Injection mold temperature controller to solve your temperature setting
2022/06/27 By Topstar
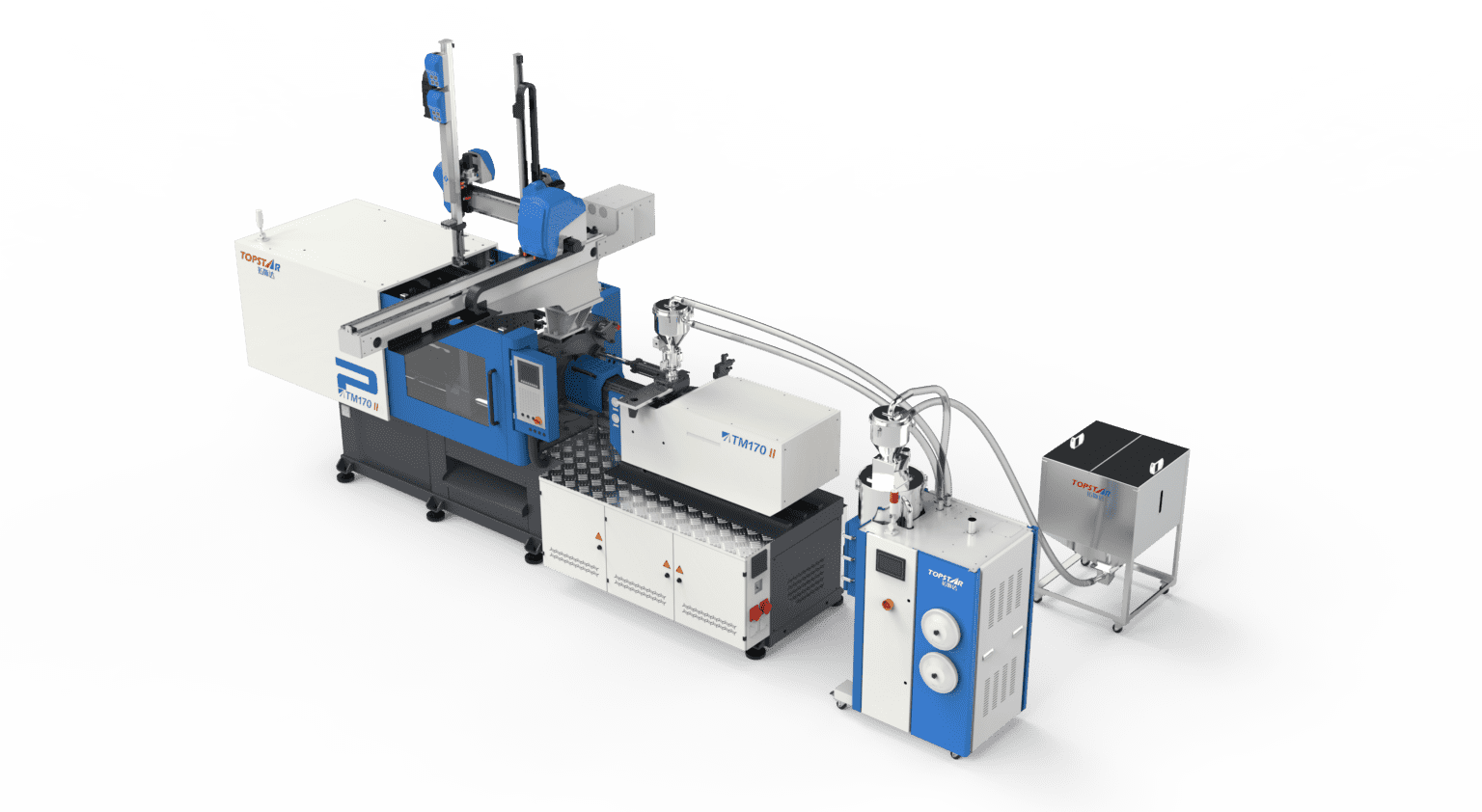
The primary role of the Injection mold temperature controller is to sustain a chosen temperature setting of molds that is suitable for the components and material mixture being formed. The mold thermostat device flows coolant liquid through the mold’s temperature control chambers to balance heat flux during each cycle.
What problems may arise without an Injection mold temperature controller?
Mold temperature control is among other process variables that can influence the performance of an injection molded product. Even within that very restricted segment of molding technique, the number of possible variations is nearly infinite. As a result, we will confine here some of the fundamental reasons for three types of quality problems: difficulties that arise during startup, issues that emerge abruptly, and problems that evolve.
