Injection molding machines designed for the production of high-quality preforms
2024/07/24 By Topstar
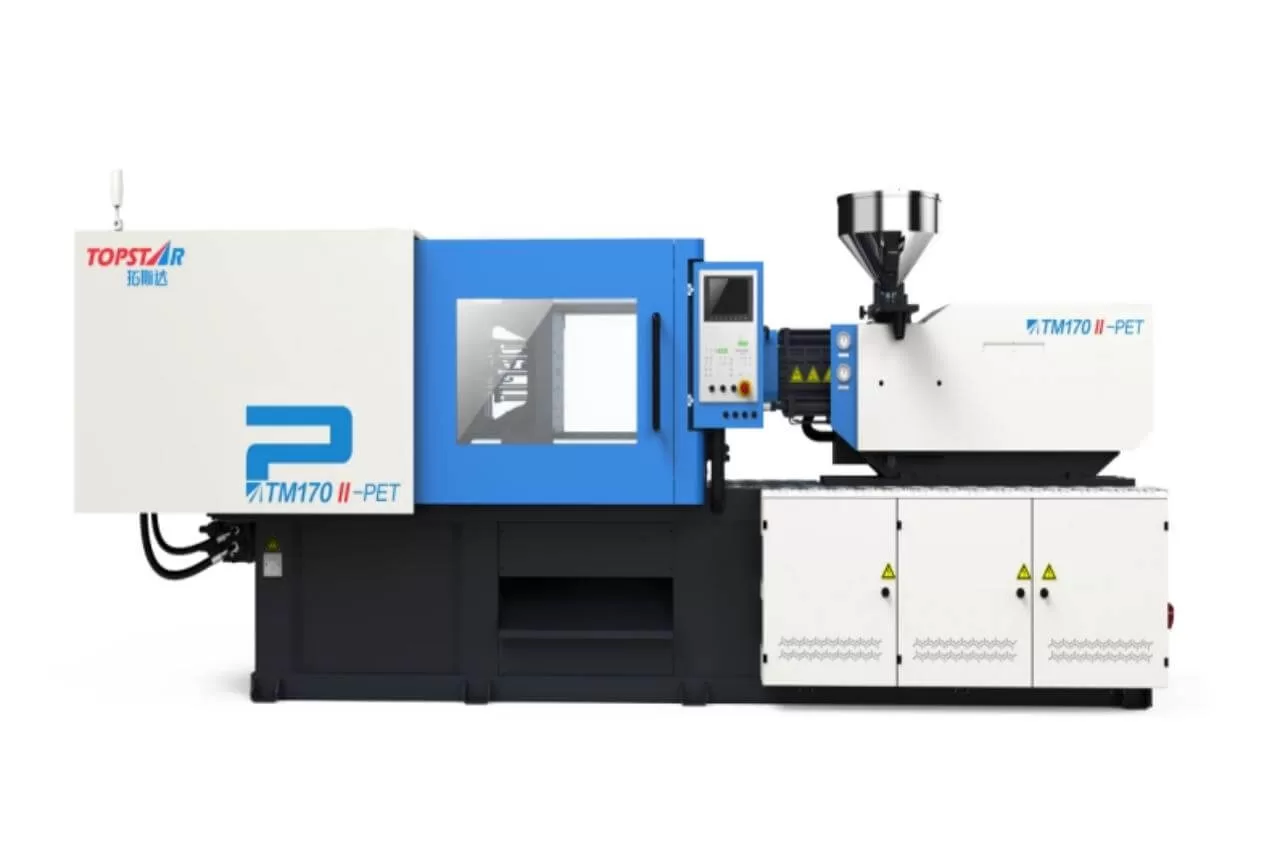
The entire injection molding market is facing constant updates and iterations to cater to the needs of different users. After extensive market testing, Topstar launched a new generation of preform injection molding machines – TMII-PET. In various plastic manufacturing industries, especially in producing plastic bottles and plastic containers, the quality of the preform is very important. The preform is an intermediate product that, after heating and blowing, becomes the final plastic container used in various industries. The preform injection molding machine is able to produce the highest quality preforms, ensuring their durability, transparency and overall product performance.
