How to integrate mold temperature controller with existing system?
2024/10/30 By Topstar
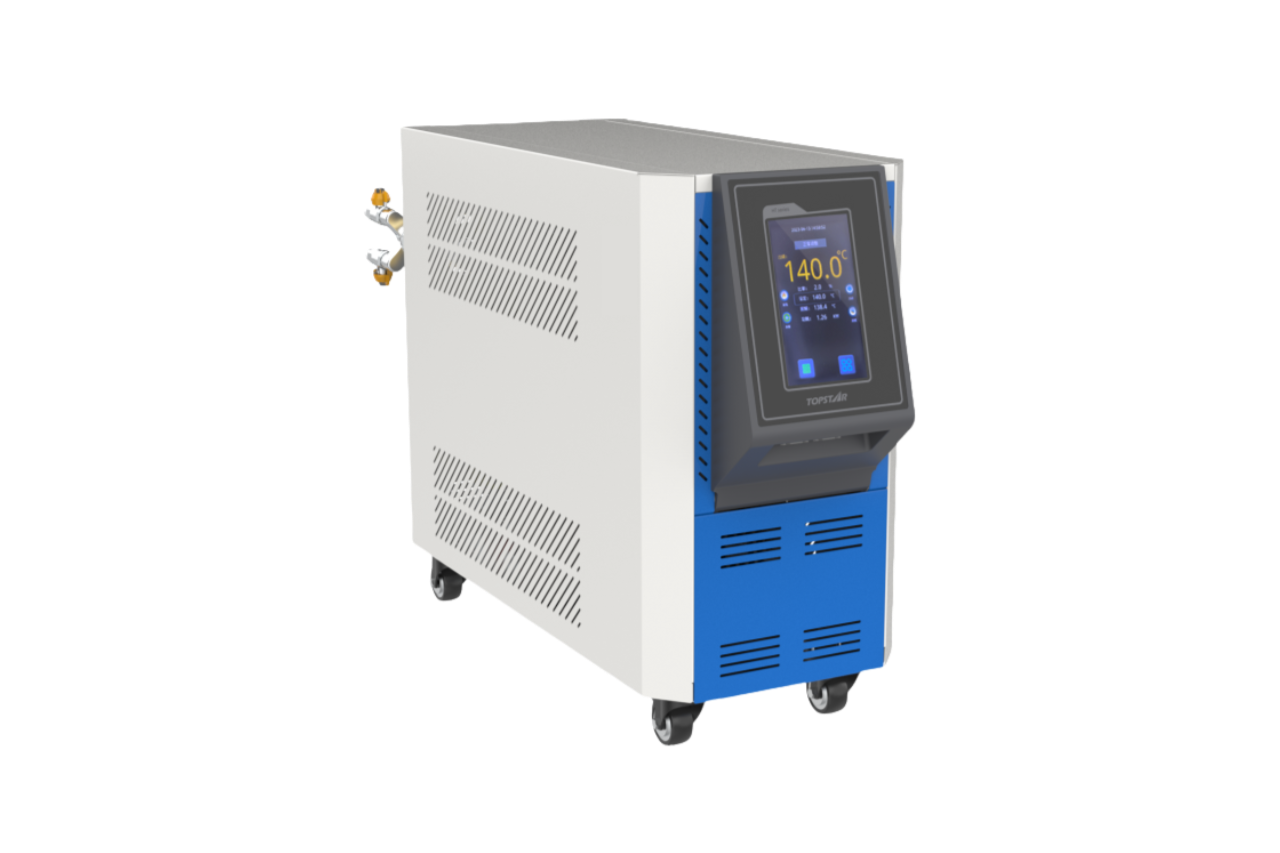
The right mold temperature is required to produce high-quality parts during the injection molding process. In injection molding equipment, mold temperature controllers can play a role in maintaining optimal temperature, directly affecting the quality of molded products. Some injection moulding workshops cannot integrate the mold temperature controller with the existing injection moulding system, making production management difficult, inflexible and inefficient. With the development of the manufacturing industry, everyone will pursue the integrity of the entire injection molding equipment system, so it is becoming more and more important to integrate mold temperature controllers into existing systems.
Evaluate the integration opportunities of mold temperature controllers with existing systems
The first step in integrating mold temperature controllers is to evaluate the existing system. This involves understanding the current setup, including the injection molding machine, heating system, and control interface. We need to understand the compatibility of the existing system with the existing equipment, the ability of the current system to handle additional components and any potential challenges that may arise during the integration process. In the injection molding solutions provided by Topstar, the mold temperature controller can be well-compatible with injection molding machines, auxiliary equipment, etc. The entire set of injection molding equipment adopts a unified communication language, and the open communication interface can achieve interconnection with other equipment, improve the collaborative efficiency of the entire production process, and optimize staffing to the greatest extent.
At the same time, the system automatically records the equipment operation status and alarm logs, improves the fault response speed and maintenance efficiency, and reduces downtime.
