How to use a plastic molding machine to achieve a closed loop of the entire production process?
2025/04/16 By Topstar
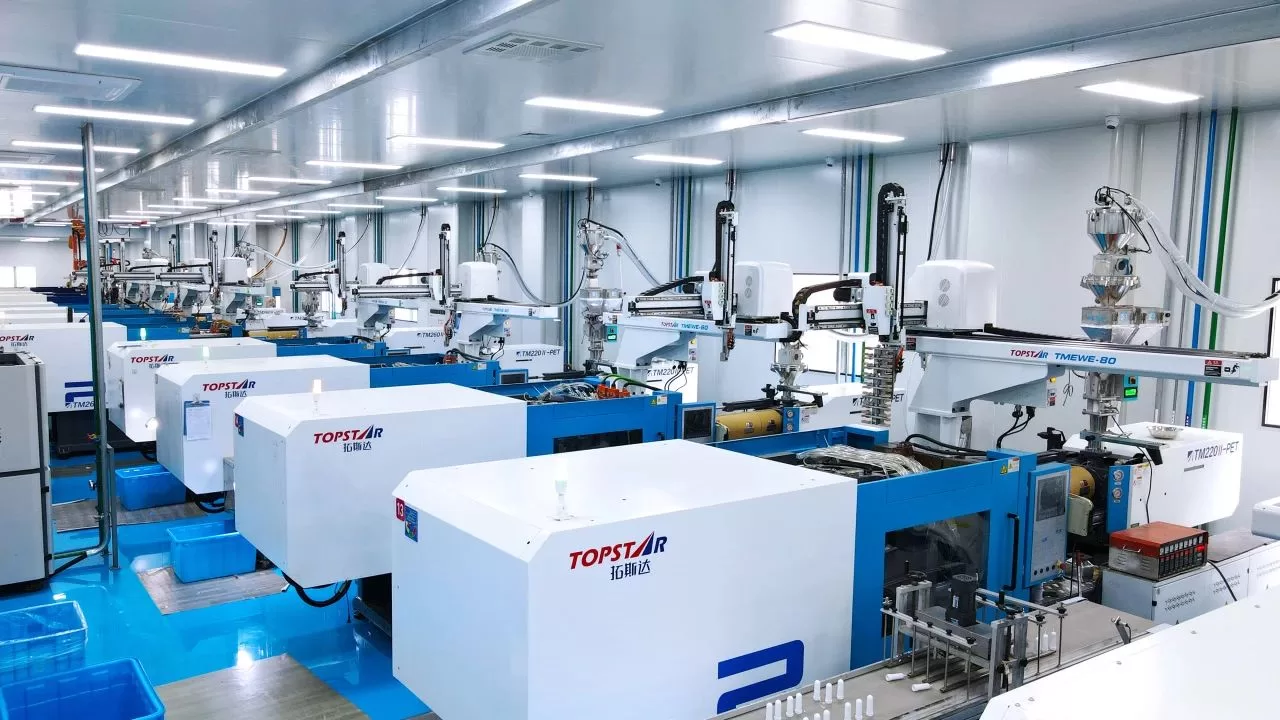
In the injection molding manufacturing industry, which advocates cost reduction and efficiency improvement, integrated closed-loop production processes can maximize efficiency, reduce waste, and maintain stable production. To help customers achieve the full process of high-speed closed-loop production, injection molding machines with integrated injection molding processes are used. These machines can work with surrounding auxiliary equipment and report their operating status under a unified control system. This integration helps achieve real-time remote intelligent operation and maintenance, ensuring that each component on the production line can coordinate. In addition, the plastic molding machine is also compatible with the robot to achieve functions such as automatic trajectory adjustment and synchronous linkage with the mold opening process. These integrated compatibilities help reduce the number of abnormal alarms and minimize downtime caused by equipment maintenance, improving overall production efficiency.
