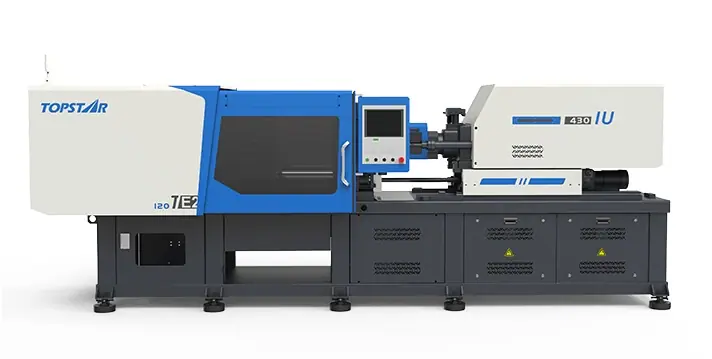
Injection molding machines enable various industries to produce high-quality plastic products in large quantities, so the failure rate of injection molding machines is critical. Suppose the injection molding machines you use have a high failure rate. In that case, they will frequently shut down and alarm during the production process, affecting the overall surrounding injection molding robots and auxiliary equipment and the overall production efficiency. Therefore, this article will introduce the characteristics and importance of an injection molding machine with a low failure rate.
The importance of low failure rates in injection molding
The low failure rate in injection molding can directly impact production efficiency. Since injection molding operates at high speed and is produced in large quantities, even minor failures will have a major chain reaction throughout the production process, resulting in extended product delivery. Time and so on. Therefore, reducing machine breakdowns can increase throughput and meet timely production targets.
In addition, maintaining a low failure rate in injection molding can also ensure product quality and consistency. Generally speaking, plastic product parts have strict size and surface finish requirements. High or inconsistent failure rates can lead to defects such as burrs, sink marks, warping, etc., compromising the integrity and functionality of the final product. By keeping failure rates low, manufacturers can achieve the highest quality control standards and reduce scrap and rework.
The main features of low failure rate injection molding machines
Injection molding machines with low failure rates will have several key features to improve reliability, efficiency, and productivity in the production process. The first item is to use highly stable and high-rigidity formwork to provide stable dynamic support and make the opening and closing of the mold more stable. The second item is to use extremely low injection speed and high-performance injection molding robot grabbing. The third item is the modular design, allowing them to adapt to various working conditions. The fourth item is that the simple operation interface can make maintenance easier. The most critical of these are the first three.
High-rigidity formwork features
The key feature of high-rigidity formwork is its strong structure, which is made of high-strength steel with high tensile strength, hardness, and wear resistance. Manufacturers can achieve the stiffness and stability needed for reliable and repeatable injection molding operations using high-quality materials and precision machining techniques. In addition, the design of the highly rigid formwork is optimized to effectively disperse and withstand the forces generated during the injection molding process. Their wide supporting feet provide stable dynamic support, making the opening and closing of the mold smoother while enhancing the rigidity and anti-deflection capabilities of the template, ensuring uniform pressure distribution throughout the mold cavity. It reduces the risk of premature wear or failure of critical components such as guide rails, clamping mechanisms, and ejection systems. Thereby reducing the failure rate of the injection molding machine.
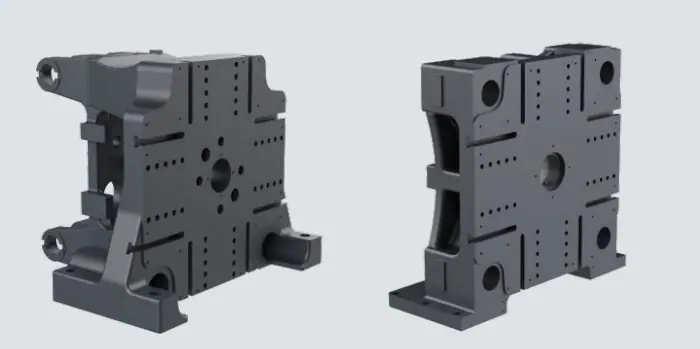
Features of extremely low injection speed
Extremely low injection speed is one of the important features to ensure a low failure rate of an injection molding machine. The extremely low injection speed ensures gentle and gradual filling of the mold cavity, reducing shear that may cause defects such as streamlines and burn marks in finished parts. Failure problems of shear force and pressure fluctuation. By operating at extremely low speeds, the injection molding machine reduces the shock and vibration associated with high-speed injection, reducing wear and fatigue on key components such as screws, barrels, and clamping systems, thereby reducing failure rates. Thereby reducing the failure rate of the injection molding machine.
