Plastic injection molding equipment suitable for high-end manufacturing industries
2024/12/25 By Topstar
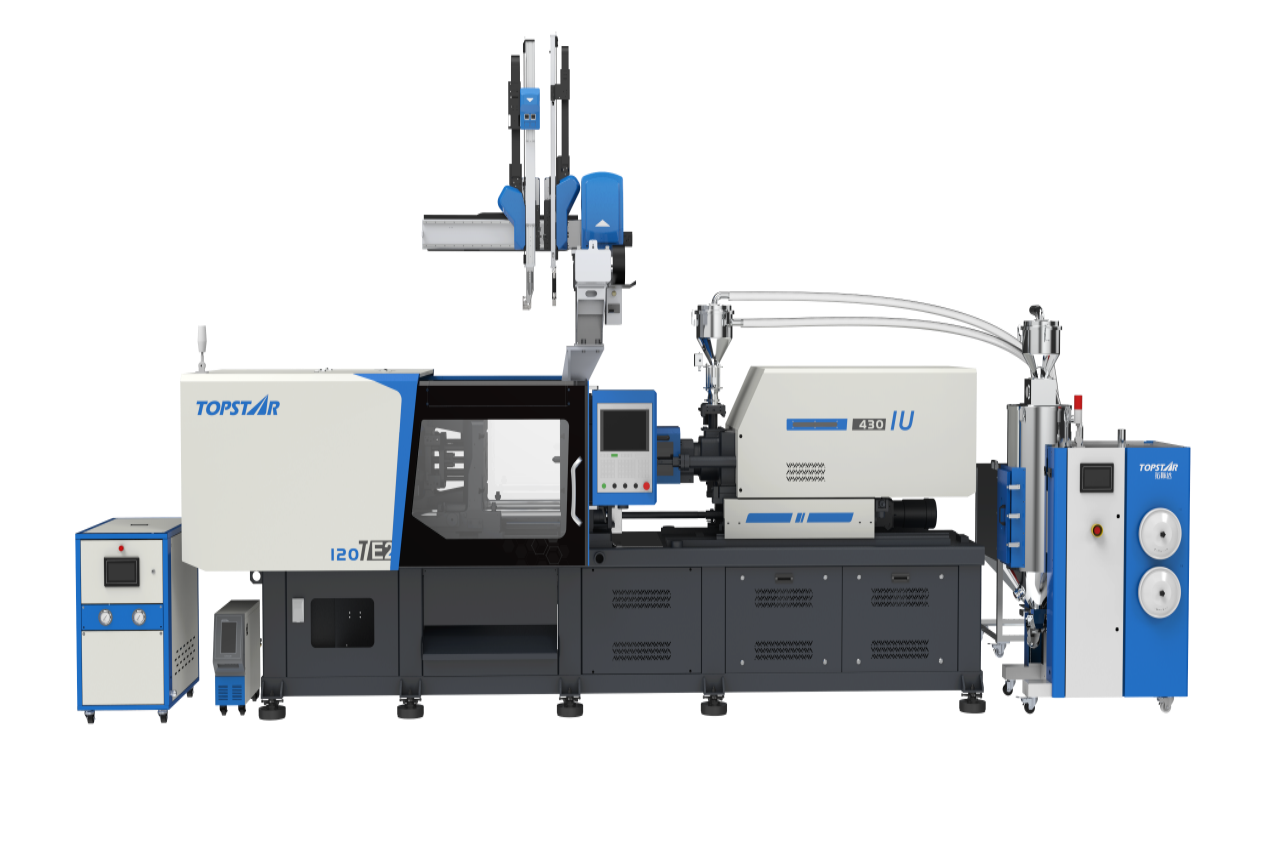
Plastic injection molding equipment has become essential in aerospace, electronics, electrical appliances, automobiles, etc. In these high-end manufacturing industries, the auxiliary equipment around the injection molding machine and the materials and production processes used must meet the most stringent standards and put forward higher requirements. Therefore, the plastic injection molding equipment created by Topstar can better play its value in the field of injection molding with its precise control and intelligent properties and help the high-end manufacturing industry gain market opportunities.
Plastic injection molding equipment: intelligent injection molding servo manipulator
One plastic injection molding equipment used in high-end manufacturing is the injection molding servo manipulator. The entire series of manipulators focuses on achieving customers’ needs for safety, intelligence, precision, and energy savings and has become a standard item for the injection molding factory to upgrade from automation to intelligence.
