The Ultimate Guide to Selecting a Plastic Molding Machine
2022/02/26 By Topstar
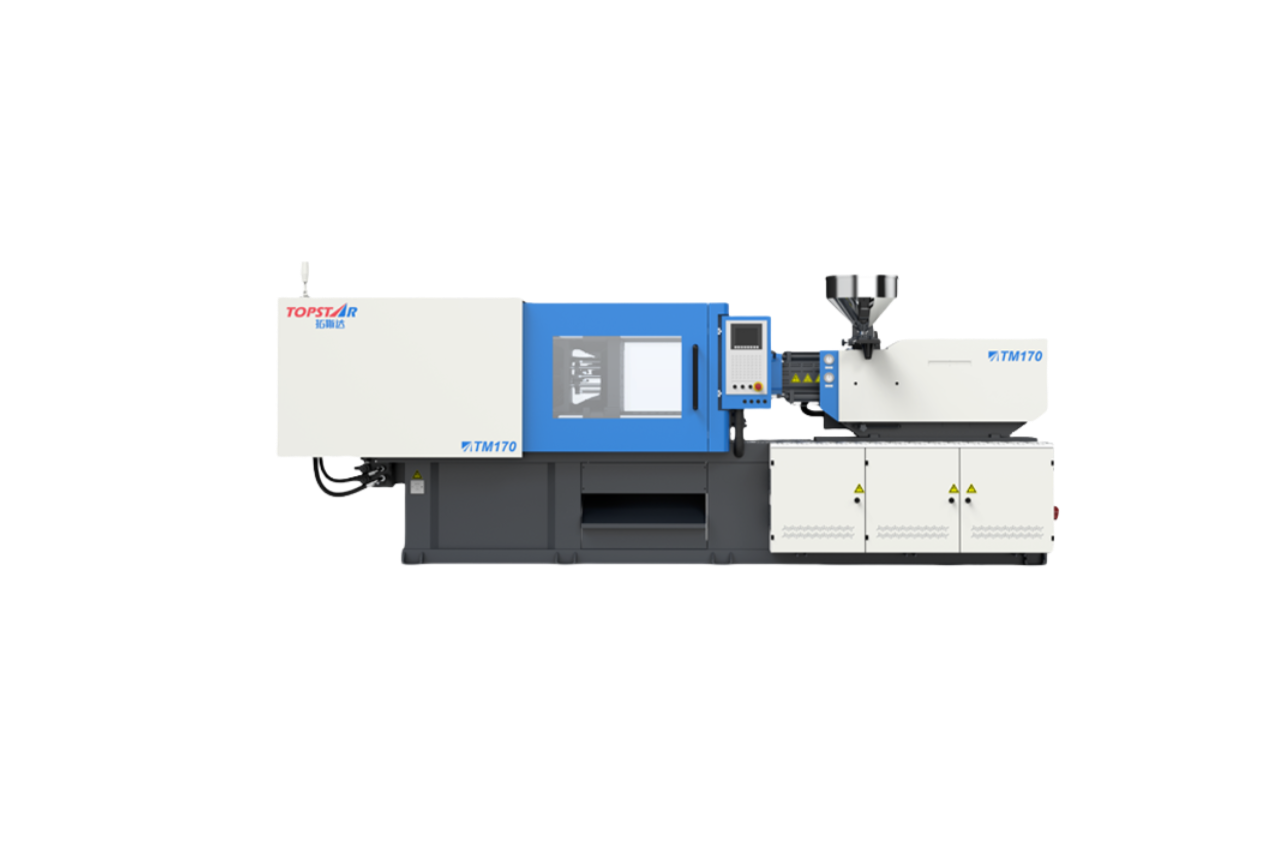
When manufacturing plastic products, choosing the right injection molding equipment can ensure production quality and greater efficiency. The plastic molding machine is one of the most essential pieces of equipment in this injection molding process. Whether you are producing small, high-precision parts or more significant, more robust products, choosing the right plastic molding machine can significantly impact your production speed, quality, and cost-effectiveness. In this ultimate guide, we will discuss the essential factors to consider when choosing your business and provide insights and professional advice.
