How to run a plastic injection molding machine?
2024/06/05 By Topstar
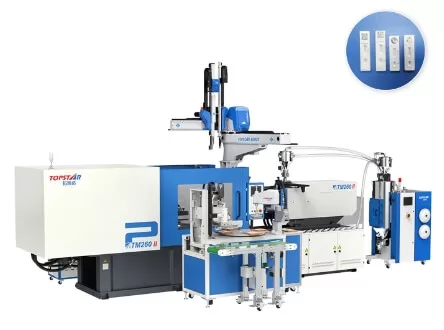
This guide can inspire and instruct manufacturers or operators unfamiliar with operating plastic injection molding machine. In this guide, divided into five parts, I will introduce you to how to operate plastic injection molding machines individually, taking you through some of the details and setup processes that need to be understood in detail to run these machines.
Getting Started: Setting Up Your Plastic Injection Molding Machine
You must set up your plastic injection molding machine correctly before running it. This is the stage when you have just received the machine and put it into production for the first time. First, you must ensure the machine is clean and has no material residue. Check the molds to ensure they are in good condition and installed correctly.
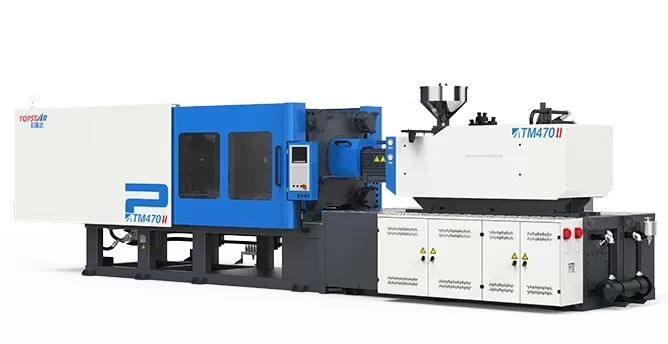
Next, check the hydraulic and electrical systems of the plastic injection molding machine. Ensure all connections are secure and there are no leaks in the hydraulic system. Verify that the power supply meets the machine’s requirements and that all safety mechanisms are in place. Check that the control panel of the machine is functioning as it should. And make sure that the connections with the surrounding injection molding robots and auxiliary equipment such as the mould temperature controller are normal. Load the appropriate type of plastic resin into the hopper. Once everything is ready, you can turn on the machine and start preheating the mold to the required temperature.
Programming the Plastic Injection Molding Machine
It’s time to program the plastic injection molding machine. You need to set the injection parameters, including injection speed, pressure, and time. You must adjust these parameters according to the type of plastic resin you are using and the complexity of the mold. The next step is to set the clamping force. The clamping device holds the two halves of the mold together during injection. Balance the force to avoid excess or insufficient amounts.
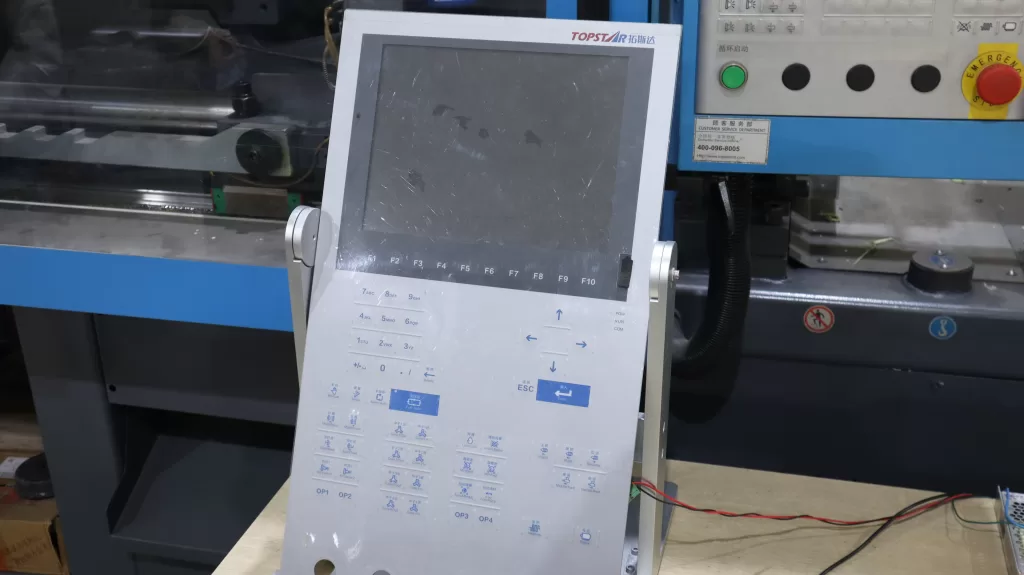
Then, the cooling time is set, determining how long the molded part stays in the mold to cool and solidify. Finally, the ejection system is programmed. The ejection parameters, including ejection speed and force, must be accurately set to avoid damaging the part or the mold. These related parameters can be set and operated through the control panel.