Preform injection molding machine uses a special screw combination for PET
Topstar preform injection molding machines using a special screw combination for PET. Unlike standard screws optimized for general plasticization, this dedicated PET screw configuration handles the unique properties of PET with careful design. Because PET has a high melting point and specific viscosity characteristics, it is very difficult to use traditional standard injection molding processes. The dedicated PET screw combination ensures optimal melting and homogenization of PET, reduces thermal degradation and improves the overall quality of the produced preforms. The use of a dedicated screw combination brings an improvement in plasticizing efficiency, which is more than 20% higher than that of traditional injection molding machines. Enhanced plasticizing efficiency not only speeds up the production process but also saves energy and reduces operating costs.
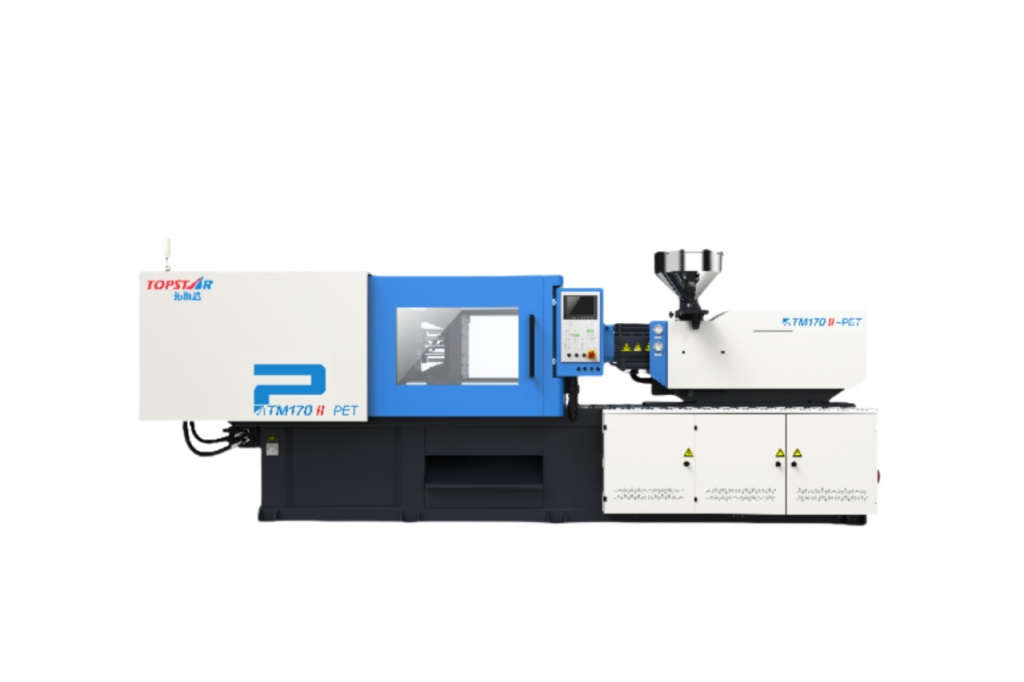
High rigidity reinforcement of the frame
The preform injection molding machine has high rigidity reinforcement on the frame. In preform injection molding, the dimensional accuracy and consistency of each preform are crucial. Any bending or vibration of the frame may cause defects and variations in the final product. The high rigidity frame ensures that the mold and injection unit remain perfectly aligned, thereby producing a uniform and high-quality preforms. The stability provided by the high-rigidity frame reduces the wear of mold components, extends mold life, reduces maintenance costs, and reduces the frequency of mold changes, thereby ensuring uninterrupted production and high-precision molding.
Enlarged hydraulic motor for preform injection molding machine
The outstanding advantage of an enlarged hydraulic motor is its low-speed stability. In injection molding, maintaining a stable and controlled speed during the injection and holding phases is the key to achieving high-quality results. Low-speed stability in preform injection molding machines allows precise control of the injection process, reducing the risk of defects such as flow marks, sink marks and voids. It ensures that the PET material is injected smoothly and evenly into the mold cavity, resulting in preforms with excellent dimensional accuracy and surface finish. The combination of high torque and low-speed stability not only improves the machine’s performance but also improves its overall efficiency and reliability. Enlarged hydraulic motors reduce cycle times without affecting the quality of the output.
Increased ejector force and ejector stroke
Ejector force is a critical parameter in injection molding, especially for PET preforms. PET products often have complex designs that require precise demoulding to avoid damage, which can produce a product with fewer defects and higher quality. In this regard, the preform injection molding machine’s increased ejector force ensures smooth and consistent ejection of the preform from the mold. This higher force is a good way to solve the preform and mold adhesion.