Identify the type of plastic molding machine that is right for you.
The first step in choosing the ideal plastic molding machine is to understand the different types of machines available and which one is best suited to your production needs. There are three types of plastic molding machines, including:
Hydraulic plastic molding machines:
It uses a hydraulic system to drive the injection process, providing strong clamping force, ideal for molding large and heavy plastic parts. Hydraulic presses are particularly suitable for automotive, packaging, and heavy consumer goods industries, where strength and reliability are key factors. The main advantage of hydraulic molding machines is their ability to handle high tonnage and quickly produce large, complex parts.
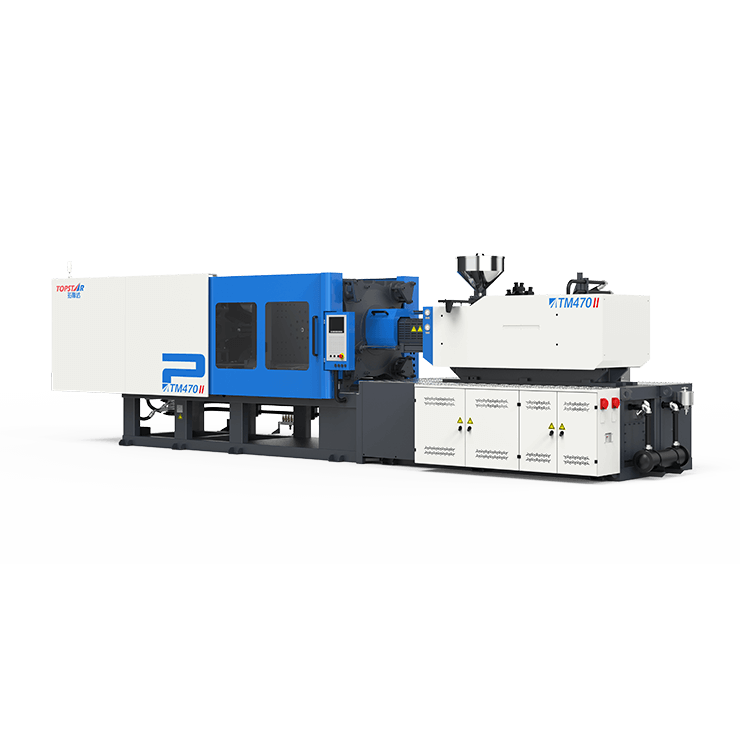
Electric plastic molding machines:
Electric molding machines utilize electric motors to drive the injection and clamping processes, which are significantly more energy-efficient than hydraulic presses. People know these machines for their high precision, repeatability, and faster cycle times. They are also quieter and cleaner in operation and have less environmental impact due to the absence of hydraulic fluid, making them ideal for producing high-quality parts with tight tolerances. This makes them ideal for medical device manufacturing, electronics, and consumer goods industries.
