Injection molding equipment for mass manufacturing
2024/05/17 By Topstar
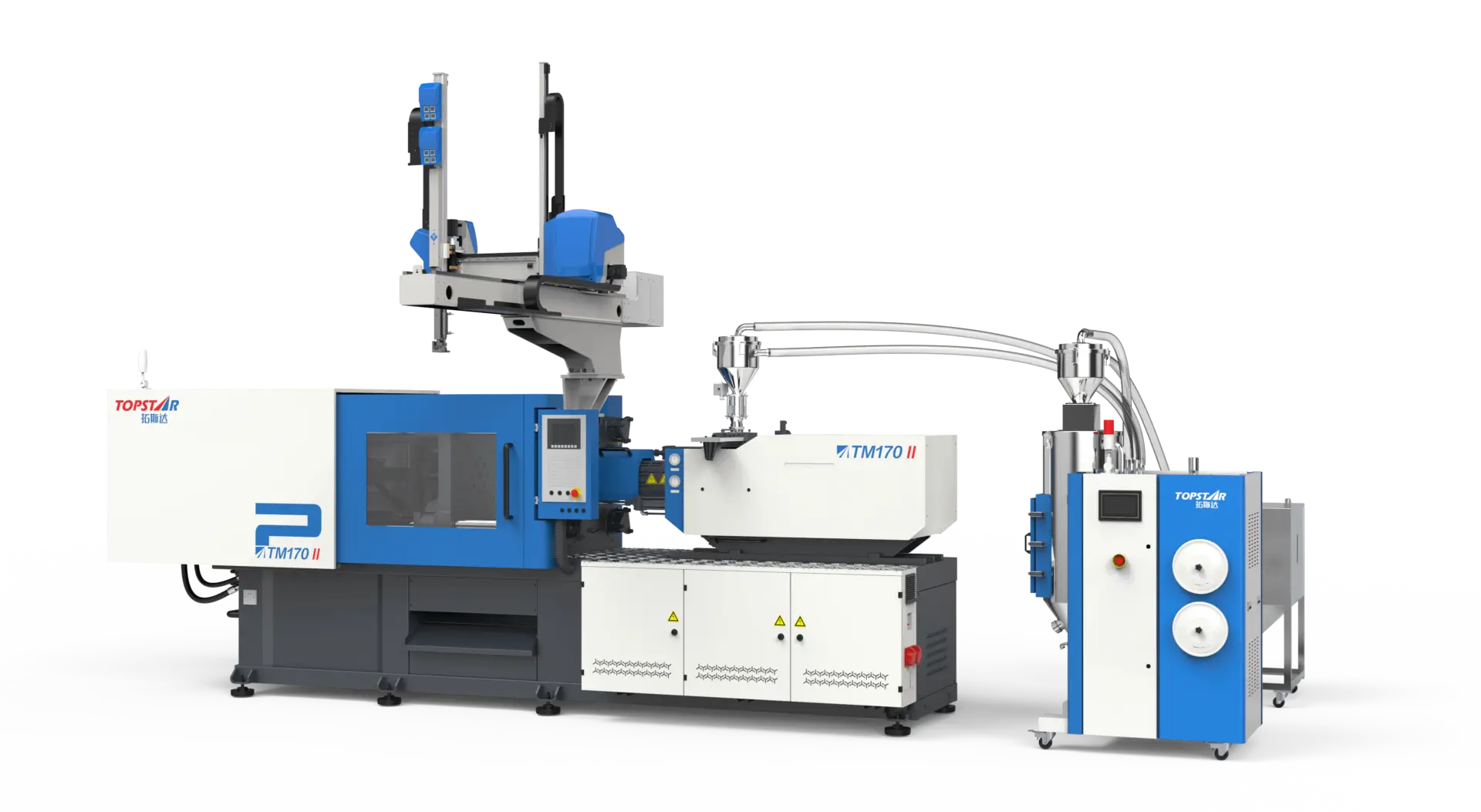
In the field of plastic parts manufacturing, it is very important to have a complete set of injection molding equipment. This equipment ensures the efficiency of the entire production line in the face of mass production. As demand rises in various industries, these injection molding equipment have gradually become the cornerstone of mass production. This guide will look in-depth at what injection molding equipment is used for high-volume manufacturing.
The most important role of injection molding machines in mass production
The injection molding machine is the core of injection molding equipment and plays a core injection molding role in mass production and manufacturing. They are indispensable for a variety of plastic products in various industries.
