Intelligent transformation of injection molding machines: How to cope with the Spanish injection molding market?
2025/03/03 By Topstar
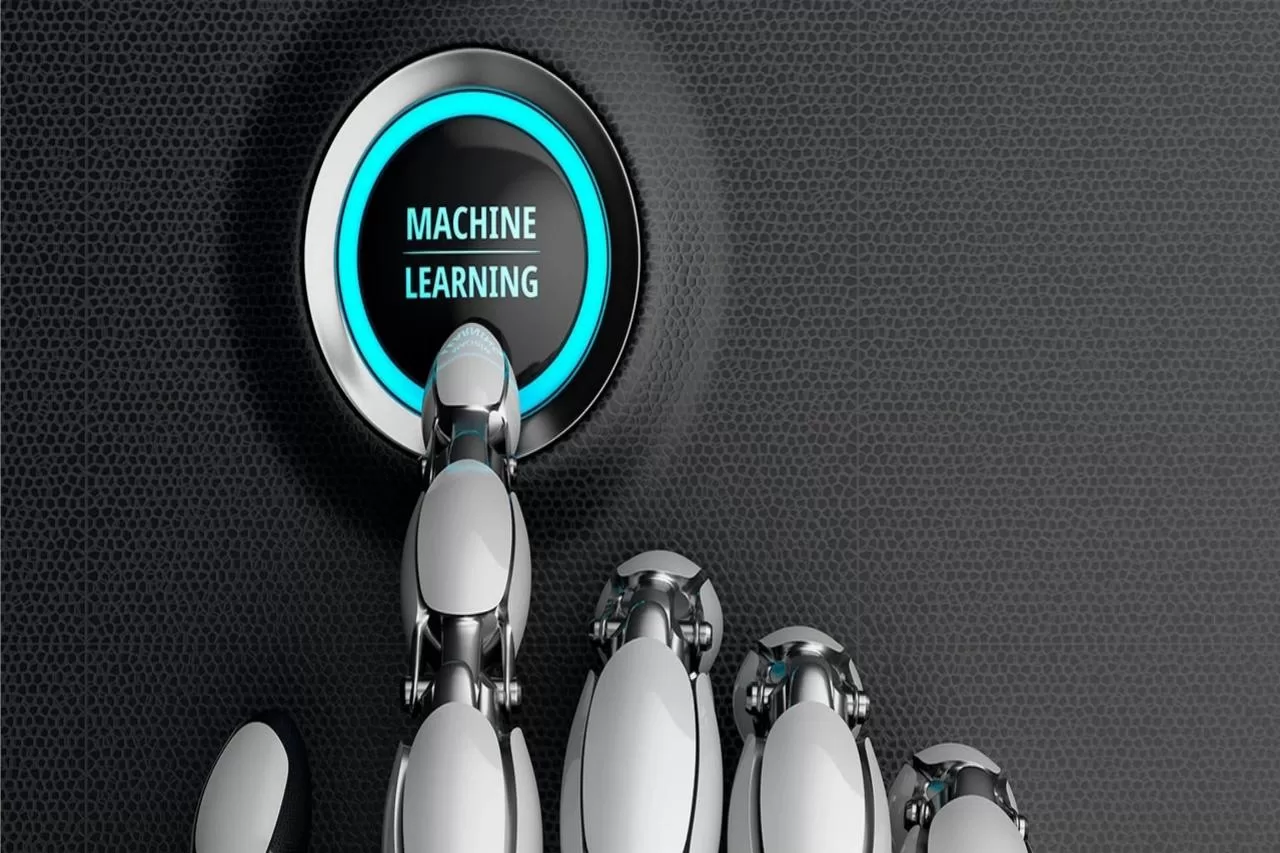
Demand in Spain is focused on large, high-precision and high-efficiency injection molding machines for producing automotive parts, including interior components, electronic components and lightweight plastic parts. However, rising labor costs and the need for faster and more reliable production have driven the market towards integrated intelligent solutions. To this end, Topstar has taken the lead in developing intelligent injection molding machines, using advanced auxiliary equipment, IoT remote monitoring and data acquisition systems to improve production efficiency while reducing manual intervention. This article explores in depth how our intelligent transformation strategy enables injection molding machines to continuously optimize control, communication and performance to meet the injection molding needs of the Spanish market.