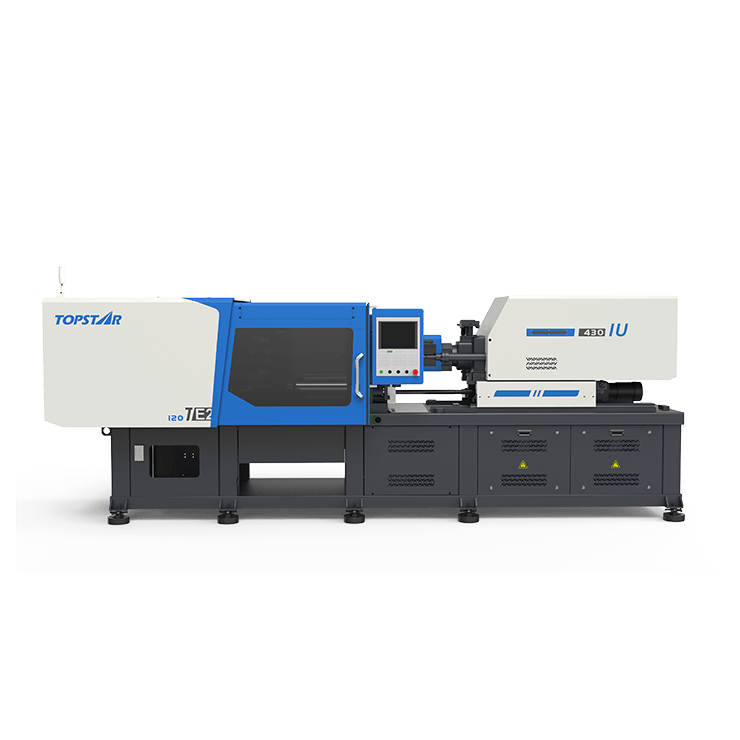
Hybrid Plastic Molding Machines:
Hybrid machines combine the advantages of hydraulic and electric technology. They use hydraulic power to provide clamping force and electric motors to provide injection and mold movement, resulting in a balance between energy efficiency, precision, and high clamping force. Hybrid machines are ideal for manufacturers looking for the best of both worlds—efficient energy use while maintaining the power required for heavy-duty applications. These machines suit industries requiring high-speed production, energy savings, and flexibility in part size and complexity.
Key Factors to Consider When Choosing the Right Plastic Molding Machine
In addition to choosing the right type, several other factors will influence your decision. These include:
Production volume: The type of machine you choose should match the number of parts you intend to produce. Machines for large-volume production require faster cycle times and may offer automation features, while machines for smaller batches may benefit from machines that offer flexibility and easy changeover.
Part Complexity: Some machines are better suited for complex designs and intricate molds, while others are better suited for more straightforward, high-volume items.
Material Compatibility: Different plastic molding machines can handle a wide range of materials. If you plan on using specialized plastics or composites, ensure the machine is compatible with those materials.
Energy Efficiency: Energy costs are essential, especially if you plan on running the machine continuously. Electric plastic molding machines are designed to be more energy efficient, helping you reduce your overall operating costs.
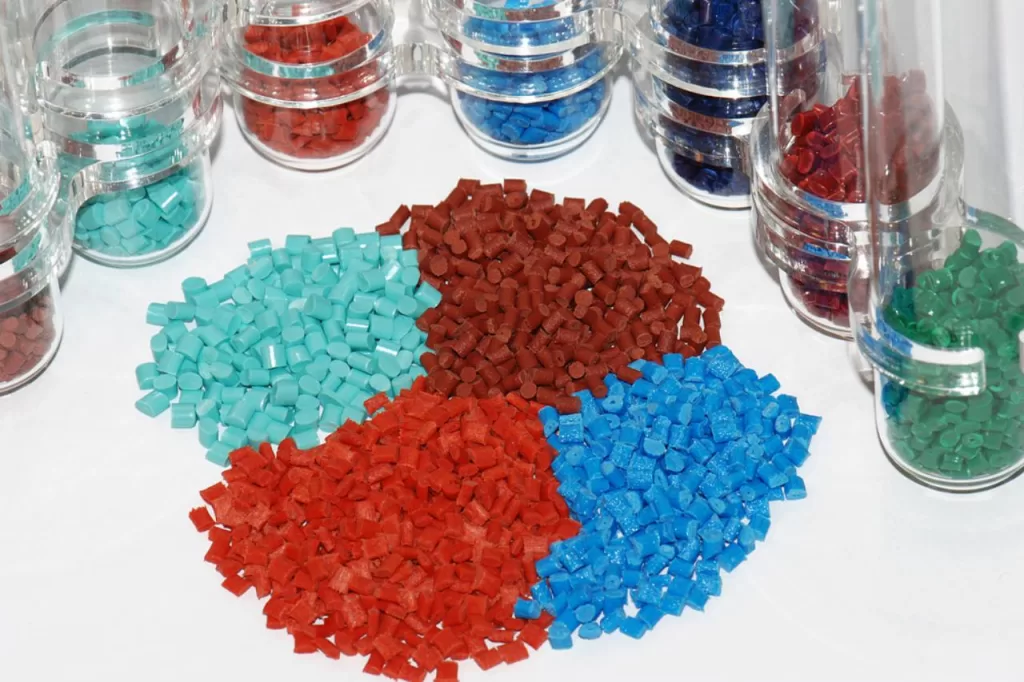
Machine Size and Clamping Force
A plastic molding machine’s size and clamping force are key factors in ensuring it can handle your specific production requirements. Clamping force is the pressure the machine’s mold platens apply to hold the mold closed during the injection process. This is critical to ensure that molten plastic does not escape from the mold cavity during injection.
