Mould temperature controller with mould load adaptation
2024/12/18 By Topstar
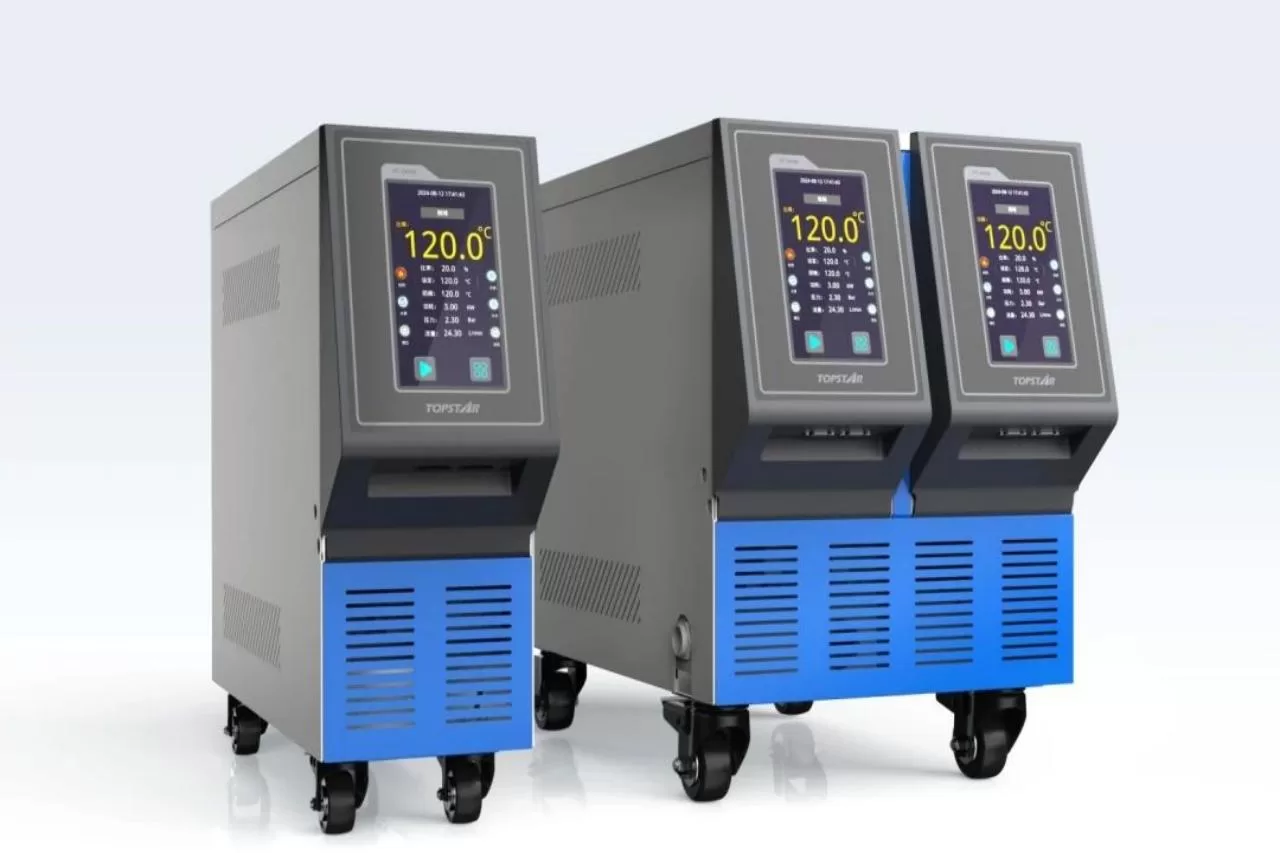
The mould temperature controller is a core product among the auxiliary equipment around the injection molding machine. Its temperature control accuracy will directly affect the quality of the injection moulded product. Especially in industrial automation control, there is a common problem when performing temperature control: a time delay in the system response, which leads to difficulties in the control process. To better solve this problem and ensure the accuracy and stability of temperature control, Topstar proposed the method of “mold load adaptive temperature intelligent control” to upgrade the traditional PID control algorithm of the mould temperature controller so that the equipment can automatically adapt to load changes and make intelligent adjustments like unmanned driving.
Market size and technical challenges of mould temperature controller
According to the “In-depth Research and Future Trend Analysis Report on the Development of Global and Chinese Injection Molding Machine Auxiliary Equipment Industry from 2023 to 2029”, the global mould temperature controller sales reached US$520 million in 2023, accounting for 32% of the auxiliary equipment market.
