How to make injection molding easier through injection molding machines?
2024/11/04 By Topstar
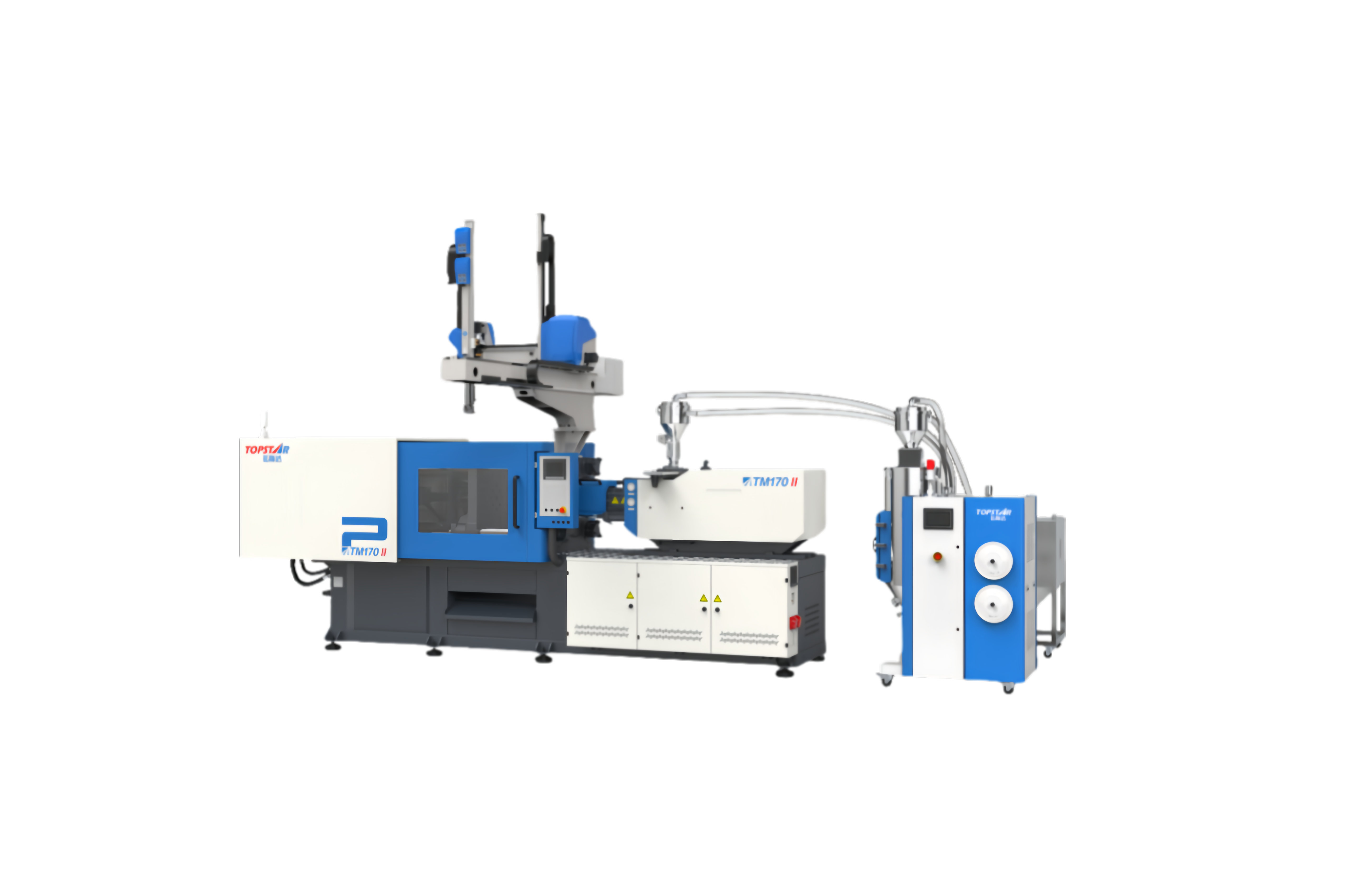
Faced with the changes in market demand for injection molding machines and the upgrade of injection molding, how to ensure the stability, quality, and delivery of equipment that customers care about, help customers optimize processes, improve manufacturing, and provide more reliable services, what unique value can Topstar provide to customers? Therefore, for single-machine equipment, we put forward the concept of intelligent equipment, give the customers upgrades in various application scenarios through open software control, and improve equipment performance through hardware core technology. The characteristics of injection molding are feeding automation, molding automation, removal automation, and whole factory modularization to improve injection molding efficiency for customers, thus proposing the product concept of a “processing all-in-one injection molding machine.”