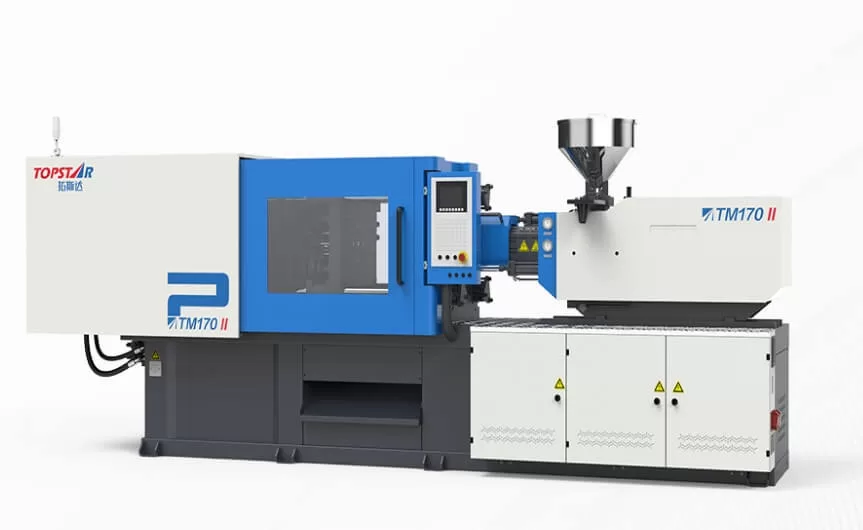
Injection molding machines utilize control and automation systems to precisely control every aspect of the injection molding process, including injection speed, pressure, temperature, and cooling time. This ensures that every part produced is consistent in quality, size, and surface finish. At the same time, they can produce large quantities of parts quickly, which is most needed in mass-production applications. Features such as fast cycle times and multiple cavities allow them to produce large numbers of parts per hour. Their three different series allow them to adapt to various plastic materials and part geometries.
The role of injection molding robots in mass production
An injection molding robot is also one type of injection molding equipment. In large-scale production, it is mainly integrated with the injection molding machine to grab, pick, and place plastic items during the injection molding process. After the plastic part is formed, an injection molding robot is mounted on the machine, and a robotic arm is used to remove the material from the mold cavity and transfer it to downstream processes, such as assembly or packaging. This automation eliminates the need for manual intervention, reduces cycle time, and increases throughput. Injection molding robots handle parts with greater precision and consistency than manual labor. They can pick and place parts with millimeter accuracy, ensuring consistent part placement and orientation.
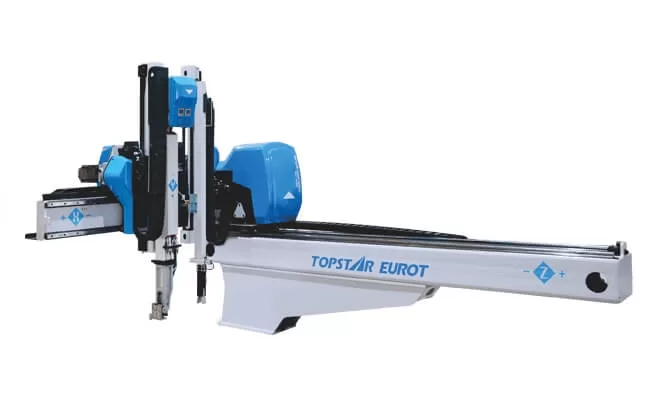
Auxiliary equipment
Auxiliary equipment is also one type of injection molding equipment. In large-scale injection molding production, these auxiliary equipment can work together with the injection molding machine to optimize all aspects of the production workflow.
Auxiliary equipment handles and prepares raw materials used in the injection molding process. This includes material dryers, material conveyors, and material loaders. Material drying systems remove moisture from hygroscopic resins to prevent defects in molded parts, while conveyors and loaders ensure the transport of materials.
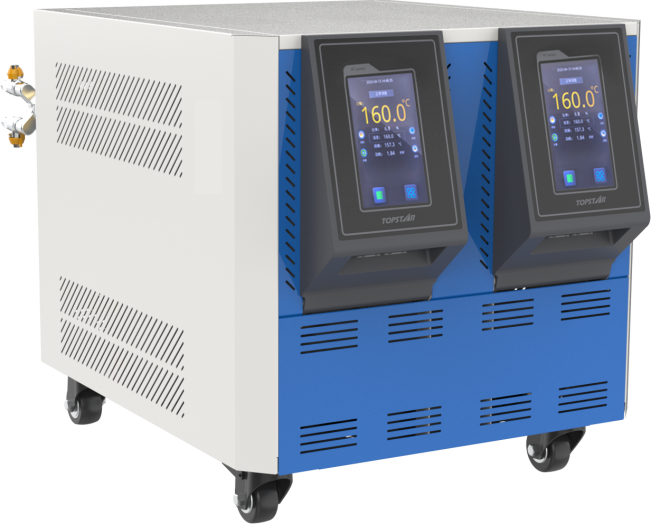
Maintaining precise mold temperatures is important to obtain high-quality molded parts with the shortest cycle times. Auxiliary equipment such as mould temperature controller regulates mold temperature to ensure consistent cooling and optimal part quality. By providing consistent and even cooling, these systems help reduce part warpage, shrinkage, and cycle times, thereby improving part quality.