We’ll presume that the injection molding machine is appropriately set up, that the cooling periods and total cycle duration are acceptable, and that the polymer is adequately heated before injection molding. In an ideal world, anyone running a specific mold would know what the mold designer established as the appropriate cooling water temperature and flow rate. Operators and setup people do not always understand these settings, or something changes, necessitating trial and error to re-establish them.
Quality issues:
Quality issues with heat exchange in the mold are frequently caused by poor polymer flow in the instrument because of over- or under-cooling. The latter problem occurs when pieces are not entirely hardened and remain in the mold or distort after being evacuated. When part or all the mold cavities need not filled appropriately, over-cooling may be considered. Material texture may not be duplicated perfectly.
Process Condition or Circumstances:
Molders should be aware of how much process circumstances can affect the final qualities of the part. When working with processors, you may have noticed how much process conditions might influence the standard rates of the molded item. The general view tends to be that the chosen material exhibits the attributes regardless of how the scrap metal is transformed into the set object. According to this logic, the processor’s task is to melt the material, pass it through the proper processing facilities, and re-solidify the polymers into the Form described by the print. Sadly, it is not as simple as that. Molding circumstances, for example, significantly impact the end properties of a material irrespective of the component design in injection molding. Melt temperature and mold temperature are processes that significantly affect polymer behavior.
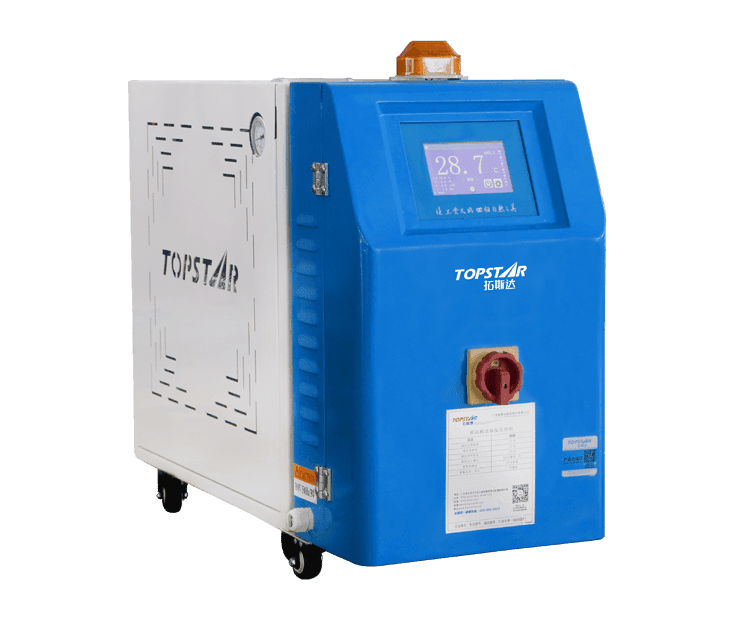
Factors affecting mold temperature:
First, we must distinguish between such processing conditions and the pre-existing conditions we utilize to govern them. The polymer’s heat when it exits the tip and enters the mold is called melt temperature. The barrel set points indicate the instruments we employ to achieve the appropriate liquid temperature but are not interchangeable. The mechanical work given to the substance, the residence period, and the quality of the screws and barrel all influence the actual melt temperature. Likewise, the actual average temperature of the mold cores and cavities is related to, but not always the same one as, the ambient temperature traveling through the mold channels. Provided that we can investigate the influence of these two
Mold Temperature:
Mold temperature has a less evident but frequently more significant impact on final characteristics. Higher mold temperatures in synthetic materials such as ABS and celluloid will lower moldable stress levels. To improve impact toughness, stress tolerance, and fatigue performance.
The function of the Injection mold temperature controller:
A function of a mold thermostat is to force coolant to flow and steady coolant temperature. The primary duty of a mold thermostat’s pump is to force coolant to flow. When the flow rate increases, the pump pressure lowers. The pump pressure increases when the flow rate decreases. The max flow rate and pressure values on the injection mold temperature controller specification can be seen. Through cooling channel analysis, the user can access the fluid pressure difference of each cooling channel. The mold temperature controller must supply the entire flow rate of the cooling channels.