What is an “injection molding processing all-in-one machine”?
When an enterprise puts injection molding into production, the equipment planning link is like assembling a computer. It is necessary to buy the monitor, motherboard, graphics card, etc. separately, and then connect them into a whole to achieve “start-up”. This is a complicated process that requires mastering the technology of various host and peripheral equipment from procurement to technology. This range is too wide and will affect the efficiency. Therefore, we introduced the product concept of an injection molding processing all-in-one machine, which we will implement in three stages: system connection, hardware integration, and process innovation. By diagnosing and configuring a system with integrated processes for customers, we enable the system to connect effectively. If it is an open system machine, it is easier and faster to achieve system connection. Therefore, we can also customize the design with customers in specific industries for the customer’s manufacturing process.
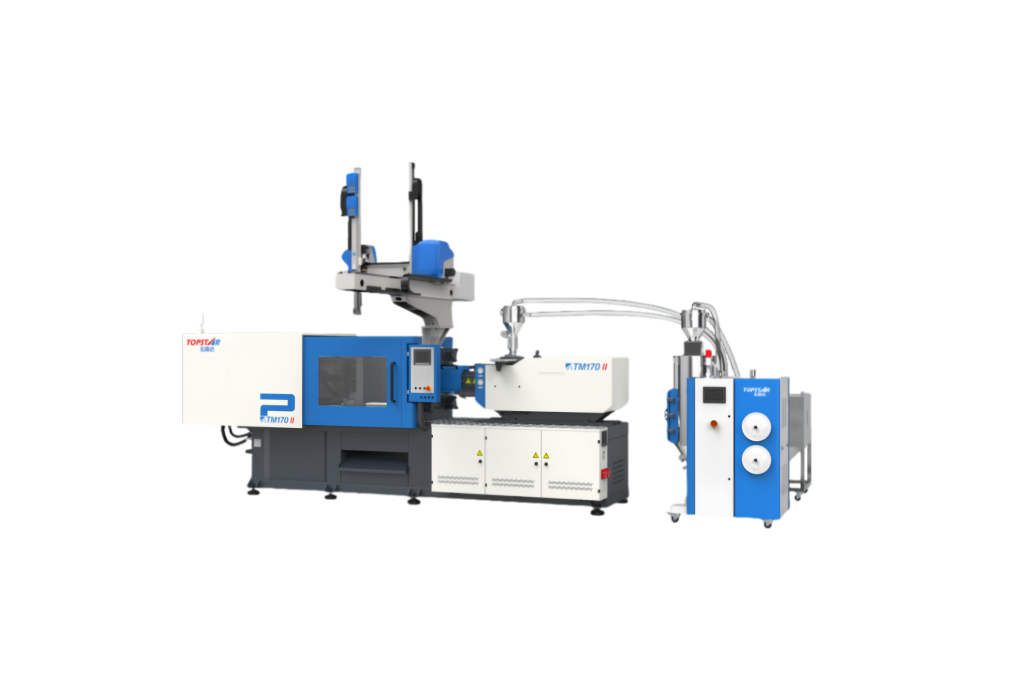
What is the difference between it and traditional injection molding machines?
The traditional injection molding machine is a mature mechanism. Each equipment manufacturer provides customers with overall services through an open communication interface. The technical division of labor usually maintains the advancement of each piece of equipment. However, each customer’s needs and usage scenarios differ, and traditional matching is like an independent individual. You need to equip it separately before connecting it into an intelligent whole. Such technology has high management and maintenance requirements, and it is difficult to coordinate between equipment. Topstar integrates multiple technologies. Through the self-developed control system, the communication between injection molding machines, auxiliary machines, and automated matching is realized, and the integrated control and hardware concept is launched. Based on the connection of the software system, a control interface is realized to link multiple devices, and the entire injection molding process is optimized, including injection molding pretreatment, plasticization, molding control, and removal.
