How to select the right injection speed for a hydraulic injection molding machine?
2024/09/02 By Topstar
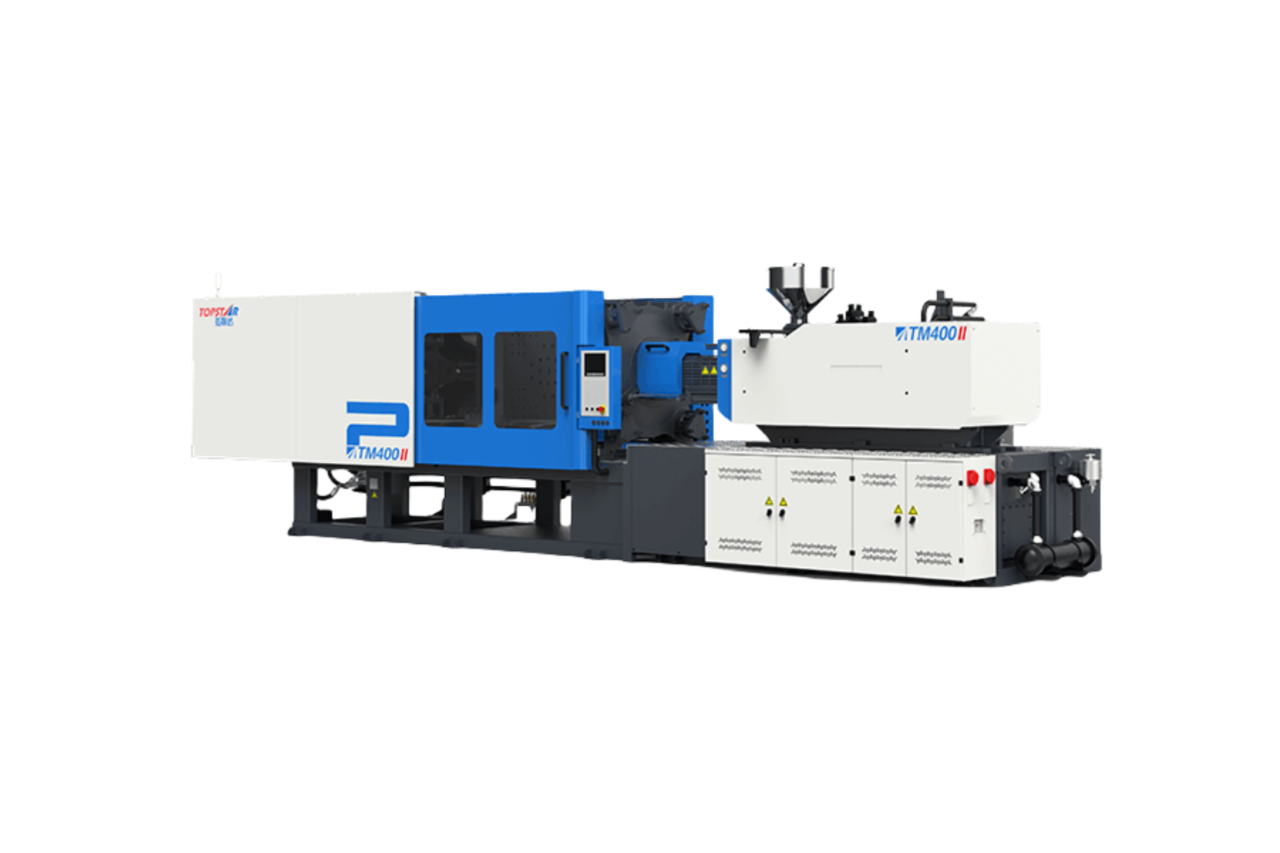
The correct injection speed in the process of injection molding can ensure the quality and efficiency of the production process. The injection speed determines the speed at which the molten plastic is injected into the mold, and plays a key role in the final characteristics of the molded part. Injection speed is also a parameter we must consider when selecting injection molding machines. In this article, we will provide you with the process of choosing the appropriate injection speed for a hydraulic injection molding machine and let you know more about the injection part of the hydraulic injection molding machine.
