Injection Molding Machine: 4 Major Features
2021/12/16 By Topstar
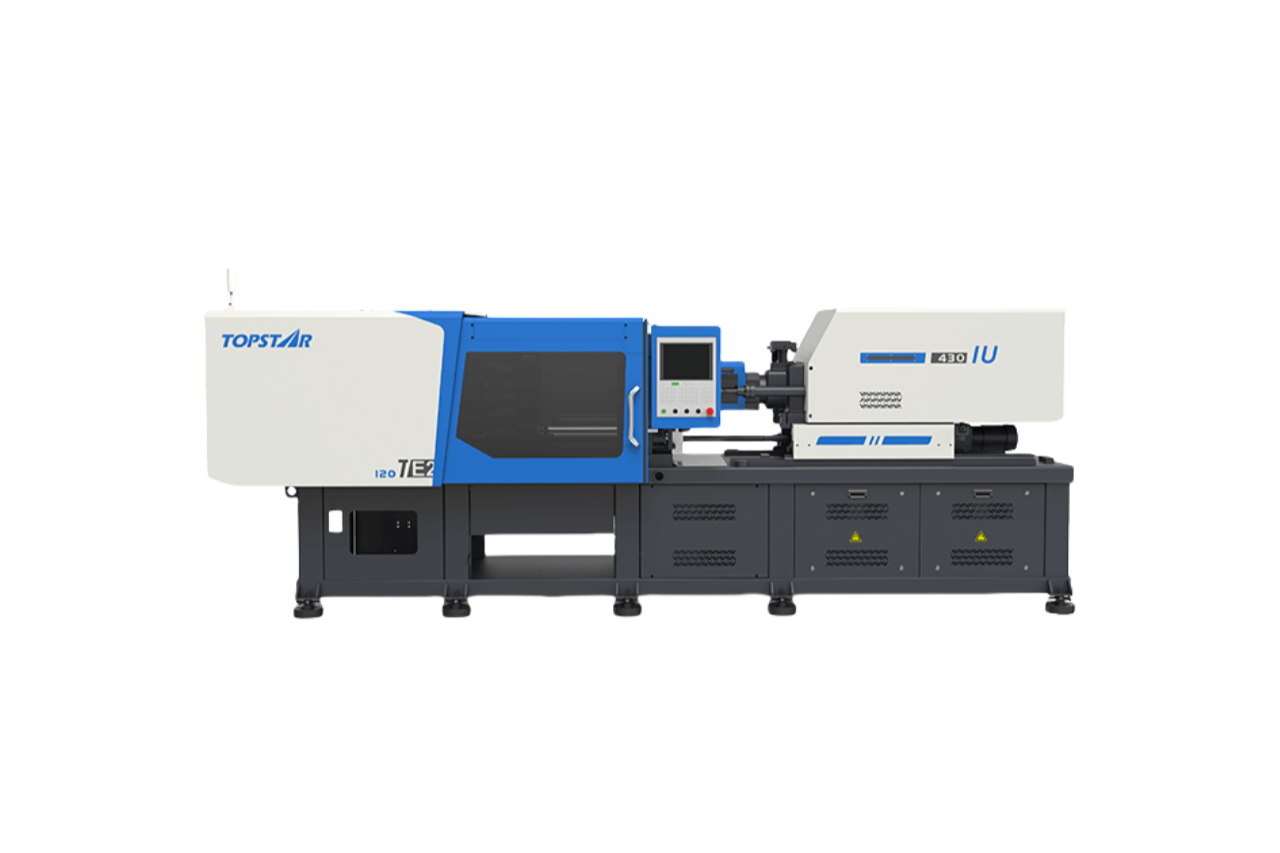
Injection molding machines enable manufacturers to produce a wide range of products with complex designs and high precision. As technology advances, injection molding machines evolve and incorporate new features to improve performance, reduce operating costs, and enhance product quality. In this article, we will share with you the four significant features of injection molding machines that make injection molding machines indispensable in today’s manufacturing environment. These features are non-contact tie rods, lubrication-free tie rod mechanisms, low-damping injection units for precise metering, and high-rigidity, low-friction mechanical structures. Each component ensures that the injection molding machine operates efficiently, accurately, and cost-effectively.