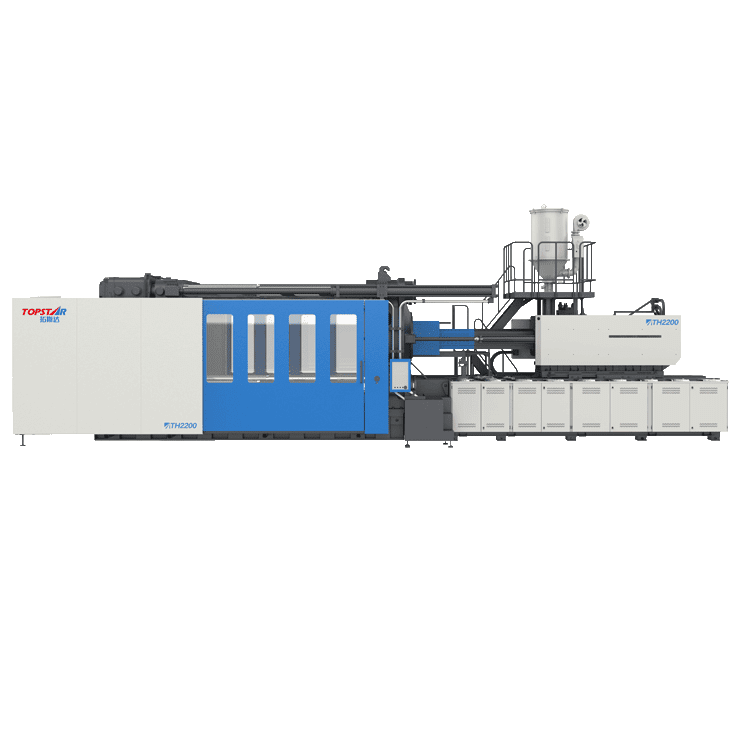
Choosing the right size and clamping force requires understanding the size and volume of the parts you produce. A machine with a higher clamping force is generally required for more extensive or thicker parts that require more pressure to hold the mold together. On the other hand, more minor parts may require less clamping force, which can reduce operating costs. In addition, the size of the plastic molding machine must be compatible with the size of your molds and the layout of your factory floor.
Automation and Control Features
Today’s plastic molding machines have various automation and control features designed to increase production efficiency, reduce human error, and streamline operations. These features are handy for high-volume production where precision and speed are critical. Key automation features to look for include:
Robot integration: Some plastic molding machines come with robotic arms for removing finished parts, placing inserts, or assisting with mold changes, which can increase production speeds and reduce labor costs.
Remote monitoring: Remote control and monitoring systems allow operators to track machine performance from a distance, which is helpful in large-scale operations.
Mold opening compensation: With automatic compensation for mold opening positions, part placement is more accurate, and part consistency is improved.