The importance of injection speed in hydraulic injection molding machine
The injection speed in hydraulic injection molding machines is not just a parameter. It is also a key factor affecting the quality of the final product. The injection speed refers to the speed at which the screw or plunger moves during injection. The faster the speed, the shorter the time required to complete an injection stroke, and the greater the output. By setting the filling speed near the gate, in the body, and at the end of the flow and adjusting the corresponding injection position, you can produce products with a good appearance and less internal stress.
-1024x573.png)
It affects several key aspects of the molding process, including the flow of molten plastic, the filling of the mold cavity, the cooling time, and the total cycle time. The correct injection speed helps to achieve uniform part quality and reduce defects such as dents or welds. In a hydraulic injection molding machine, the injection speed is controlled by adjusting the flow rate of the hydraulic oil, thereby controlling the movement of the injection screw. Injection speed depends on several factors, including the type of plastic, the geometry of the mold, and the product requirements.
Effect of Mold Geometry on Injection Speed Setting
Mold geometry includes the shape, size, and complexity of the mold cavity and features such as thin walls, ribs, and intricate details. These geometric features directly affect how molten material flows into the mold. Thin-walled mold sections require higher injection speeds, and thick-walled parts require a slow-fast-slow speed profile to avoid defects. Setting the injection speed balances the need for fast filling and prevents defects. This balance is achieved by considering the specific geometry of the mold. A multi-step injection speed profile is required for complex molds with varying wall thicknesses, and the speed varies throughout the injection process.
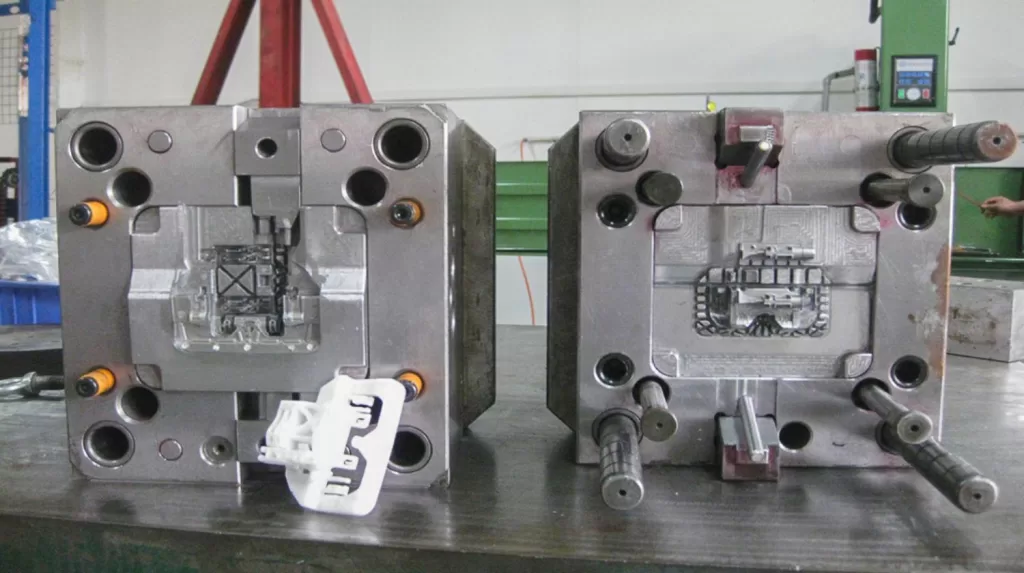
Multi-stage injection speed
Multi-stage injection speed refers to the ability of the hydraulic injection molding machine to adjust the speed of the injection piston or screw in multiple stages throughout the injection process. Unlike a single-speed injection system, the molten plastic is injected into the mold cavity at a constant speed, and multi-stage speed allows different speeds to be used at various points in the process.