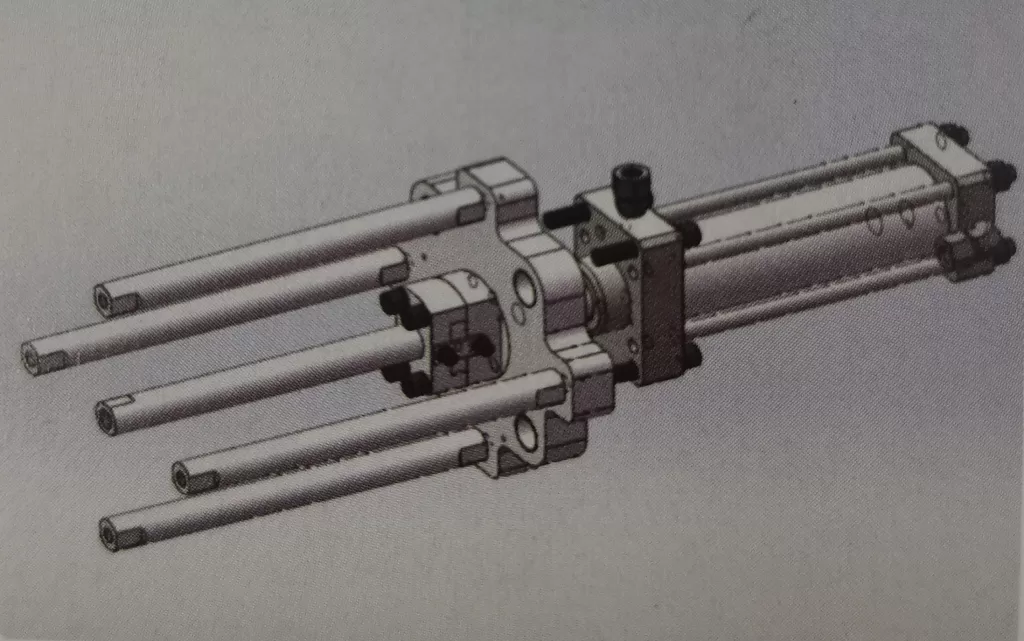
In addition to increased ejector force, Topstar’s preform injection molding machines also feature an extended ejector stroke. The ejector stroke is the distance the ejector system pushes the preform out of the mold. The increased ejector stroke is especially beneficial for complex PET preforms, which may have deeper cavities or require greater movement to eject from the mold fully. The extended ejector stroke can accommodate a wider variety of PET designs.
Suitable application areas
The most prominent application of preform injection molding machines is in the beverage industry, where they are used to make PET preforms for bottles. These preforms are subsequently blown into bottles for packaging water, carbonated drinks, juices and other beverages. In some pharmaceutical and healthcare fields, PET injection molding machines are used to produce PET containers and bottles for packaging medicines, syrups and other healthcare products. High cleanliness standards and precision make them ideal for these applications.
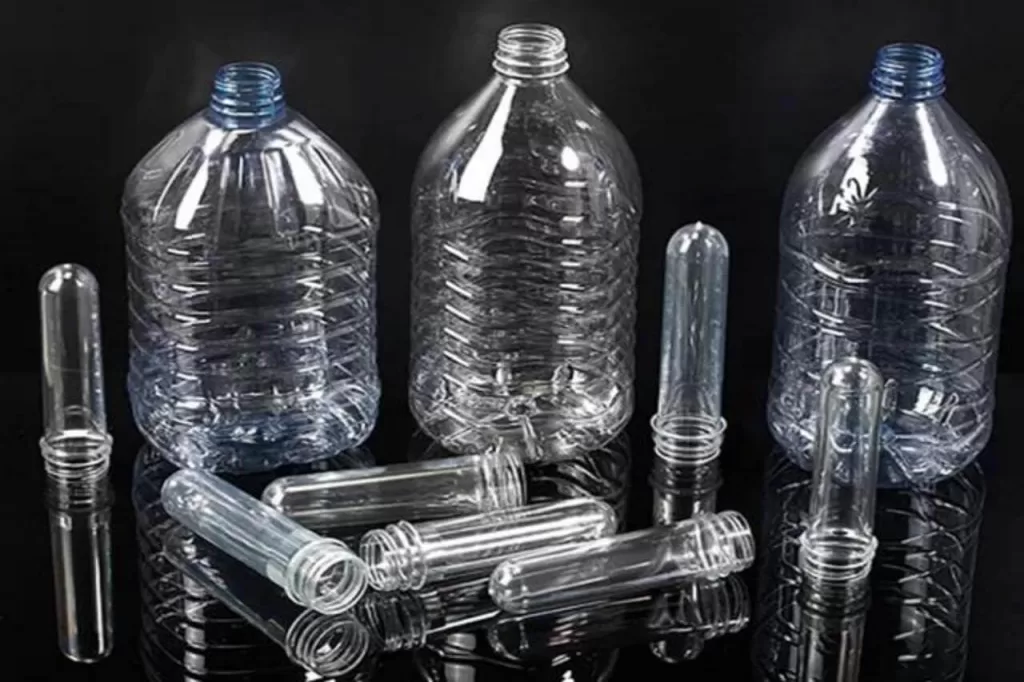
Produce high-quality preforms
The preform injection molding machine uses a special PET screw combination and a reinforced frame, which can ensure the production of stable, accurate and clean preforms. In addition, they can meet the needs of various industries while reducing production costs.