Injection molding machine: non-contact tie rods for improved precision
One of the outstanding features of modern injection molding machines is the non-contact tie rods. Traditional injection molding machines often rely on mechanical tie rods to connect different machine parts. Still, over time, these parts will wear out, reducing the efficiency and precision of the machine. However, non-contact tie rods eliminate this problem using a design that does not require physical contact between the tie rod and other parts. Using non-contact tie rods ensures less friction between moving parts, reducing wear and tear on the machine. At the same time, it also makes the movement of the injection unit smoother and more precise, thereby improving the overall accuracy of the molding process. By reducing the effects of friction and wear, non-contact tie rods increase the machine’s durability and help maintain high precision.
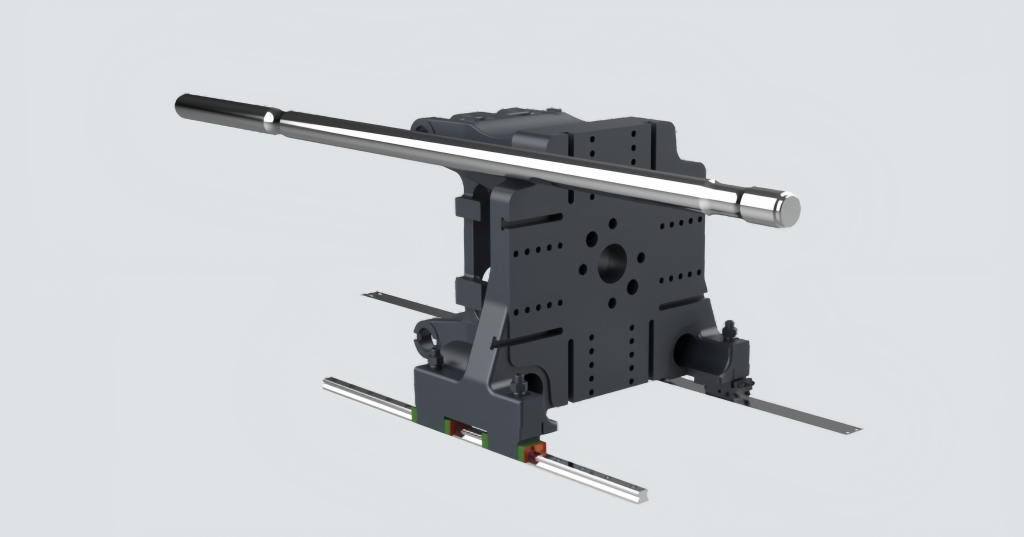
Injection molding machine: lubrication-free tie rod mechanism
The tie rod in the injection molding machine is essential to its operation because it helps stabilize and support the moving parts during the molding process. The tie rod must be lubricated regularly to ensure smooth operation and prevent excessive friction. However, modern injection molding machines have adopted a lubrication-free tie rod mechanism that does not require constant lubrication while maintaining optimal performance. This feature can significantly reduce maintenance time and costs because there is no need to check or change lubricants regularly. In addition, the lubrication-free design prevents contaminants from entering the molding process, ensuring cleaner production and higher-quality products. By reducing the reliance on lubricants, manufacturers can reduce operating costs and improve the overall efficiency of the production process. In addition, they are particularly beneficial in cleanroom environments.
Low-damping injection unit for precise metering
Precision is crucial in injection molding because the success of the molding process often depends on the exact amount of material injected into the mold. Injection molding machines with low-damping injection units have significant advantages in this regard. Low-damping injection units are designed to provide consistent and precise material metering, essential for producing high-quality products with tight tolerances. The damping characteristics of the injection unit affect the speed and accuracy of the injection process. High damping can cause injection rate fluctuations, leading to inconsistent part quality and increased scrap rates. By incorporating low-damping injection units, modern machines ensure that material is injected at a steady, controlled rate, reducing the likelihood of defects such as inconsistent wall thickness or flow marks.
High-rigidity, low-friction mechanical structure
The mechanical structure of an injection molding machine plays a vital role in its overall performance. A high-rigidity, low-friction mechanical structure ensures that the machine can withstand the stress of the molding process while maintaining accuracy. The frame’s rigidity prevents deflection during operation, ensuring that the mold remains perfectly aligned throughout the injection cycle. This alignment is essential to achieving accurate and consistent part quality.
The low-friction design of the mechanical structure also reduces wear on moving parts, extending the life of the injection molding machine and reducing maintenance costs. The combination of high rigidity and low friction allows modern injection molding machines to produce high-precision parts with minimal distortion or variation. This feature is particularly beneficial in applications that require fine details or tight tolerances, such as in the automotive or aerospace industries, where precision is critical to product performance and safety.
