Intelligent Injection Molding in Indian Factories with Injection Mold Machines
2025/03/26 By Topstar
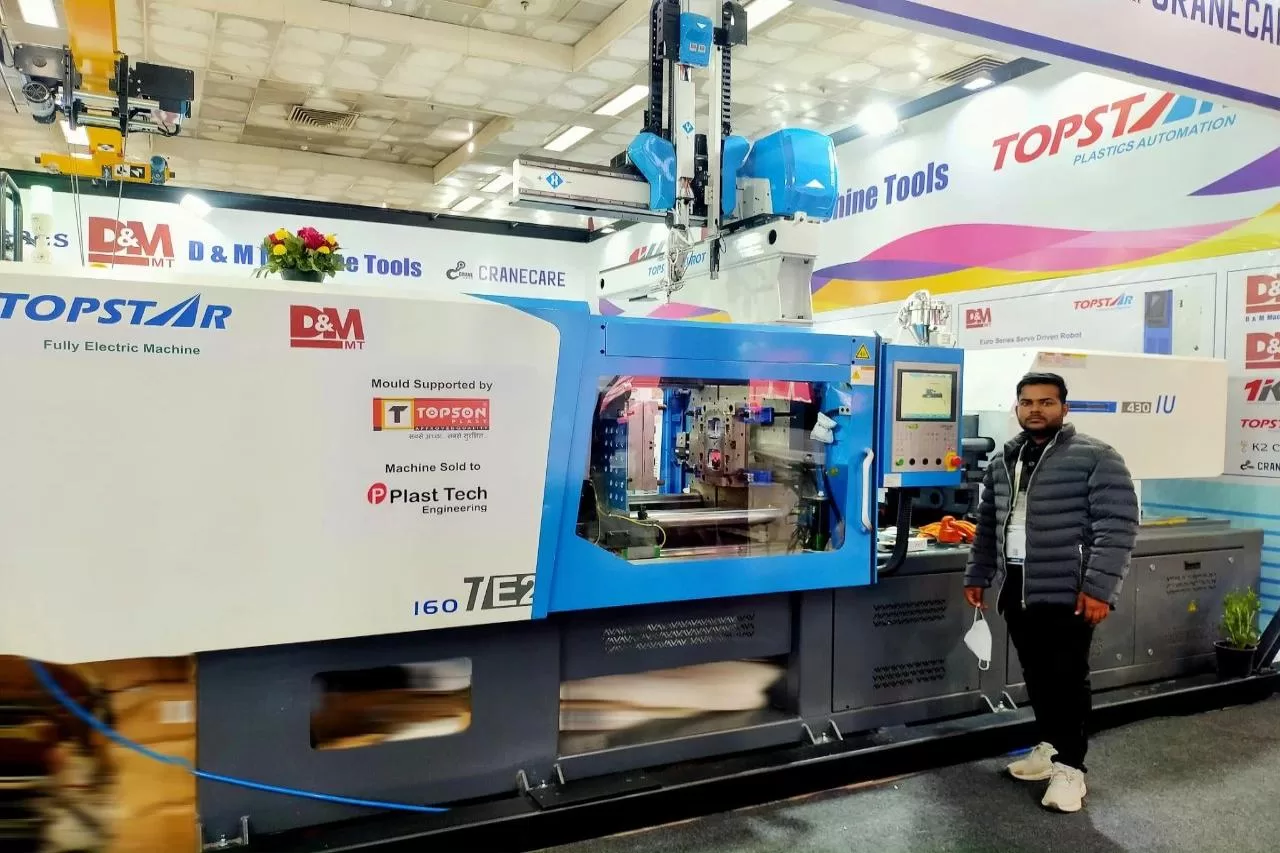
The Indian plastics manufacturing industry is experiencing unprecedented growth, driven by growing demand from the automotive, packaging and consumer goods industries. However, this rapid expansion is constrained by a significant technological gap in India’s injection molding capabilities. Today, the global manufacturing industry is implementing Industry 4.0 solutions through connected smart factories, but currently, about 75% of Indian plastics manufacturers, especially small and medium-sized enterprises, still use injection mold machines that rely heavily on manual processes. This technological gap has caused multiple pain points: inconsistent product quality, non-compliance with international standards, excessive energy consumption, resulting in rising operating costs, low production efficiency, and limiting competitiveness in the global market. For the Indian market, Topstar can provide specialized injection molding solutions that combine automation, intelligence, and energy-saving technologies, focusing on improving equipment performance and changing the entire injection molding production ecosystem.