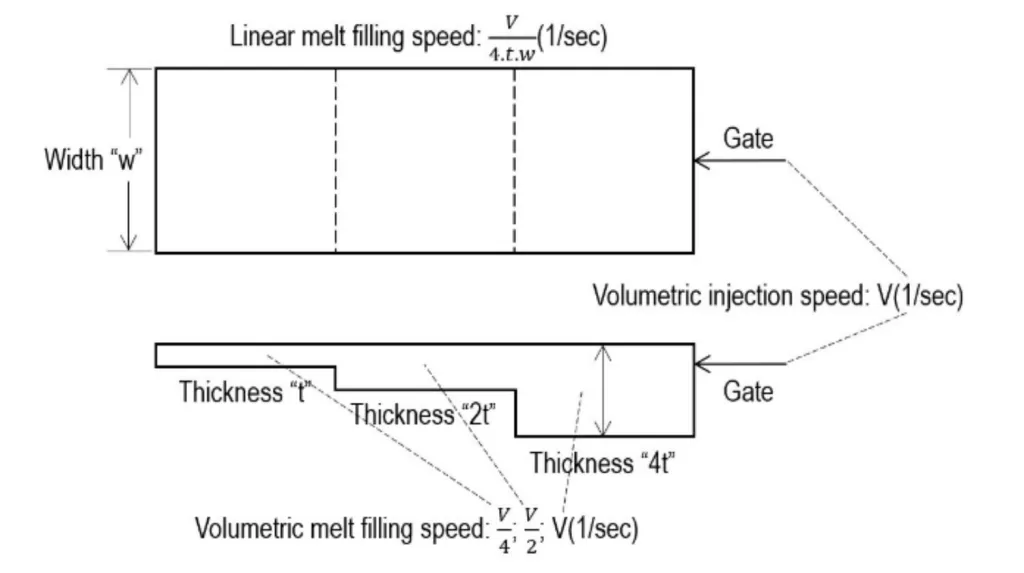
The injection process can be divided into several stages (three stages, as an example). Each stage can have different speed settings, allowing precise control over how the molten plastic is injected:
Initial injection stage: During this stage, higher speeds can quickly fill most of the mold cavity, reducing cycle time and ensuring that the plastic reaches all areas of the mold before it starts to cool.
Press holding stage: After the initial fill, the injection speed can be reduced by applying pressure gradually. Slower speeds help fill the molten plastic into all the intricate details of the mold, reducing the risk of defects such as sink marks.
Holding stage: Once the mold cavity is filled and compacted, the speed is further reduced to maintain pressure. At the same time, the plastic cools and solidifies, allowing the final product to keep its intended shape and size.
What are the characteristics of high and low injection speeds?
High injection speed
- Faster filling time:
It can fill the mold cavity faster, especially for large parts or molds with complex geometries. Faster filling time helps to reduce cycle time and improve the overall productivity of the molding process. - Reduce viscosity:
When you inject plastic at high speed, the shear rate increases, temporarily decreasing viscosity. This reduction makes it easier for the molten material to flow into the mold and fill intricate details and thin walls more effectively. - Potential for defects:
While high injection speeds can improve filling and cycle times, they also increase the risk of certain defects. For example, high speeds can cause jetting. Plastic enters the mold too quickly and forms a serpentine pattern. In addition, high speeds can cause increased internal stress in the material, resulting in warping, sink marks, or internal voids. - Enhanced surface finish:
In some cases, high injection speeds can help the material reach and fill the fine details of the mold before it cools, thereby improving the surface finish of the molded part.
Low Injection Speed
- Controlled Filling Process:
Lower injection speeds allow for a more controlled and progressive filling of the mold cavity, ensuring that the material flows evenly into all areas of the mold, reducing the possibility of air pockets and voids. - Reduced Shear Stress:
Lower speeds reduce the shear rate, which minimizes the stresses on the material during the injection process. Reduced stress helps maintain the material’s properties and can result in better dimensional stability in the final part. - Improved Part Quality:
Infection defects such as burn marks, flow lines, and welds can be minimized by reducing the injection speed. These defects can occur when material enters the die too quickly, causing turbulence and improper fusion. - Increased Cycle Time:
The downside of low injection speeds is that they can increase cycle time. Since the mold fills more slowly, the total time required for each molding cycle increases.
