How to use water chiller to achieve efficient and energy-saving injection molding cooling?
2025/04/11 By Topstar
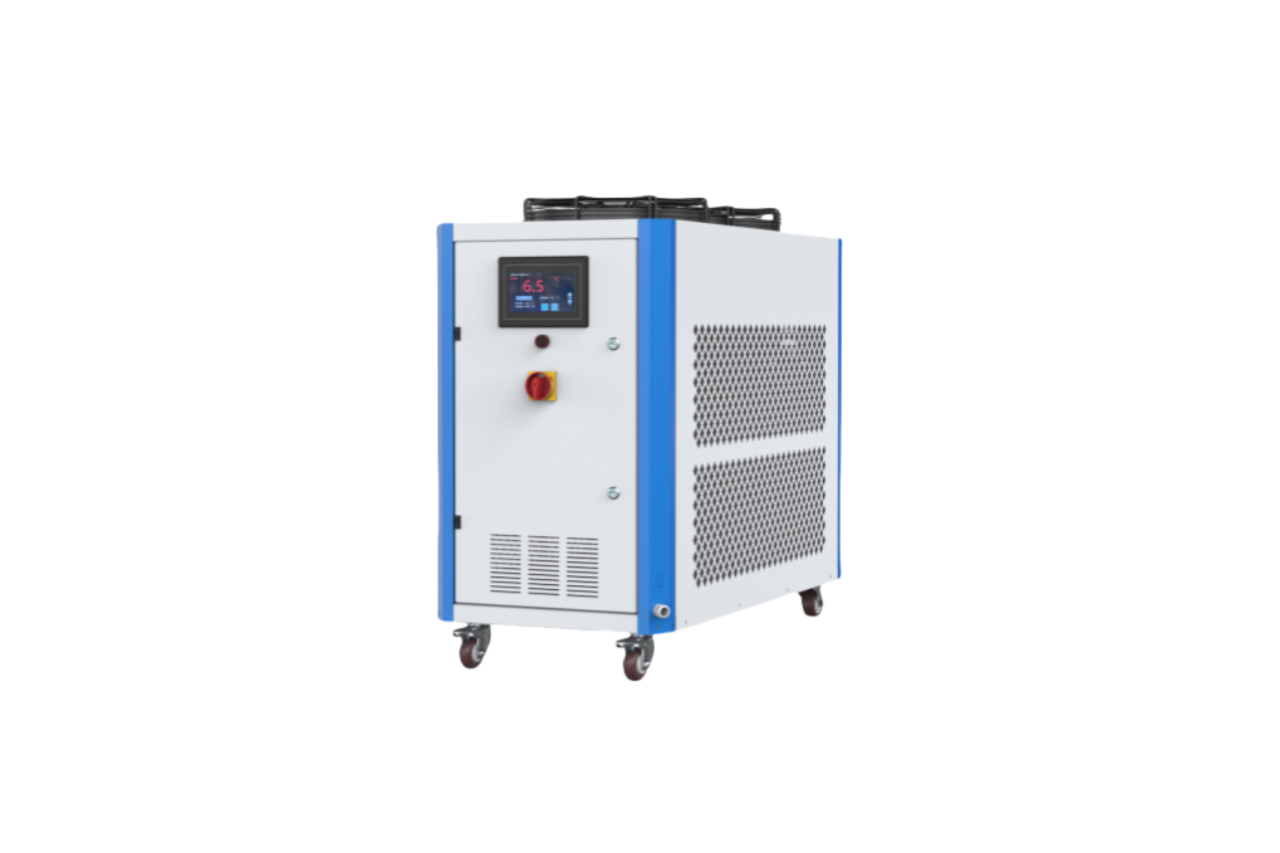
The role of the water chiller is to regulate the mold temperature during the injection molding process to prevent defects such as warping or long cycle times. In injection molding, the cooling process is as vital as the molding process. Efficient cooling ensures high-quality parts, faster production cycles, and significant energy savings; for manufacturers pursuing precision and energy saving, high-performance, high-efficiency water chillers are key to improving overall production efficiency.
Multi-compressor staged control of water chiller, energy saving, and improved efficiency.
Topstar water chillers use multi-compressor staged control, which can directly improve cooling efficiency and energy saving. In traditional refrigeration systems, one compressor is responsible for maintaining a constant cooling output regardless of how the demand changes throughout the day. This often leads to energy waste because the system will run at full capacity despite low cooling demand. Multi-compressor staged control can be activated and deactivated according to the cooling demand of the system. This staged control ensures that the chiller operates optimally and consumes only the energy required to meet the demand. While improving energy efficiency, it also extends the life of the equipment and avoids the continuous wear and tear caused by a single compressor running at full capacity.