Automation gap in Indian injection mold machines factories
The automation gap in the Indian plastics manufacturing industry is particularly serious, with most small and medium-sized enterprises operating at a level far below global benchmarks. The average automation penetration rate of Indian factories is only 35-40%. This gap is reflected in several key aspects:
- Production lines require excessive manual intervention, such as material feeding, mold changes, and quality checks;
- Operators often perform process monitoring through visual inspection rather than sensor-based systems.;
- Production data collection is still largely paper-based;
Productivity levels in India’s injection molding business are typically 30-40% lower than their automated counterparts in developed markets. Topstar solves these issues with a comprehensive injection molding solution that Indian manufacturers can implement in phases, allowing them to gradually upgrade their capabilities. The injection molding solutions provided include injection molding robot handling systems that can reduce labor requirements by up to 60%, automated quality inspection stations using machine vision, and centralized production monitoring dashboards that provide real-time performance analysis.
Outdated injection mold machines and their impact on quality
The widespread aging of injection mold machines in India also poses a continuous quality challenge to manufacturers, weakening their competitiveness in the high-end market. Many small and medium enterprises are still using 15-20-year-old hydraulic presses that lack modern precision controls and require frequent repairs and maintenance. These traditional systems often experience pressure variations of more than ±5% and temperature fluctuations of ±3-5°C —far beyond the tolerances required for high-precision applications such as medical or automotive parts.
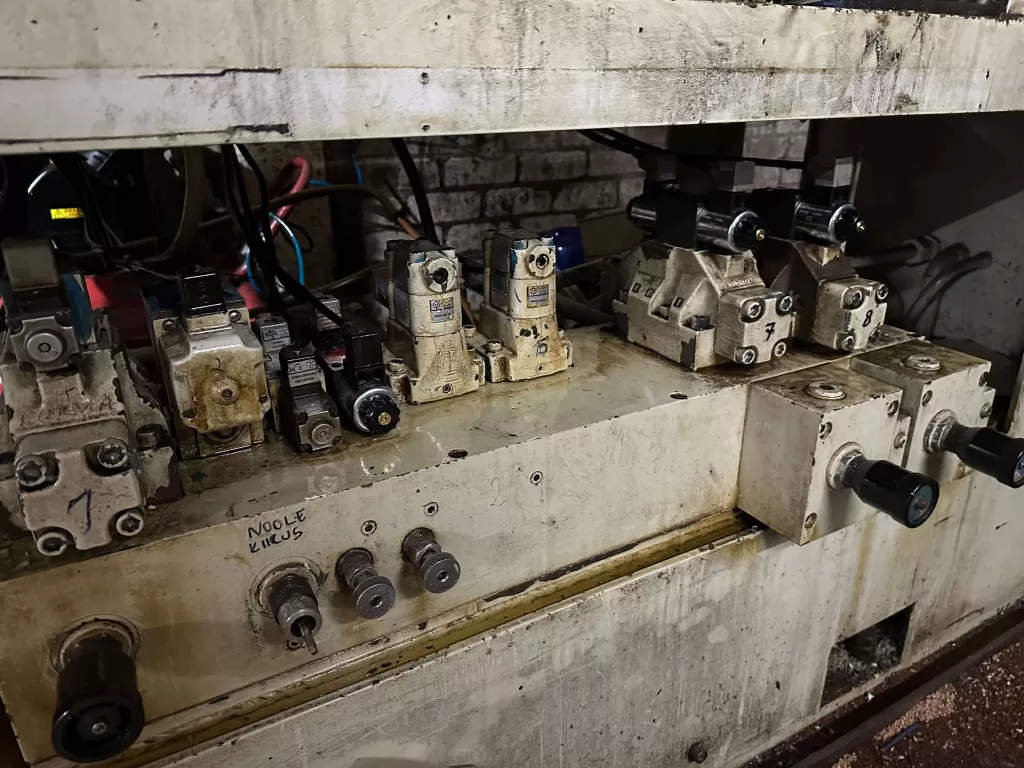
The resulting quality issues include dimensional inaccuracies, surface defects and material degradation – resulting in rejection rates that are 3-4 times higher than global benchmarks. According to industry surveys, nearly 40% of Indian plastic component exporters face order cancellations due to inconsistent quality. Topstar’s new generation of electric injection mold machines addresses these challenges through intelligent electric drive control systems, self-developed full-set injection mold equipment, and interconnected data between injection mold equipment systems to improve production efficiency and product quality.
