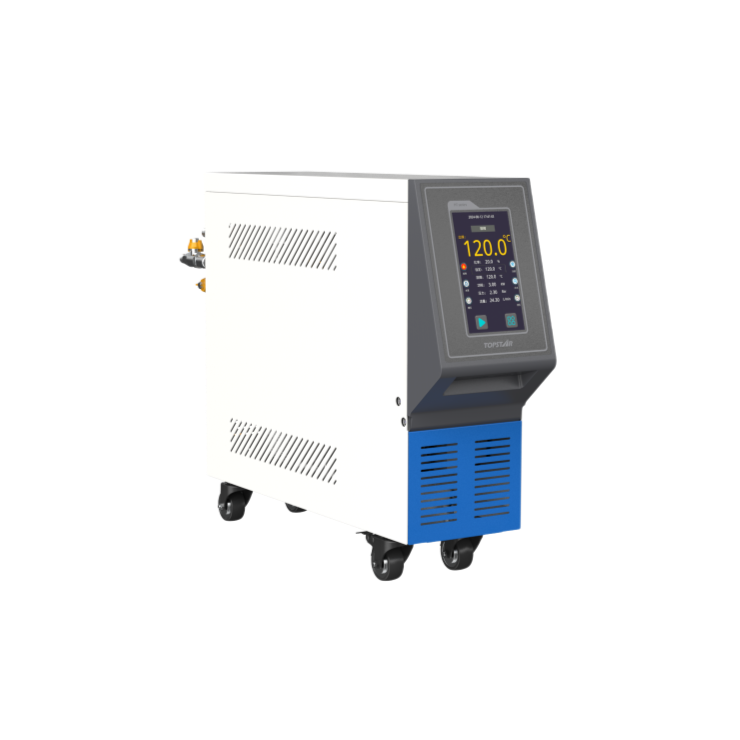
High-precision filter: The standard configuration is a 50-mesh high-precision filter, and the optional configuration is a 30μm filtration grade precision filter. In addition, the filter aperture is about 0.03mm, which can effectively filter impurities and prevent mold clogging.
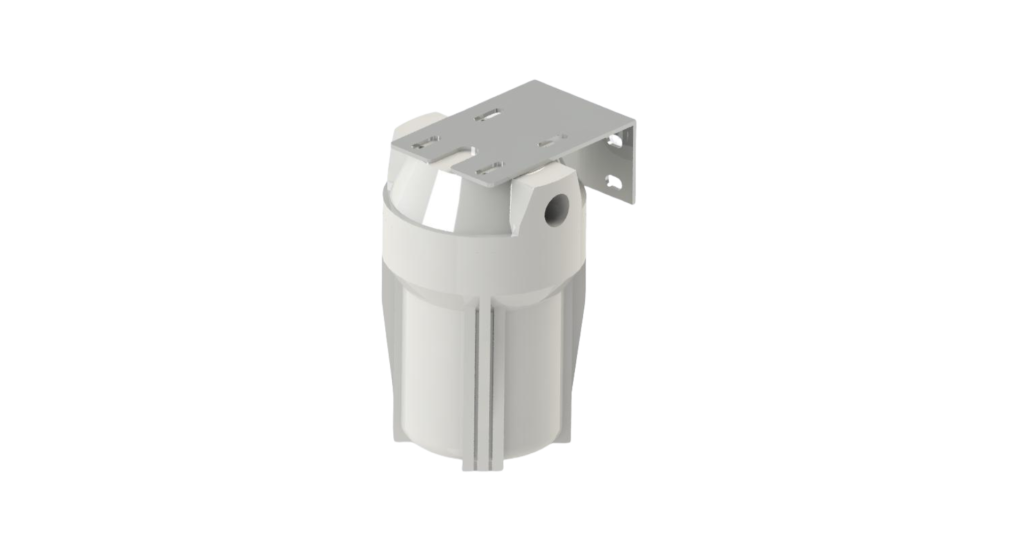
Liquid level detection function: Teflon float is suitable for pure water, has a float zero welding process, and has no welding leakage problem.
Water pressure adaptive temperature adjustment: The 120℃ standard mold temperature machine includes a pressure detector that achieves 1% detection accuracy, and you can adjust the upper limit of the usage temperature according to different water inlet pressures to ensure proper operation when the water inlet pressure is low.