TRENDING POSTS
- What factors can cause delays in the injection molding process of plastic molding machine? 2024/07/24
- Exhibition Review| Topstar participates in InterPlas Thailand 2024 2024/07/24
- Star Case | Topstar helps Santong upgrade its intelligent plant 2024/07/24
- Topstar Special | National Science and Technology Workers Day 2024/07/24
HOT TOPIC
- .ervo motor-driven linear robots
- 3 axis robot
- 3 axis robots
- 3 in 1 Compact Dehumidifying Dryer
- 3-axis robot
- 3-axis robots
- 5-axis CNC machine
- accuracy
- Air Chillers
- all electric injection molding machine
- all electric injection molding machines
- All-electric injection molding machines
- and overall production quality. Therefore
- AP-RubberPlas
- automated injection molding machine
- Automation changed engineering
- automation of injection molding robots
- auxiliary machine
- Bench Injection Molding Machine
- Cabinet dryer manufacturers
- Cabinet dryers
- chiller
- CNC Drilling Machine
- CNC Drilling Machines
- cnc engraving machine manufacturer
- cnc laser cutting machine manufacturer
- CNC machine
- CNC Machine Center
- CNC Machine for Sale
- CNC Machine Manufacturing
- CNC Machine Tool
- CNC machine tool product
- CNC Machining Center
- CNC wood carving machine
- Cooling system
- Cross-Walking Single Axis Servo Cylinder Robot
- Cross-Walking Single-Axis Servo Cylinder Robot
- Cross-Walking Three-Axis/Five-Axis Servo Driven Robot
- cross-walking three-axis/five-axis servo-driven robot
- Dehumidifier Dryer
- Dehumidifying Dryer
- delta parallel robot
- Desktop Injection Molding Machine
- Desktop injection molding machines
- Desktop Molding Machine
- desktop plastic injection machine
- Desktop Plastic Injection Molding Machine
- direct clamp injection molding machine
- Direct clamp injection molding machines
- Dosing & mixing system
- Drilling Centers
- Drying and dehumidification system
- drying and dehumidifying equipment
- Drying and Dehumidifying System
- drying system
- effective and efficient. Cabinet dryers are also used in other industries where large quantities of material need to be dried
- efficient injection molding machine
- elbow hydraulic injection molding machines
- electric injection molding machine
- electric injection molding machines
- energy-efficient injection molding robot
- energy-saving injection molding machine
- etc. Among injection molding robots
- exhibition
- features of CNC machine
- Feeding And Conveying System
- Five Axis Machine Center
- Fully automatic injection molding machine
- Gathering Topstar
- giant injection molding machine
- GMU-600 5-Axis Machining Center
- Granulating & Recycling System
- Heavy duty injection molding machine
- High-precision electric molding machines
- high-precision plastic molding machines
- high-speed all electric injection molding machine
- Honeycomb rotor dehumidifier
- horizontal injection molding machine
- Horizontal Injection Molding Machines
- Horizontal Injection Moulding Machine
- Horizontal Mixer manufacturer
- How The CNC Machine Works
- hybrid injection molding machine
- hydraulic injection molding machine
- Hydraulic Injection Molding Machines
- in this article
- Industrial robot
- Industrial Robot Chinese brand
- industrial robot parts
- industrial robot supplier
- Industrial robots
- Industry Chain
- Injection Manipulator
- injection manipulator robot
- injection mold machines
- Injection molding
- Injection molding automation
- Injection Molding Automation Solution
- injection molding dryer
- Injection molding equipment
- injection molding hopper dryer
- Injection molding machine
- injection molding machine brand
- Injection Molding Machine Factory
- Injection Molding Machine Manufacture
- Injection molding machine manufacturer
- injection molding machine manufacturers
- Injection molding machine procurement
- injection molding machine robotic arm
- injection molding machine with a robot
- Injection molding machines
- injection molding material dehumidifying
- injection molding plant
- Injection Molding Robot
- injection molding robot arm
