Innovative Injection Molding Technology in Production of plastic seats
2023/09/20 By Topstar
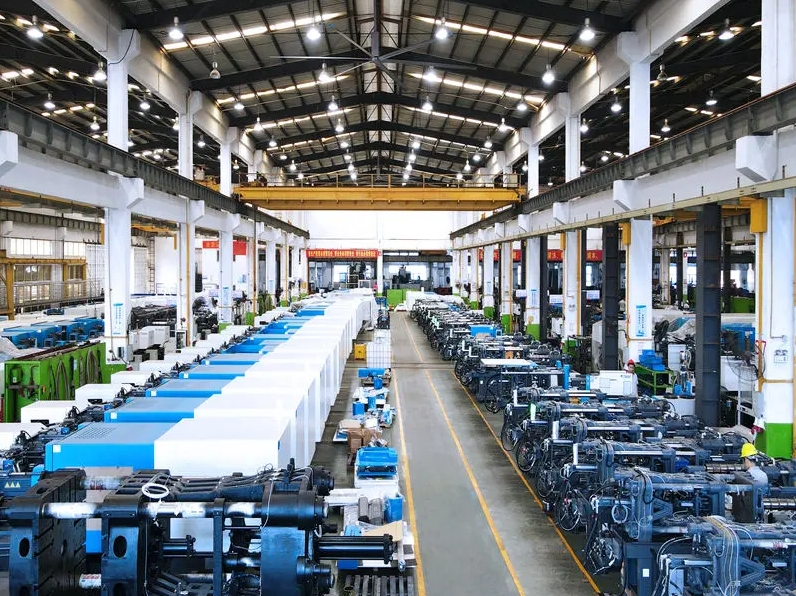
In today’s ever-evolving manufacturing world, innovation is the driving force behind our daily product improvements, driving us to develop better products for the market continuously. Among them, our injection molding technology is an innovation that changes the production of plastic seats. In this sharing, we share with you how this innovative process shapes the future of comfortable seating and revolutionizes how plastic chairs are produced.
Injection molding process for the production of plastic seats
Imagine pouring molten plastic into molds to create the perfect seat that performs a beautiful dance. This is the art of injection molding. This precise and efficient process allows manufacturers to create centers with unparalleled precision. So whether it’s the ergonomic contours of a car seat or the comfortable embrace of your favorite chair, injection molding ensures that every detail is captured. Injection molding starts with a careful selection of plastic materials. The materials are heated until they reach a liquid state and are ready to be poured into molds. These molds are precisely engineered to create plastic seats with the desired shape and functionality. When molten plastic is injected, it fills every nook and cranny of the mold, creating a chair that perfectly replicates the mold’s design.
Efficiency in the production of plastic seats
One of the outstanding features of injection molding in producing plastic seats is its efficiency. The process is speedy, and multiple cores can be made within minutes. This not only reduces production time but also minimizes material waste. Manufacturers can optimize their resources to save costs and create a greener, more sustainable future. Our Topstar injection molding machines have advanced technology to ensure consistent and precise production. This means that every seat produced is nearly identical in quality and appearance. Whether making a small batch of seats or paying thousands for a large project, injection molding guarantees reliability and efficiency.