The minimum pressure required by the mold temperature controller is the maximum pressure in the cooling system. If the coordination point is lower, it indicates that the mold temperature controller can supply an adequate flow rate and pressure. If the coordination point is higher, it suggests that the mold temperature controller cannot deliver sufficient flow rate and pressure. The optimum cooling channel condition in injection molding is commonly set at a high flow rate. However, after adjusting it to suit the criteria of the mold temperature controls, users will receive a considerable value.
Temperature regulation in polymer injection:
Temperature management keeps quality and other issues, like shrinkage, strains, and warping, at bay throughout the injection molding process.
Advantages of using an Injection Molding Controller:
Injection molding is an industrial method to create plastic components and objects. The injection molding technique outperforms traditional plastic manufacturing techniques in the following ways:
- Because the rate/unit of creating a part of injection mold is minimal by using an Injection mold temperature controller, manufacturers can save significantly more money.
- It is a device for an accurate and continuous procedure that can be virtually automated.
- This contributes to lower work costs, faster manufacturing, and a shorter marketing time for new items.
- It also assists producers in reducing resource waste.
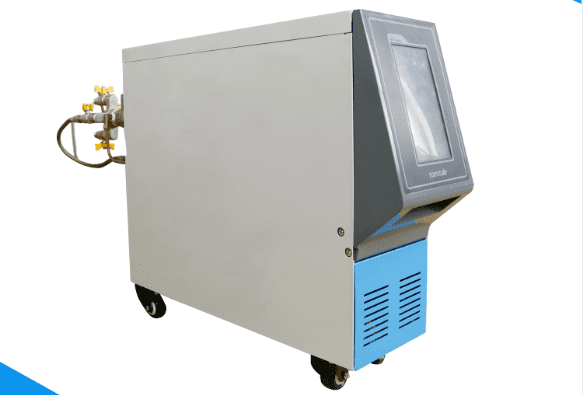
Why should you choose TopStar?
Topstar is one of the leading manufacturers in the market. We provide high-quality and reasonable machinery to our customers and believe that customers are our greatest asset. Our best-selling Injection mold temperature controller offers multiple features like Form in a mold. It’s highly dimensional, contains short molding cycles ranging from a few moments to several minutes, and provides increased productivity, which means less labor is required to finish. It is excellent for thermoplastic processing.
TRENDING POSTS
- What factors can cause delays in the injection molding process of plastic molding machine? 2022/06/27
- Exhibition Review| Topstar participates in InterPlas Thailand 2024 2022/06/27
- Star Case | Topstar helps Santong upgrade its intelligent plant 2022/06/27
- Topstar Special | National Science and Technology Workers Day 2022/06/27
HOT TOPIC
- 3 in 1 Compact Dehumidifying Dryer
- 5-axis CNC machine
- accuracy
- Air Chillers
- all electric injection molding machine
- All-electric injection molding machines
- and overall production quality. Therefore
- AP-RubberPlas
- automated injection molding machine
- Automation changed engineering
- automation of injection molding robots
- auxiliary machine
- Bench Injection Molding Machine
- Cabinet dryer manufacturers
- Cabinet dryers
- chiller
- CNC Drilling Machine
- CNC Drilling Machines
- cnc engraving machine manufacturer
- cnc laser cutting machine manufacturer
- CNC machine
- CNC Machine Center
- CNC Machine for Sale
- CNC Machine Manufacturing
- CNC Machine Tool
- CNC machine tool product
- CNC Machining Center
- CNC wood carving machine
- Cooling system
- Cross-Walking Single Axis Servo Cylinder Robot
- Cross-Walking Single-Axis Servo Cylinder Robot
- Cross-Walking Three-Axis/Five-Axis Servo Driven Robot
- cross-walking three-axis/five-axis servo-driven robot
- Dehumidifier Dryer
- Dehumidifying Dryer
- delta parallel robot
- Desktop Injection Molding Machine
- Desktop injection molding machines
- Desktop Molding Machine
- desktop plastic injection machine
- Desktop Plastic Injection Molding Machine
- direct clamp injection molding machine
- Direct clamp injection molding machines
- Dosing & mixing system
- Drilling Centers
- Drying and dehumidification system
- drying and dehumidifying equipment
- Drying and Dehumidifying System
- drying system
- effective and efficient. Cabinet dryers are also used in other industries where large quantities of material need to be dried
- efficient injection molding machine
- elbow hydraulic injection molding machines
- electric injection molding machine
- electric injection molding machines
- etc. Among injection molding robots
- exhibition
- features of CNC machine
- Feeding And Conveying System
- Five Axis Machine Center
- Fully automatic injection molding machine
- Gathering Topstar
- giant injection molding machine
- GMU-600 5-Axis Machining Center
- Granulating & Recycling System
- Heavy duty injection molding machine
- Honeycomb rotor dehumidifier
- horizontal injection molding machine