Various related equipment are indispensable
The various types of equipment mentioned above are indispensable in large-scale production to achieve efficient and high-quality manufacturing processes. Each piece of equipment plays a vital role at different stages of the injection molding process. Generally speaking, the injection molding machine is the core of the injection molding process, responsible for melting the thermoplastic material and injecting it into the mold cavity. Manufacturers use injection molding robots to handle parts in the injection molding process. They can perform process tasks such as removing molded parts from molds and transferring parts to assembly. Manufacturers use relevant auxiliary equipment to dry, dehumidify, and transport the raw materials to ensure that the molded parts are free of defects.
Enable large-scale manufacturing to be performed efficiently and reliably
These equipment are the basis for large-scale manufacturing and, when integrated, can provide efficient production for various industrial applications, ensuring the integrity of the final quality. By and through, the advanced technologies within can unlock new possibilities in mass production.
TRENDING POSTS
- What factors can cause delays in the injection molding process of plastic molding machine? 2024/05/17
- Exhibition Review| Topstar participates in InterPlas Thailand 2024 2024/05/17
- Star Case | Topstar helps Santong upgrade its intelligent plant 2024/05/17
- Topstar Special | National Science and Technology Workers Day 2024/05/17
HOT TOPIC
- .ervo motor-driven linear robots
- 3 axis robot
- 3 axis robots
- 3 in 1 Compact Dehumidifying Dryer
- 3-axis robot
- 3-axis robots
- 5-axis CNC machine
- accuracy
- Air Chillers
- all electric injection molding machine
- all electric injection molding machines
- All-electric injection molding machines
- and overall production quality. Therefore
- AP-RubberPlas
- automated injection molding machine
- Automation changed engineering
- automation of injection molding robots
- auxiliary machine
- Bench Injection Molding Machine
- Cabinet dryer manufacturers
- Cabinet dryers
- chiller
- CNC Drilling Machine
- CNC Drilling Machines
- cnc engraving machine manufacturer
- cnc laser cutting machine manufacturer
- CNC machine
- CNC Machine Center
- CNC Machine for Sale
- CNC Machine Manufacturing
- CNC Machine Tool
- CNC machine tool product
- CNC Machining Center
- CNC wood carving machine
- Cooling system
- Cross-Walking Single Axis Servo Cylinder Robot
- Cross-Walking Single-Axis Servo Cylinder Robot
- Cross-Walking Three-Axis/Five-Axis Servo Driven Robot
- cross-walking three-axis/five-axis servo-driven robot
- Dehumidifier Dryer
- Dehumidifying Dryer
- delta parallel robot
- Desktop Injection Molding Machine
- Desktop injection molding machines
- Desktop Molding Machine
- desktop plastic injection machine
- Desktop Plastic Injection Molding Machine
- direct clamp injection molding machine
- Direct clamp injection molding machines
- Dosing & mixing system
- Drilling Centers
- Drying and dehumidification system
- drying and dehumidifying equipment
- Drying and Dehumidifying System
- drying system
- effective and efficient. Cabinet dryers are also used in other industries where large quantities of material need to be dried
- efficient injection molding machine
- elbow hydraulic injection molding machines
- electric injection molding machine
- electric injection molding machines
- energy-efficient injection molding robot
- energy-saving injection molding machine
- etc. Among injection molding robots
- exhibition
- features of CNC machine
- Feeding And Conveying System
- Five Axis Machine Center
- Fully automatic injection molding machine
- Gathering Topstar
- giant injection molding machine
- GMU-600 5-Axis Machining Center
- Granulating & Recycling System
- Heavy duty injection molding machine
- High-precision electric molding machines
- high-precision plastic molding machines
- high-speed all electric injection molding machine
- Honeycomb rotor dehumidifier
- horizontal injection molding machine
- Horizontal Injection Molding Machines
- Horizontal Injection Moulding Machine
- Horizontal Mixer manufacturer
- How The CNC Machine Works
- hybrid injection molding machine
- hydraulic injection molding machine
- Hydraulic Injection Molding Machines
- in this article
- Industrial robot
- Industrial Robot Chinese brand
- industrial robot parts
- industrial robot supplier
- Industrial robots
- Industry Chain
- Injection Manipulator
- injection manipulator robot
- injection mold machines
- Injection molding
- Injection molding automation
- Injection Molding Automation Solution