Although the market size of mould temperature controllers accounts for one-third of the auxiliary machine market, there are still technical challenges. Through in-depth research on the actual application scenarios of 15,000 customers, Topstar found that although the control technology of the mould temperature controller had reached the “semi-automation” stage after several iterations, external load changes, such as mould size adjustments or seasonal temperature shifts, could cause the temperature control accuracy to decline if users did not adjust the parameters in time. Product quality will be difficult to guarantee. In addition, traditional PID controllers rely heavily on setting control parameters and require skilled operators to make professional adjustments.
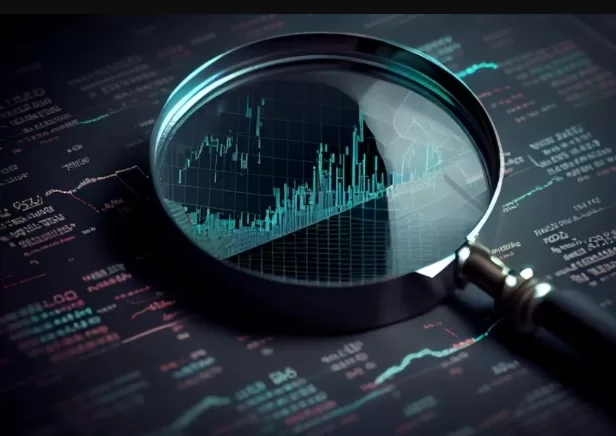
What is the PID algorithm in the mould temperature controller?
PID is a proportional (P), integral (I), and differential (D) control algorithm that can dynamically adjust the control input according to the difference between the expected output and the actual output of the system. By adjusting the three parameters in the PID controller, the system can reduce its hysteresis effect, enhance its stability, avoid strong oscillations, and improve control accuracy.
The upgraded PID control algorithm is the unmanned driving system of the car:
“P” is adjusted according to the current error size to help the system approach the target value faster. “I” is adjusted according to the accumulation of past errors to eliminate the deviation accumulated by the system. “D” is adjusted according to the rate of change of the error to improve the system’s stability and prevent system oscillation.
New temperature control solution
“Speed and accuracy” are two key indicators to measure the quality of the mould temperature controller. Adjusting the three parameters P, I, and D in the PID control algorithm is the key to achieving these indicators. We hope the equipment can automatically operate in the customer’s factory with just one button. Therefore, Topstar uses evaluation functions and mathematical models to adjust the parameters of the control algorithm in real-time based on traditional PID control.
After adopting the “mould load adaptive temperature intelligent control” method, the mould temperature controller increases the heating speed by 20% and reaches the target state quickly and stably. At the same time, it can also reduce preparation time and improve production efficiency. In addition, the temperature control accuracy reaches ±0.1℃, which reduces the fluctuation of mould temperature so that the mould temperature controller can meet the production needs of precision products such as aerospace, electronics, and new energy vehicles.
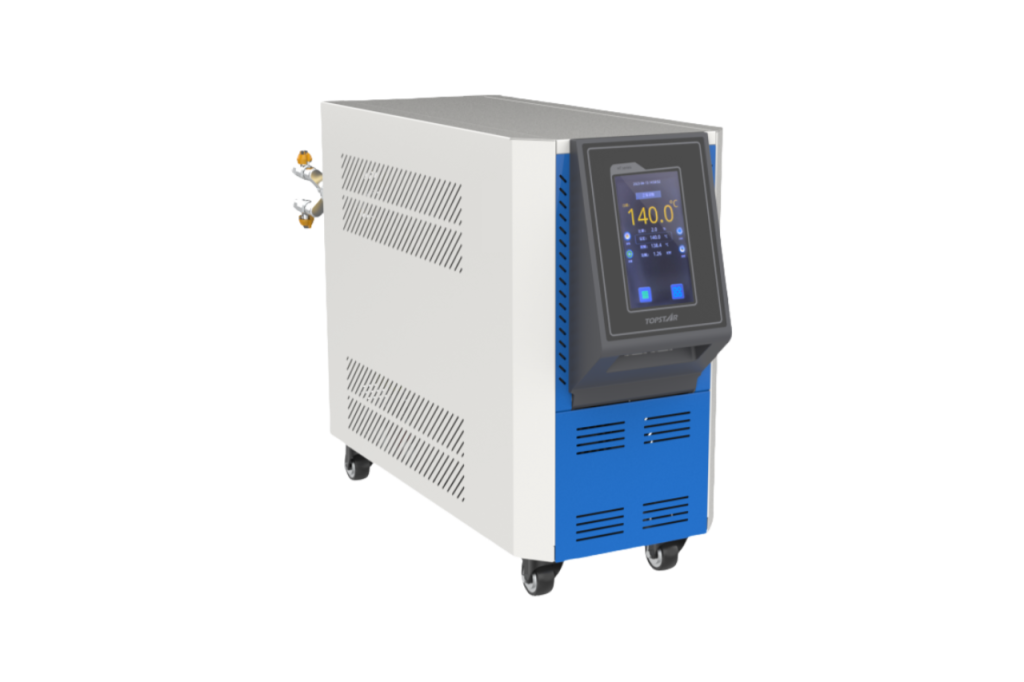
Trends in digitalization and intelligence
At the digital level, the injection molding machine interconnects with the mould temperature controller, supports host call signals, and achieves seamless connection with the Internet through the digital MES system. Customers can access the equipment data in real-time on their computers, tablets, mobile phones, and other terminals, making management more convenient. In addition, future advancements in artificial intelligence technology will plan and implement equipment health assessments and predictions, allowing users to detect potential equipment problems in advance through cloud models. At the same time, customers can be notified to carry out planned equipment maintenance and maintenance, reduce the risk of unexpected equipment downtime, and ensure the continuity and efficiency of the production process.
