Injection Molding Machine: Ultimate Guide 2022
2022/03/01 By Topstar
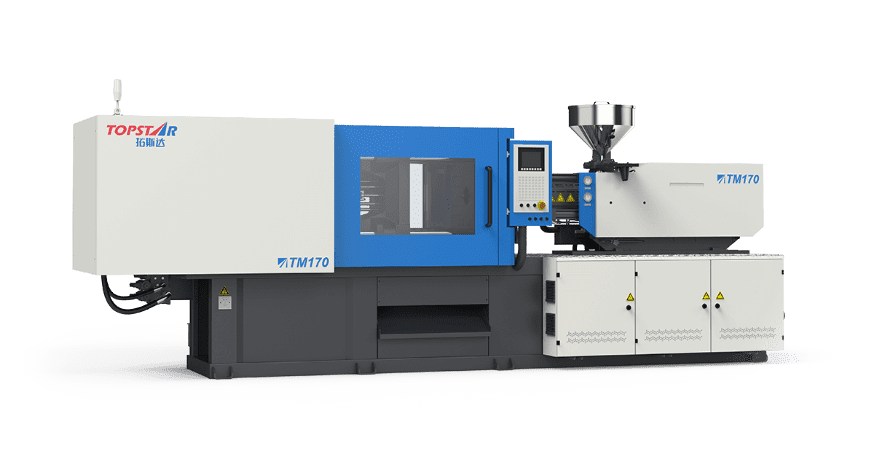
The injection molding machine is standard in injection molding machines for manufacturing three-dimensional parts of various configurations from plastic, metal, and rubber.
In the mold of an injection molding machine, one or more parts are easy to produce simultaneously. Moreover, it is common in mass or serial production.
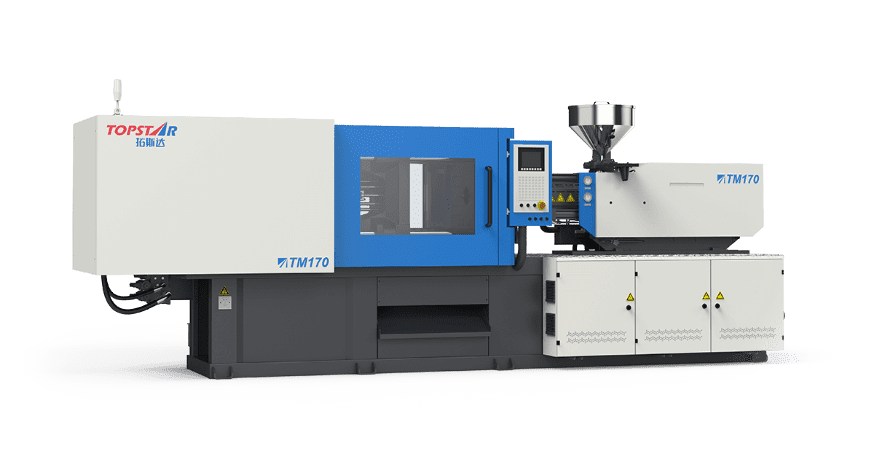
What is an injection mold?
Injection molds consist of fixed matrices and movable punches with a cavity inside for forming blanks. Moreover, the material is fed into the mold using gating systems: cold runner, hot runner, and combined. In some designs of forms, the installation of embedded details is possible.
Injection molding machine to create thin-walled products
Plastic injection molding is common to develop thin-walled products of various configurations. However, casting technology allows you to create reinforced and hollow parts, multi-colored and combining multiple polymeric materials.
The required pressure indicator is from 80 to 200 MPa. Furthermore, at lower pressures, cavities or underfills may form. Exceeding the values \u200b\u200b can lead to the formation of a flash.
Sand casting for simple or complex shapes in the injection molding machine
One of the most common types of casting of bulk billets. Moreover, it is common in automotive, machine tool building, and other industries. However, this injection molding machine is standard in mass production, small series or single items of simple or complex shape.
With such casting, products of low quality are obtained. Similarly, there may be voids and various foreign inclusions.