Self-developed horizontal multi-stage centrifugal pump
In addition to the multi-compressor stage control, self-developed horizontal multi-stage centrifugal pumps are used in the chiller to improve cooling efficiency. The overall design includes multi-stage pressurization, large flow, and low-noise operation, which can improve the overall performance of the water chiller. These centrifugal pumps are responsible for circulating the coolant in the system to ensure adequate heat dissipation from the mold. The advantage of multi-stage centrifugal pumps is that they provide higher flow with lower energy consumption. The multi-stage design ensures that water is pumped constantly, especially in a large-scale injection molding production environment, to maintain a stable cooling effect. In addition to improving cooling efficiency, the centrifugal pump design also focuses on minimizing noise, allowing the water chiller to ensure a quieter and more comfortable workplace.
Small diameter parallel multi-channel coil design, faster cooling speed
The coil design of the water chiller is crucial to the heat exchange efficiency. The water chiller adopts a small diameter parallel multi-channel coil design. This efficient configuration can improve both cooling speed and pressure resistance. In this design, the coolant flows through multiple channels simultaneously, increasing the heat exchange surface area and allowing the system to cool the mold faster. The use of small diameter channels in the coil improves the flow dynamics of the coolant, ensuring a consistent temperature throughout the cooling process, resulting in faster cooling, shorter cycle times, higher production efficiency, and preventing defects such as mold warping or incomplete filling caused by temperature fluctuations. In addition to more rapid cooling, the multi-channel design also improves the system’s pressure resistance. This allows the chiller to withstand higher pressure in environments without compromising performance or safety.
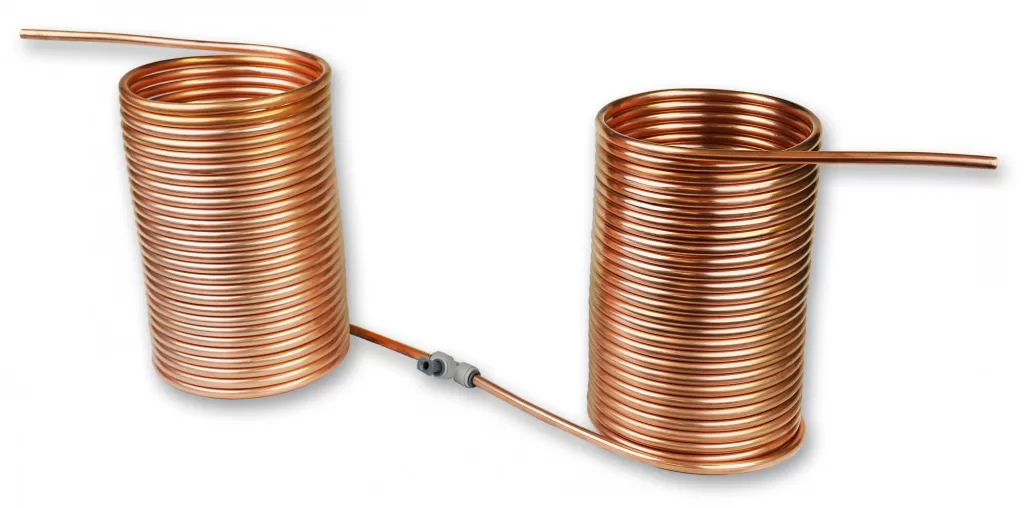
Reduced weld points in the water chiller to enhance durability
The chiller’s body has been carefully designed to reduce 60% of weld points, which directly reduces the risk of weld corrosion and water leakage. Traditional chillers’ weld points are often susceptible to stress, corrosion, and damage, especially in environments with temperature fluctuations and high humidity.
The reduction in weld points also reduces the system failure rate and the need for frequent maintenance, thereby improving the overall efficiency of the chiller. At the same time, it also reduces the possibility of weak points, ensuring that the chiller can operate smoothly for a more extended period. In addition, this design improvement also improves the safety of the water chiller, reducing potential leak points, avoiding the loss of coolant and the decline in system efficiency, and ensuring that the system is more sealed and safe, thereby maintaining stable cooling performance.