Intelligent integration of plastic molding machine and peripheral auxiliary equipment
When the plastic molding machine is reasonably integrated with auxiliary equipment, it acts as the central nervous system of closed-loop production. Topstar uses IoT connectivity through a unified control system and communication language to build a seamless network between the central injection unit and all supporting components.
This integration goes beyond simple communication and achieves predictive coordination, enabling the molding machine to predict the needs of downstream equipment. For example, when sensors detect increased moisture content in the resin, the system automatically adjusts the dryer settings while notifying the material handling system to prepare for additional drying time. This level of automation eliminates the traditional lag between detection and response, reducing material waste by up to 25%. Its real advantage lies in standardized communication protocols that enable different injection molding equipment to work together. It can minimize mold change time by 40% while improving product consistency across all production lines.

Comprehensive real-time monitoring for optimal performance
Operators must continuously and meticulously monitor all aspects of the molding process to achieve actual closed-loop production.
Topstar’s plastic molding machines are under a self-developed control system, connecting the underlying control system, and can track key parameters such as melt temperature, cavity pressure, and hydraulic pressure through a unified control panel. It can transmit data to a central processor, which analyzes real-time information and compares the current state with ideal production parameters. The system is not only able to monitor but also learn and adapt. Through machine learning algorithms, it can detect subtle patterns before quality problems occur,
For example, when the screw gradually wears or subtle changes in material viscosity. When deviations occur, the system makes fine adjustments to maintain optimal conditions. When the cavity pressure deviates from acceptable limits, the machine can compensate within milliseconds by adjusting the injection speed or holding pressure. This proactive process control approach has helped manufacturers reduce scrap rates by up to 35% while maintaining tighter finish product tolerances. The monitoring system also tracks energy consumption patterns to identify opportunities to optimize power usage without compromising product quality.
Intelligent injection molding robot technology for seamless integration