Spanish injection molding market and demand for injection molding machines
Spain is the second largest automobile producer in Europe. Volkswagen, Peugeot and Citroen are all located in Spain. It is also a central hub for the European automotive industry, and many of its factories are dedicated to producing high-quality parts. These Spanish automakers require injection molding machines to have high precision, high speed, and consistent quality within strict tolerances. In this competitive environment, injection molding machines are also needed to produce complex plastic parts that meet rigorous standards.
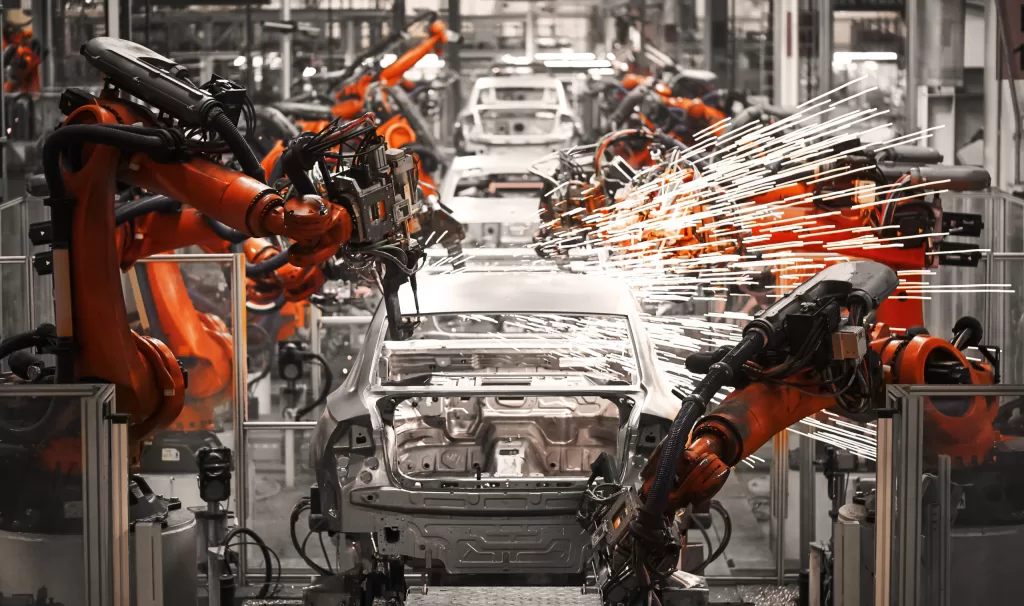
For the Spanish market, traditional injection molding equipment often cannot meet the requirements of intelligence and equipment integration. Due to high labor costs and the need to continuously improve efficiency, there is a strong demand for a fully integrated system that combines injection molding robots, auxiliary equipment and remote monitoring based on the Internet of Things. Reimagining the injection molding process as an integrated system (real-time communication, control, optimization and perception of equipment) is Topstar’s understanding of injection molding intelligence, and it can also meet the needs of such intelligent injection molding machines. Functions that ensure optimal control of key factors such as temperature, speed, position, pressure and cycle time.
The Injection Molding Machine Concept: Redefining the Injection Molding Machine
Topstar’s “injection molding process integrated machine” concept combines hardware and software into a unified ecosystem. Unlike traditional setups where robots, dryers and temperature controllers operate independently, Topstar’s injection molding machines coordinate natively with peripherals through a single control interface. With a self-developed control system, the injection molding machine performs its primary function of molding plastic parts and coordinates with peripherals such as injection molding robots and auxiliary equipment such as temperature controllers. This holistic approach finely tunes and optimizes every aspect of the molding process for maximum efficiency.