Moreover, casting in sand-clay molds is typical for manufacturing frames for the metalworking industry, body elements of machinery and equipment, various wheels, rings, and other bulky and heavy workpieces.
Casting in vacuum film injection molding machine
The technology is standard for casting any number of products weighing from one kilogram to ten tons, up to several meters in size.
Forms are made in the following order:
- A model kit is cut out of expanded polystyrene or other gas-tight materials;
- Moreover, a preheated synthetic film applies to the model;
Moreover, a vacuum device is created between the model kit and the film, tightly attracting the film to the model. A layer of chalk limestone clay (flask) is applied to the film, covered with dry sand and ram, and covered hermetically with a movie. However, air is removed from the flask using a vacuum device. The model set is released from the finished half-mold from the injection molding machine.
All parts are made and assembled into a single form
During the entire technological process, the constituent elements of the mold are under vacuum.
Molten metal pours into the assembled mold. After cooling the castings, the vacuum device turns off, as a result of which the sand is removed from the mold. The casting is easily removed from the mold.
Die casting from aluminum, non-ferrous, and ferrous metals
A chill mold is a metal multi-turn mold made of cast iron, aluminum, or steel. Moreover, die casting is suitable for manufacturing aluminum, non-ferrous, and ferrous metal products in injection molding machines.
The die-casting technology consists of several stages:
Furthermore, fixing metal half-forms, heating the working mold cavity to a temperature of about 180°C;
lubrication of the surface with a layer of protective refractory coating; pouring molten raw materials through sprues;
In addition, mold cooling, mold opening, and casting excavation. Moreover, Castings in a chill mold are of high quality and have geometric accuracy of dimensions.
Investment casting: does not require additional processing
The method of obtaining castings is to manufacture a model from low-melting compositions in molds. However, after drying, the hardened model removes the mold and is covered with several layers of suspension and a ceramic shell. The model inside the injection molding machine shell melts, creating a molded body with thin ceramic walls.
Moreover, after cooling, a molten mixture pours into the resulting mold, which forms a product that exactly repeats the model’s configuration. According to investment models, details are of high quality and surface cleanliness and do not require additional processing.
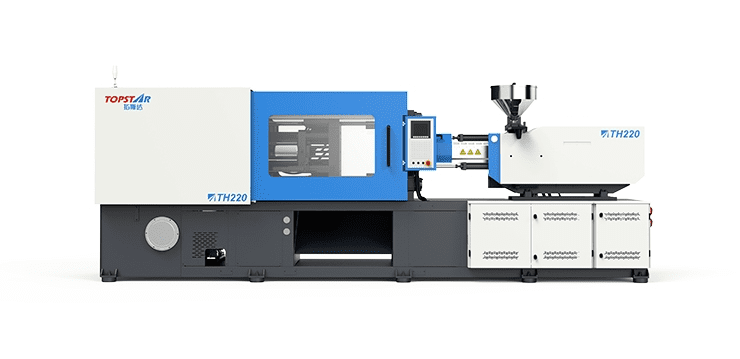
Casting on gasified models: polystyrene is most suitable
A method for producing cast products using models from materials that turn into gas upon contact with molten metal. Expanded polystyrene is ideal for this.
Models are made on an injection molding machine or by pouring polystyrene of small fractions under pressure into molds and then sintering at high temperatures. Moreover, model elements are glued or soldered into blocks, coated with a fire-resistant coating by pouring or dipping, and formed on a vibrating table into unique flasks.
- The molten metal is fed directly onto the model blocks, burning and gasifying the polystyrene.
- The finished castings more relaxed in the molds, then removed and cleaned of the non-stick coating.
- The casting technology for gasified patterns allows the production of products with smooth, precise shapes.
- Gases formed during the burning of polystyrene were removed with extractors.
Centrifugal casting for hollow cylindrical containers
It is typical for the manufacture of open cylindrical containers. Moreover, the injection molding machine is based on the principle of forming castings in the field of centrifugal forces. The molten metal from the ladle is fed through the filling funnel into a rotating cylinder, the inner side of which is the forming surface.