- Horizontal Injection Molding Machines
- Horizontal Injection Moulding Machine
- Horizontal Mixer manufacturer
- How The CNC Machine Works
- hybrid injection molding machine
- hydraulic injection molding machine
- Hydraulic Injection Molding Machines
- in this article
- Industrial robot
- Industrial Robot Chinese brand
- industrial robot parts
- industrial robot supplier
- Industrial robots
- Industry Chain
- Injection Manipulator
- injection mold machines
- Injection molding
- Injection molding automation
- Injection Molding Automation Solution
- injection molding dryer
- Injection molding equipment
- injection molding hopper dryer
- Injection molding machine
- injection molding machine brand
- Injection Molding Machine Factory
- Injection Molding Machine Manufacture
- Injection molding machine manufacturer
- injection molding machine manufacturers
- Injection molding machine procurement
- injection molding machine robotic arm
- injection molding machine with a robot
- Injection molding machines
- injection molding material dehumidifying
- injection molding plant
- Injection Molding Robot
- injection molding robot arm
- Injection molding robot automation
- Injection molding robotic arm
- injection molding robots
- Injection Moulding Robots
- Injection Robot
- Injection robot arm
- Injection robot manufacturer
- Injection robot wholesale
- injection robots
- intelligent injection molding machines
- Introducing Injection Robot
- It is the best choice for drying large quantities of material at once. Cabinetmakers use these machines because they are fast
- large injection molding machine
- Learn what industrial automation and robotics is
- low speed sound-proof granulator
- machine plastic molding
- make sure to add some! Improvements (2) Keyphrase in introduction: Your keyphrase or its synonyms appear in the first paragraph of the copy
- manipulator machine
- manufacturing
- micro injection molding machine
- middle speed granulator
- Mini CNC machine manufacturers.
- Mold Temperature Control System
- mold temperature controller
- molding material Dehumidifying System
- mould temperature controller
- mould temperature controllers
- New electric injection molding machine
- nitrogen dryer manufacturer
- nitrogen dryer system manufacturer
- Oil type mold temperature controller
- open day
- Outbound links: No outbound links appear in this page. Add some! Images: No images appear on this page. Add some! Internal links: No internal links appear in this page
- PET Preform injection molding
- phone case maker machine
- phone case making machine
- plastic bottle making machine
- plastic bottle manufacturing
- plastic bucket making machine
- plastic bucket manufacturing
- Plastic chair making machine
- plastic forming equipment
- plastic hopper dryer
- plastic injection machine
- plastic injection machines
- plastic injection molding
- Plastic injection molding equipment
- Plastic injection molding machine
- Plastic Injection Molding Machines
- plastic injection robot
- Plastic Molding machine
- Plastic Molding Machines
- plastic molding press
- plastic phone case making machine
- plastic-molding machine
- powerful granulator
- Powerful Type Sound-Proof Granulator
- production of plastic seats
- Robot injection molding
- robot injection molding machine
- robot manufacturing companies
- Robotic arm for injection molding machine
- robotic injection molding machines
- robotics in injection molding
- SCARA robot
- SCARA robots
- Service-oriented manufacturing
- Servo Cylinder Robot
- servo driven robot
- Servo Driven Robots
- servo injection robots
- Servo-Driven Robot
- Setup of injection machine
- Silicone Injection Molding Machine
- six-axis industrial robot
- Stainless Hopper Dryer
- Stainless Hopper Dryers
- star club
- swing arm robot
- the choice between servo-driven robots and hydraulic robots will have a certain impact on efficiency
- the most popular injection molding machine
- the type of injection molding robot
- toggle clamp injection molding machine
- Toggle Hydraulic Injection Molding Machines
- toggle injection molding machine
- Top 10 brands of injection robots
- Topstar
- Topstar Engineering
- Topstar Industrial Robots
- Topstar injection molding intelligent
- Topstar Scara Robots
- Useful Injection molding machine
- Vertical machining centers
- volumetric type blender
- water chiller
- water chillers
- water distributor
- Water Type MoldTemperature Controller
- We often face choices when performing injection molding. We will choose the type of injection molding machine
- wholesale of injection molding machines
- x carve CNC