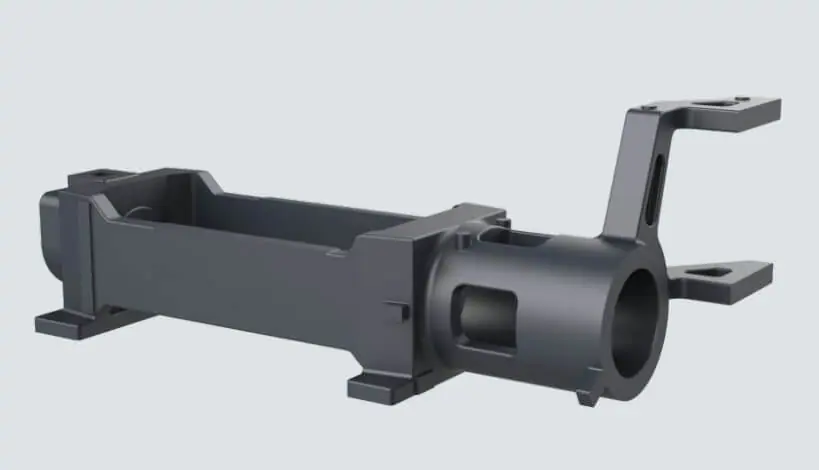
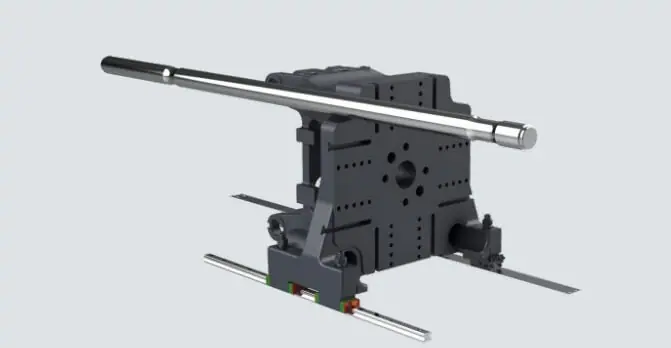
Features of modular design
The modular design can adapt the injection molding machine to various working conditions according to production requirements. Manufacturers can configure and customize the machine to meet specific needs by breaking down the machine into interchangeable modules or components. Additionally, the modular design is easy to assemble, install, and maintain, reducing downtime and minimizing disruption to production schedules. Standardized interfaces and connections between modules simplify the integration process, allowing for quick set-up and commissioning of the injection molding machine. Modular components can be easily accessed and replaced, making routine maintenance and repairs easier. Reduce the problem of failure due to mismatch between modules.
Keep your injection molding shop with a low failure rate
An injection molding machine with a low failure rate can bring great returns to plastic manufacturers. Reducing the failure rate a little can improve the efficiency of injection molding and bring substantial returns. As more and more manufacturers require reliable and high-performance equipment, investing in injection molding machines with low failure rates is a long-term success option for various industries.
TRENDING POSTS
- What factors can cause delays in the injection molding process of plastic molding machine? 2024/04/17
- Exhibition Review| Topstar participates in InterPlas Thailand 2024 2024/04/17
- Star Case | Topstar helps Santong upgrade its intelligent plant 2024/04/17
- Topstar Special | National Science and Technology Workers Day 2024/04/17
HOT TOPIC
- 3 in 1 Compact Dehumidifying Dryer
- 5-axis CNC machine
- accuracy
- Air Chillers
- all electric injection molding machine
- all electric injection molding machines
- All-electric injection molding machines
- and overall production quality. Therefore
- AP-RubberPlas
- automated injection molding machine
- Automation changed engineering
- automation of injection molding robots
- auxiliary machine
- Bench Injection Molding Machine
- Cabinet dryer manufacturers
- Cabinet dryers
- chiller
- CNC Drilling Machine
- CNC Drilling Machines
- cnc engraving machine manufacturer
- cnc laser cutting machine manufacturer
- CNC machine
- CNC Machine Center
- CNC Machine for Sale
- CNC Machine Manufacturing
- CNC Machine Tool
- CNC machine tool product
- CNC Machining Center
- CNC wood carving machine
- Cooling system
- Cross-Walking Single Axis Servo Cylinder Robot
- Cross-Walking Single-Axis Servo Cylinder Robot
- Cross-Walking Three-Axis/Five-Axis Servo Driven Robot
- cross-walking three-axis/five-axis servo-driven robot
- Dehumidifier Dryer
- Dehumidifying Dryer
- delta parallel robot
- Desktop Injection Molding Machine
- Desktop injection molding machines
- Desktop Molding Machine
- desktop plastic injection machine
- Desktop Plastic Injection Molding Machine
- direct clamp injection molding machine
- Direct clamp injection molding machines
- Dosing & mixing system
- Drilling Centers
- Drying and dehumidification system
- drying and dehumidifying equipment
- Drying and Dehumidifying System
- drying system
- effective and efficient. Cabinet dryers are also used in other industries where large quantities of material need to be dried
- efficient injection molding machine
- elbow hydraulic injection molding machines
- electric injection molding machine
- electric injection molding machines
- energy-saving injection molding machine
- etc. Among injection molding robots
- exhibition
- features of CNC machine
- Feeding And Conveying System
- Five Axis Machine Center
- Fully automatic injection molding machine
- Gathering Topstar
- giant injection molding machine
- GMU-600 5-Axis Machining Center
- Granulating & Recycling System
- Heavy duty injection molding machine
- Honeycomb rotor dehumidifier
- horizontal injection molding machine
- Horizontal Injection Molding Machines
- Horizontal Injection Moulding Machine
- Horizontal Mixer manufacturer
- How The CNC Machine Works
- hybrid injection molding machine
- hydraulic injection molding machine
- Hydraulic Injection Molding Machines
- in this article
- Industrial robot
- Industrial Robot Chinese brand