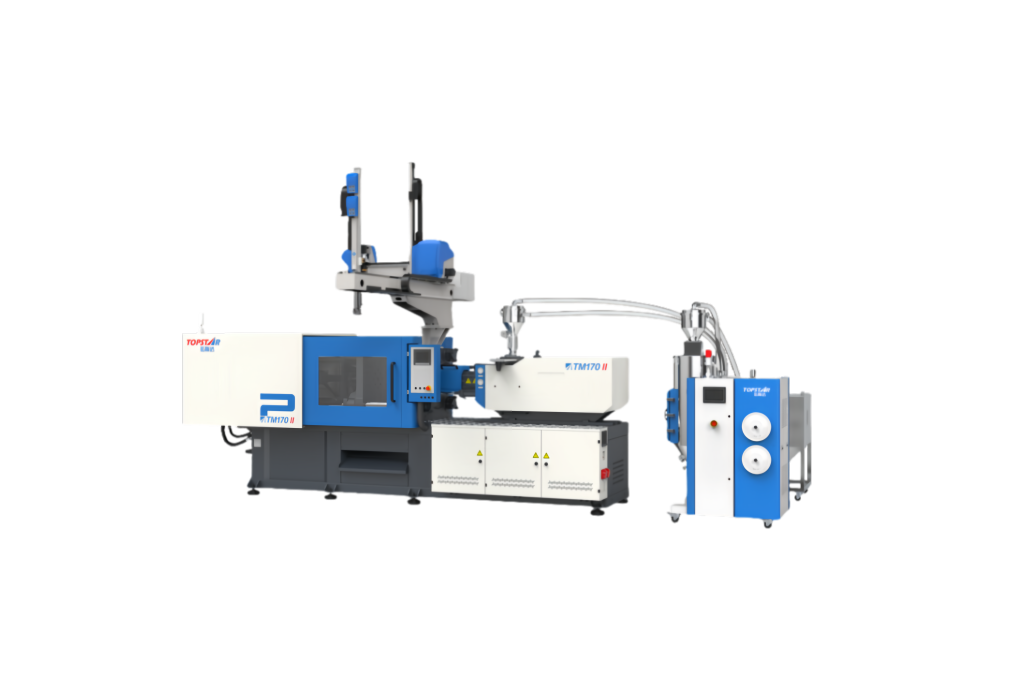
The embedded communication framework facilitates real-time data exchange between multiple components. It enables rapid adjustment of process parameters, ensuring continuous monitoring and adjustment of variables such as temperature, pressure, speed, and positioning. This tight integration minimizes the margin for error and reduces the possibility of production interruptions due to misalignment or process deviations. A single HMI panel allows operators to adjust mold temperature, screw speed, and injection robot trajectory.
Leveraging IoT and data collection for process optimization
The cornerstone of the intelligent transformation of injection molding machines is the strategic use of Internet of Things (IoT) technology and data collection systems. In today’s intelligent age, real-time data is the lifeblood of efficient manufacturing processes. For the injection molding machine, integrated IoT sensors and advanced data analytics enable continuous monitoring and precise control of every stage of the production process. This intelligent digital integration is particularly valuable in high-risk environments. It can be critical to achieving optimal performance and minimal downtime for the Spanish automotive industry and other industries.
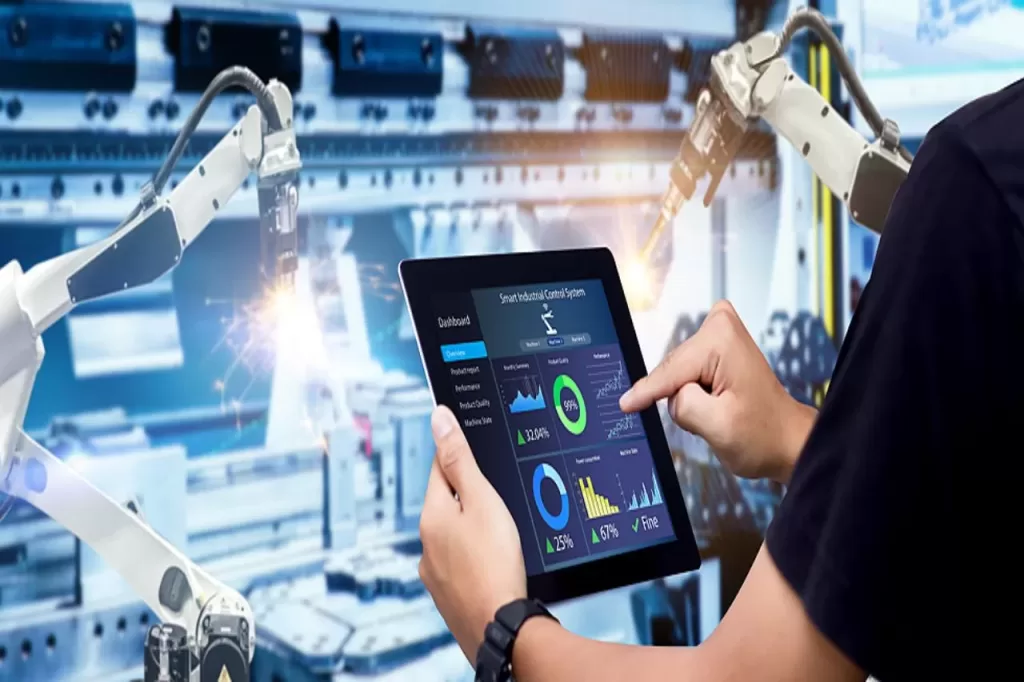
