How to solve the problem of excessive vibration of injection molding robot?
2025/04/09 By Topstar
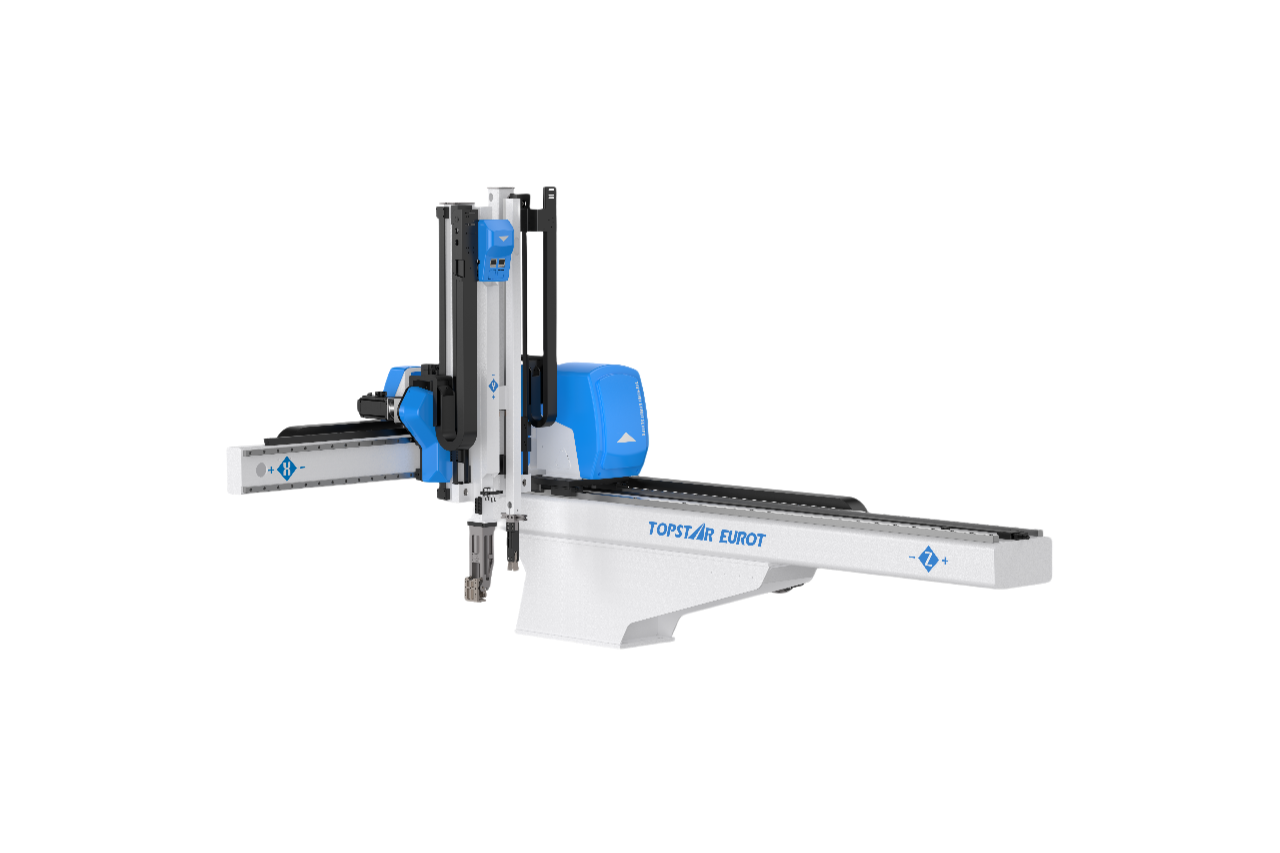
Injection molding robots can achieve efficient operation, high-precision grasping, and other tasks in injection molding. Suppose your injection molding robot is not installed firmly, or the overall design is imperfect during molding. In that case, excessive vibration will occur, resulting in inaccurate grasping, affecting product quality, shortening machine life, and ultimately affecting overall productivity. This guide will list the common causes of vibration in injection molding robots and explain how to solve them on Topstar’s robots to avoid excessive vibration and improve operating performance.