Monitor the Injection Process
As a plastic injection molding machine operator, you must observe the injection phase to ensure that the plastic resin flows smoothly into the mold cavity without interruptions, such as short shots or flashes. Keep a close eye on the pressure gauge and control panel. Pressure should remain within the set parameters throughout the injection molding process, and any major deviations may indicate a problem with the machine or material.
During the cooling phase, monitor cooling time and temperature to ensure that the part cools evenly. Uneven cooling can cause warping or other dimensional inaccuracies. Observe the ejection process to ensure that you eject the molded part smoothly without causing any damage. If the part sticks to the mold or shows signs of deformation, adjust the ejection parameters or apply a release agent.
Maintenance and troubleshooting
Modern plastic injection molding machines are basically perfect in function and mechanism and do not require much maintenance, but they still need regular maintenance occasionally. This also ensures that the plastic injection molding machine has a long service life and optimal performance. Daily life includes cleaning the machine, checking for leaks, and checking the mold for wear. Perform a more thorough monthly inspection of the hydraulic and electrical systems. Check the oil level and quality of the hydraulic oil, replace it if necessary, and calibrate the sensors and control system regularly.
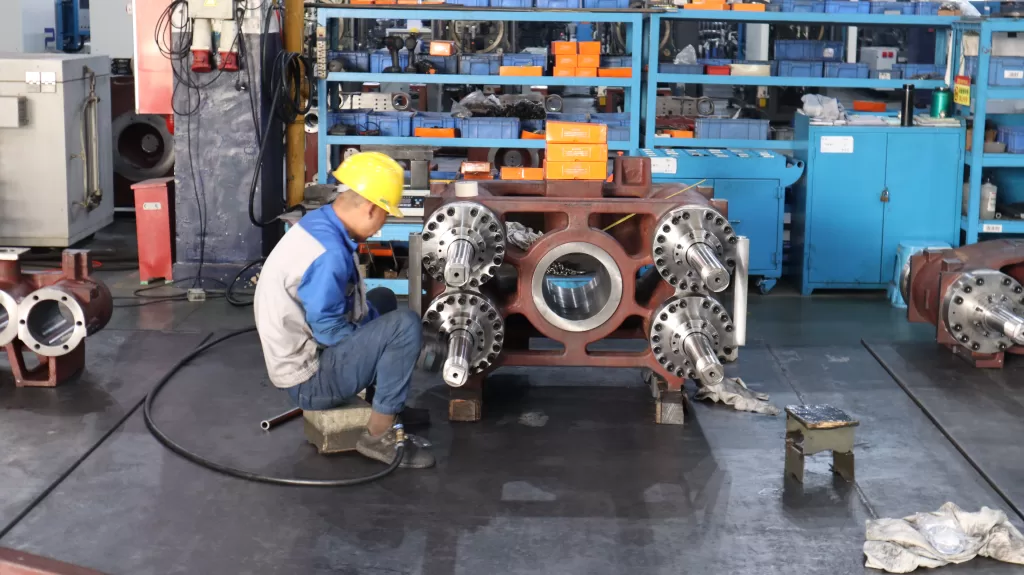
If some problems occur. Examples include inconsistent part quality, excessive burrs, or machine downtime. This could be related to machine setup, material, or mold. For example, a common problem of excessive flash could be caused by insufficient clamping force or damage to the mold surface. This problem can be solved by adjusting the clamping force or repairing the mold.