Topstar’s self-developed control system supports software upgrades and updates, injection molding machines to call manipulator signals, integrated linkage, and more precise control. At the same time, the manipulator incorporates a dual system, allowing customers to choose freely and program the required special actions. Combined with the fully self-developed five-in-one servo drive, it provides a robust algorithm for the injection molding robot. It makes it more precise, energy-saving, and intelligent, with strong functional scalability and flexibility, and can add back-end automation processes according to customer needs.
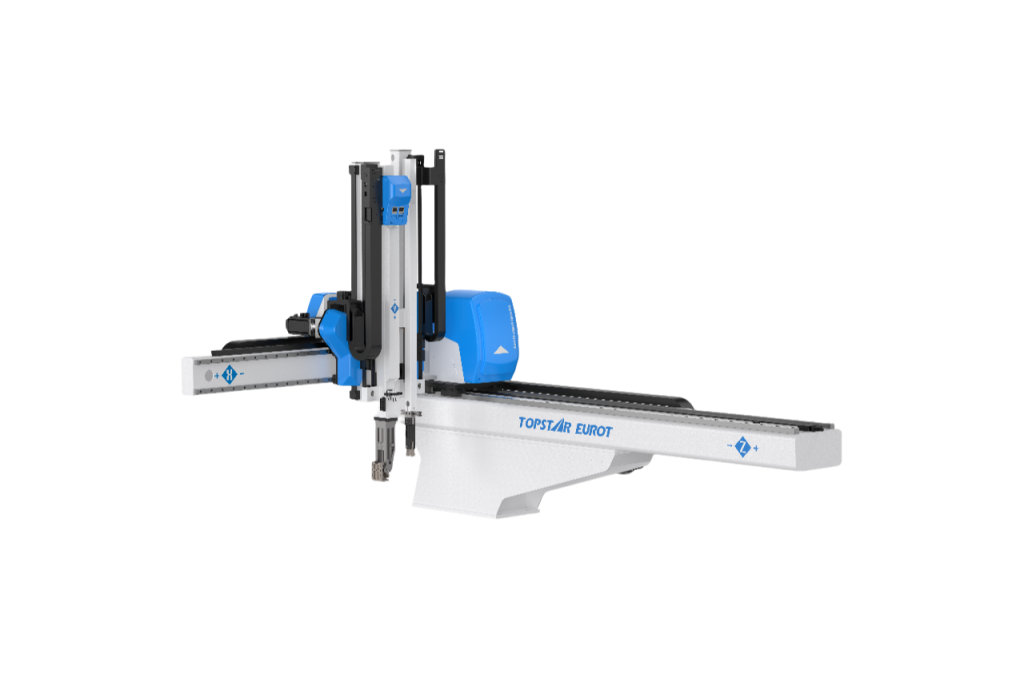
At the same time, the robot protection technology adopted can significantly improve the protection ability when facing a torque exceeding the set torque, effectively reduce the potential damage to the customer’s mold, injection molding machine ejector, and products, and further improve production efficiency and equipment stability.
Plastic injection molding equipment with precise control of mold temperature
In injection molding, maintaining precise temperature control throughout the process can obtain high-quality parts. Topstar’s mold temperature controller is divided into: water mould temperature controller (120℃~180℃), oil mould temperature controller (200℃~320℃), heating power is 8~36KW, water pump power is 1~5HP, and there are two series of single-stage temperature control and double-stage temperature control to choose from to meet the needs of different customers. Based on the temperature PID algorithm control, the temperature control accuracy can reach ±0.1℃, ensuring the uniformity of temperature, and it also has an over-temperature protection mechanism to better ensure the yield rate of plastic products.
The open communication interface can realize interconnection with other plastic injection molding equipment, improve the collaborative efficiency of the entire production process, and make the mold temperature system more intelligent. At the same time, automatically recording equipment operation status and alarm logs can improve fault response speed and maintenance efficiency and reduce downtime.