Choosing a plastic molding machine with advanced automation and control features can improve operational efficiency and ensure consistent part quality.
Consider the total cost of ownership of a plastic molding machine.
While the initial purchase price of a plastic molding machine is an important consideration, the total cost of ownership is also essential. This includes the costs of running, maintaining, and operating the machine throughout its life. Key areas to consider when calculating your total cost of ownership include:
Energy consumption: Energy-efficient machines can reduce your operating costs, especially when running high-volume production runs.
Maintenance costs: Consider the cost of regular maintenance, repairs, and replacement parts.
Cycle time and efficiency: Machines with faster cycle times and higher efficiency can reduce labor costs and increase production, making them a more cost-effective investment in the long run.
Choosing the right injection molding machine for you
In summary, choosing the right plastic molding machine for your business requires careful consideration of many factors, from machine type and production volume to automation features and maintenance support. By following the guidelines in this ultimate guide, you’ll be better able to choose the right machine for your needs, ensuring high-quality production, increased efficiency, and long-term business success.
TRENDING POSTS
- What factors can cause delays in the injection molding process of plastic molding machine? 2022/02/26
- Exhibition Review| Topstar participates in InterPlas Thailand 2024 2022/02/26
- Star Case | Topstar helps Santong upgrade its intelligent plant 2022/02/26
- Topstar Special | National Science and Technology Workers Day 2022/02/26
HOT TOPIC
- 3 in 1 Compact Dehumidifying Dryer
- 5-axis CNC machine
- accuracy
- Air Chillers
- all electric injection molding machine
- All-electric injection molding machines
- and overall production quality. Therefore
- AP-RubberPlas
- automated injection molding machine
- Automation changed engineering
- automation of injection molding robots
- auxiliary machine
- Bench Injection Molding Machine
- Cabinet dryer manufacturers
- Cabinet dryers
- chiller
- CNC Drilling Machine
- CNC Drilling Machines
- cnc engraving machine manufacturer
- cnc laser cutting machine manufacturer
- CNC machine
- CNC Machine Center
- CNC Machine for Sale
- CNC Machine Manufacturing
- CNC Machine Tool
- CNC machine tool product
- CNC Machining Center
- CNC wood carving machine
- Cooling system
- Cross-Walking Single Axis Servo Cylinder Robot
- Cross-Walking Single-Axis Servo Cylinder Robot
- Cross-Walking Three-Axis/Five-Axis Servo Driven Robot
- cross-walking three-axis/five-axis servo-driven robot
- Dehumidifier Dryer
- Dehumidifying Dryer
- delta parallel robot
- Desktop Injection Molding Machine
- Desktop injection molding machines
- Desktop Molding Machine
- desktop plastic injection machine
- Desktop Plastic Injection Molding Machine
- direct clamp injection molding machine
- Direct clamp injection molding machines
- Dosing & mixing system
- Drilling Centers
- Drying and dehumidification system
- drying and dehumidifying equipment
- Drying and Dehumidifying System
- drying system
- effective and efficient. Cabinet dryers are also used in other industries where large quantities of material need to be dried
- efficient injection molding machine
- elbow hydraulic injection molding machines
- electric injection molding machine
- electric injection molding machines
- etc. Among injection molding robots
- exhibition
- features of CNC machine
- Feeding And Conveying System
- Five Axis Machine Center
- Fully automatic injection molding machine
- Gathering Topstar
- giant injection molding machine
- GMU-600 5-Axis Machining Center
- Granulating & Recycling System
- Heavy duty injection molding machine
- Honeycomb rotor dehumidifier
- horizontal injection molding machine
- Horizontal Injection Molding Machines
- Horizontal Injection Moulding Machine
- Horizontal Mixer manufacturer
- How The CNC Machine Works
- hybrid injection molding machine
- hydraulic injection molding machine
- Hydraulic Injection Molding Machines
- in this article
- Industrial robot
- Industrial Robot Chinese brand