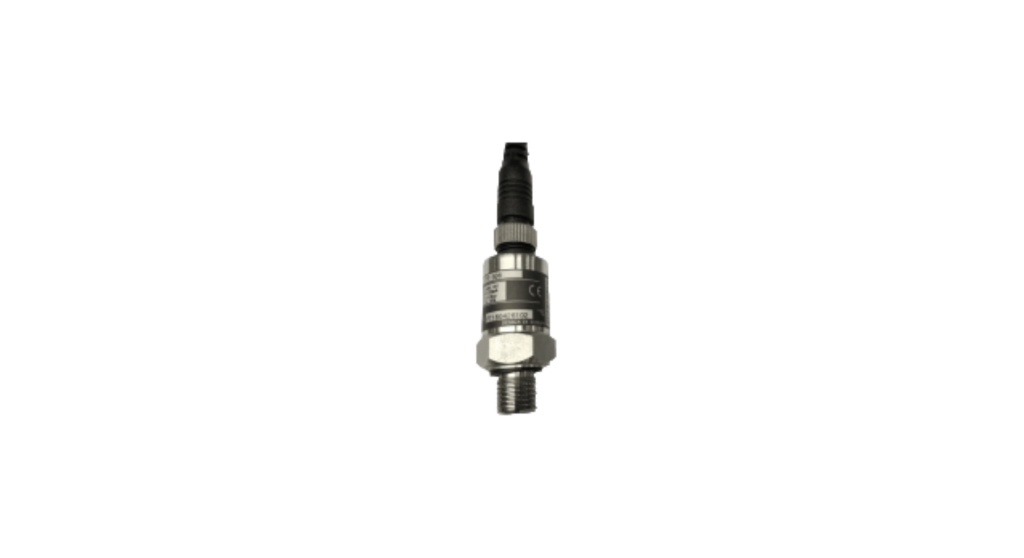
More accurate temperature control: The temperature control accuracy of the fourth-generation mold temperature controller reaches ±0.1℃. The latest PID temperature control algorithm improves the temperature control efficiency by 10%. At the same time, the hardware part adopts solid-state relay temperature control with a response time of 0.1s. The dual guarantee of software and hardware better ensures the product yield.
Make injection molding smarter and simpler.
“The new factory has been in operation for a month, and the yield rate has increased by about 25%, reducing the waste of raw material costs. The professionalism and tolerance of the products are in line with expectations, which will save a lot of energy for product quality inspection and subsequent sales.” ——-Feedback from DERXIN’s head
DERXIN plans to continuously increase its market share to 50% in the next five years. Topstar hopes to provide more companies with a series of more competitive solutions with its own experience and services in intelligent whole plants.
TRENDING POSTS
- What factors can cause delays in the injection molding process of plastic molding machine? 2024/10/08
- Exhibition Review| Topstar participates in InterPlas Thailand 2024 2024/10/08
- Star Case | Topstar helps Santong upgrade its intelligent plant 2024/10/08
- Topstar Special | National Science and Technology Workers Day 2024/10/08
HOT TOPIC
- .ervo motor-driven linear robots
- 3 axis robot
- 3 axis robots
- 3 in 1 Compact Dehumidifying Dryer
- 3-axis robot
- 3-axis robots
- 5-axis CNC machine
- accuracy
- Air Chillers
- all electric injection molding machine
- all electric injection molding machines
- All-electric injection molding machines
- and overall production quality. Therefore
- AP-RubberPlas
- automated injection molding machine
- Automation changed engineering
- automation of injection molding robots
- auxiliary machine
- Bench Injection Molding Machine
- Cabinet dryer manufacturers
- Cabinet dryers
- chiller
- CNC Drilling Machine
- CNC Drilling Machines
- cnc engraving machine manufacturer
- cnc laser cutting machine manufacturer
- CNC machine
- CNC Machine Center
- CNC Machine for Sale
- CNC Machine Manufacturing
- CNC Machine Tool
- CNC machine tool product
- CNC Machining Center
- CNC wood carving machine
- Cooling system
- Cross-Walking Single Axis Servo Cylinder Robot
- Cross-Walking Single-Axis Servo Cylinder Robot
- Cross-Walking Three-Axis/Five-Axis Servo Driven Robot
- cross-walking three-axis/five-axis servo-driven robot
- Dehumidifier Dryer
- Dehumidifying Dryer
- delta parallel robot
- Desktop Injection Molding Machine
- Desktop injection molding machines
- Desktop Molding Machine
- desktop plastic injection machine
- Desktop Plastic Injection Molding Machine
- direct clamp injection molding machine
- Direct clamp injection molding machines
- Dosing & mixing system
- Drilling Centers
- Drying and dehumidification system
- drying and dehumidifying equipment
- Drying and Dehumidifying System
- drying system
- effective and efficient. Cabinet dryers are also used in other industries where large quantities of material need to be dried
- efficient injection molding machine
- elbow hydraulic injection molding machines
- electric injection molding machine
- electric injection molding machines
- energy-efficient injection molding robot
- energy-saving injection molding machine
- etc. Among injection molding robots
- exhibition
- features of CNC machine
- Feeding And Conveying System
- Five Axis Machine Center
- Fully automatic injection molding machine
- Gathering Topstar
- giant injection molding machine
- GMU-600 5-Axis Machining Center
- Granulating & Recycling System
- Heavy duty injection molding machine
- High-precision electric molding machines
- high-precision plastic molding machines
- high-speed all electric injection molding machine
- Honeycomb rotor dehumidifier
- horizontal injection molding machine
- Horizontal Injection Molding Machines
- Horizontal Injection Moulding Machine
- Horizontal Mixer manufacturer
- How The CNC Machine Works
- hybrid injection molding machine
- hydraulic injection molding machine
- Hydraulic Injection Molding Machines
- in this article
- Industrial robot
- Industrial Robot Chinese brand
- industrial robot parts
- industrial robot supplier
- Industrial robots
- Industry Chain
- Injection Manipulator
- injection manipulator robot
- injection mold machines
- Injection molding
- Injection molding automation
- Injection Molding Automation Solution
- injection molding dryer
- Injection molding equipment