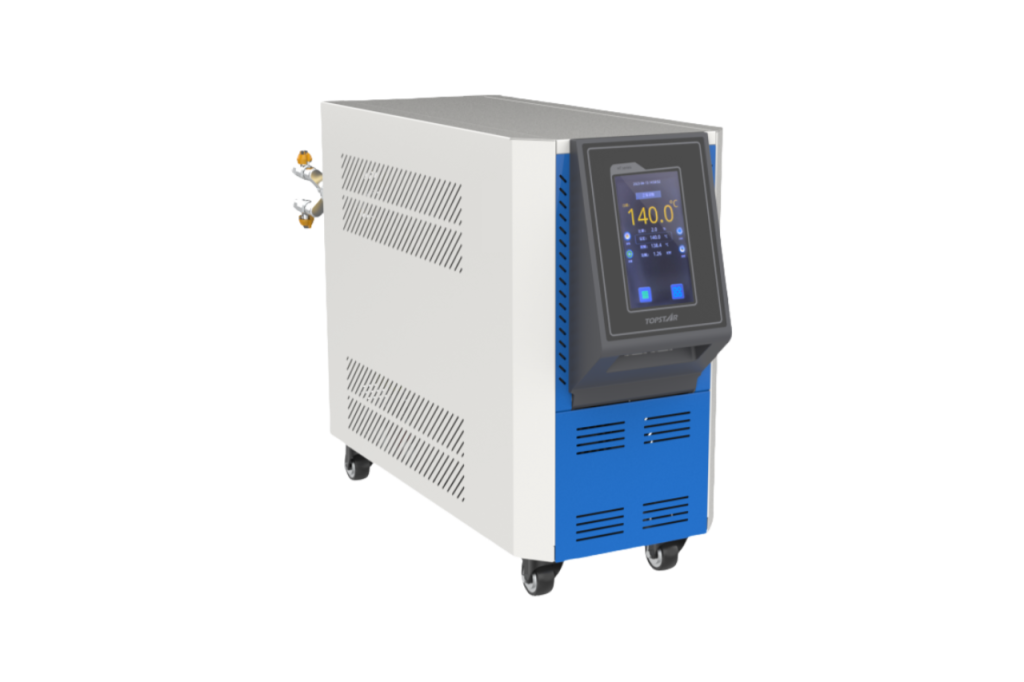
An injection molding chiller makes refrigeration more efficient
An injection molding chiller can quickly and effectively dissipate heat from the mold during injection molding and is used to maintain the required temperature range of the mold during the entire cooling stage of the injection molding cycle. Topstar’s refrigeration circuit design enables faster cooling, which allows the injection molding process to occur in a stable, low-temperature environment, improving product quality and production efficiency. The compressor and electrical components used ensure the stability and reliability of equipment operation. With the support of the self-developed control system, operators can link it with the injection molding machine, monitor the equipment status in real-time, and record the operation and alarm logs. It also supports the machine’s reservation one week in advance, which is more convenient for customers when managing production.
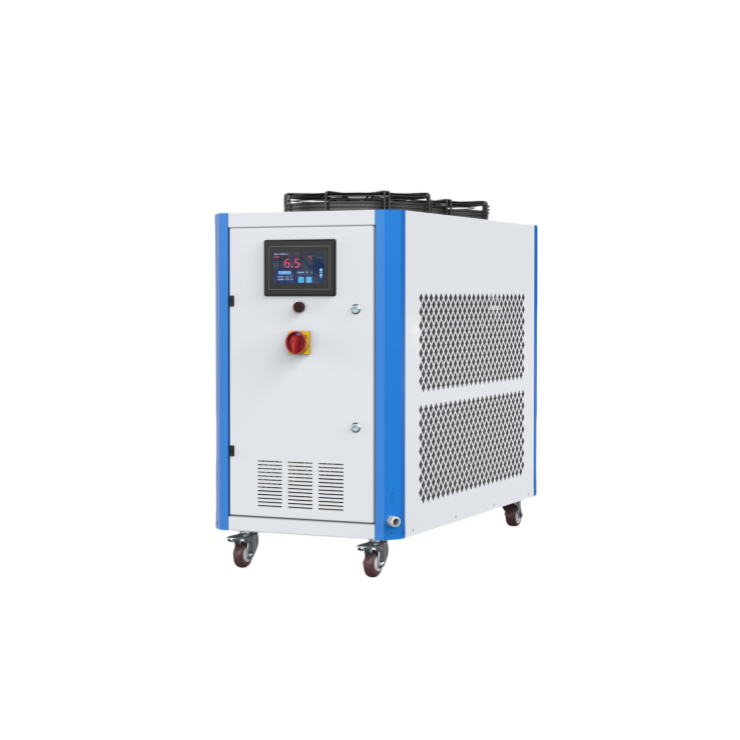
Three-in-one drying and dehumidification system
Among plastic injection molding equipment, the drying and dehumidification system provided by Topstar integrates three functions: drying, dehumidification, and transportation. It has a closed feeding circuit, which effectively prevents the dried raw materials from getting damp again due to contact with the outside air, improves the production line’s overall efficiency and management convenience, and ensures the consistency of the product. The heating and drying barrel modules adopt a double-layer insulation design to reduce energy consumption and prevent high-temperature burns.