Optimize production efficiency
After setting up and monitoring the injection molding process, you can also optimize production efficiency, which is crucial to improving the output and profitability of plastic injection molding machines. In the series of plastic injection molding machines of Topstar, the comprehensive upgrade of the design of injection, clamping, hydraulic system, etc., has increased their overall efficiency by 15%, and they perform better when facing complex structures and specific materials. One way to improve efficiency is to optimize the cycle time. Reducing the cycle time without affecting product quality can significantly increase production. Try different parameters and settings to find the best cycle time for your specific application.
Master the best way to operate
Operating a plastic injection molding machine requires an understanding of its mechanics, setup, precise programming, and a focus on optimizing production efficiency. With the best practices outlined in the guide, you can ensure your machine operates optimally and efficiently in your daily production to provide high-quality products.
TRENDING POSTS
- What factors can cause delays in the injection molding process of plastic molding machine? 2024/06/05
- Exhibition Review| Topstar participates in InterPlas Thailand 2024 2024/06/05
- Star Case | Topstar helps Santong upgrade its intelligent plant 2024/06/05
- Topstar Special | National Science and Technology Workers Day 2024/06/05
HOT TOPIC
- .ervo motor-driven linear robots
- 3 axis robot
- 3 axis robots
- 3 in 1 Compact Dehumidifying Dryer
- 3-axis robot
- 3-axis robots
- 5-axis CNC machine
- accuracy
- Air Chillers
- all electric injection molding machine
- all electric injection molding machines
- All-electric injection molding machines
- and overall production quality. Therefore
- AP-RubberPlas
- automated injection molding machine
- Automation changed engineering
- automation of injection molding robots
- auxiliary machine
- Bench Injection Molding Machine
- Cabinet dryer manufacturers
- Cabinet dryers
- chiller
- CNC Drilling Machine
- CNC Drilling Machines
- cnc engraving machine manufacturer
- cnc laser cutting machine manufacturer
- CNC machine
- CNC Machine Center
- CNC Machine for Sale
- CNC Machine Manufacturing
- CNC Machine Tool
- CNC machine tool product
- CNC Machining Center
- CNC wood carving machine
- Cooling system
- Cross-Walking Single Axis Servo Cylinder Robot
- Cross-Walking Single-Axis Servo Cylinder Robot
- Cross-Walking Three-Axis/Five-Axis Servo Driven Robot
- cross-walking three-axis/five-axis servo-driven robot
- Dehumidifier Dryer
- Dehumidifying Dryer
- delta parallel robot
- Desktop Injection Molding Machine
- Desktop injection molding machines
- Desktop Molding Machine
- desktop plastic injection machine
- Desktop Plastic Injection Molding Machine
- direct clamp injection molding machine
- Direct clamp injection molding machines
- Dosing & mixing system
- Drilling Centers
- Drying and dehumidification system
- drying and dehumidifying equipment
- Drying and Dehumidifying System
- drying system
- effective and efficient. Cabinet dryers are also used in other industries where large quantities of material need to be dried
- efficient injection molding machine
- elbow hydraulic injection molding machines
- electric injection molding machine
- electric injection molding machines
- energy-efficient injection molding robot
- energy-saving injection molding machine
- etc. Among injection molding robots
- exhibition
- features of CNC machine
- Feeding And Conveying System
- Five Axis Machine Center
- Fully automatic injection molding machine
- Gathering Topstar
- giant injection molding machine
- GMU-600 5-Axis Machining Center
- Granulating & Recycling System
- Heavy duty injection molding machine
- High-precision electric molding machines
- high-precision plastic molding machines
- high-speed all electric injection molding machine
- Honeycomb rotor dehumidifier
- horizontal injection molding machine
- Horizontal Injection Molding Machines
- Horizontal Injection Moulding Machine
- Horizontal Mixer manufacturer
- How The CNC Machine Works
- hybrid injection molding machine
- hydraulic injection molding machine
- Hydraulic Injection Molding Machines
- in this article
- Industrial robot
- Industrial Robot Chinese brand
- industrial robot parts
- industrial robot supplier
- Industrial robots
- Industry Chain
- Injection Manipulator
- injection manipulator robot
- injection mold machines
- Injection molding
- Injection molding automation
- Injection Molding Automation Solution
- injection molding dryer
