Mold temperature control system leads a new era of mold control
2023/06/02 By Topstar
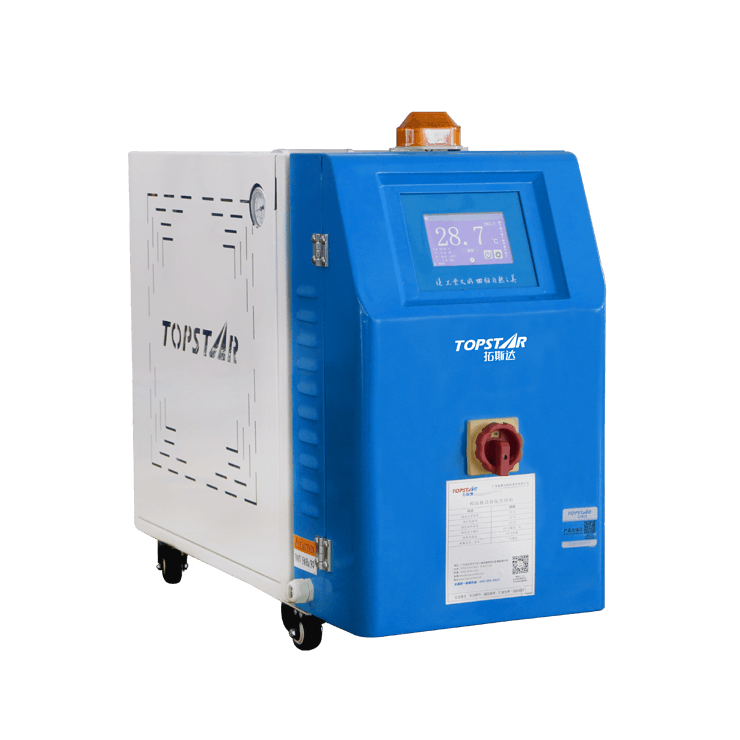
Mold temperature control system leads to a new era in mold control systems. The increase in technological advances and availability of various sensors has led to the development of many innovative approaches for managing temperature and humidity in buildings. These include climate control systems, now commonly used to maintain constant temperatures throughout a building or a room despite occupancy fluctuations due to work patterns or office hours. As such, these systems are becoming increasingly more sophisticated and versatile due to advances in technology and engineering practices.
It is an innovative solution for controlling mold temperature!
A mold temperature control system is an innovative solution for controlling the temperature of a mold. These systems suit various industries, including food manufacturing, pharmaceuticals, and cosmetics. The mold temperature control system prevents the decay from growing mold on the product during manufacturing. The mold temperature control system can also avoid mildew after manufacturing the product.
Many mold temperature control systems are available today, ranging from simple heating devices installed directly on existing machinery to complex computerized monitoring devices requiring specialized training. Offering professional installation services begins.
Mold temperature control systems can help you reduce downtime and increase productivity!
It is an essential part of any molding operation. Mold temperature control systems can help you reduce downtime and increase productivity.
A mold temperature control system can increase productivity, which means fewer parts are scrapped due to warping or cracking. They also prevent condensation from forming on mold surfaces, which can lead to poor part quality if left unchecked.
Good airflow in a factory should never be overlooked; if there isn’t enough air circulating your factory, heat energy will build up inside it, causing all sorts of problems, including increased wear-and-tear on machinery components and increased risk of fires breaking out!
Improve workflow, save money, and increase safety!
If you’re looking for a way to improve your workflow, save money, and improve worker safety, a new generation of mold control systems can help.
Mold temperature control systems have been around for some time, but they’ve never been able to offer the level of control over mold growth that is possible today. This is because there is always an inherent conflict between controlling temperature and humidity, and if you want to keep humidity low, you need more airflow, which means higher temperatures. If you try to lower the temperature, more moisture will remain in your stove.
How to prevent dangerous mold?
One of the primary functions of the MTCS is to regulate mold temperature during the molding cycle. Proper temperature control is critical to obtaining consistent and high-quality molded parts. Maintaining precise temperatures helps prevent issues such as warping, shrinkage, or uneven cooling that can compromise the integrity of the final product. Controlling mold temperature also prevents the formation of dangerous hot spots. Insufficient temperature regulation can lead to local overheating, causing thermal degradation of the plastic material and adversely affecting the life of the mold. Hot spots can lead to structural defects, cracks, or even catastrophic failure of the mold. For added safety, they often contain temperature sensors, heaters, and cooling elements to provide precise control. Automated systems can dynamically adjust temperature settings based on the specific requirements of the molding process, minimizing the risk of overheating or cooling.