Meet the needs of the market application end.
Every technology upgrade is to implement customer production better and solve problems in customers’ actual applications. By adopting the mould temperature controller with “mold load adaptive temperature intelligent control,” the system reduces the fluctuation of mould temperature and improves stability to meet the production needs of precision products.
TRENDING POSTS
- What factors can cause delays in the injection molding process of plastic molding machine? 2024/12/18
- Exhibition Review| Topstar participates in InterPlas Thailand 2024 2024/12/18
- Star Case | Topstar helps Santong upgrade its intelligent plant 2024/12/18
- Topstar Special | National Science and Technology Workers Day 2024/12/18
HOT TOPIC
- .ervo motor-driven linear robots
- 1.0 guangdong topstar technology co. ltd
- 1.0 topstar china
- 1.0 topstar robot
- 11
- 2
- 21
- 23
- 3 axis robot
- 3 axis robots
- 3 in 1 Compact Dehumidifying Dryer
- 3-axis robot
- 3-axis robots
- 39
- 41
- 5-axis CNC machine
- 62
- accuracy
- Air Chillers
- all electric injection molding machine
- all electric injection molding machines
- All-electric injection molding machines
- and overall production quality. Therefore
- AP-RubberPlas
- automated injection molding machine
- Automation changed engineering
- automation of injection molding robots
- auxiliary machine
- Bench Injection Molding Machine
- Cabinet dryer manufacturers
- Cabinet dryers
- chiller
- CNC Drilling Machine
- CNC Drilling Machines
- cnc engraving machine manufacturer
- cnc laser cutting machine manufacturer
- CNC machine
- CNC Machine Center
- CNC Machine for Sale
- CNC Machine Manufacturing
- CNC Machine Tool
- CNC machine tool product
- CNC Machining Center
- CNC wood carving machine
- Cooling system
- Cross-Walking Single Axis Servo Cylinder Robot
- Cross-Walking Single-Axis Servo Cylinder Robot
- Cross-Walking Three-Axis/Five-Axis Servo Driven Robot
- cross-walking three-axis/five-axis servo-driven robot
- Dehumidifier Dryer
- Dehumidifying Dryer
- delta parallel robot
- Desktop Injection Molding Machine
- Desktop injection molding machines
- Desktop Molding Machine
- desktop plastic injection machine
- Desktop Plastic Injection Molding Machine
- direct clamp injection molding machine
- Direct clamp injection molding machines
- Dosing & mixing system
- Drilling Centers
- Drying and dehumidification system
- drying and dehumidifying equipment
- Drying and Dehumidifying System
- drying system
- effective and efficient. Cabinet dryers are also used in other industries where large quantities of material need to be dried
- efficient injection molding machine
- elbow hydraulic injection molding machines
- electric injection molding machine
- electric injection molding machines
- energy-efficient injection molding robot
- energy-saving injection molding machine
- etc. Among injection molding robots
- exhibition
- features of CNC machine
- Feeding And Conveying System
- Five Axis Machine Center
- Fully automatic injection molding machine
- Gathering Topstar
- giant injection molding machine
- GMU-600 5-Axis Machining Center
- Granulating & Recycling System
- Heavy duty injection molding machine
- High-precision electric molding machines
- high-precision plastic molding machines
- high-speed all electric injection molding machine
- Honeycomb rotor dehumidifier
- horizontal injection molding machine
- Horizontal Injection Molding Machines
- Horizontal Injection Moulding Machine
- Horizontal Mixer manufacturer
- How The CNC Machine Works
- hybrid injection molding machine
- hydraulic injection molding machine
- Hydraulic Injection Molding Machines
- in this article
- Industrial robot
- Industrial Robot Chinese brand
- industrial robot parts
- industrial robot supplier
- Industrial robots
- Industry Chain
- Injection Manipulator
- injection manipulator robot
- injection mold machines
- Injection molding
- Injection molding automation
- Injection Molding Automation Solution
- injection molding dryer
- Injection molding equipment
- injection molding hopper dryer
- Injection molding machine
- injection molding machine brand
- Injection Molding Machine Factory
- Injection Molding Machine Manufacture
- Injection molding machine manufacturer
- injection molding machine manufacturers
- Injection molding machine procurement
- injection molding machine robotic arm