How to choose the injection speed of hydraulic injection molding machine reasonably?
The type of plastic material used will affect the ideal injection speed. Materials such as polypropylene and polyethene generally benefit from higher injection speeds because they have lower viscosity and flow into the mold more easily. In contrast, more dense materials such as polycarbonate or nylon may require lower injection speeds. Always consider the material’s melt flow index (MFI); you should use slower speeds for materials with lower MFI and those with higher MFI.
As mentioned earlier, mold design must also be considered. Molds with intricate details, thin walls, or multiple cavities require slower and more controlled injection speeds. The surface finish required for the final product can also determine the injection speed. In a production environment that requires high-volume manufacturing, there is often pressure to use higher injection speeds to reduce cycle times. However, we must balance this with the need for consistent product quality.
Modern hydraulic injection molding machines (including Topstar’s TMll series) offer multi-level injection speed settings. This feature lets you use different speeds at various stages of the injection process.
By utilizing this feature, you can optimize the injection speed to suit the different stages of the process.
Master the Right Choice
By understanding the importance of injection speed and considering the key factors influencing its selection, you can achieve high-quality results while maintaining efficient production operations during injection molding. Ultimately, the goal is to find the injection speed that achieves the best balance between quality, efficiency, and cost. By optimizing the process and monitoring it in real time, you can ensure higher-quality injection molding work.
TRENDING POSTS
- What factors can cause delays in the injection molding process of plastic molding machine? 2024/09/02
- Exhibition Review| Topstar participates in InterPlas Thailand 2024 2024/09/02
- Star Case | Topstar helps Santong upgrade its intelligent plant 2024/09/02
- Topstar Special | National Science and Technology Workers Day 2024/09/02
HOT TOPIC
- 3 in 1 Compact Dehumidifying Dryer
- 5-axis CNC machine
- accuracy
- Air Chillers
- all electric injection molding machine
- All-electric injection molding machines
- and overall production quality. Therefore
- AP-RubberPlas
- automated injection molding machine
- Automation changed engineering
- automation of injection molding robots
- auxiliary machine
- Bench Injection Molding Machine
- Cabinet dryer manufacturers
- Cabinet dryers
- chiller
- CNC Drilling Machine
- CNC Drilling Machines
- cnc engraving machine manufacturer
- cnc laser cutting machine manufacturer
- CNC machine
- CNC Machine Center
- CNC Machine for Sale
- CNC Machine Manufacturing
- CNC Machine Tool
- CNC machine tool product
- CNC Machining Center
- CNC wood carving machine
- Cooling system
- Cross-Walking Single Axis Servo Cylinder Robot
- Cross-Walking Single-Axis Servo Cylinder Robot
- Cross-Walking Three-Axis/Five-Axis Servo Driven Robot
- cross-walking three-axis/five-axis servo-driven robot
- Dehumidifier Dryer
- Dehumidifying Dryer
- delta parallel robot
- Desktop Injection Molding Machine
- Desktop injection molding machines
- Desktop Molding Machine
- desktop plastic injection machine
- Desktop Plastic Injection Molding Machine
- direct clamp injection molding machine
- Direct clamp injection molding machines
- Dosing & mixing system
- Drilling Centers
- Drying and dehumidification system
- drying and dehumidifying equipment
- Drying and Dehumidifying System
- drying system
- effective and efficient. Cabinet dryers are also used in other industries where large quantities of material need to be dried
- efficient injection molding machine
- elbow hydraulic injection molding machines
- electric injection molding machine
- electric injection molding machines
- etc. Among injection molding robots
- exhibition
- features of CNC machine
- Feeding And Conveying System
- Five Axis Machine Center
- Fully automatic injection molding machine
- Gathering Topstar
- giant injection molding machine
- GMU-600 5-Axis Machining Center
- Granulating & Recycling System
- Heavy duty injection molding machine
- Honeycomb rotor dehumidifier
- horizontal injection molding machine
- Horizontal Injection Molding Machines
- Horizontal Injection Moulding Machine
- Horizontal Mixer manufacturer