- injection molding hopper dryer
- Injection molding machine
- injection molding machine brand
- Injection Molding Machine Factory
- Injection Molding Machine Manufacture
- Injection molding machine manufacturer
- injection molding machine manufacturers
- Injection molding machine procurement
- injection molding machine robotic arm
- injection molding machine with a robot
- Injection molding machines
- injection molding material dehumidifying
- injection molding plant
- Injection Molding Robot
- injection molding robot arm
- Injection molding robot automation
- Injection molding robotic arm
- injection molding robots
- Injection moulding machine
- Injection Moulding Robots
- Injection Robot
- Injection robot arm
- Injection robot manufacturer
- Injection robot wholesale
- injection robots
- intelligent injection molding machines
- Introducing Injection Robot
- It is the best choice for drying large quantities of material at once. Cabinetmakers use these machines because they are fast
- large injection molding machine
- Learn what industrial automation and robotics is
- linear robot
- linear robots
- low speed sound-proof granulator
- machine plastic molding
- make sure to add some! Improvements (2) Keyphrase in introduction: Your keyphrase or its synonyms appear in the first paragraph of the copy
- manipulator machine
- manufacturing
- medical grade injection molding machines
- medical injection molding machine
- medical injection molding machines
- micro injection molding machine
- middle speed granulator
- Mini CNC machine manufacturers.
- Mold Temperature Control System
- mold temperature controller
- mold temperature controllers
- molding material Dehumidifying System
- mould temperature control system
- mould temperature controller
- mould temperature controllers
- New electric injection molding machine
- nitrogen dryer manufacturer
- nitrogen dryer system manufacturer
- Oil type mold temperature controller
- Oil type mold temperature controllers
- open day
- Outbound links: No outbound links appear in this page. Add some! Images: No images appear on this page. Add some! Internal links: No internal links appear in this page
- PET Preform injection molding
- phone case maker machine
- phone case making machine
- plastic bottle making machine
- plastic bottle manufacturing
- plastic bucket making machine
- plastic bucket manufacturing
- Plastic chair making machine
- plastic forming equipment
- plastic hopper dryer
- plastic injection machine
- plastic injection machines
- plastic injection molding
- Plastic injection molding equipment
- Plastic injection molding machine
- Plastic Injection Molding Machines
- plastic injection moulding machine
- plastic injection robot
- Plastic Molding machine
- Plastic Molding Machines
- plastic molding press
- plastic moulding machine
- plastic phone case making machine
- plastic-molding machine
- powerful granulator
- Powerful Type Sound-Proof Granulator
- precision injection molding
- precision injection molding machines
- production of plastic seats
- pure water mould temperature controller
- Robot injection molding
- robot injection molding machine
- robot manufacturing companies
- Robotic arm for injection molding machine
- robotic injection molding machines
- robotics in injection molding
- SCARA robot
- SCARA robots
- Service-oriented manufacturing
- Servo Cylinder Robot
- servo driven robot
- Servo Driven Robots
- servo injection robots
- servo motor-driven linear robots
- servo-driven 3-axis robot
- Servo-Driven Robot
- Setup of injection machine
- Silicone Injection Molding Machine
- six-axis industrial robot
- Stainless Hopper Dryer
- Stainless Hopper Dryers
- star club
- swing arm robot
- take-out robots
- the choice between servo-driven robots and hydraulic robots will have a certain impact on efficiency
- the most popular injection molding machine
- the type of injection molding robot
- toggle clamp injection molding machine
- Toggle Hydraulic Injection Molding Machines
- toggle injection molding machine
- Top 10 brands of injection robots
- Topstar
- Topstar Engineering
- Topstar Industrial Robots
- Topstar injection molding intelligent
- Topstar Scara Robots
- Useful Injection molding machine
- Vertical machining centers
- volumetric type blender
- water chiller
- water chillers
- water distributor
- water type mold temperature controller
- Water Type MoldTemperature Controller
- Water-Type Mould Temperature Controllers
- We often face choices when performing injection molding. We will choose the type of injection molding machine
- wholesale of injection molding machines
- x carve CNC