- industrial robot parts
- industrial robot supplier
- Industrial robots
- Industry Chain
- Injection Manipulator
- injection mold machines
- Injection molding
- Injection molding automation
- Injection Molding Automation Solution
- injection molding dryer
- Injection molding equipment
- injection molding hopper dryer
- Injection molding machine
- injection molding machine brand
- Injection Molding Machine Factory
- Injection Molding Machine Manufacture
- Injection molding machine manufacturer
- injection molding machine manufacturers
- Injection molding machine procurement
- injection molding machine robotic arm
- injection molding machine with a robot
- Injection molding machines
- injection molding material dehumidifying
- injection molding plant
- Injection Molding Robot
- injection molding robot arm
- Injection molding robot automation
- Injection molding robotic arm
- injection molding robots
- Injection Moulding Robots
- Injection Robot
- Injection robot arm
- Injection robot manufacturer
- Injection robot wholesale
- injection robots
- intelligent injection molding machines
- Introducing Injection Robot
- It is the best choice for drying large quantities of material at once. Cabinetmakers use these machines because they are fast
- large injection molding machine
- Learn what industrial automation and robotics is
- low speed sound-proof granulator
- machine plastic molding
- make sure to add some! Improvements (2) Keyphrase in introduction: Your keyphrase or its synonyms appear in the first paragraph of the copy
- manipulator machine
- manufacturing
- micro injection molding machine
- middle speed granulator
- Mini CNC machine manufacturers.
- Mold Temperature Control System
- mold temperature controller
- molding material Dehumidifying System
- mould temperature controller
- mould temperature controllers
- New electric injection molding machine
- nitrogen dryer manufacturer
- nitrogen dryer system manufacturer
- Oil type mold temperature controller
- open day
- Outbound links: No outbound links appear in this page. Add some! Images: No images appear on this page. Add some! Internal links: No internal links appear in this page
- PET Preform injection molding
- phone case maker machine
- phone case making machine
- plastic bottle making machine
- plastic bottle manufacturing
- plastic bucket making machine
- plastic bucket manufacturing
- Plastic chair making machine
- plastic forming equipment
- plastic hopper dryer
- plastic injection machine
- plastic injection machines
- plastic injection molding
- Plastic injection molding equipment
- Plastic injection molding machine
- Plastic Injection Molding Machines
- plastic injection robot
- Plastic Molding machine
- Plastic Molding Machines
- plastic molding press
- plastic phone case making machine
- plastic-molding machine
- powerful granulator
- Powerful Type Sound-Proof Granulator
- production of plastic seats
- Robot injection molding
- robot injection molding machine
- robot manufacturing companies
- Robotic arm for injection molding machine
- robotic injection molding machines
- robotics in injection molding
- SCARA robot
- SCARA robots
- Service-oriented manufacturing
- Servo Cylinder Robot
- servo driven robot
- Servo Driven Robots
- servo injection robots
- Servo-Driven Robot
- Setup of injection machine
- Silicone Injection Molding Machine
- six-axis industrial robot
- Stainless Hopper Dryer
- Stainless Hopper Dryers
- star club
- swing arm robot
- the choice between servo-driven robots and hydraulic robots will have a certain impact on efficiency
- the most popular injection molding machine
- the type of injection molding robot
- toggle clamp injection molding machine
- Toggle Hydraulic Injection Molding Machines
- toggle injection molding machine
- Top 10 brands of injection robots
- Topstar
- Topstar Engineering
- Topstar Industrial Robots
- Topstar injection molding intelligent
- Topstar Scara Robots
- Useful Injection molding machine
- Vertical machining centers
- volumetric type blender
- water chiller
- water chillers
- water distributor
- Water Type MoldTemperature Controller
- We often face choices when performing injection molding. We will choose the type of injection molding machine
- wholesale of injection molding machines
- x carve CNC