- How The CNC Machine Works
- hybrid injection molding machine
- hydraulic injection molding machine
- Hydraulic Injection Molding Machines
- in this article
- Industrial robot
- Industrial Robot Chinese brand
- industrial robot parts
- industrial robot supplier
- Industrial robots
- Industry Chain
- Injection Manipulator
- injection mold machines
- Injection molding
- Injection molding automation
- Injection Molding Automation Solution
- injection molding dryer
- Injection molding equipment
- injection molding hopper dryer
- Injection molding machine
- injection molding machine brand
- Injection Molding Machine Factory
- Injection Molding Machine Manufacture
- Injection molding machine manufacturer
- injection molding machine manufacturers
- Injection molding machine procurement
- injection molding machine robotic arm
- injection molding machine with a robot
- Injection molding machines
- injection molding material dehumidifying
- injection molding plant
- Injection Molding Robot
- injection molding robot arm
- Injection molding robot automation
- Injection molding robotic arm
- injection molding robots
- Injection Moulding Robots
- Injection Robot
- Injection robot arm
- Injection robot manufacturer
- Injection robot wholesale
- injection robots
- intelligent injection molding machines
- Introducing Injection Robot
- It is the best choice for drying large quantities of material at once. Cabinetmakers use these machines because they are fast
- large injection molding machine
- Learn what industrial automation and robotics is
- low speed sound-proof granulator
- machine plastic molding
- make sure to add some! Improvements (2) Keyphrase in introduction: Your keyphrase or its synonyms appear in the first paragraph of the copy
- manipulator machine
- manufacturing
- micro injection molding machine
- middle speed granulator
- Mini CNC machine manufacturers.
- Mold Temperature Control System
- mold temperature controller
- molding material Dehumidifying System
- mould temperature controller
- mould temperature controllers
- New electric injection molding machine
- nitrogen dryer manufacturer
- nitrogen dryer system manufacturer
- Oil type mold temperature controller
- open day
- Outbound links: No outbound links appear in this page. Add some! Images: No images appear on this page. Add some! Internal links: No internal links appear in this page
- PET Preform injection molding
- phone case maker machine
- phone case making machine
- plastic bottle making machine
- plastic bottle manufacturing
- plastic bucket making machine
- plastic bucket manufacturing
- Plastic chair making machine
- plastic forming equipment
- plastic hopper dryer
- plastic injection machine
- plastic injection machines
- plastic injection molding
- Plastic injection molding equipment
- Plastic injection molding machine
- Plastic Injection Molding Machines
- plastic injection robot
- Plastic Molding machine
- Plastic Molding Machines
- plastic molding press
- plastic phone case making machine
- plastic-molding machine
- powerful granulator
- Powerful Type Sound-Proof Granulator
- production of plastic seats
- Robot injection molding
- robot injection molding machine
- robot manufacturing companies
- Robotic arm for injection molding machine
- robotic injection molding machines
- robotics in injection molding
- SCARA robot
- SCARA robots
- Service-oriented manufacturing
- Servo Cylinder Robot
- servo driven robot
- Servo Driven Robots
- servo injection robots
- Servo-Driven Robot
- Setup of injection machine
- Silicone Injection Molding Machine
- six-axis industrial robot
- Stainless Hopper Dryer
- Stainless Hopper Dryers
- star club
- swing arm robot
- the choice between servo-driven robots and hydraulic robots will have a certain impact on efficiency
- the most popular injection molding machine
- the type of injection molding robot
- toggle clamp injection molding machine
- Toggle Hydraulic Injection Molding Machines
- toggle injection molding machine
- Top 10 brands of injection robots
- Topstar
- Topstar Engineering
- Topstar Industrial Robots
- Topstar injection molding intelligent
- Topstar Scara Robots
- Useful Injection molding machine
- Vertical machining centers
- volumetric type blender
- water chiller
- water chillers
- water distributor
- Water Type MoldTemperature Controller
- We often face choices when performing injection molding. We will choose the type of injection molding machine
- wholesale of injection molding machines
- x carve CNC