Topstar’s intelligent injection molding machines collect many operating data, including temperature fluctuations, pressure changes, cycle times, and material flow rates. The system transmits this data in real-time to a centralized control unit, which analyzes performance trends, identifies potential problems, and dynamically adjusts parameters. Our system optimizes each molding cycle by leveraging data collection capabilities for maximum efficiency and quality. In addition, remotely monitoring and adjusting processes minimizes production interruptions and reduces the need for on-site manual supervision, further reducing labor costs.
Optimize production efficiency and reduce manual intervention.
High labor costs in Spain and EU sustainable development regulations have pressured minimizing manual intervention. In response to this need, under the integrated control of injection molding and process linkage, Topstar’s injection molding machines can reduce the operator’s workload of fine-tuning and monitoring the main and auxiliary equipment, reduce labor costs, and improve production efficiency. It enables one operator to monitor and fine-tune multiple devices, reducing the labor input of various devices. After calculation, 18 injection molding machines require at least 25 workers according to the original staffing, but now only 11 workers are needed to complete all the work.
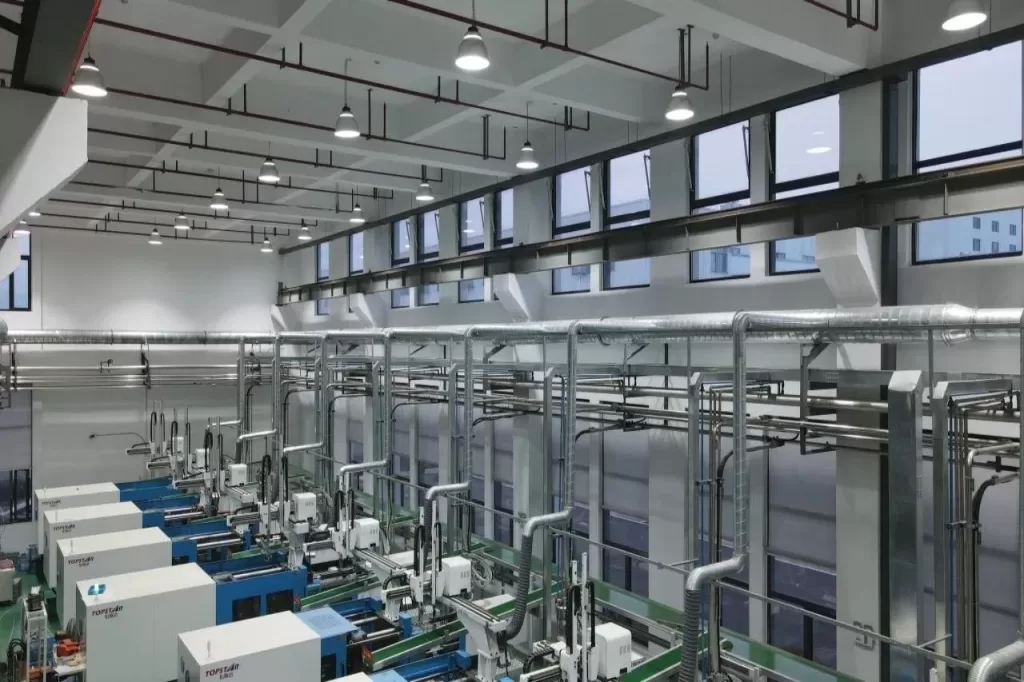
When manufacturing high-precision automotive parts that require precise tolerances, reducing manual intervention can reduce labor costs and minimize the risk of human error. Thus, manufacturers can achieve a more reliable and predictable manufacturing process and meet the high standards required by the Spanish market.