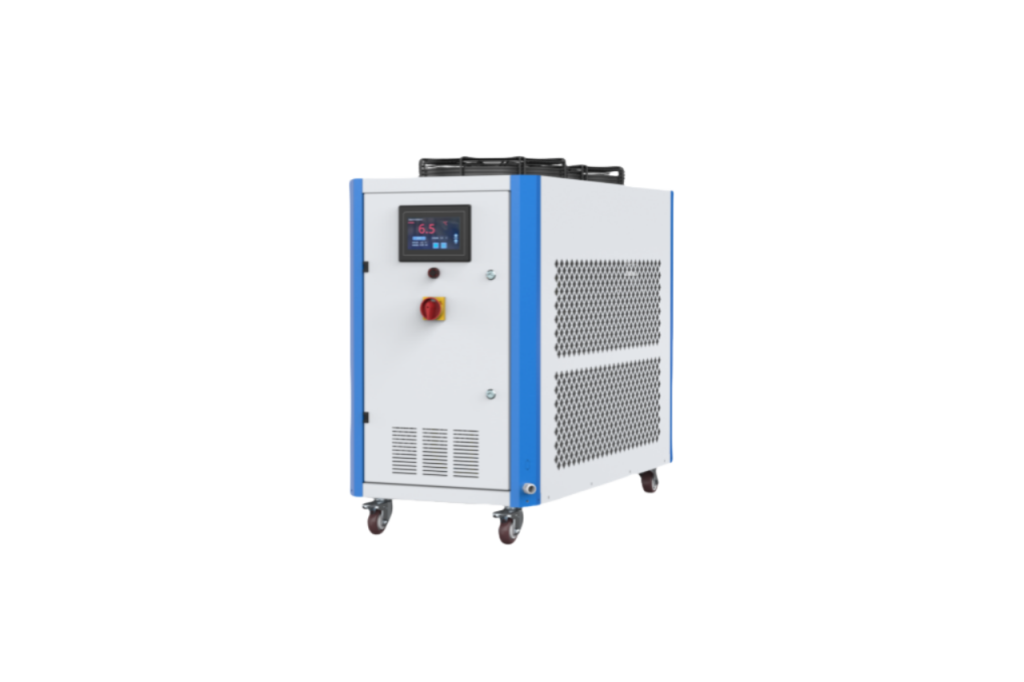
Added safety features
To ensure that the water chiller is safer during operation, Topstar uses door interlock circuit breakers to ensure safe operation at all times. The door interlock circuit breaker automatically cuts off the power when the access door is open, preventing the chiller from operating when the access door is open, thereby ensuring the safety of technicians and operators while the system is running. In addition to protecting the operator, this safety feature also helps maintain the integrity of the chiller’s cooling process. Opening the door while the chiller is running can cause temperature fluctuations and interrupt the cooling cycle, resulting in inefficiency and possible damage to the system. The interlock circuit breaker keeps the cooling process uninterrupted while the system runs, preventing this from happening.
Achieve efficient and energy-saving injection molding cooling
Topstar’s water chillers combine energy-saving design with practical functions directly affecting performance and efficiency. The chiller provides reliable, stable, and efficient cooling performance through multi-compressor staged control, self-developed horizontal multi-stage centrifugal pumps, multi-channel coils, and other designs. It allows more precise temperature control during molding, shortens cycle time, and improves overall productivity.
TRENDING POSTS
- What factors can cause delays in the injection molding process of plastic molding machine? 2025/04/11
- Exhibition Review| Topstar participates in InterPlas Thailand 2024 2025/04/11
- Star Case | Topstar helps Santong upgrade its intelligent plant 2025/04/11
- Topstar Special | National Science and Technology Workers Day 2025/04/11
HOT TOPIC
- 3 in 1 Compact Dehumidifying Dryer
- 5-axis CNC machine
- accuracy
- Air Chillers
- all electric injection molding machine
- All-electric injection molding machines
- and overall production quality. Therefore
- AP-RubberPlas
- automated injection molding machine
- Automation changed engineering
- automation of injection molding robots
- auxiliary machine
- Bench Injection Molding Machine
- Cabinet dryer manufacturers
- Cabinet dryers
- chiller
- CNC Drilling Machine
- CNC Drilling Machines
- cnc engraving machine manufacturer
- cnc laser cutting machine manufacturer
- CNC machine
- CNC Machine Center
- CNC Machine for Sale
- CNC Machine Manufacturing
- CNC Machine Tool
- CNC machine tool product
- CNC Machining Center
- CNC wood carving machine
- Cooling system
- Cross-Walking Single Axis Servo Cylinder Robot
- Cross-Walking Single-Axis Servo Cylinder Robot
- Cross-Walking Three-Axis/Five-Axis Servo Driven Robot
- cross-walking three-axis/five-axis servo-driven robot
- Dehumidifier Dryer
- Dehumidifying Dryer
- delta parallel robot
- Desktop Injection Molding Machine
- Desktop injection molding machines
- Desktop Molding Machine
- desktop plastic injection machine
- Desktop Plastic Injection Molding Machine
- direct clamp injection molding machine
- Direct clamp injection molding machines
- Dosing & mixing system
- Drilling Centers
- Drying and dehumidification system
- drying and dehumidifying equipment
- Drying and Dehumidifying System
- drying system
- effective and efficient. Cabinet dryers are also used in other industries where large quantities of material need to be dried
- efficient injection molding machine
- elbow hydraulic injection molding machines
- electric injection molding machine
- electric injection molding machines
- etc. Among injection molding robots
- exhibition
- features of CNC machine
- Feeding And Conveying System
- Five Axis Machine Center
- Fully automatic injection molding machine
- Gathering Topstar
- giant injection molding machine
- GMU-600 5-Axis Machining Center
- Granulating & Recycling System
- Heavy duty injection molding machine
- Honeycomb rotor dehumidifier
- horizontal injection molding machine
- Horizontal Injection Molding Machines
- Horizontal Injection Moulding Machine
- Horizontal Mixer manufacturer
- How The CNC Machine Works
- hybrid injection molding machine
- hydraulic injection molding machine
- Hydraulic Injection Molding Machines
- in this article
- Industrial robot
- Industrial Robot Chinese brand
- industrial robot parts