- injection molding machine with a robot
- Injection molding machines
- injection molding material dehumidifying
- injection molding plant
- Injection Molding Robot
- injection molding robot arm
- Injection molding robot automation
- Injection molding robotic arm
- injection molding robots
- Injection moulding machine
- Injection Moulding Robots
- Injection Robot
- Injection robot arm
- Injection robot manufacturer
- Injection robot wholesale
- injection robots
- intelligent injection molding machines
- Introducing Injection Robot
- It is the best choice for drying large quantities of material at once. Cabinetmakers use these machines because they are fast
- large injection molding machine
- large injection molding machines
- Learn what industrial automation and robotics is
- linear robot
- linear robots
- low speed sound-proof granulator
- machine plastic molding
- make sure to add some! Improvements (2) Keyphrase in introduction: Your keyphrase or its synonyms appear in the first paragraph of the copy
- manipulator machine
- manufacturing
- medical grade injection molding machines
- medical injection molding machine
- medical injection molding machines
- micro injection molding machine
- middle speed granulator
- Mini CNC machine manufacturers.
- Mold Temperature Control System
- mold temperature controller
- mold temperature controllers
- molding material Dehumidifying System
- mould temperature control system
- mould temperature controller
- mould temperature controllers
- New electric injection molding machine
- nitrogen dryer manufacturer
- nitrogen dryer system manufacturer
- Oil type mold temperature controller
- Oil type mold temperature controllers
- open day
- Outbound links: No outbound links appear in this page. Add some! Images: No images appear on this page. Add some! Internal links: No internal links appear in this page
- PET Preform injection molding
- phone case maker machine
- phone case making machine
- plastic bottle making machine
- plastic bottle manufacturing
- plastic bucket making machine
- plastic bucket manufacturing
- Plastic chair making machine
- plastic forming equipment
- plastic hopper dryer
- plastic injection machine
- plastic injection machines
- plastic injection molding
- Plastic injection molding equipment
- Plastic injection molding machine
- Plastic Injection Molding Machines
- plastic injection moulding machine
- plastic injection robot
- Plastic Molding machine
- Plastic Molding Machines
- plastic molding press
- plastic moulding machine
- plastic phone case making machine
- plastic-molding machine
- powerful granulator
- Powerful Type Sound-Proof Granulator
- precision injection molding
- precision injection molding machines
- production of plastic seats
- pure water mould temperature controller
- Robot injection molding
- robot injection molding machine
- robot manufacturing companies
- Robotic arm for injection molding machine
- robotic injection molding machines
- robotics in injection molding
- SCARA robot
- SCARA robots
- Service-oriented manufacturing
- Servo Cylinder Robot
- servo driven robot
- Servo Driven Robots
- servo injection robots
- servo motor-driven linear robots
- servo-driven 3-axis robot
- Servo-Driven Robot
- Setup of injection machine
- Silicone Injection Molding Machine
- six-axis industrial robot
- Stainless Hopper Dryer
- Stainless Hopper Dryers
- star club
- swing arm robot
- take-out robots
- the choice between servo-driven robots and hydraulic robots will have a certain impact on efficiency
- the most popular injection molding machine
- the type of injection molding robot
- toggle clamp injection molding machine
- Toggle Hydraulic Injection Molding Machines
- toggle injection molding machine
- Top 10 brands of injection robots
- Topstar
- Topstar Engineering
- Topstar Industrial Robots
- Topstar injection molding intelligent
- Topstar Scara Robots
- Useful Injection molding machine
- Vertical machining centers
- volumetric type blender
- water chiller
- water chillers
- water distributor
- water type mold temperature controller
- Water Type MoldTemperature Controller
- Water-Type Mould Temperature Controllers
- We often face choices when performing injection molding. We will choose the type of injection molding machine
- wholesale of injection molding machines
- x carve CNC
- 热门查询 点击次数 展示 排名 topstar