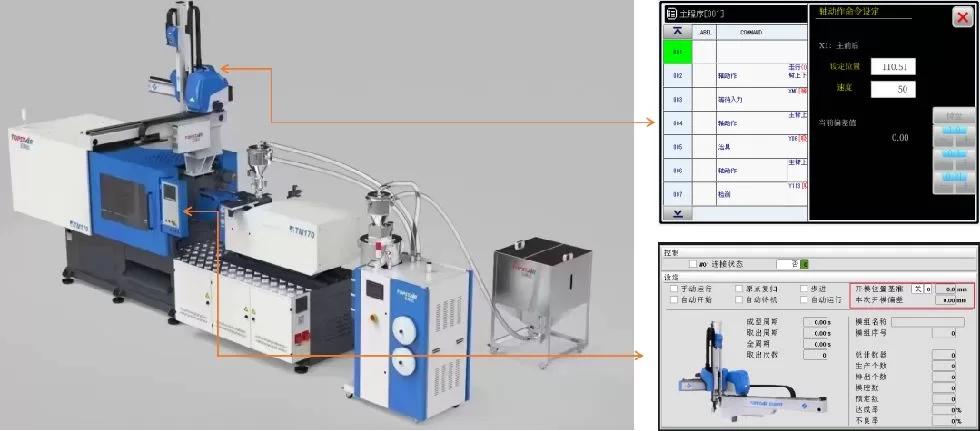
For customers, we will greatly improve compatibility, control capability, production stability, operation convenience, and maintenance simplicity, ensuring efficient production as the core guarantee. Of course, we will also analyze and diagnose customers’ production conditions and usage scenarios, including processing conditions, personnel skills, etc., to match you with the appropriate optimized equipment.
What production and operation problems can we solve?
First, operators’ workload on fine-tuning and monitoring injection molding machines and auxiliary equipment can be reduced through integrated control and process linkage, reducing labor costs and improving production efficiency. In this way, one operator can monitor and fine-tune multiple devices, reducing the labor input of multiple devices. Topstar calculates that after customers use the processing all-in-one injection molding machine, they need only 11 workers to complete the work previously, requiring at least 25 workers for 18 injection molding machines.
Secondly, the process machine realizes the synchronous linkage of the injection molding robot and the mold opening process, shortens the molding cycle, and improves production efficiency through early arrival and precision compensation functions. In addition, the open system adopted also provides space for the expansion and upgrading of equipment, making management easier.
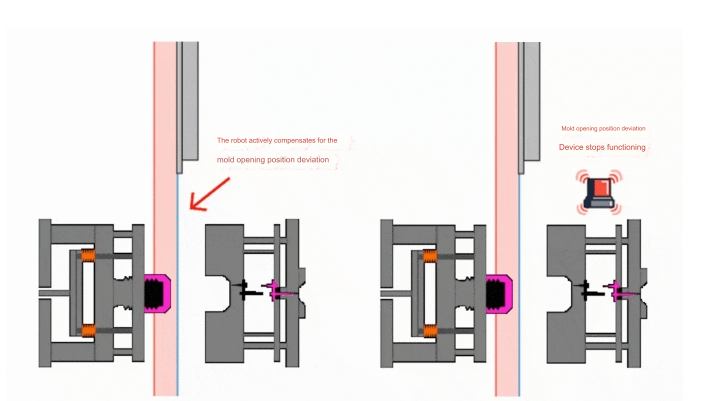
Bring the development of customized injection molding machine solutions
Topstar has a wealth of cases in customized applications and has developed and customized solutions in multiple industries. The processing all-in-one injection molding machine now successfully serves the 3C, auto parts, home appliances, and other industries.
In the auto parts industry, after customers used the processing all-in-one injection molding machine, the yield rate reached more than 95%, exceeding the expected 80%. At the same time, we shortened the molding cycle by 16 seconds and increased production efficiency by more than 20%. In the 3C industry, companies can reduce labor costs by 50% and increase production efficiency by more than 40%.
Impact on the injection molding industry?
Equipment intelligence is an area that the entire industry is working hard to expand, and it is also a trend of high-quality manufacturing. From the perspective of improving the production efficiency of enterprises, the processing all-in-one injection molding machine can greatly improve the efficiency of injection molding production by optimizing the injection molding process and realizing linkage control between processes. At the same time, it reduces manual operation and debugging time, and automation and precise control make the production process more stable and efficient, thereby shortening the production cycle, increasing production capacity, and reducing production costs.