Synchronization between plastic molding machines and robotic systems is one of the key elements of closed-loop production. Topstar’s solution is based on an open architecture through the underlying control system, which enables injection molding peripheral auxiliary machines and injection molding machines to have a native system integration language, making equipment interconnection an extension of the system rather than just a communication connection.
As a result, the injection molding robot can support the host to call signals and realize integrated operation, and the control system automatically optimizes the process of removal, improves the injection molding efficiency of the production line, and establishes intelligent collaboration between the injection molding machine and the injection molding robot. For example, if a part is slightly stuck during ejection, the robot can detect resistance and adjust the gripping force accordingly. The system’s “early arrival” function significantly shortens cycle time. With gripping mode, the robot can locate and remove the part when ejection begins, saving valuable time for each cycle.
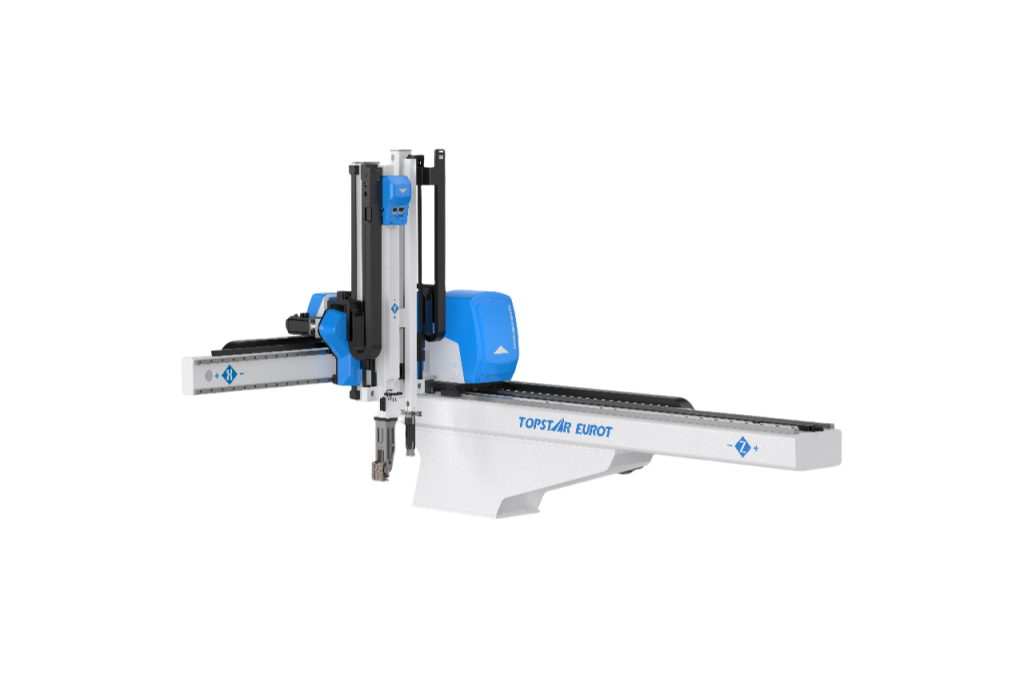
High-speed plastic molding machine, maximized efficiency
Topstar’s electric plastic molding machines eliminate the energy losses and response delays associated with fluid power systems by replacing traditional hydraulic systems with discrete intelligent drive controls. The electric drive unit responds instantly to control inputs, enabling precise injection speed and pressure adjustment at each stage of the molding cycle, achieving excellent molding cycles of 2-7.6 seconds. The parallel processing function prepares the next shot while the current shot is still cooling. Intelligent algorithms optimize clamping force based on material properties and mold geometry, reducing energy consumption by up to 30% compared to traditional systems. For the medical industry, switching to Topstar’s electric plastic molding machines has increased the output of precision catheter components by 40%, reducing energy costs and meeting strict cleanroom standards. The closed-loop control system maintains consistency within 0.5% for each shot.
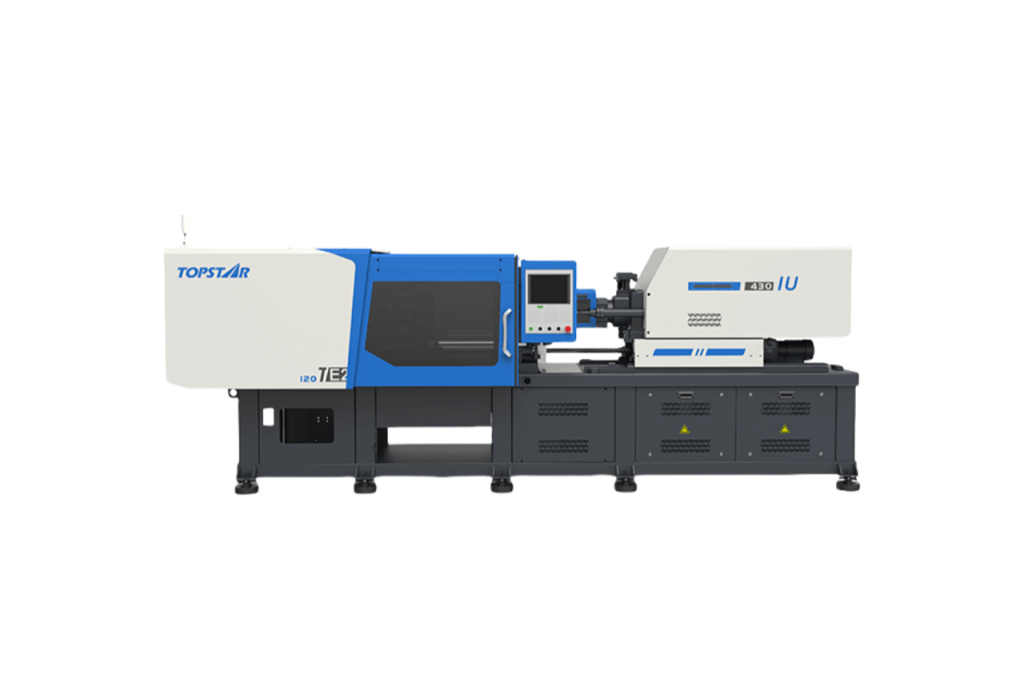
Space-saving modular production system
Engineers have redesigned the traditional linear production layout into a compact modular work cell that vertically combines multiple functions. They have integrated material handling systems directly into the machine frame, eliminating the need for an extensive conveyor network. Engineers have also integrated quality inspection stations into the part removal process to verify components immediately before they go into packaging.