Mold Temperature Control Systems are the future of mold control technology!
It is the future of mold control technology. Utilizing these new methods can improve process efficiency and reduce costs while reducing workers’ health and safety risks.
A more efficient mold temperature control system allows you to pinpoint the parts of your facility where heat buildup occurs, saving you the labor costs of installing additional units. Mold temperature control systems are safer for workers: Workers exposed to high temperatures often face serious health problems. A well-designed MTCS reduces these risks by keeping temperatures safe for extended periods. A mold temperature control system can help you save money: it helps eliminate unnecessary downtime and reduces repairs!
To sum up
As we can see, the future of mold control systems is here, not just for temperature control. With new developments in technology and materials, mold has become a problem that can be controlled in many ways. Whether using robotics or artificial intelligence to detect where mold might grow next or developing new materials that resist moisture better than ever, many ways to tackle this problem affect us all. Having such a machine in your workshop will undoubtedly greatly help your production. If you want to know more, please get in touch with us!
TRENDING POSTS
- What factors can cause delays in the injection molding process of plastic molding machine? 2023/06/02
- Exhibition Review| Topstar participates in InterPlas Thailand 2024 2023/06/02
- Star Case | Topstar helps Santong upgrade its intelligent plant 2023/06/02
- Topstar Special | National Science and Technology Workers Day 2023/06/02
HOT TOPIC
- .ervo motor-driven linear robots
- 3 axis robot
- 3 axis robots
- 3 in 1 Compact Dehumidifying Dryer
- 3-axis robot
- 3-axis robots
- 5-axis CNC machine
- accuracy
- Air Chillers
- all electric injection molding machine
- all electric injection molding machines
- All-electric injection molding machines
- and overall production quality. Therefore
- AP-RubberPlas
- automated injection molding machine
- Automation changed engineering
- automation of injection molding robots
- auxiliary machine
- Bench Injection Molding Machine
- Cabinet dryer manufacturers
- Cabinet dryers
- chiller
- CNC Drilling Machine
- CNC Drilling Machines
- cnc engraving machine manufacturer
- cnc laser cutting machine manufacturer
- CNC machine
- CNC Machine Center
- CNC Machine for Sale
- CNC Machine Manufacturing
- CNC Machine Tool
- CNC machine tool product
- CNC Machining Center
- CNC wood carving machine
- Cooling system
- Cross-Walking Single Axis Servo Cylinder Robot
- Cross-Walking Single-Axis Servo Cylinder Robot
- Cross-Walking Three-Axis/Five-Axis Servo Driven Robot
- cross-walking three-axis/five-axis servo-driven robot
- Dehumidifier Dryer
- Dehumidifying Dryer
- delta parallel robot
- Desktop Injection Molding Machine
- Desktop injection molding machines
- Desktop Molding Machine
- desktop plastic injection machine
- Desktop Plastic Injection Molding Machine
- direct clamp injection molding machine
- Direct clamp injection molding machines
- Dosing & mixing system
- Drilling Centers
- Drying and dehumidification system
- drying and dehumidifying equipment
- Drying and Dehumidifying System
- drying system
- effective and efficient. Cabinet dryers are also used in other industries where large quantities of material need to be dried
- efficient injection molding machine
- elbow hydraulic injection molding machines
- electric injection molding machine
- electric injection molding machines
- energy-efficient injection molding robot
- energy-saving injection molding machine
- etc. Among injection molding robots
- exhibition
- features of CNC machine
- Feeding And Conveying System
- Five Axis Machine Center
- Fully automatic injection molding machine
- Gathering Topstar
- giant injection molding machine
- GMU-600 5-Axis Machining Center
- Granulating & Recycling System
- Heavy duty injection molding machine
- High-precision electric molding machines
- high-precision plastic molding machines
- high-speed all electric injection molding machine
- Honeycomb rotor dehumidifier
- horizontal injection molding machine
- Horizontal Injection Molding Machines
- Horizontal Injection Moulding Machine
- Horizontal Mixer manufacturer
- How The CNC Machine Works
- hybrid injection molding machine
- hydraulic injection molding machine
- Hydraulic Injection Molding Machines
- in this article
- Industrial robot
- Industrial Robot Chinese brand
- industrial robot parts
- industrial robot supplier
- Industrial robots
- Industry Chain
- Injection Manipulator
- injection manipulator robot
- injection mold machines
- Injection molding
- Injection molding automation