Energy efficiency is a factor of change.
Over the past five years, electricity costs have increased by an average of 8-10% per year. Traditional hydraulic injection mold machines still dominate the Indian market. They are particularly energy-intensive and typically waste 40-50% of input power due to heat and continuous pump operation. India’s frequent power fluctuations and voltage inconsistencies exacerbate this inefficiency, further reducing equipment performance and energy utilization.
Topstar’s electric injection mold machines use intelligent electric drive control, which can reduce the impact of communication delays on the high-speed operation of servo motors, realize real-time control of servo motors, improve the accuracy of position, speed and pressure control, and increase the response speed by 8-16 times. At the same time, it can cooperate with peripheral auxiliary equipment and injection molding robots to reduce the number of times front-line operators debug the equipment, especially for those industries with clean production requirements. Compared to hydraulic models, the system reduces net consumption by 50-70%.
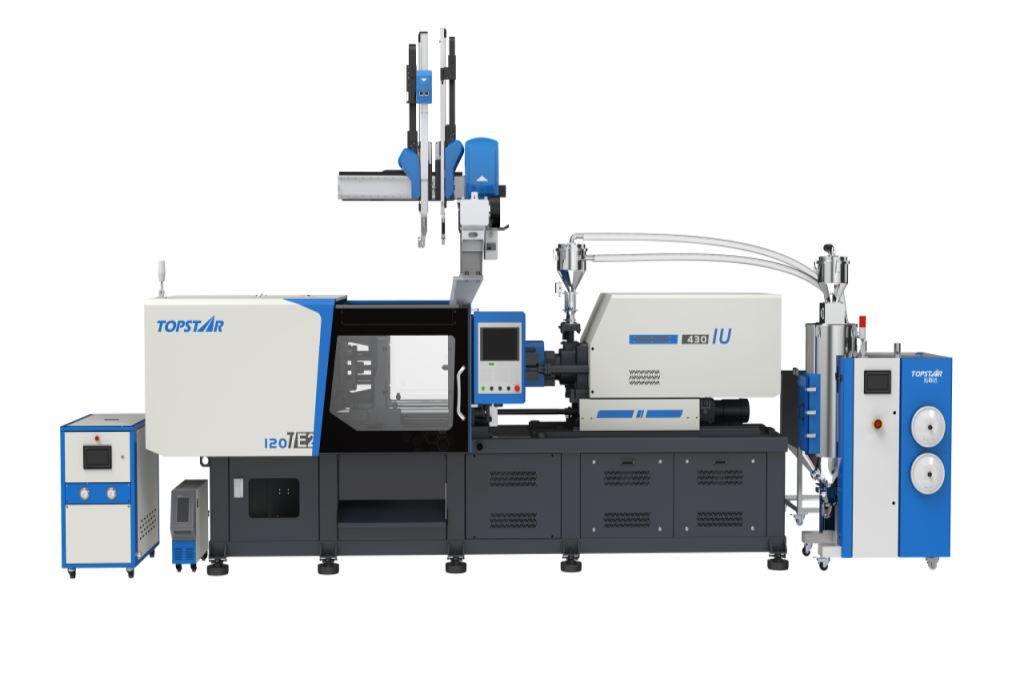
The rise of intelligent automation
The integration of intelligent technology and injection mold machines is changing the production capacity of factories across India. Indian manufacturers, especially those in the consumer electronics, automotive and home appliance industries, are increasingly in need of machines with intelligent functions to simplify operations, reduce manual labor and improve production efficiency. The human-machine interface on the injection mold machine can monitor everything from screw position accuracy to melt viscosity in real-time, creating a comprehensive digital twin of the injection molding process. We design the human-machine interface (HMI) on our machines for India’s multilingual workforce, and it features an intuitive graphical interface. Remote monitoring capabilities enable operators to oversee multiple machines via mobile devices and receive instant alerts about any process deviations. Most importantly, our systems include adaptive learning capabilities that continuously improve performance based on historical production data, making each production run smarter.