Future trends in the Spanish injection molding market
The advantages of using intelligent injection molding machines are apparent. For Spanish automakers, our intelligent system provides a solution to optimize production efficiency, reduce dependence on labor, and improve overall product quality. Integrating the Internet of Things, data acquisition, and intelligent control systems ensures the streamlining and efficiency of the injection molding process. It provides real-time insights, enabling proactive maintenance and continuous improvement. These technological advances have the potential to reduce downtime, lower production costs, and gain a more substantial competitive advantage in the global market. The benefits of intelligent injection molding machines also extend to environmental management, enabling a greener and more sustainable manufacturing process.
Bringing innovative transformation to the Spanish injection molding market
Topstar’s innovative approach integrates advanced robotics, IoT remote monitoring, data acquisition and integrated control systems to provide a robust solution that meets the high precision and efficiency requirements of automotive production. By focusing on integrating software and hardware, our injection molding machines optimize every stage of the injection molding process – from pretreatment and plasticization to molding control and removal coordination. These intelligent systems improve production efficiency through manual intervention, providing reduced operating costs and a more sustainable manufacturing process.
TRENDING POSTS
- What factors can cause delays in the injection molding process of plastic molding machine? 2025/03/03
- Exhibition Review| Topstar participates in InterPlas Thailand 2024 2025/03/03
- Star Case | Topstar helps Santong upgrade its intelligent plant 2025/03/03
- Topstar Special | National Science and Technology Workers Day 2025/03/03
HOT TOPIC
- 3 in 1 Compact Dehumidifying Dryer
- 5-axis CNC machine
- accuracy
- Air Chillers
- all electric injection molding machine
- all electric injection molding machines
- All-electric injection molding machines
- and overall production quality. Therefore
- AP-RubberPlas
- automated injection molding machine
- Automation changed engineering
- automation of injection molding robots
- auxiliary machine
- Bench Injection Molding Machine
- Cabinet dryer manufacturers
- Cabinet dryers
- chiller
- CNC Drilling Machine
- CNC Drilling Machines
- cnc engraving machine manufacturer
- cnc laser cutting machine manufacturer
- CNC machine
- CNC Machine Center
- CNC Machine for Sale
- CNC Machine Manufacturing
- CNC Machine Tool
- CNC machine tool product
- CNC Machining Center
- CNC wood carving machine
- Cooling system
- Cross-Walking Single Axis Servo Cylinder Robot
- Cross-Walking Single-Axis Servo Cylinder Robot
- Cross-Walking Three-Axis/Five-Axis Servo Driven Robot
- cross-walking three-axis/five-axis servo-driven robot
- Dehumidifier Dryer
- Dehumidifying Dryer
- delta parallel robot
- Desktop Injection Molding Machine
- Desktop injection molding machines
- Desktop Molding Machine
- desktop plastic injection machine
- Desktop Plastic Injection Molding Machine
- direct clamp injection molding machine
- Direct clamp injection molding machines
- Dosing & mixing system
- Drilling Centers
- Drying and dehumidification system
- drying and dehumidifying equipment
- Drying and Dehumidifying System
- drying system
- effective and efficient. Cabinet dryers are also used in other industries where large quantities of material need to be dried
- efficient injection molding machine
- elbow hydraulic injection molding machines
- electric injection molding machine
- electric injection molding machines
- energy-saving injection molding machine
- etc. Among injection molding robots
- exhibition
- features of CNC machine
- Feeding And Conveying System
- Five Axis Machine Center
- Fully automatic injection molding machine
- Gathering Topstar
- giant injection molding machine
- GMU-600 5-Axis Machining Center
- Granulating & Recycling System
- Heavy duty injection molding machine
- Honeycomb rotor dehumidifier
- horizontal injection molding machine
- Horizontal Injection Molding Machines
- Horizontal Injection Moulding Machine
- Horizontal Mixer manufacturer
- How The CNC Machine Works
- hybrid injection molding machine
- hydraulic injection molding machine