The high-performance dehumidification system can continuously provide dry gas with a dew point of -40℃, which is particularly suitable for drying raw materials such as PA, PC, PBT, PET, and other engineering plastics with strong hygroscopicity. It can maintain the dryness and quality of the raw materials and improve the product yield. In addition, the equipment has safety functions such as over-temperature protection and motor overload to further ensure the safety of equipment operation.
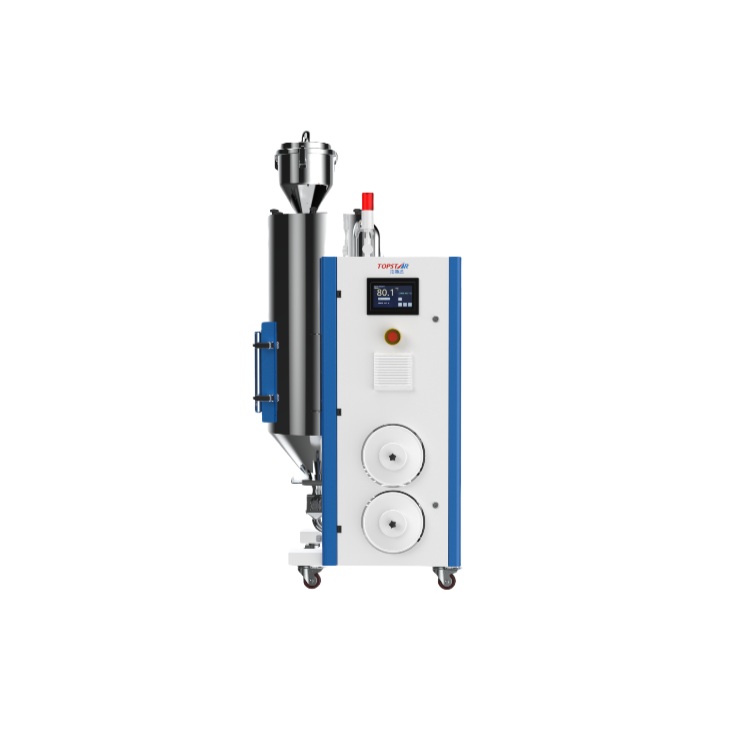
Self-developed injection molding machine: realize multi-device interconnection
The injection molding machine is the core of plastic injection molding equipment. Topstar has developed an “injection molding process integrated machine” on its self-developed control system. It has realized an integrated joint adjustment robot, mould temperature controller, three-in-one machine, and other equipment to achieve your process guarantee from raw materials to products. These machines can be optimized for specific applications, materials, and production environments, providing high flexibility and adaptability.
For high-end manufacturing industries such as medical devices, aerospace, and electronics, the ability of integrated intelligence ensures that complex parts with strict tolerances and high-performance requirements are produced with high efficiency and minimal waste. In addition, injection molding machines with “injection molding process integrated machine” can enable manufacturers to better control the entire production process, integrate cutting-edge intelligence, real-time monitoring systems, and data analysis, and maximize efficiency.