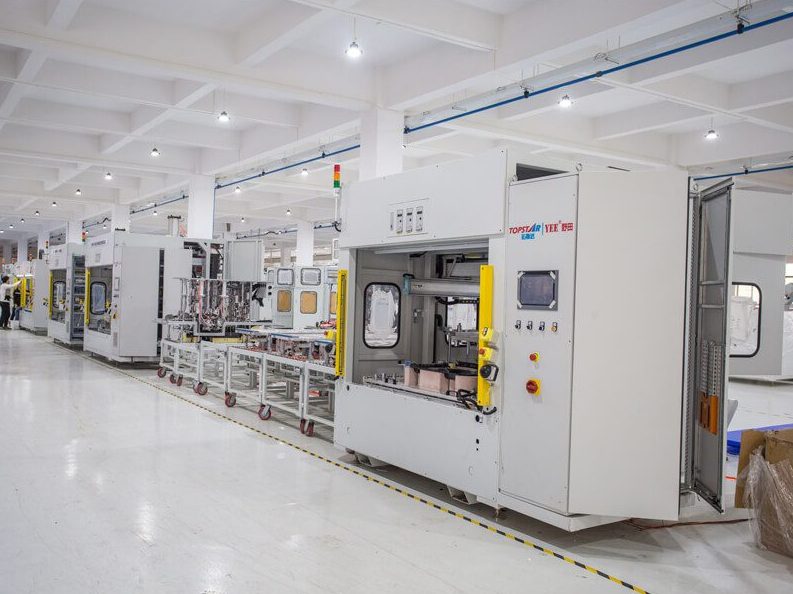
Injection molding also has customization capabilities!
The beauty of injection molding is its ability to create custom solutions. Whether you need a luxury car seat or an ergonomic office chair, injection molding can be tailored to meet specific design requirements. This kind of flexibility is necessary in an industry where comfort and aesthetics are essential. Injection molds can be easily modified to suit different designs and specifications. This means manufacturers can quickly adapt to changing consumer preferences and market demands. Whether it’s new seat designs, color variations, or special features, injection molding provides the versatility needed to stay ahead in the competitive world of seating solutions.
Strength and durability
Plastic seats produced through injection molding are not only comfortable; They are also very durable. This process ensures that the plastic material is evenly distributed, giving the seat exceptional strength and durability. They are designed to stand the test of time and resist wear and tear even with heavy use. Because injection-molded chairs are known for their superior structural integrity, the even distribution of plastic material during molding eliminates weak points, ensuring the chair can support the user’s weight without the risk of breaking or deforming. This strength and durability are critical, especially in industries where safety and longevity are crucial.
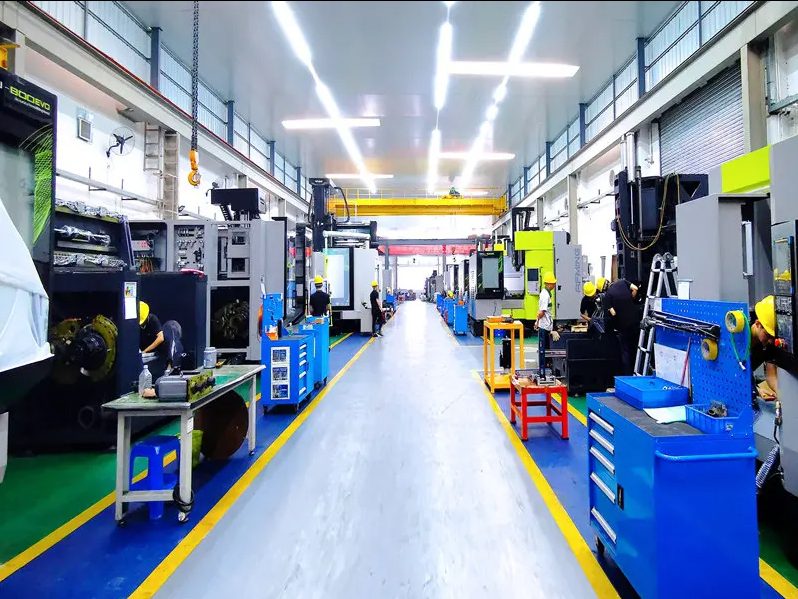
Cost-effective solutions for plastic seat production
In today’s depressed economy, cost-effective manufacturing is crucial. Injection molding offers a cost-effective solution for plastic seat production. Efficient use of materials and rapid production capabilities means manufacturers can deliver high-quality seats without breaking the bank. The cost savings associated with injection molding result from several factors. First, the process minimizes material waste by injecting the required amount of plastic into the mold, leaving little to no excess space. This efficiency translates into reduced material costs. Additionally, the speed of the injection molding machine means shorter production times, further reducing labor costs and increasing overall productivity.