- industrial robot supplier
- Industrial robots
- Industry Chain
- Injection Manipulator
- injection mold machines
- Injection molding
- Injection molding automation
- Injection Molding Automation Solution
- injection molding dryer
- Injection molding equipment
- injection molding hopper dryer
- Injection molding machine
- injection molding machine brand
- Injection Molding Machine Factory
- Injection Molding Machine Manufacture
- Injection molding machine manufacturer
- injection molding machine manufacturers
- Injection molding machine procurement
- injection molding machine robotic arm
- injection molding machine with a robot
- Injection molding machines
- injection molding material dehumidifying
- injection molding plant
- Injection Molding Robot
- injection molding robot arm
- Injection molding robot automation
- Injection molding robotic arm
- injection molding robots
- Injection Moulding Robots
- Injection Robot
- Injection robot arm
- Injection robot manufacturer
- Injection robot wholesale
- injection robots
- intelligent injection molding machines
- Introducing Injection Robot
- It is the best choice for drying large quantities of material at once. Cabinetmakers use these machines because they are fast
- large injection molding machine
- Learn what industrial automation and robotics is
- low speed sound-proof granulator
- machine plastic molding
- make sure to add some! Improvements (2) Keyphrase in introduction: Your keyphrase or its synonyms appear in the first paragraph of the copy
- manipulator machine
- manufacturing
- micro injection molding machine
- middle speed granulator
- Mini CNC machine manufacturers.
- Mold Temperature Control System
- mold temperature controller
- molding material Dehumidifying System
- mould temperature controller
- mould temperature controllers
- New electric injection molding machine
- nitrogen dryer manufacturer
- nitrogen dryer system manufacturer
- Oil type mold temperature controller
- open day
- Outbound links: No outbound links appear in this page. Add some! Images: No images appear on this page. Add some! Internal links: No internal links appear in this page
- PET Preform injection molding
- phone case maker machine
- phone case making machine
- plastic bottle making machine
- plastic bottle manufacturing
- plastic bucket making machine
- plastic bucket manufacturing
- Plastic chair making machine
- plastic forming equipment
- plastic hopper dryer
- plastic injection machine
- plastic injection machines
- plastic injection molding
- Plastic injection molding equipment
- Plastic injection molding machine
- Plastic Injection Molding Machines
- plastic injection robot
- Plastic Molding machine
- Plastic Molding Machines
- plastic molding press
- plastic phone case making machine
- plastic-molding machine
- powerful granulator
- Powerful Type Sound-Proof Granulator
- production of plastic seats
- Robot injection molding
- robot injection molding machine
- robot manufacturing companies
- Robotic arm for injection molding machine
- robotic injection molding machines
- robotics in injection molding
- SCARA robot
- SCARA robots
- Service-oriented manufacturing
- Servo Cylinder Robot
- servo driven robot
- Servo Driven Robots
- servo injection robots
- Servo-Driven Robot
- Setup of injection machine
- Silicone Injection Molding Machine
- six-axis industrial robot
- Stainless Hopper Dryer
- Stainless Hopper Dryers
- star club
- swing arm robot
- the choice between servo-driven robots and hydraulic robots will have a certain impact on efficiency
- the most popular injection molding machine
- the type of injection molding robot
- toggle clamp injection molding machine
- Toggle Hydraulic Injection Molding Machines
- toggle injection molding machine
- Top 10 brands of injection robots
- Topstar
- Topstar Engineering
- Topstar Industrial Robots
- Topstar injection molding intelligent
- Topstar Scara Robots
- Useful Injection molding machine
- Vertical machining centers
- volumetric type blender
- water chiller
- water chillers
- water distributor
- Water Type MoldTemperature Controller
- We often face choices when performing injection molding. We will choose the type of injection molding machine
- wholesale of injection molding machines
- x carve CNC