Ensure the stable installation and hardware integrity of injection molding robot.
First, let’s start with installation. The main reason for the excessive vibration of injection molding robots may be unstable installation. During the installation process, all mounting devices must be thoroughly fixed, and screws and bolts must be tightened according to the specifications provided by the manufacturer. Any loose connection or insufficient tightening will aggravate vibration and cause misalignment during high-speed operation. At the same time, it is also necessary to ensure the correct alignment of the robot with the injection molding machine. If there is misalignment, it will also increase mechanical stress and cause uneven loads, thereby aggravating vibration. Meticulous attention to detail is required during the installation stage. Stable installation involves choosing a suitable foundation and regularly checking for any looseness – especially in high-vibration environments. Operators must periodically check fasteners and mounting hardware for signs of wear or looseness. By ensuring the injection molding robot is securely fixed.
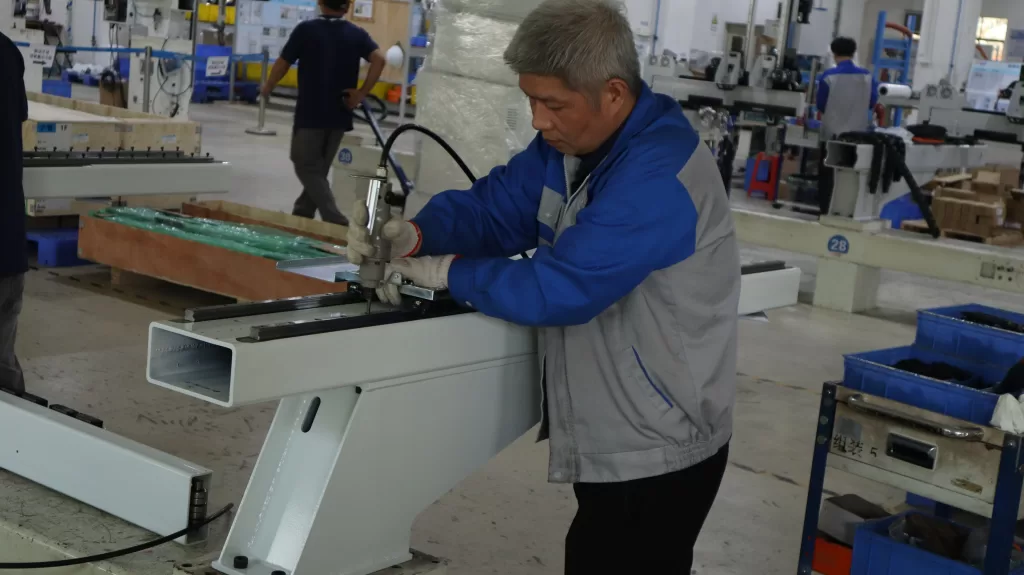
Vibration Suppression Technology
Topstar’s Euro series injection molding robots are ideal for high-precision take-out molding. A standout feature of these models is the integrated vibration suppression function, designed for operations that require precise removal. This advanced technology actively monitors and adjusts the robot’s real-time trajectory and movement to counteract any unexpected vibrations.
The vibration suppression function combines sensor data and dynamic control algorithms. These systems continuously analyze mechanical vibrations during operation and adjust the injection molding robot’s movement path instantly. The result is a smoother, more consistent performance with minimized vibration, critical to maintaining high product quality. Field tests have shown that the European series can reduce the vibration amplitude of the end effector by 60-75% when retrieving small precision parts compared to traditional robots. It also works seamlessly with various end effector tool configurations and automatically adapts to different payload weights.