- Hydraulic Injection Molding Machines
- in this article
- Industrial robot
- Industrial Robot Chinese brand
- industrial robot parts
- industrial robot supplier
- Industrial robots
- Industry Chain
- Injection Manipulator
- injection mold machines
- Injection molding
- Injection molding automation
- Injection Molding Automation Solution
- injection molding dryer
- Injection molding equipment
- injection molding hopper dryer
- Injection molding machine
- injection molding machine brand
- Injection Molding Machine Factory
- Injection Molding Machine Manufacture
- Injection molding machine manufacturer
- injection molding machine manufacturers
- Injection molding machine procurement
- injection molding machine robotic arm
- injection molding machine with a robot
- Injection molding machines
- injection molding material dehumidifying
- injection molding plant
- Injection Molding Robot
- injection molding robot arm
- Injection molding robot automation
- Injection molding robotic arm
- injection molding robots
- Injection Moulding Robots
- Injection Robot
- Injection robot arm
- Injection robot manufacturer
- Injection robot wholesale
- injection robots
- intelligent injection molding machines
- Introducing Injection Robot
- It is the best choice for drying large quantities of material at once. Cabinetmakers use these machines because they are fast
- large injection molding machine
- Learn what industrial automation and robotics is
- linear robot
- low speed sound-proof granulator
- machine plastic molding
- make sure to add some! Improvements (2) Keyphrase in introduction: Your keyphrase or its synonyms appear in the first paragraph of the copy
- manipulator machine
- manufacturing
- micro injection molding machine
- middle speed granulator
- Mini CNC machine manufacturers.
- Mold Temperature Control System
- mold temperature controller
- molding material Dehumidifying System
- mould temperature controller
- mould temperature controllers
- New electric injection molding machine
- nitrogen dryer manufacturer
- nitrogen dryer system manufacturer
- Oil type mold temperature controller
- open day
- Outbound links: No outbound links appear in this page. Add some! Images: No images appear on this page. Add some! Internal links: No internal links appear in this page
- PET Preform injection molding
- phone case maker machine
- phone case making machine
- plastic bottle making machine
- plastic bottle manufacturing
- plastic bucket making machine
- plastic bucket manufacturing
- Plastic chair making machine
- plastic forming equipment
- plastic hopper dryer
- plastic injection machine
- plastic injection machines
- plastic injection molding
- Plastic injection molding equipment
- Plastic injection molding machine
- Plastic Injection Molding Machines
- plastic injection robot
- Plastic Molding machine
- Plastic Molding Machines
- plastic molding press
- plastic phone case making machine
- plastic-molding machine
- powerful granulator
- Powerful Type Sound-Proof Granulator
- production of plastic seats
- Robot injection molding
- robot injection molding machine
- robot manufacturing companies
- Robotic arm for injection molding machine
- robotic injection molding machines
- robotics in injection molding
- SCARA robot
- SCARA robots
- Service-oriented manufacturing
- Servo Cylinder Robot
- servo driven robot
- Servo Driven Robots
- servo injection robots
- Servo-Driven Robot
- Setup of injection machine
- Silicone Injection Molding Machine
- six-axis industrial robot
- Stainless Hopper Dryer
- Stainless Hopper Dryers
- star club
- swing arm robot
- the choice between servo-driven robots and hydraulic robots will have a certain impact on efficiency
- the most popular injection molding machine
- the type of injection molding robot
- toggle clamp injection molding machine
- Toggle Hydraulic Injection Molding Machines
- toggle injection molding machine
- Top 10 brands of injection robots
- Topstar
- Topstar Engineering
- Topstar Industrial Robots
- Topstar injection molding intelligent
- Topstar Scara Robots
- Useful Injection molding machine
- Vertical machining centers
- volumetric type blender
- water chiller
- water chillers
- water distributor
- Water Type MoldTemperature Controller
- We often face choices when performing injection molding. We will choose the type of injection molding machine
- wholesale of injection molding machines
- x carve CNC