Shell casting for sequential operations
The technology is common to manufacture exact parts with high-quality requirements. Moreover, on automatic lines, shell molds are made from resin-sand mixture, thermosetting resins, quartz, or zircon sand.
Casting includes several sequential operations:
- Mixture preparation;
- Production of models in the form of thin-walled shells;
- Assembly and preparation of molds for pouring;
- Metal melting and pouring into finished molds;
- Cooling and extraction of castings;
- Cleaning and shot blasting
Injection molding machines are typical for manufacturing cast iron, steel, non-ferrous metals, and aluminum products. Cheaper devices with side or straight sprues and cold runner systems.
Technological shrinkage of the forming parts
Moreover, in manufacturing injection molds, it is necessary to consider the possible technological shrinkage of the forming parts during the cooling process.
Shrinkage may depend on the following factors:
- The type of materials common for the manufacture of molds;
- The presence of reinforcing fibers;
- Sprue type and size;
- Uniformity of temperature distribution;
- Design features of forms.
Adding reinforcing fibers to the raw material will help reduce shrinkage phenomena.
Development of Injection mold design
Moreover, the development of the project of an injection molding machine is carried out based on the customer’s technical specifications. The necessary calculations are performed, a 3D model of the future product is created, and working drawings are made.
TRENDING POSTS
- What factors can cause delays in the injection molding process of plastic molding machine? 2022/03/01
- Exhibition Review| Topstar participates in InterPlas Thailand 2024 2022/03/01
- Star Case | Topstar helps Santong upgrade its intelligent plant 2022/03/01
- Topstar Special | National Science and Technology Workers Day 2022/03/01
HOT TOPIC
- 3 in 1 Compact Dehumidifying Dryer
- 5-axis CNC machine
- accuracy
- Air Chillers
- all electric injection molding machine
- All-electric injection molding machines
- and overall production quality. Therefore
- AP-RubberPlas
- automated injection molding machine
- Automation changed engineering
- automation of injection molding robots
- auxiliary machine
- Bench Injection Molding Machine
- Cabinet dryer manufacturers
- Cabinet dryers
- chiller
- CNC Drilling Machine
- CNC Drilling Machines
- cnc engraving machine manufacturer
- cnc laser cutting machine manufacturer
- CNC machine
- CNC Machine Center
- CNC Machine for Sale
- CNC Machine Manufacturing
- CNC Machine Tool
- CNC machine tool product
- CNC Machining Center
- CNC wood carving machine
- Cooling system
- Cross-Walking Single Axis Servo Cylinder Robot
- Cross-Walking Single-Axis Servo Cylinder Robot
- Cross-Walking Three-Axis/Five-Axis Servo Driven Robot
- cross-walking three-axis/five-axis servo-driven robot
- Dehumidifier Dryer
- Dehumidifying Dryer
- delta parallel robot
- Desktop Injection Molding Machine
- Desktop injection molding machines
- Desktop Molding Machine
- desktop plastic injection machine
- Desktop Plastic Injection Molding Machine
- direct clamp injection molding machine
- Direct clamp injection molding machines
- Dosing & mixing system
- Drilling Centers
- Drying and dehumidification system
- drying and dehumidifying equipment
- Drying and Dehumidifying System
- drying system
- effective and efficient. Cabinet dryers are also used in other industries where large quantities of material need to be dried
- efficient injection molding machine
- elbow hydraulic injection molding machines
- electric injection molding machine
- electric injection molding machines
- etc. Among injection molding robots
- exhibition
- features of CNC machine
- Feeding And Conveying System
- Five Axis Machine Center
- Fully automatic injection molding machine
- Gathering Topstar
- giant injection molding machine
- GMU-600 5-Axis Machining Center
- Granulating & Recycling System
- Heavy duty injection molding machine
- Honeycomb rotor dehumidifier
- horizontal injection molding machine
- Horizontal Injection Molding Machines
- Horizontal Injection Moulding Machine
- Horizontal Mixer manufacturer
- How The CNC Machine Works
- hybrid injection molding machine
- hydraulic injection molding machine
- Hydraulic Injection Molding Machines
- in this article