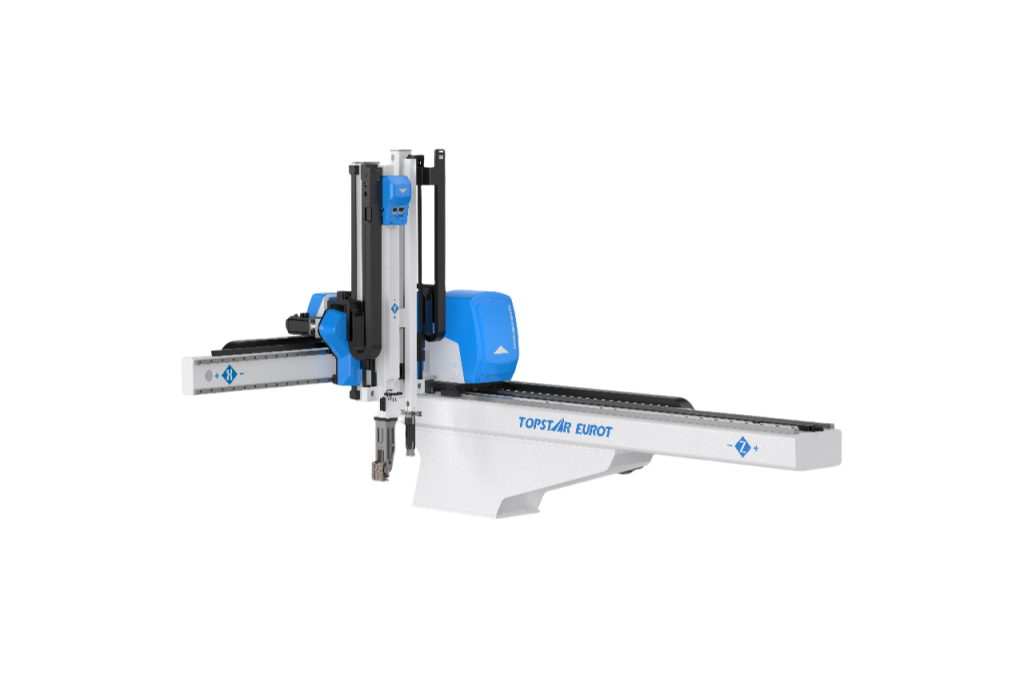
Leveraging Lightweight A6061 Material
To improve overall performance and reduce excessive vibration, the entire main arm of these machines is made of lightweight, high-strength A6061 material. First, the lightweight of the A6061 material minimizes stress on mechanical components during rapid acceleration and deceleration, which can be a significant source of vibration. Second, its high strength ensures that the injection molding robot maintains structural integrity and performance stability even under heavy loads. Reducing mechanical stress reduces vibration and enables precise control, especially when performing delicate operations such as high-precision insert molding. In addition, using A6061 material enhances the robot’s overall responsiveness. The lighter main arm can move faster and more accurately, ensuring the automated process is efficient and consistent. Combined with advanced vibration suppression, a rugged, reliable gripping system provides excellent operating performance.
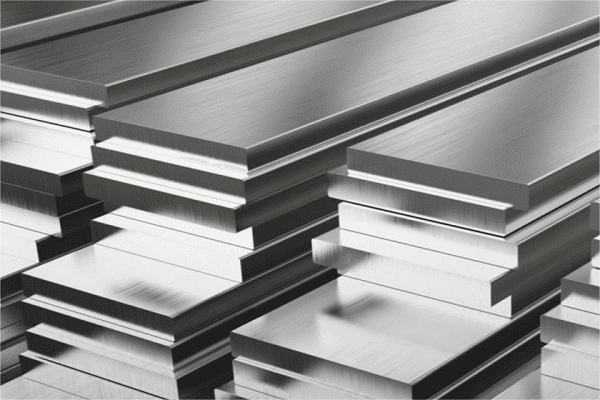
Optimizing Motion Parameters
Proper injection molding robot motion profile programming can significantly affect the vibration level. Avoid using abrupt acceleration/deceleration settings that produce mechanical shocks, and instead use an S-curve acceleration profile to accelerate and decelerate smoothly. Topstar’s programming software includes a built-in optimization wizard that automatically calculates ideal motion parameters based on payload weight, arms reach, and desired cycle time. Consider slightly increasing non-productive move time for vibration-sensitive applications to allow smoother transitions between positions. Many users have found that reducing maximum speed by 5-10% can minimize vibration amplitude by 30% or more with minimal impact on overall cycle time. Fine-tuning these parameters improves performance during high-speed operation and ensures the life and reliability of mechanical components.