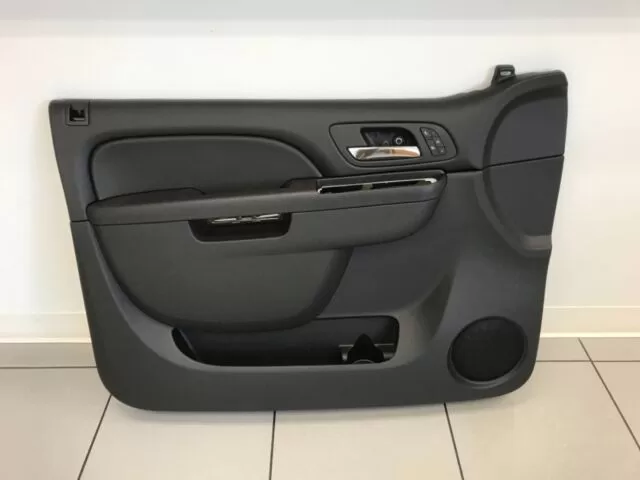
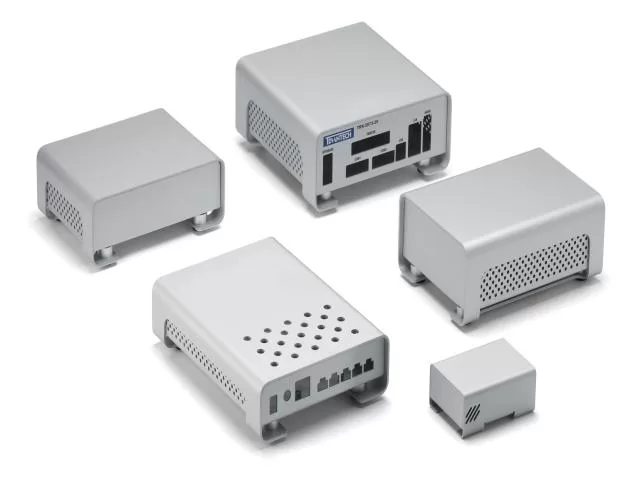
Integrated control and automation functions have relieved the difficulty of operation in terms of reducing labor costs. More efficient personnel input and less manual debugging time mean enterprises can rationally plan and allocate human resources, improve labor utilization, and save costs in personnel training.
Development and future prospects
The development of processing all-in-one injection molding machine technology is based on the upgrading of the underlying technology, diversification of application technology, and integration of injection molding processes. Topstar will develop in the direction of process cost reduction, intelligence, modularization, and efficiency. The continuous optimization and refined control of the process can further reduce production costs. Injection molding machines in the future will tend to be more intelligent and digital, achieving more efficient, precise, and sustainable production. At the same time, they will also adopt a more modular design and customize features according to customer needs.
TRENDING POSTS
- What factors can cause delays in the injection molding process of plastic molding machine? 2024/11/04
- Exhibition Review| Topstar participates in InterPlas Thailand 2024 2024/11/04
- Star Case | Topstar helps Santong upgrade its intelligent plant 2024/11/04
- Topstar Special | National Science and Technology Workers Day 2024/11/04
HOT TOPIC
- 3 in 1 Compact Dehumidifying Dryer
- 5-axis CNC machine
- accuracy
- Air Chillers
- all electric injection molding machine
- all electric injection molding machines
- All-electric injection molding machines
- and overall production quality. Therefore
- AP-RubberPlas
- automated injection molding machine
- Automation changed engineering
- automation of injection molding robots
- auxiliary machine
- Bench Injection Molding Machine
- Cabinet dryer manufacturers
- Cabinet dryers
- chiller
- CNC Drilling Machine
- CNC Drilling Machines
- cnc engraving machine manufacturer
- cnc laser cutting machine manufacturer
- CNC machine
- CNC Machine Center
- CNC Machine for Sale
- CNC Machine Manufacturing
- CNC Machine Tool
- CNC machine tool product
- CNC Machining Center
- CNC wood carving machine
- Cooling system
- Cross-Walking Single Axis Servo Cylinder Robot
- Cross-Walking Single-Axis Servo Cylinder Robot
- Cross-Walking Three-Axis/Five-Axis Servo Driven Robot
- cross-walking three-axis/five-axis servo-driven robot
- Dehumidifier Dryer
- Dehumidifying Dryer
- delta parallel robot
- Desktop Injection Molding Machine
- Desktop injection molding machines
- Desktop Molding Machine
- desktop plastic injection machine
- Desktop Plastic Injection Molding Machine
- direct clamp injection molding machine
- Direct clamp injection molding machines
- Dosing & mixing system
- Drilling Centers
- Drying and dehumidification system
- drying and dehumidifying equipment
- Drying and Dehumidifying System
- drying system
- effective and efficient. Cabinet dryers are also used in other industries where large quantities of material need to be dried
- efficient injection molding machine
- elbow hydraulic injection molding machines
- electric injection molding machine
- electric injection molding machines
- energy-saving injection molding machine
- etc. Among injection molding robots
- exhibition
- features of CNC machine
- Feeding And Conveying System
- Five Axis Machine Center
- Fully automatic injection molding machine
- Gathering Topstar
- giant injection molding machine
- GMU-600 5-Axis Machining Center
- Granulating & Recycling System
- Heavy duty injection molding machine
- Honeycomb rotor dehumidifier
- horizontal injection molding machine
- Horizontal Injection Molding Machines
- Horizontal Injection Moulding Machine
- Horizontal Mixer manufacturer
- How The CNC Machine Works
- hybrid injection molding machine
- hydraulic injection molding machine
- Hydraulic Injection Molding Machines
- in this article
- Industrial robot
- Industrial Robot Chinese brand
- industrial robot parts
- industrial robot supplier
- Industrial robots
- Industry Chain
- Injection Manipulator