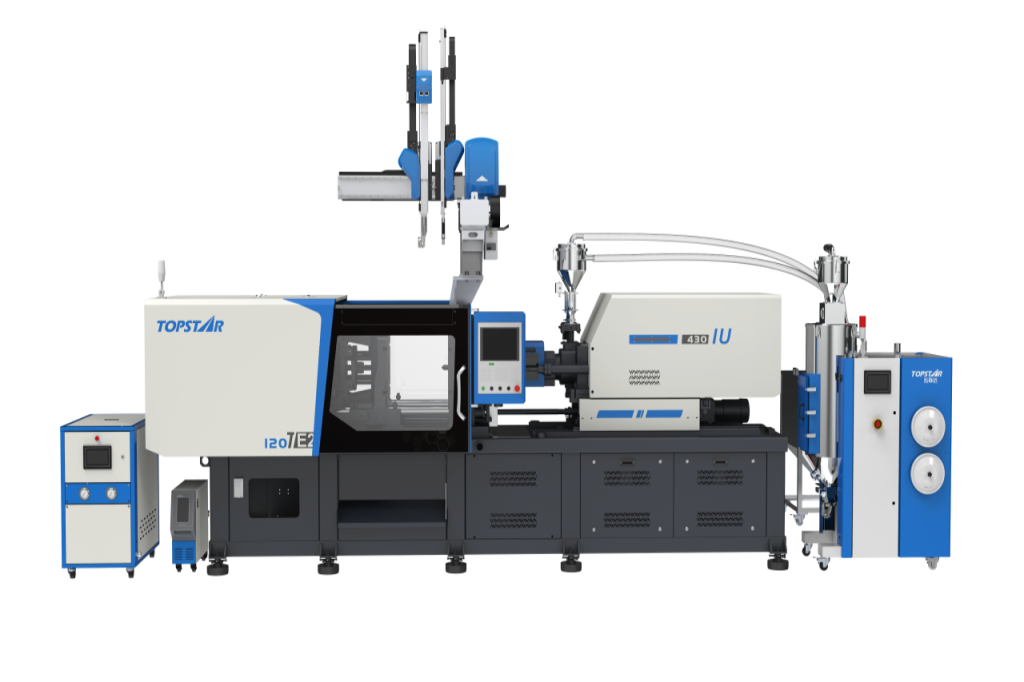
Achieve the manufacture of the best injection molded products
Plastic injection molding equipment such as servo manipulators, mold temperature controllers, chillers, three-in-one systems, and self-developed injection molding machines can help high-end manufacturing industries optimize production, improve injection molding efficiency, and improve part quality. Through the core concept of “injection molding process integrated machine”, customers can achieve process guarantees from raw materials to products, escort customers’ efficient and stable production, and simplify injection molding.
TRENDING POSTS
- What factors can cause delays in the injection molding process of plastic molding machine? 2024/12/25
- Exhibition Review| Topstar participates in InterPlas Thailand 2024 2024/12/25
- Star Case | Topstar helps Santong upgrade its intelligent plant 2024/12/25
- Topstar Special | National Science and Technology Workers Day 2024/12/25
HOT TOPIC
- 3 in 1 Compact Dehumidifying Dryer
- 5-axis CNC machine
- accuracy
- Air Chillers
- all electric injection molding machine
- All-electric injection molding machines
- and overall production quality. Therefore
- AP-RubberPlas
- automated injection molding machine
- Automation changed engineering
- automation of injection molding robots
- auxiliary machine
- Bench Injection Molding Machine
- Cabinet dryer manufacturers
- Cabinet dryers
- chiller
- CNC Drilling Machine
- CNC Drilling Machines
- cnc engraving machine manufacturer
- cnc laser cutting machine manufacturer
- CNC machine
- CNC Machine Center
- CNC Machine for Sale
- CNC Machine Manufacturing
- CNC Machine Tool
- CNC machine tool product
- CNC Machining Center
- CNC wood carving machine
- Cooling system
- Cross-Walking Single Axis Servo Cylinder Robot
- Cross-Walking Single-Axis Servo Cylinder Robot
- Cross-Walking Three-Axis/Five-Axis Servo Driven Robot
- cross-walking three-axis/five-axis servo-driven robot
- Dehumidifier Dryer
- Dehumidifying Dryer
- delta parallel robot
- Desktop Injection Molding Machine
- Desktop injection molding machines
- Desktop Molding Machine
- desktop plastic injection machine
- Desktop Plastic Injection Molding Machine
- direct clamp injection molding machine
- Direct clamp injection molding machines
- Dosing & mixing system
- Drilling Centers
- Drying and dehumidification system
- drying and dehumidifying equipment
- Drying and Dehumidifying System
- drying system
- effective and efficient. Cabinet dryers are also used in other industries where large quantities of material need to be dried
- efficient injection molding machine
- elbow hydraulic injection molding machines
- electric injection molding machine
- electric injection molding machines
- etc. Among injection molding robots
- exhibition
- features of CNC machine
- Feeding And Conveying System
- Five Axis Machine Center
- Fully automatic injection molding machine
- Gathering Topstar
- giant injection molding machine
- GMU-600 5-Axis Machining Center
- Granulating & Recycling System
- Heavy duty injection molding machine
- Honeycomb rotor dehumidifier
- horizontal injection molding machine
- Horizontal Injection Molding Machines
- Horizontal Injection Moulding Machine
- Horizontal Mixer manufacturer
- How The CNC Machine Works
- hybrid injection molding machine
- hydraulic injection molding machine
- Hydraulic Injection Molding Machines
- in this article
- Industrial robot
- Industrial Robot Chinese brand
- industrial robot parts
- industrial robot supplier
- Industrial robots
- Industry Chain
- Injection Manipulator
- injection mold machines
- Injection molding
- Injection molding automation
- Injection Molding Automation Solution
- injection molding dryer
- Injection molding equipment
- injection molding hopper dryer
- Injection molding machine
- injection molding machine brand