- Industrial robot
- Industrial Robot Chinese brand
- industrial robot parts
- industrial robot supplier
- Industrial robots
- Industry Chain
- Injection Manipulator
- injection mold machines
- Injection molding
- Injection molding automation
- Injection Molding Automation Solution
- injection molding dryer
- Injection molding equipment
- injection molding hopper dryer
- Injection molding machine
- injection molding machine brand
- Injection Molding Machine Factory
- Injection Molding Machine Manufacture
- Injection molding machine manufacturer
- injection molding machine manufacturers
- Injection molding machine procurement
- injection molding machine robotic arm
- injection molding machine with a robot
- Injection molding machines
- injection molding material dehumidifying
- injection molding plant
- Injection Molding Robot
- injection molding robot arm
- Injection molding robot automation
- Injection molding robotic arm
- injection molding robots
- Injection Moulding Robots
- Injection Robot
- Injection robot arm
- Injection robot manufacturer
- Injection robot wholesale
- injection robots
- intelligent injection molding machines
- Introducing Injection Robot
- It is the best choice for drying large quantities of material at once. Cabinetmakers use these machines because they are fast
- large injection molding machine
- Learn what industrial automation and robotics is
- low speed sound-proof granulator
- machine plastic molding
- make sure to add some! Improvements (2) Keyphrase in introduction: Your keyphrase or its synonyms appear in the first paragraph of the copy
- manipulator machine
- manufacturing
- micro injection molding machine
- middle speed granulator
- Mini CNC machine manufacturers.
- Mold Temperature Control System
- mold temperature controller
- molding material Dehumidifying System
- mould temperature controller
- mould temperature controllers
- New electric injection molding machine
- nitrogen dryer manufacturer
- nitrogen dryer system manufacturer
- Oil type mold temperature controller
- open day
- Outbound links: No outbound links appear in this page. Add some! Images: No images appear on this page. Add some! Internal links: No internal links appear in this page
- PET Preform injection molding
- phone case maker machine
- phone case making machine
- plastic bottle making machine
- plastic bottle manufacturing
- plastic bucket making machine
- plastic bucket manufacturing
- Plastic chair making machine
- plastic forming equipment
- plastic hopper dryer
- plastic injection machine
- plastic injection machines
- plastic injection molding
- Plastic injection molding equipment
- Plastic injection molding machine
- Plastic Injection Molding Machines
- plastic injection robot
- Plastic Molding machine
- Plastic Molding Machines
- plastic molding press
- plastic phone case making machine
- plastic-molding machine
- powerful granulator
- Powerful Type Sound-Proof Granulator
- production of plastic seats
- Robot injection molding
- robot injection molding machine
- robot manufacturing companies
- Robotic arm for injection molding machine
- robotic injection molding machines
- robotics in injection molding
- SCARA robot
- SCARA robots
- Service-oriented manufacturing
- Servo Cylinder Robot
- servo driven robot
- Servo Driven Robots
- servo injection robots
- Servo-Driven Robot
- Setup of injection machine
- Silicone Injection Molding Machine
- six-axis industrial robot
- Stainless Hopper Dryer
- Stainless Hopper Dryers
- star club
- swing arm robot
- the choice between servo-driven robots and hydraulic robots will have a certain impact on efficiency
- the most popular injection molding machine
- the type of injection molding robot
- toggle clamp injection molding machine
- Toggle Hydraulic Injection Molding Machines
- toggle injection molding machine
- Top 10 brands of injection robots
- Topstar
- Topstar Engineering
- Topstar Industrial Robots
- Topstar injection molding intelligent
- Topstar Scara Robots
- Useful Injection molding machine
- Vertical machining centers
- volumetric type blender
- water chiller
- water chillers
- water distributor
- Water Type MoldTemperature Controller
- We often face choices when performing injection molding. We will choose the type of injection molding machine
- wholesale of injection molding machines
- x carve CNC