- Injection molding robot automation
- Injection molding robotic arm
- injection molding robots
- Injection moulding machine
- Injection Moulding Robots
- Injection Robot
- Injection robot arm
- Injection robot manufacturer
- Injection robot wholesale
- injection robots
- intelligent injection molding machines
- Introducing Injection Robot
- It is the best choice for drying large quantities of material at once. Cabinetmakers use these machines because they are fast
- large injection molding machine
- Learn what industrial automation and robotics is
- linear robot
- linear robots
- low speed sound-proof granulator
- machine plastic molding
- make sure to add some! Improvements (2) Keyphrase in introduction: Your keyphrase or its synonyms appear in the first paragraph of the copy
- manipulator machine
- manufacturing
- medical grade injection molding machines
- medical injection molding machine
- medical injection molding machines
- micro injection molding machine
- middle speed granulator
- Mini CNC machine manufacturers.
- Mold Temperature Control System
- mold temperature controller
- mold temperature controllers
- molding material Dehumidifying System
- mould temperature control system
- mould temperature controller
- mould temperature controllers
- New electric injection molding machine
- nitrogen dryer manufacturer
- nitrogen dryer system manufacturer
- Oil type mold temperature controller
- Oil type mold temperature controllers
- open day
- Outbound links: No outbound links appear in this page. Add some! Images: No images appear on this page. Add some! Internal links: No internal links appear in this page
- PET Preform injection molding
- phone case maker machine
- phone case making machine
- plastic bottle making machine
- plastic bottle manufacturing
- plastic bucket making machine
- plastic bucket manufacturing
- Plastic chair making machine
- plastic forming equipment
- plastic hopper dryer
- plastic injection machine
- plastic injection machines
- plastic injection molding
- Plastic injection molding equipment
- Plastic injection molding machine
- Plastic Injection Molding Machines
- plastic injection moulding machine
- plastic injection robot
- Plastic Molding machine
- Plastic Molding Machines
- plastic molding press
- plastic moulding machine
- plastic phone case making machine
- plastic-molding machine
- powerful granulator
- Powerful Type Sound-Proof Granulator
- precision injection molding
- precision injection molding machines
- production of plastic seats
- pure water mould temperature controller
- Robot injection molding
- robot injection molding machine
- robot manufacturing companies
- Robotic arm for injection molding machine
- robotic injection molding machines
- robotics in injection molding
- SCARA robot
- SCARA robots
- Service-oriented manufacturing
- Servo Cylinder Robot
- servo driven robot
- Servo Driven Robots
- servo injection robots
- servo motor-driven linear robots
- servo-driven 3-axis robot
- Servo-Driven Robot
- Setup of injection machine
- Silicone Injection Molding Machine
- six-axis industrial robot
- Stainless Hopper Dryer
- Stainless Hopper Dryers
- star club
- swing arm robot
- take-out robots
- the choice between servo-driven robots and hydraulic robots will have a certain impact on efficiency
- the most popular injection molding machine
- the type of injection molding robot
- toggle clamp injection molding machine
- Toggle Hydraulic Injection Molding Machines
- toggle injection molding machine
- Top 10 brands of injection robots
- Topstar
- Topstar Engineering
- Topstar Industrial Robots
- Topstar injection molding intelligent
- Topstar Scara Robots
- Useful Injection molding machine
- Vertical machining centers
- volumetric type blender
- water chiller
- water chillers
- water distributor
- water type mold temperature controller
- Water Type MoldTemperature Controller
- Water-Type Mould Temperature Controllers
- We often face choices when performing injection molding. We will choose the type of injection molding machine
- wholesale of injection molding machines
- x carve CNC