Versatility meets creativity
Injection molds can be easily modified to suit different designs and specifications. This means manufacturers can quickly adapt to changing consumer preferences and market demands. Whether it’s new seat designs, color variations, or special features, injection molding provides the versatility needed to stay ahead in the highly competitive world of plastic seating production solutions. Additionally, this versatility extends to creating intricate patterns, textures, and even branding directly on the seats. Injection molding machines equipped with advanced technology can produce sophisticated and beautiful chairs.
The last point
For manufacturers who want to produce plastics, I believe this article will be helpful to you. From the perspective of an injection molding machine supplier, we tell you how simple and convenient it is to use the injection molding process. Its versatility makes it worth choosing. Because everyone wants to get good products, you might as well start with the injection molding process!
TRENDING POSTS
- What factors can cause delays in the injection molding process of plastic molding machine? 2023/09/20
- Exhibition Review| Topstar participates in InterPlas Thailand 2024 2023/09/20
- Star Case | Topstar helps Santong upgrade its intelligent plant 2023/09/20
- Topstar Special | National Science and Technology Workers Day 2023/09/20
HOT TOPIC
- 3 in 1 Compact Dehumidifying Dryer
- 5-axis CNC machine
- accuracy
- Air Chillers
- all electric injection molding machine
- all electric injection molding machines
- All-electric injection molding machines
- and overall production quality. Therefore
- AP-RubberPlas
- automated injection molding machine
- Automation changed engineering
- automation of injection molding robots
- auxiliary machine
- Bench Injection Molding Machine
- Cabinet dryer manufacturers
- Cabinet dryers
- chiller
- CNC Drilling Machine
- CNC Drilling Machines
- cnc engraving machine manufacturer
- cnc laser cutting machine manufacturer
- CNC machine
- CNC Machine Center
- CNC Machine for Sale
- CNC Machine Manufacturing
- CNC Machine Tool
- CNC machine tool product
- CNC Machining Center
- CNC wood carving machine
- Cooling system
- Cross-Walking Single Axis Servo Cylinder Robot
- Cross-Walking Single-Axis Servo Cylinder Robot
- Cross-Walking Three-Axis/Five-Axis Servo Driven Robot
- cross-walking three-axis/five-axis servo-driven robot
- Dehumidifier Dryer
- Dehumidifying Dryer
- delta parallel robot
- Desktop Injection Molding Machine
- Desktop injection molding machines
- Desktop Molding Machine
- desktop plastic injection machine
- Desktop Plastic Injection Molding Machine
- direct clamp injection molding machine
- Direct clamp injection molding machines
- Dosing & mixing system
- Drilling Centers
- Drying and dehumidification system
- drying and dehumidifying equipment
- Drying and Dehumidifying System
- drying system
- effective and efficient. Cabinet dryers are also used in other industries where large quantities of material need to be dried
- efficient injection molding machine
- elbow hydraulic injection molding machines
- electric injection molding machine
- electric injection molding machines
- energy-saving injection molding machine
- etc. Among injection molding robots
- exhibition
- features of CNC machine
- Feeding And Conveying System
- Five Axis Machine Center
- Fully automatic injection molding machine
- Gathering Topstar
- giant injection molding machine
- GMU-600 5-Axis Machining Center
- Granulating & Recycling System
- Heavy duty injection molding machine
- Honeycomb rotor dehumidifier
- horizontal injection molding machine
- Horizontal Injection Molding Machines
- Horizontal Injection Moulding Machine
- Horizontal Mixer manufacturer
- How The CNC Machine Works
- hybrid injection molding machine
- hydraulic injection molding machine
- Hydraulic Injection Molding Machines
- in this article
- Industrial robot
- Industrial Robot Chinese brand
- industrial robot parts
- industrial robot supplier
- Industrial robots
- Industry Chain
- Injection Manipulator
- injection mold machines
- Injection molding