- Injection molding equipment
- injection molding hopper dryer
- Injection molding machine
- injection molding machine brand
- Injection Molding Machine Factory
- Injection Molding Machine Manufacture
- Injection molding machine manufacturer
- injection molding machine manufacturers
- Injection molding machine procurement
- injection molding machine robotic arm
- injection molding machine with a robot
- Injection molding machines
- injection molding material dehumidifying
- injection molding plant
- Injection Molding Robot
- injection molding robot arm
- Injection molding robot automation
- Injection molding robotic arm
- injection molding robots
- Injection moulding machine
- Injection Moulding Robots
- Injection Robot
- Injection robot arm
- Injection robot manufacturer
- Injection robot wholesale
- injection robots
- intelligent injection molding machines
- Introducing Injection Robot
- It is the best choice for drying large quantities of material at once. Cabinetmakers use these machines because they are fast
- large injection molding machine
- Learn what industrial automation and robotics is
- linear robot
- linear robots
- low speed sound-proof granulator
- machine plastic molding
- make sure to add some! Improvements (2) Keyphrase in introduction: Your keyphrase or its synonyms appear in the first paragraph of the copy
- manipulator machine
- manufacturing
- medical grade injection molding machines
- medical injection molding machine
- medical injection molding machines
- micro injection molding machine
- middle speed granulator
- Mini CNC machine manufacturers.
- Mold Temperature Control System
- mold temperature controller
- mold temperature controllers
- molding material Dehumidifying System
- mould temperature control system
- mould temperature controller
- mould temperature controllers
- New electric injection molding machine
- nitrogen dryer manufacturer
- nitrogen dryer system manufacturer
- Oil type mold temperature controller
- Oil type mold temperature controllers
- open day
- Outbound links: No outbound links appear in this page. Add some! Images: No images appear on this page. Add some! Internal links: No internal links appear in this page
- PET Preform injection molding
- phone case maker machine
- phone case making machine
- plastic bottle making machine
- plastic bottle manufacturing
- plastic bucket making machine
- plastic bucket manufacturing
- Plastic chair making machine
- plastic forming equipment
- plastic hopper dryer
- plastic injection machine
- plastic injection machines
- plastic injection molding
- Plastic injection molding equipment
- Plastic injection molding machine
- Plastic Injection Molding Machines
- plastic injection moulding machine
- plastic injection robot
- Plastic Molding machine
- Plastic Molding Machines
- plastic molding press
- plastic moulding machine
- plastic phone case making machine
- plastic-molding machine
- powerful granulator
- Powerful Type Sound-Proof Granulator
- precision injection molding
- precision injection molding machines
- production of plastic seats
- pure water mould temperature controller
- Robot injection molding
- robot injection molding machine
- robot manufacturing companies
- Robotic arm for injection molding machine
- robotic injection molding machines
- robotics in injection molding
- SCARA robot
- SCARA robots
- Service-oriented manufacturing
- Servo Cylinder Robot
- servo driven robot
- Servo Driven Robots
- servo injection robots
- servo motor-driven linear robots
- servo-driven 3-axis robot
- Servo-Driven Robot
- Setup of injection machine
- Silicone Injection Molding Machine
- six-axis industrial robot
- Stainless Hopper Dryer
- Stainless Hopper Dryers
- star club
- swing arm robot
- take-out robots
- the choice between servo-driven robots and hydraulic robots will have a certain impact on efficiency
- the most popular injection molding machine
- the type of injection molding robot
- toggle clamp injection molding machine
- Toggle Hydraulic Injection Molding Machines
- toggle injection molding machine
- Top 10 brands of injection robots
- Topstar
- Topstar Engineering
- Topstar Industrial Robots
- Topstar injection molding intelligent
- Topstar Scara Robots
- Useful Injection molding machine
- Vertical machining centers
- volumetric type blender
- water chiller
- water chillers
- water distributor
- water type mold temperature controller
- Water Type MoldTemperature Controller
- Water-Type Mould Temperature Controllers
- We often face choices when performing injection molding. We will choose the type of injection molding machine
- wholesale of injection molding machines
- x carve CNC