- industrial robot parts
- industrial robot supplier
- Industrial robots
- Industry Chain
- Injection Manipulator
- injection mold machines
- Injection molding
- Injection molding automation
- Injection Molding Automation Solution
- injection molding dryer
- Injection molding equipment
- injection molding hopper dryer
- Injection molding machine
- injection molding machine brand
- Injection Molding Machine Factory
- Injection Molding Machine Manufacture
- Injection molding machine manufacturer
- injection molding machine manufacturers
- Injection molding machine procurement
- injection molding machine robotic arm
- injection molding machine with a robot
- Injection molding machines
- injection molding material dehumidifying
- injection molding plant
- Injection Molding Robot
- injection molding robot arm
- Injection molding robot automation
- Injection molding robotic arm
- injection molding robots
- Injection Moulding Robots
- Injection Robot
- Injection robot arm
- Injection robot manufacturer
- Injection robot wholesale
- injection robots
- intelligent injection molding machines
- Introducing Injection Robot
- It is the best choice for drying large quantities of material at once. Cabinetmakers use these machines because they are fast
- large injection molding machine
- Learn what industrial automation and robotics is
- low speed sound-proof granulator
- machine plastic molding
- make sure to add some! Improvements (2) Keyphrase in introduction: Your keyphrase or its synonyms appear in the first paragraph of the copy
- manipulator machine
- manufacturing
- micro injection molding machine
- middle speed granulator
- Mini CNC machine manufacturers.
- Mold Temperature Control System
- mold temperature controller
- molding material Dehumidifying System
- mould temperature controller
- mould temperature controllers
- New electric injection molding machine
- nitrogen dryer manufacturer
- nitrogen dryer system manufacturer
- Oil type mold temperature controller
- open day
- Outbound links: No outbound links appear in this page. Add some! Images: No images appear on this page. Add some! Internal links: No internal links appear in this page
- PET Preform injection molding
- phone case maker machine
- phone case making machine
- plastic bottle making machine
- plastic bottle manufacturing
- plastic bucket making machine
- plastic bucket manufacturing
- Plastic chair making machine
- plastic forming equipment
- plastic hopper dryer
- plastic injection machine
- plastic injection machines
- plastic injection molding
- Plastic injection molding equipment
- Plastic injection molding machine
- Plastic Injection Molding Machines
- plastic injection robot
- Plastic Molding machine
- Plastic Molding Machines
- plastic molding press
- plastic phone case making machine
- plastic-molding machine
- powerful granulator
- Powerful Type Sound-Proof Granulator
- production of plastic seats
- Robot injection molding
- robot injection molding machine
- robot manufacturing companies
- Robotic arm for injection molding machine
- robotic injection molding machines
- robotics in injection molding
- SCARA robot
- SCARA robots
- Service-oriented manufacturing
- Servo Cylinder Robot
- servo driven robot
- Servo Driven Robots
- servo injection robots
- Servo-Driven Robot
- Setup of injection machine
- Silicone Injection Molding Machine
- six-axis industrial robot
- Stainless Hopper Dryer
- Stainless Hopper Dryers
- star club
- swing arm robot
- the choice between servo-driven robots and hydraulic robots will have a certain impact on efficiency
- the most popular injection molding machine
- the type of injection molding robot
- toggle clamp injection molding machine
- Toggle Hydraulic Injection Molding Machines
- toggle injection molding machine
- Top 10 brands of injection robots
- Topstar
- Topstar Engineering
- Topstar Industrial Robots
- Topstar injection molding intelligent
- Topstar Scara Robots
- Useful Injection molding machine
- Vertical machining centers
- volumetric type blender
- water chiller
- water chillers
- water distributor
- Water Type MoldTemperature Controller
- We often face choices when performing injection molding. We will choose the type of injection molding machine
- wholesale of injection molding machines
- x carve CNC