Tailor-made injection molding solutions for Indian SMEs
Topstar currently has a branch in India, which makes it easier to provide Indian customers with specialized injection molding machine solutions that balance advanced features with practical economics. They can be designed to be durable in India’s challenging operating environment – with enhanced cooling systems for hot regions, corrosion-resistant components for coastal areas, and robust power conditioning for areas with unstable power supply. At the same time, Topstar’s application engineering team in India works closely with each customer to optimize the machine configuration for their specific products and materials, whether it’s molding thin-wall packaging with recycled PET or molding precision automotive parts with engineering-grade resins. This localized support extends to training programs to improve operators’ machine operation and basic troubleshooting skills, creating lasting value.
Towards a smarter, more efficient path
By integrating advanced intelligence, energy-saving features and precise control systems, Indian manufacturers can achieve higher output, greater consistency and more sustainable manufacturing. The continued development and adoption of smart injection molding technology will become a major driver of growth in India’s manufacturing industry, helping to enhance the country’s position in the global market.
TRENDING POSTS
- What factors can cause delays in the injection molding process of plastic molding machine? 2025/03/26
- Exhibition Review| Topstar participates in InterPlas Thailand 2024 2025/03/26
- Star Case | Topstar helps Santong upgrade its intelligent plant 2025/03/26
- Topstar Special | National Science and Technology Workers Day 2025/03/26
HOT TOPIC
- 3 in 1 Compact Dehumidifying Dryer
- 5-axis CNC machine
- accuracy
- Air Chillers
- all electric injection molding machine
- all electric injection molding machines
- All-electric injection molding machines
- and overall production quality. Therefore
- AP-RubberPlas
- automated injection molding machine
- Automation changed engineering
- automation of injection molding robots
- auxiliary machine
- Bench Injection Molding Machine
- Cabinet dryer manufacturers
- Cabinet dryers
- chiller
- CNC Drilling Machine
- CNC Drilling Machines
- cnc engraving machine manufacturer
- cnc laser cutting machine manufacturer
- CNC machine
- CNC Machine Center
- CNC Machine for Sale
- CNC Machine Manufacturing
- CNC Machine Tool
- CNC machine tool product
- CNC Machining Center
- CNC wood carving machine
- Cooling system
- Cross-Walking Single Axis Servo Cylinder Robot
- Cross-Walking Single-Axis Servo Cylinder Robot
- Cross-Walking Three-Axis/Five-Axis Servo Driven Robot
- cross-walking three-axis/five-axis servo-driven robot
- Dehumidifier Dryer
- Dehumidifying Dryer
- delta parallel robot
- Desktop Injection Molding Machine
- Desktop injection molding machines
- Desktop Molding Machine
- desktop plastic injection machine
- Desktop Plastic Injection Molding Machine
- direct clamp injection molding machine
- Direct clamp injection molding machines
- Dosing & mixing system
- Drilling Centers
- Drying and dehumidification system
- drying and dehumidifying equipment
- Drying and Dehumidifying System
- drying system
- effective and efficient. Cabinet dryers are also used in other industries where large quantities of material need to be dried
- efficient injection molding machine
- elbow hydraulic injection molding machines
- electric injection molding machine
- electric injection molding machines
- energy-saving injection molding machine
- etc. Among injection molding robots
- exhibition
- features of CNC machine
- Feeding And Conveying System
- Five Axis Machine Center
- Fully automatic injection molding machine
- Gathering Topstar
- giant injection molding machine
- GMU-600 5-Axis Machining Center
- Granulating & Recycling System
- Heavy duty injection molding machine
- High-precision electric molding machines
- high-precision plastic molding machines
- Honeycomb rotor dehumidifier
- horizontal injection molding machine
- Horizontal Injection Molding Machines
- Horizontal Injection Moulding Machine
- Horizontal Mixer manufacturer
- How The CNC Machine Works
- hybrid injection molding machine
- hydraulic injection molding machine
- Hydraulic Injection Molding Machines
- in this article
- Industrial robot