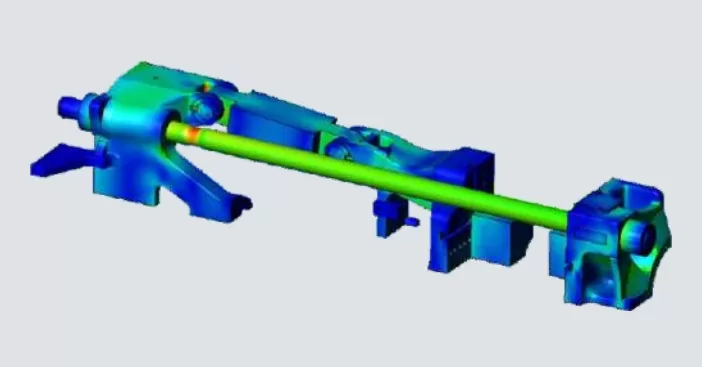
Servo self-driven motors for stable operation
Servo self-driven motors enable extremely low and stable operating speeds. This motor technology eliminates the need for traditional hydraulic systems, which are often inefficient and unstable. Servo motors operate with high precision and can operate smoothly and stably even at low speeds.
This feature improves the machine’s overall energy efficiency and helps achieve more consistent molding results. The precise control of the servo motor ensures that the injection process is carried out with minimal fluctuations, which is essential for eliminating product flow marks and achieving a high level of surface finish. In addition, the reduced operating speed helps minimize noise and vibration, making the injection molding machine more comfortable to operate and less prone to mechanical wear.
Maximize efficiency with these features.
From non-contact tie rods and lubrication-free systems to low-damping injection units and servo motors, these features improve the machine’s overall performance, resulting in improved energy efficiency, reduced maintenance costs, and improved product quality. Investing in an injection molding machine with these advanced features can provide a significant competitive advantage.
TRENDING POSTS
- What factors can cause delays in the injection molding process of plastic molding machine? 2021/12/16
- Exhibition Review| Topstar participates in InterPlas Thailand 2024 2021/12/16
- Star Case | Topstar helps Santong upgrade its intelligent plant 2021/12/16
- Topstar Special | National Science and Technology Workers Day 2021/12/16
HOT TOPIC
- 3 in 1 Compact Dehumidifying Dryer
- 5-axis CNC machine
- accuracy
- Air Chillers
- all electric injection molding machine
- All-electric injection molding machines
- and overall production quality. Therefore
- AP-RubberPlas
- automated injection molding machine
- Automation changed engineering
- automation of injection molding robots
- auxiliary machine
- Bench Injection Molding Machine
- Cabinet dryer manufacturers
- Cabinet dryers
- chiller
- CNC Drilling Machine
- CNC Drilling Machines
- cnc engraving machine manufacturer
- cnc laser cutting machine manufacturer
- CNC machine
- CNC Machine Center
- CNC Machine for Sale
- CNC Machine Manufacturing
- CNC Machine Tool
- CNC machine tool product
- CNC Machining Center
- CNC wood carving machine
- Cooling system
- Cross-Walking Single Axis Servo Cylinder Robot
- Cross-Walking Single-Axis Servo Cylinder Robot
- Cross-Walking Three-Axis/Five-Axis Servo Driven Robot
- cross-walking three-axis/five-axis servo-driven robot
- Dehumidifier Dryer
- Dehumidifying Dryer
- delta parallel robot
- Desktop Injection Molding Machine
- Desktop injection molding machines
- Desktop Molding Machine
- desktop plastic injection machine
- Desktop Plastic Injection Molding Machine
- direct clamp injection molding machine
- Direct clamp injection molding machines
- Dosing & mixing system
- Drilling Centers
- Drying and dehumidification system
- drying and dehumidifying equipment
- Drying and Dehumidifying System
- drying system
- effective and efficient. Cabinet dryers are also used in other industries where large quantities of material need to be dried
- efficient injection molding machine
- elbow hydraulic injection molding machines
- electric injection molding machine
- electric injection molding machines
- etc. Among injection molding robots
- exhibition
- features of CNC machine
- Feeding And Conveying System
- Five Axis Machine Center
- Fully automatic injection molding machine
- Gathering Topstar
- giant injection molding machine
- GMU-600 5-Axis Machining Center
- Granulating & Recycling System
- Heavy duty injection molding machine
- Honeycomb rotor dehumidifier
- horizontal injection molding machine
- Horizontal Injection Molding Machines
- Horizontal Injection Moulding Machine
- Horizontal Mixer manufacturer
- How The CNC Machine Works
- hybrid injection molding machine
- hydraulic injection molding machine
- Hydraulic Injection Molding Machines
- in this article
- Industrial robot
- Industrial Robot Chinese brand
- industrial robot parts
- industrial robot supplier
- Industrial robots