Injection Molding Robot End-of-Arm Tooling Considerations
The tools mounted on the injection molding robot can significantly affect vibration characteristics. Make sure the gripper and other end effectors are correctly balanced. Unbalanced tools can generate centrifugal forces that cause vibration, especially when rotating at high speeds. Topstar offers dynamically balanced accessory options with adjustable counterweights for perfect mass distribution. When using suction cup arrays, symmetrically distribute vacuum lines to prevent uneven force distribution. Topstar uses large-bore cylinders for heavy tools to increase thrust and load by 20%, making it easy to handle large parts.
Solving Excessive Vibration with a Comprehensive Solution
Solving vibration in injection molding robots requires a comprehensive approach that combines proper installation, advanced vibration suppression, and high-strength A6061 materials. Manufacturers can significantly reduce unwanted vibrations and improve overall performance during the injection molding process. With the onboard proprietary control system, fine-tuning some operating parameters can further promote a robust and reliable injection molding process.
TRENDING POSTS
- What factors can cause delays in the injection molding process of plastic molding machine? 2025/04/09
- Exhibition Review| Topstar participates in InterPlas Thailand 2024 2025/04/09
- Star Case | Topstar helps Santong upgrade its intelligent plant 2025/04/09
- Topstar Special | National Science and Technology Workers Day 2025/04/09
HOT TOPIC
- 3 in 1 Compact Dehumidifying Dryer
- 5-axis CNC machine
- accuracy
- Air Chillers
- all electric injection molding machine
- All-electric injection molding machines
- and overall production quality. Therefore
- AP-RubberPlas
- automated injection molding machine
- Automation changed engineering
- automation of injection molding robots
- auxiliary machine
- Bench Injection Molding Machine
- Cabinet dryer manufacturers
- Cabinet dryers
- chiller
- CNC Drilling Machine
- CNC Drilling Machines
- cnc engraving machine manufacturer
- cnc laser cutting machine manufacturer
- CNC machine
- CNC Machine Center
- CNC Machine for Sale
- CNC Machine Manufacturing
- CNC Machine Tool
- CNC machine tool product
- CNC Machining Center
- CNC wood carving machine
- Cooling system
- Cross-Walking Single Axis Servo Cylinder Robot
- Cross-Walking Single-Axis Servo Cylinder Robot
- Cross-Walking Three-Axis/Five-Axis Servo Driven Robot
- cross-walking three-axis/five-axis servo-driven robot
- Dehumidifier Dryer
- Dehumidifying Dryer
- delta parallel robot
- Desktop Injection Molding Machine
- Desktop injection molding machines
- Desktop Molding Machine
- desktop plastic injection machine
- Desktop Plastic Injection Molding Machine
- direct clamp injection molding machine
- Direct clamp injection molding machines
- Dosing & mixing system
- Drilling Centers
- Drying and dehumidification system
- drying and dehumidifying equipment
- Drying and Dehumidifying System
- drying system
- effective and efficient. Cabinet dryers are also used in other industries where large quantities of material need to be dried
- efficient injection molding machine
- elbow hydraulic injection molding machines
- electric injection molding machine
- electric injection molding machines
- etc. Among injection molding robots
- exhibition
- features of CNC machine
- Feeding And Conveying System
- Five Axis Machine Center
- Fully automatic injection molding machine
- Gathering Topstar
- giant injection molding machine
- GMU-600 5-Axis Machining Center
- Granulating & Recycling System
- Heavy duty injection molding machine
- Honeycomb rotor dehumidifier
- horizontal injection molding machine
- Horizontal Injection Molding Machines
- Horizontal Injection Moulding Machine
- Horizontal Mixer manufacturer
- How The CNC Machine Works
- hybrid injection molding machine
- hydraulic injection molding machine
- Hydraulic Injection Molding Machines
- in this article
- Industrial robot
- Industrial Robot Chinese brand
- industrial robot parts
- industrial robot supplier
- Industrial robots
- Industry Chain
- Injection Manipulator