- Injection Molding Automation Solution
- injection molding dryer
- Injection molding equipment
- injection molding hopper dryer
- Injection molding machine
- injection molding machine brand
- Injection Molding Machine Factory
- Injection Molding Machine Manufacture
- Injection molding machine manufacturer
- injection molding machine manufacturers
- Injection molding machine procurement
- injection molding machine robotic arm
- injection molding machine with a robot
- Injection molding machines
- injection molding material dehumidifying
- injection molding plant
- Injection Molding Robot
- injection molding robot arm
- Injection molding robot automation
- Injection molding robotic arm
- injection molding robots
- Injection moulding machine
- Injection Moulding Robots
- Injection Robot
- Injection robot arm
- Injection robot manufacturer
- Injection robot wholesale
- injection robots
- intelligent injection molding machines
- Introducing Injection Robot
- It is the best choice for drying large quantities of material at once. Cabinetmakers use these machines because they are fast
- large injection molding machine
- large injection molding machines
- Learn what industrial automation and robotics is
- linear robot
- linear robots
- low speed sound-proof granulator
- machine plastic molding
- make sure to add some! Improvements (2) Keyphrase in introduction: Your keyphrase or its synonyms appear in the first paragraph of the copy
- manipulator machine
- manufacturing
- medical grade injection molding machines
- medical injection molding machine
- medical injection molding machines
- micro injection molding machine
- middle speed granulator
- Mini CNC machine manufacturers.
- Mold Temperature Control System
- mold temperature controller
- mold temperature controllers
- molding material Dehumidifying System
- mould temperature control system
- mould temperature controller
- mould temperature controllers
- New electric injection molding machine
- nitrogen dryer manufacturer
- nitrogen dryer system manufacturer
- Oil type mold temperature controller
- Oil type mold temperature controllers
- open day
- Outbound links: No outbound links appear in this page. Add some! Images: No images appear on this page. Add some! Internal links: No internal links appear in this page
- PET Preform injection molding
- phone case maker machine
- phone case making machine
- plastic bottle making machine
- plastic bottle manufacturing
- plastic bucket making machine
- plastic bucket manufacturing
- Plastic chair making machine
- plastic forming equipment
- plastic hopper dryer
- plastic injection machine
- plastic injection machines
- plastic injection molding
- Plastic injection molding equipment
- Plastic injection molding machine
- Plastic Injection Molding Machines
- plastic injection moulding machine
- plastic injection robot
- Plastic Molding machine
- Plastic Molding Machines
- plastic molding press
- plastic moulding machine
- plastic phone case making machine
- plastic-molding machine
- powerful granulator
- Powerful Type Sound-Proof Granulator
- precision injection molding
- precision injection molding machines
- production of plastic seats
- pure water mould temperature controller
- Robot injection molding
- robot injection molding machine
- robot manufacturing companies
- Robotic arm for injection molding machine
- robotic injection molding machines
- robotics in injection molding
- SCARA robot
- SCARA robots
- Service-oriented manufacturing
- Servo Cylinder Robot
- servo driven robot
- Servo Driven Robots
- servo injection robots
- servo motor-driven linear robots
- servo-driven 3-axis robot
- Servo-Driven Robot
- Setup of injection machine
- Silicone Injection Molding Machine
- six-axis industrial robot
- Stainless Hopper Dryer
- Stainless Hopper Dryers
- star club
- swing arm robot
- take-out robots
- the choice between servo-driven robots and hydraulic robots will have a certain impact on efficiency
- the most popular injection molding machine
- the type of injection molding robot
- toggle clamp injection molding machine
- Toggle Hydraulic Injection Molding Machines
- toggle injection molding machine
- Top 10 brands of injection robots
- Topstar
- Topstar Engineering
- Topstar Industrial Robots
- Topstar injection molding intelligent
- Topstar Scara Robots
- Useful Injection molding machine
- Vertical machining centers
- volumetric type blender
- water chiller
- water chillers
- water distributor
- water type mold temperature controller
- Water Type MoldTemperature Controller
- Water-Type Mould Temperature Controllers
- We often face choices when performing injection molding. We will choose the type of injection molding machine
- wholesale of injection molding machines
- x carve CNC