- Industry Chain
- Injection Manipulator
- injection mold machines
- Injection molding
- Injection molding automation
- Injection Molding Automation Solution
- injection molding dryer
- Injection molding equipment
- injection molding hopper dryer
- Injection molding machine
- injection molding machine brand
- Injection Molding Machine Factory
- Injection Molding Machine Manufacture
- Injection molding machine manufacturer
- injection molding machine manufacturers
- Injection molding machine procurement
- injection molding machine robotic arm
- injection molding machine with a robot
- Injection molding machines
- injection molding material dehumidifying
- injection molding plant
- Injection Molding Robot
- injection molding robot arm
- Injection molding robot automation
- Injection molding robotic arm
- injection molding robots
- Injection Moulding Robots
- Injection Robot
- Injection robot arm
- Injection robot manufacturer
- Injection robot wholesale
- injection robots
- intelligent injection molding machines
- Introducing Injection Robot
- It is the best choice for drying large quantities of material at once. Cabinetmakers use these machines because they are fast
- large injection molding machine
- Learn what industrial automation and robotics is
- low speed sound-proof granulator
- machine plastic molding
- make sure to add some! Improvements (2) Keyphrase in introduction: Your keyphrase or its synonyms appear in the first paragraph of the copy
- manipulator machine
- manufacturing
- micro injection molding machine
- middle speed granulator
- Mini CNC machine manufacturers.
- Mold Temperature Control System
- mold temperature controller
- molding material Dehumidifying System
- mould temperature controller
- mould temperature controllers
- New electric injection molding machine
- nitrogen dryer manufacturer
- nitrogen dryer system manufacturer
- Oil type mold temperature controller
- open day
- Outbound links: No outbound links appear in this page. Add some! Images: No images appear on this page. Add some! Internal links: No internal links appear in this page
- PET Preform injection molding
- phone case maker machine
- phone case making machine
- plastic bottle making machine
- plastic bottle manufacturing
- plastic bucket making machine
- plastic bucket manufacturing
- Plastic chair making machine
- plastic forming equipment
- plastic hopper dryer
- plastic injection machine
- plastic injection machines
- plastic injection molding
- Plastic injection molding equipment
- Plastic injection molding machine
- Plastic Injection Molding Machines
- plastic injection robot
- Plastic Molding machine
- Plastic Molding Machines
- plastic molding press
- plastic phone case making machine
- plastic-molding machine
- powerful granulator
- Powerful Type Sound-Proof Granulator
- production of plastic seats
- Robot injection molding
- robot injection molding machine
- robot manufacturing companies
- Robotic arm for injection molding machine
- robotic injection molding machines
- robotics in injection molding
- SCARA robot
- SCARA robots
- Service-oriented manufacturing
- Servo Cylinder Robot
- servo driven robot
- Servo Driven Robots
- servo injection robots
- Servo-Driven Robot
- Setup of injection machine
- Silicone Injection Molding Machine
- six-axis industrial robot
- Stainless Hopper Dryer
- Stainless Hopper Dryers
- star club
- swing arm robot
- the choice between servo-driven robots and hydraulic robots will have a certain impact on efficiency
- the most popular injection molding machine
- the type of injection molding robot
- toggle clamp injection molding machine
- Toggle Hydraulic Injection Molding Machines
- toggle injection molding machine
- Top 10 brands of injection robots
- Topstar
- Topstar Engineering
- Topstar Industrial Robots
- Topstar injection molding intelligent
- Topstar Scara Robots
- Useful Injection molding machine
- Vertical machining centers
- volumetric type blender
- water chiller
- water chillers
- water distributor
- Water Type MoldTemperature Controller
- We often face choices when performing injection molding. We will choose the type of injection molding machine
- wholesale of injection molding machines
- x carve CNC