- injection molding dryer
- Injection molding equipment
- injection molding hopper dryer
- Injection molding machine
- injection molding machine brand
- Injection Molding Machine Factory
- Injection Molding Machine Manufacture
- Injection molding machine manufacturer
- injection molding machine manufacturers
- Injection molding machine procurement
- injection molding machine robotic arm
- injection molding machine with a robot
- Injection molding machines
- injection molding material dehumidifying
- injection molding plant
- Injection Molding Robot
- injection molding robot arm
- Injection molding robot automation
- Injection molding robotic arm
- injection molding robots
- Injection moulding machine
- Injection Moulding Robots
- Injection Robot
- Injection robot arm
- Injection robot manufacturer
- Injection robot wholesale
- injection robots
- intelligent injection molding machines
- Introducing Injection Robot
- It is the best choice for drying large quantities of material at once. Cabinetmakers use these machines because they are fast
- large injection molding machine
- Learn what industrial automation and robotics is
- linear robot
- linear robots
- low speed sound-proof granulator
- machine plastic molding
- make sure to add some! Improvements (2) Keyphrase in introduction: Your keyphrase or its synonyms appear in the first paragraph of the copy
- manipulator machine
- manufacturing
- medical grade injection molding machines
- medical injection molding machine
- medical injection molding machines
- micro injection molding machine
- middle speed granulator
- Mini CNC machine manufacturers.
- Mold Temperature Control System
- mold temperature controller
- mold temperature controllers
- molding material Dehumidifying System
- mould temperature control system
- mould temperature controller
- mould temperature controllers
- New electric injection molding machine
- nitrogen dryer manufacturer
- nitrogen dryer system manufacturer
- Oil type mold temperature controller
- Oil type mold temperature controllers
- open day
- Outbound links: No outbound links appear in this page. Add some! Images: No images appear on this page. Add some! Internal links: No internal links appear in this page
- PET Preform injection molding
- phone case maker machine
- phone case making machine
- plastic bottle making machine
- plastic bottle manufacturing
- plastic bucket making machine
- plastic bucket manufacturing
- Plastic chair making machine
- plastic forming equipment
- plastic hopper dryer
- plastic injection machine
- plastic injection machines
- plastic injection molding
- Plastic injection molding equipment
- Plastic injection molding machine
- Plastic Injection Molding Machines
- plastic injection moulding machine
- plastic injection robot
- Plastic Molding machine
- Plastic Molding Machines
- plastic molding press
- plastic moulding machine
- plastic phone case making machine
- plastic-molding machine
- powerful granulator
- Powerful Type Sound-Proof Granulator
- precision injection molding
- precision injection molding machines
- production of plastic seats
- pure water mould temperature controller
- Robot injection molding
- robot injection molding machine
- robot manufacturing companies
- Robotic arm for injection molding machine
- robotic injection molding machines
- robotics in injection molding
- SCARA robot
- SCARA robots
- Service-oriented manufacturing
- Servo Cylinder Robot
- servo driven robot
- Servo Driven Robots
- servo injection robots
- servo motor-driven linear robots
- servo-driven 3-axis robot
- Servo-Driven Robot
- Setup of injection machine
- Silicone Injection Molding Machine
- six-axis industrial robot
- Stainless Hopper Dryer
- Stainless Hopper Dryers
- star club
- swing arm robot
- take-out robots
- the choice between servo-driven robots and hydraulic robots will have a certain impact on efficiency
- the most popular injection molding machine
- the type of injection molding robot
- toggle clamp injection molding machine
- Toggle Hydraulic Injection Molding Machines
- toggle injection molding machine
- Top 10 brands of injection robots
- Topstar
- Topstar Engineering
- Topstar Industrial Robots
- Topstar injection molding intelligent
- Topstar Scara Robots
- Useful Injection molding machine
- Vertical machining centers
- volumetric type blender
- water chiller
- water chillers
- water distributor
- water type mold temperature controller
- Water Type MoldTemperature Controller
- Water-Type Mould Temperature Controllers
- We often face choices when performing injection molding. We will choose the type of injection molding machine
- wholesale of injection molding machines
- x carve CNC