This modular approach can significantly reduce installation time, and a Mexican automotive parts supplier completed the transformation of its entire production workshop in just three weeks. The vertical design can reduce the footprint of each production unit by up to 60% compared to traditional layouts. More importantly, the integrated nature of these systems improves material flow and reduces handling time between processes. Components go directly from molding to secondary processing to packaging in a continuous, optimized process. In addition, the modular design provides flexibility – additional functions can be added as needed without large-scale reconfiguration of the production line.
Achieving a closed loop in the entire production process
Achieving a closed-loop production process includes interconnecting all peripheral auxiliary equipment under a unified control system, continuously monitoring machine performance, and implementing predictive maintenance strategies. The ability to automatically adjust and fine-tune operating parameters in real time minimizes downtime and improves overall product consistency and quality. This holistic injection molding production approach combines advanced technology with seamless automation and integrated design, enabling manufacturers to achieve continuous operations and high-quality output.
TRENDING POSTS
- What factors can cause delays in the injection molding process of plastic molding machine? 2025/04/16
- Exhibition Review| Topstar participates in InterPlas Thailand 2024 2025/04/16
- Star Case | Topstar helps Santong upgrade its intelligent plant 2025/04/16
- Topstar Special | National Science and Technology Workers Day 2025/04/16
HOT TOPIC
- 3 in 1 Compact Dehumidifying Dryer
- 5-axis CNC machine
- accuracy
- Air Chillers
- all electric injection molding machine
- All-electric injection molding machines
- and overall production quality. Therefore
- AP-RubberPlas
- automated injection molding machine
- Automation changed engineering
- automation of injection molding robots
- auxiliary machine
- Bench Injection Molding Machine
- Cabinet dryer manufacturers
- Cabinet dryers
- chiller
- CNC Drilling Machine
- CNC Drilling Machines
- cnc engraving machine manufacturer
- cnc laser cutting machine manufacturer
- CNC machine
- CNC Machine Center
- CNC Machine for Sale
- CNC Machine Manufacturing
- CNC Machine Tool
- CNC machine tool product
- CNC Machining Center
- CNC wood carving machine
- Cooling system
- Cross-Walking Single Axis Servo Cylinder Robot
- Cross-Walking Single-Axis Servo Cylinder Robot
- Cross-Walking Three-Axis/Five-Axis Servo Driven Robot
- cross-walking three-axis/five-axis servo-driven robot
- Dehumidifier Dryer
- Dehumidifying Dryer
- delta parallel robot
- Desktop Injection Molding Machine
- Desktop injection molding machines
- Desktop Molding Machine
- desktop plastic injection machine
- Desktop Plastic Injection Molding Machine
- direct clamp injection molding machine
- Direct clamp injection molding machines
- Dosing & mixing system
- Drilling Centers
- Drying and dehumidification system
- drying and dehumidifying equipment
- Drying and Dehumidifying System
- drying system
- effective and efficient. Cabinet dryers are also used in other industries where large quantities of material need to be dried
- efficient injection molding machine
- elbow hydraulic injection molding machines
- electric injection molding machine
- electric injection molding machines
- etc. Among injection molding robots
- exhibition
- features of CNC machine
- Feeding And Conveying System
- Five Axis Machine Center
- Fully automatic injection molding machine
- Gathering Topstar
- giant injection molding machine
- GMU-600 5-Axis Machining Center
- Granulating & Recycling System
- Heavy duty injection molding machine
- Honeycomb rotor dehumidifier
- horizontal injection molding machine
- Horizontal Injection Molding Machines
- Horizontal Injection Moulding Machine
- Horizontal Mixer manufacturer
- How The CNC Machine Works
- hybrid injection molding machine
- hydraulic injection molding machine
- Hydraulic Injection Molding Machines
- in this article
- Industrial robot
- Industrial Robot Chinese brand
- industrial robot parts