- Injection molding automation
- Injection Molding Automation Solution
- injection molding dryer
- Injection molding equipment
- injection molding hopper dryer
- Injection molding machine
- injection molding machine brand
- Injection Molding Machine Factory
- Injection Molding Machine Manufacture
- Injection molding machine manufacturer
- injection molding machine manufacturers
- Injection molding machine procurement
- injection molding machine robotic arm
- injection molding machine with a robot
- Injection molding machines
- injection molding material dehumidifying
- injection molding plant
- Injection Molding Robot
- injection molding robot arm
- Injection molding robot automation
- Injection molding robotic arm
- injection molding robots
- Injection Moulding Robots
- Injection Robot
- Injection robot arm
- Injection robot manufacturer
- Injection robot wholesale
- injection robots
- intelligent injection molding machines
- Introducing Injection Robot
- It is the best choice for drying large quantities of material at once. Cabinetmakers use these machines because they are fast
- large injection molding machine
- Learn what industrial automation and robotics is
- linear robot
- low speed sound-proof granulator
- machine plastic molding
- make sure to add some! Improvements (2) Keyphrase in introduction: Your keyphrase or its synonyms appear in the first paragraph of the copy
- manipulator machine
- manufacturing
- micro injection molding machine
- middle speed granulator
- Mini CNC machine manufacturers.
- Mold Temperature Control System
- mold temperature controller
- molding material Dehumidifying System
- mould temperature controller
- mould temperature controllers
- New electric injection molding machine
- nitrogen dryer manufacturer
- nitrogen dryer system manufacturer
- Oil type mold temperature controller
- open day
- Outbound links: No outbound links appear in this page. Add some! Images: No images appear on this page. Add some! Internal links: No internal links appear in this page
- PET Preform injection molding
- phone case maker machine
- phone case making machine
- plastic bottle making machine
- plastic bottle manufacturing
- plastic bucket making machine
- plastic bucket manufacturing
- Plastic chair making machine
- plastic forming equipment
- plastic hopper dryer
- plastic injection machine
- plastic injection machines
- plastic injection molding
- Plastic injection molding equipment
- Plastic injection molding machine
- Plastic Injection Molding Machines
- plastic injection robot
- Plastic Molding machine
- Plastic Molding Machines
- plastic molding press
- plastic phone case making machine
- plastic-molding machine
- powerful granulator
- Powerful Type Sound-Proof Granulator
- production of plastic seats
- Robot injection molding
- robot injection molding machine
- robot manufacturing companies
- Robotic arm for injection molding machine
- robotic injection molding machines
- robotics in injection molding
- SCARA robot
- SCARA robots
- Service-oriented manufacturing
- Servo Cylinder Robot
- servo driven robot
- Servo Driven Robots
- servo injection robots
- Servo-Driven Robot
- Setup of injection machine
- Silicone Injection Molding Machine
- six-axis industrial robot
- Stainless Hopper Dryer
- Stainless Hopper Dryers
- star club
- swing arm robot
- the choice between servo-driven robots and hydraulic robots will have a certain impact on efficiency
- the most popular injection molding machine
- the type of injection molding robot
- toggle clamp injection molding machine
- Toggle Hydraulic Injection Molding Machines
- toggle injection molding machine
- Top 10 brands of injection robots
- Topstar
- Topstar Engineering
- Topstar Industrial Robots
- Topstar injection molding intelligent
- Topstar Scara Robots
- Useful Injection molding machine
- Vertical machining centers
- volumetric type blender
- water chiller
- water chillers
- water distributor
- Water Type MoldTemperature Controller
- We often face choices when performing injection molding. We will choose the type of injection molding machine
- wholesale of injection molding machines
- x carve CNC