- Injection Molding Machine Factory
- Injection Molding Machine Manufacture
- Injection molding machine manufacturer
- injection molding machine manufacturers
- Injection molding machine procurement
- injection molding machine robotic arm
- injection molding machine with a robot
- Injection molding machines
- injection molding material dehumidifying
- injection molding plant
- Injection Molding Robot
- injection molding robot arm
- Injection molding robot automation
- Injection molding robotic arm
- injection molding robots
- Injection Moulding Robots
- Injection Robot
- Injection robot arm
- Injection robot manufacturer
- Injection robot wholesale
- injection robots
- intelligent injection molding machines
- Introducing Injection Robot
- It is the best choice for drying large quantities of material at once. Cabinetmakers use these machines because they are fast
- large injection molding machine
- Learn what industrial automation and robotics is
- low speed sound-proof granulator
- machine plastic molding
- make sure to add some! Improvements (2) Keyphrase in introduction: Your keyphrase or its synonyms appear in the first paragraph of the copy
- manipulator machine
- manufacturing
- micro injection molding machine
- middle speed granulator
- Mini CNC machine manufacturers.
- Mold Temperature Control System
- mold temperature controller
- molding material Dehumidifying System
- mould temperature controller
- mould temperature controllers
- New electric injection molding machine
- nitrogen dryer manufacturer
- nitrogen dryer system manufacturer
- Oil type mold temperature controller
- open day
- Outbound links: No outbound links appear in this page. Add some! Images: No images appear on this page. Add some! Internal links: No internal links appear in this page
- PET Preform injection molding
- phone case maker machine
- phone case making machine
- plastic bottle making machine
- plastic bottle manufacturing
- plastic bucket making machine
- plastic bucket manufacturing
- Plastic chair making machine
- plastic forming equipment
- plastic hopper dryer
- plastic injection machine
- plastic injection machines
- plastic injection molding
- Plastic injection molding equipment
- Plastic injection molding machine
- Plastic Injection Molding Machines
- plastic injection robot
- Plastic Molding machine
- Plastic Molding Machines
- plastic molding press
- plastic phone case making machine
- plastic-molding machine
- powerful granulator
- Powerful Type Sound-Proof Granulator
- production of plastic seats
- Robot injection molding
- robot injection molding machine
- robot manufacturing companies
- Robotic arm for injection molding machine
- robotic injection molding machines
- robotics in injection molding
- SCARA robot
- SCARA robots
- Service-oriented manufacturing
- Servo Cylinder Robot
- servo driven robot
- Servo Driven Robots
- servo injection robots
- Servo-Driven Robot
- Setup of injection machine
- Silicone Injection Molding Machine
- six-axis industrial robot
- Stainless Hopper Dryer
- Stainless Hopper Dryers
- star club
- swing arm robot
- the choice between servo-driven robots and hydraulic robots will have a certain impact on efficiency
- the most popular injection molding machine
- the type of injection molding robot
- toggle clamp injection molding machine
- Toggle Hydraulic Injection Molding Machines
- toggle injection molding machine
- Top 10 brands of injection robots
- Topstar
- Topstar Engineering
- Topstar Industrial Robots
- Topstar injection molding intelligent
- Topstar Scara Robots
- Useful Injection molding machine
- Vertical machining centers
- volumetric type blender
- water chiller
- water chillers
- water distributor
- Water Type MoldTemperature Controller
- We often face choices when performing injection molding. We will choose the type of injection molding machine
- wholesale of injection molding machines
- x carve CNC