- industrial robot supplier
- Industrial robots
- Industry Chain
- Injection Manipulator
- injection mold machines
- Injection molding
- Injection molding automation
- Injection Molding Automation Solution
- injection molding dryer
- Injection molding equipment
- injection molding hopper dryer
- Injection molding machine
- injection molding machine brand
- Injection Molding Machine Factory
- Injection Molding Machine Manufacture
- Injection molding machine manufacturer
- injection molding machine manufacturers
- Injection molding machine procurement
- injection molding machine robotic arm
- injection molding machine with a robot
- Injection molding machines
- injection molding material dehumidifying
- injection molding plant
- Injection Molding Robot
- injection molding robot arm
- Injection molding robot automation
- Injection molding robotic arm
- injection molding robots
- Injection Moulding Robots
- Injection Robot
- Injection robot arm
- Injection robot manufacturer
- Injection robot wholesale
- injection robots
- intelligent injection molding machines
- Introducing Injection Robot
- It is the best choice for drying large quantities of material at once. Cabinetmakers use these machines because they are fast
- large injection molding machine
- Learn what industrial automation and robotics is
- low speed sound-proof granulator
- machine plastic molding
- make sure to add some! Improvements (2) Keyphrase in introduction: Your keyphrase or its synonyms appear in the first paragraph of the copy
- manipulator machine
- manufacturing
- micro injection molding machine
- middle speed granulator
- Mini CNC machine manufacturers.
- Mold Temperature Control System
- mold temperature controller
- molding material Dehumidifying System
- mould temperature controller
- mould temperature controllers
- New electric injection molding machine
- nitrogen dryer manufacturer
- nitrogen dryer system manufacturer
- Oil type mold temperature controller
- open day
- Outbound links: No outbound links appear in this page. Add some! Images: No images appear on this page. Add some! Internal links: No internal links appear in this page
- PET Preform injection molding
- phone case maker machine
- phone case making machine
- plastic bottle making machine
- plastic bottle manufacturing
- plastic bucket making machine
- plastic bucket manufacturing
- Plastic chair making machine
- plastic forming equipment
- plastic hopper dryer
- plastic injection machine
- plastic injection machines
- plastic injection molding
- Plastic injection molding equipment
- Plastic injection molding machine
- Plastic Injection Molding Machines
- plastic injection robot
- Plastic Molding machine
- Plastic Molding Machines
- plastic molding press
- plastic phone case making machine
- plastic-molding machine
- powerful granulator
- Powerful Type Sound-Proof Granulator
- production of plastic seats
- Robot injection molding
- robot injection molding machine
- robot manufacturing companies
- Robotic arm for injection molding machine
- robotic injection molding machines
- robotics in injection molding
- SCARA robot
- SCARA robots
- Service-oriented manufacturing
- Servo Cylinder Robot
- servo driven robot
- Servo Driven Robots
- servo injection robots
- Servo-Driven Robot
- Setup of injection machine
- Silicone Injection Molding Machine
- six-axis industrial robot
- Stainless Hopper Dryer
- Stainless Hopper Dryers
- star club
- swing arm robot
- the choice between servo-driven robots and hydraulic robots will have a certain impact on efficiency
- the most popular injection molding machine
- the type of injection molding robot
- toggle clamp injection molding machine
- Toggle Hydraulic Injection Molding Machines
- toggle injection molding machine
- Top 10 brands of injection robots
- Topstar
- Topstar Engineering
- Topstar Industrial Robots
- Topstar injection molding intelligent
- Topstar Scara Robots
- Useful Injection molding machine
- Vertical machining centers
- volumetric type blender
- water chiller
- water chillers
- water distributor
- Water Type MoldTemperature Controller
- We often face choices when performing injection molding. We will choose the type of injection molding machine
- wholesale of injection molding machines
- x carve CNC