- Industrial Robot Chinese brand
- industrial robot parts
- industrial robot supplier
- Industrial robots
- Industry Chain
- Injection Manipulator
- injection manipulator robot
- injection mold machines
- Injection molding
- Injection molding automation
- Injection Molding Automation Solution
- injection molding dryer
- Injection molding equipment
- injection molding hopper dryer
- Injection molding machine
- injection molding machine brand
- Injection Molding Machine Factory
- Injection Molding Machine Manufacture
- Injection molding machine manufacturer
- injection molding machine manufacturers
- Injection molding machine procurement
- injection molding machine robotic arm
- injection molding machine with a robot
- Injection molding machines
- injection molding material dehumidifying
- injection molding plant
- Injection Molding Robot
- injection molding robot arm
- Injection molding robot automation
- Injection molding robotic arm
- injection molding robots
- Injection Moulding Robots
- Injection Robot
- Injection robot arm
- Injection robot manufacturer
- Injection robot wholesale
- injection robots
- intelligent injection molding machines
- Introducing Injection Robot
- It is the best choice for drying large quantities of material at once. Cabinetmakers use these machines because they are fast
- large injection molding machine
- Learn what industrial automation and robotics is
- linear robot
- low speed sound-proof granulator
- machine plastic molding
- make sure to add some! Improvements (2) Keyphrase in introduction: Your keyphrase or its synonyms appear in the first paragraph of the copy
- manipulator machine
- manufacturing
- micro injection molding machine
- middle speed granulator
- Mini CNC machine manufacturers.
- Mold Temperature Control System
- mold temperature controller
- molding material Dehumidifying System
- mould temperature controller
- mould temperature controllers
- New electric injection molding machine
- nitrogen dryer manufacturer
- nitrogen dryer system manufacturer
- Oil type mold temperature controller
- open day
- Outbound links: No outbound links appear in this page. Add some! Images: No images appear on this page. Add some! Internal links: No internal links appear in this page
- PET Preform injection molding
- phone case maker machine
- phone case making machine
- plastic bottle making machine
- plastic bottle manufacturing
- plastic bucket making machine
- plastic bucket manufacturing
- Plastic chair making machine
- plastic forming equipment
- plastic hopper dryer
- plastic injection machine
- plastic injection machines
- plastic injection molding
- Plastic injection molding equipment
- Plastic injection molding machine
- Plastic Injection Molding Machines
- plastic injection robot
- Plastic Molding machine
- Plastic Molding Machines
- plastic molding press
- plastic phone case making machine
- plastic-molding machine
- powerful granulator
- Powerful Type Sound-Proof Granulator
- precision injection molding
- production of plastic seats
- Robot injection molding
- robot injection molding machine
- robot manufacturing companies
- Robotic arm for injection molding machine
- robotic injection molding machines
- robotics in injection molding
- SCARA robot
- SCARA robots
- Service-oriented manufacturing
- Servo Cylinder Robot
- servo driven robot
- Servo Driven Robots
- servo injection robots
- Servo-Driven Robot
- Setup of injection machine
- Silicone Injection Molding Machine
- six-axis industrial robot
- Stainless Hopper Dryer
- Stainless Hopper Dryers
- star club
- swing arm robot
- the choice between servo-driven robots and hydraulic robots will have a certain impact on efficiency
- the most popular injection molding machine
- the type of injection molding robot
- toggle clamp injection molding machine
- Toggle Hydraulic Injection Molding Machines
- toggle injection molding machine
- Top 10 brands of injection robots
- Topstar
- Topstar Engineering
- Topstar Industrial Robots
- Topstar injection molding intelligent
- Topstar Scara Robots
- Useful Injection molding machine
- Vertical machining centers
- volumetric type blender
- water chiller
- water chillers
- water distributor
- Water Type MoldTemperature Controller
- We often face choices when performing injection molding. We will choose the type of injection molding machine
- wholesale of injection molding machines
- x carve CNC