- injection mold machines
- Injection molding
- Injection molding automation
- Injection Molding Automation Solution
- injection molding dryer
- Injection molding equipment
- injection molding hopper dryer
- Injection molding machine
- injection molding machine brand
- Injection Molding Machine Factory
- Injection Molding Machine Manufacture
- Injection molding machine manufacturer
- injection molding machine manufacturers
- Injection molding machine procurement
- injection molding machine robotic arm
- injection molding machine with a robot
- Injection molding machines
- injection molding material dehumidifying
- injection molding plant
- Injection Molding Robot
- injection molding robot arm
- Injection molding robot automation
- Injection molding robotic arm
- injection molding robots
- Injection Moulding Robots
- Injection Robot
- Injection robot arm
- Injection robot manufacturer
- Injection robot wholesale
- injection robots
- intelligent injection molding machines
- Introducing Injection Robot
- It is the best choice for drying large quantities of material at once. Cabinetmakers use these machines because they are fast
- large injection molding machine
- Learn what industrial automation and robotics is
- low speed sound-proof granulator
- machine plastic molding
- make sure to add some! Improvements (2) Keyphrase in introduction: Your keyphrase or its synonyms appear in the first paragraph of the copy
- manipulator machine
- manufacturing
- micro injection molding machine
- middle speed granulator
- Mini CNC machine manufacturers.
- Mold Temperature Control System
- mold temperature controller
- molding material Dehumidifying System
- mould temperature controller
- mould temperature controllers
- New electric injection molding machine
- nitrogen dryer manufacturer
- nitrogen dryer system manufacturer
- Oil type mold temperature controller
- open day
- Outbound links: No outbound links appear in this page. Add some! Images: No images appear on this page. Add some! Internal links: No internal links appear in this page
- PET Preform injection molding
- phone case maker machine
- phone case making machine
- plastic bottle making machine
- plastic bottle manufacturing
- plastic bucket making machine
- plastic bucket manufacturing
- Plastic chair making machine
- plastic forming equipment
- plastic hopper dryer
- plastic injection machine
- plastic injection machines
- plastic injection molding
- Plastic injection molding equipment
- Plastic injection molding machine
- Plastic Injection Molding Machines
- plastic injection robot
- Plastic Molding machine
- Plastic Molding Machines
- plastic molding press
- plastic phone case making machine
- plastic-molding machine
- powerful granulator
- Powerful Type Sound-Proof Granulator
- production of plastic seats
- Robot injection molding
- robot injection molding machine
- robot manufacturing companies
- Robotic arm for injection molding machine
- robotic injection molding machines
- robotics in injection molding
- SCARA robot
- SCARA robots
- Service-oriented manufacturing
- Servo Cylinder Robot
- servo driven robot
- Servo Driven Robots
- servo injection robots
- Servo-Driven Robot
- Setup of injection machine
- Silicone Injection Molding Machine
- six-axis industrial robot
- Stainless Hopper Dryer
- Stainless Hopper Dryers
- star club
- swing arm robot
- the choice between servo-driven robots and hydraulic robots will have a certain impact on efficiency
- the most popular injection molding machine
- the type of injection molding robot
- toggle clamp injection molding machine
- Toggle Hydraulic Injection Molding Machines
- toggle injection molding machine
- Top 10 brands of injection robots
- Topstar
- Topstar Engineering
- Topstar Industrial Robots
- Topstar injection molding intelligent
- Topstar Scara Robots
- Useful Injection molding machine
- Vertical machining centers
- volumetric type blender
- water chiller
- water chillers
- water distributor
- Water Type MoldTemperature Controller
- We often face choices when performing injection molding. We will choose the type of injection molding machine
- wholesale of injection molding machines
- x carve CNC