- injection mold machines
- Injection molding
- Injection molding automation
- Injection Molding Automation Solution
- injection molding dryer
- Injection molding equipment
- injection molding hopper dryer
- Injection molding machine
- injection molding machine brand
- Injection Molding Machine Factory
- Injection Molding Machine Manufacture
- Injection molding machine manufacturer
- injection molding machine manufacturers
- Injection molding machine procurement
- injection molding machine robotic arm
- injection molding machine with a robot
- Injection molding machines
- injection molding material dehumidifying
- injection molding plant
- Injection Molding Robot
- injection molding robot arm
- Injection molding robot automation
- Injection molding robotic arm
- injection molding robots
- Injection Moulding Robots
- Injection Robot
- Injection robot arm
- Injection robot manufacturer
- Injection robot wholesale
- injection robots
- intelligent injection molding machines
- Introducing Injection Robot
- It is the best choice for drying large quantities of material at once. Cabinetmakers use these machines because they are fast
- large injection molding machine
- Learn what industrial automation and robotics is
- low speed sound-proof granulator
- machine plastic molding
- make sure to add some! Improvements (2) Keyphrase in introduction: Your keyphrase or its synonyms appear in the first paragraph of the copy
- manipulator machine
- manufacturing
- micro injection molding machine
- middle speed granulator
- Mini CNC machine manufacturers.
- Mold Temperature Control System
- mold temperature controller
- molding material Dehumidifying System
- mould temperature controller
- mould temperature controllers
- New electric injection molding machine
- nitrogen dryer manufacturer
- nitrogen dryer system manufacturer
- Oil type mold temperature controller
- open day
- Outbound links: No outbound links appear in this page. Add some! Images: No images appear on this page. Add some! Internal links: No internal links appear in this page
- PET Preform injection molding
- phone case maker machine
- phone case making machine
- plastic bottle making machine
- plastic bottle manufacturing
- plastic bucket making machine
- plastic bucket manufacturing
- Plastic chair making machine
- plastic forming equipment
- plastic hopper dryer
- plastic injection machine
- plastic injection machines
- plastic injection molding
- Plastic injection molding equipment
- Plastic injection molding machine
- Plastic Injection Molding Machines
- plastic injection robot
- Plastic Molding machine
- Plastic Molding Machines
- plastic molding press
- plastic phone case making machine
- plastic-molding machine
- powerful granulator
- Powerful Type Sound-Proof Granulator
- production of plastic seats
- Robot injection molding
- robot injection molding machine
- robot manufacturing companies
- Robotic arm for injection molding machine
- robotic injection molding machines
- robotics in injection molding
- SCARA robot
- SCARA robots
- Service-oriented manufacturing
- Servo Cylinder Robot
- servo driven robot
- Servo Driven Robots
- servo injection robots
- Servo-Driven Robot
- Setup of injection machine
- Silicone Injection Molding Machine
- six-axis industrial robot
- Stainless Hopper Dryer
- Stainless Hopper Dryers
- star club
- swing arm robot
- the choice between servo-driven robots and hydraulic robots will have a certain impact on efficiency
- the most popular injection molding machine
- the type of injection molding robot
- toggle clamp injection molding machine
- Toggle Hydraulic Injection Molding Machines
- toggle injection molding machine
- Top 10 brands of injection robots
- Topstar
- Topstar Engineering
- Topstar Industrial Robots
- Topstar injection molding intelligent
- Topstar Scara Robots
- Useful Injection molding machine
- Vertical machining centers
- volumetric type blender
- water chiller
- water chillers
- water distributor
- Water Type MoldTemperature Controller
- We often face choices when performing injection molding. We will choose the type of injection molding machine
- wholesale of injection molding machines
- x carve CNC