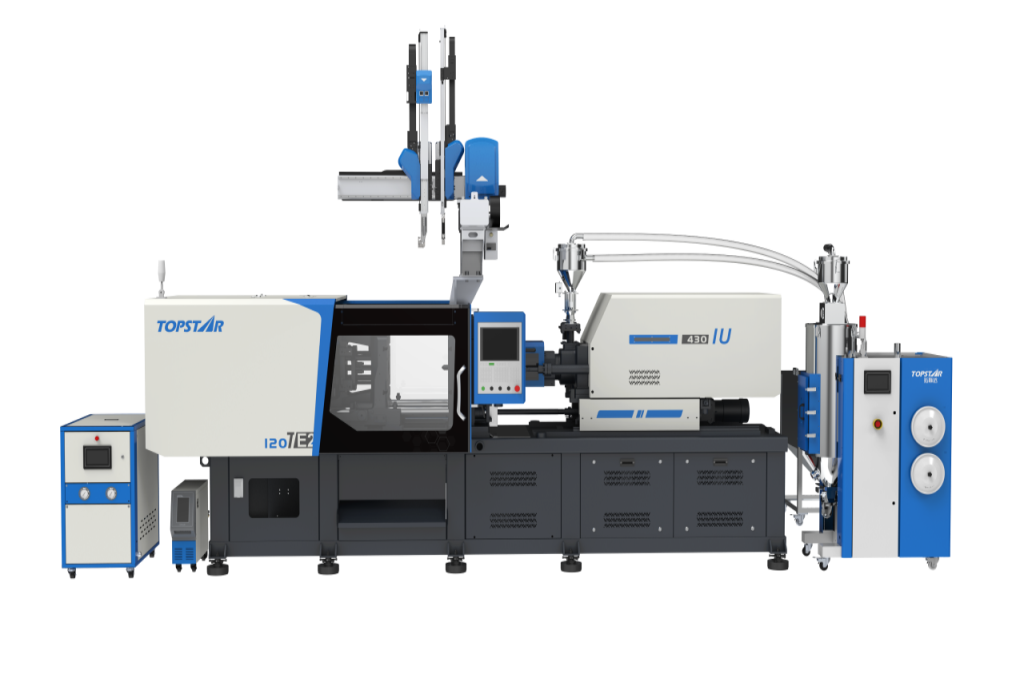
Choose the suitable mold temperature controller
Choosing the suitable mould temperature controller can effectively help integration. Different applications may require specific features and capabilities, so it is essential to consider the unique needs of the manufacturing process. Factors to consider include the temperature range, heating and cooling capacity, control accuracy, and response time of the MTC. Topstar’s fourth-generation mold temperature controller is divided into water-type mold temperature controller (120℃-180℃), oil-type mold temperature controller (200℃-320℃), heating power 8-36KW, water pump power 1-5HP, single-stage temperature control, and double-stage temperature control two series to choose from, a total of more than 60 products to meet the different working conditions of customers. Whether water-type or oil-type, it can be integrated to ensure your production process from raw materials to products.
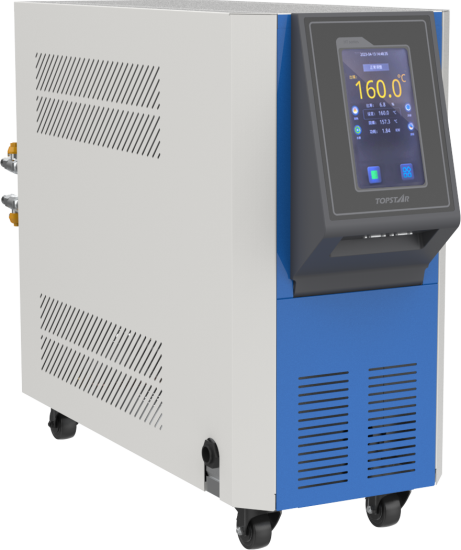
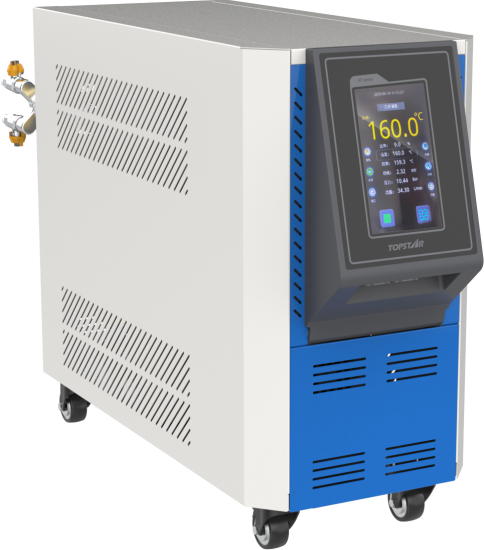
Plan the integration process of the mold temperature controller and system.
After you select the suitable mold temperature controller, the next step is to plan the integration process. Key elements of the integration plan should include determining where to install the mold temperature controller, preparing any necessary modifications to existing equipment, and arranging the installation process to align with the production schedule. Suppose you want to completely upgrade your existing injection molding workshop and transform it into a digital, automated, and intelligent workshop. In that case, Topstar can also provide you with a complete injection molding plant solution. Reasonably plan the location of each device and the placement of each production line for you, and realize the intelligent workshop with the integrated design of factory planning and system integration + injection molding automation production line + data management.
1-1024x682.webp)
Test and fine-tune the system
After installation and configuration, testing the integrated system is critical to ensure everything runs as expected. This testing phase should include running the injection molding process with the new mold temperature controller and monitoring the system performance in real-time. Observing how the MTC responds to temperature changes and whether it remains stable throughout the production cycle is critical. During the testing process, we pay close attention to key performance indicators such as temperature accuracy, response time, and the overall quality of the molded parts. Therefore, you should note any deviations from expected performance and may need to adjust the MTC settings to fine-tune for optimal operation.
Make injection molding easier by integrating with existing systems.
For manufacturers seeking to enhance the injection molding process, it is essential to integrate mold temperature controllers with existing systems. Therefore, by understanding the benefits of temperature controllers, evaluating existing systems, selecting the right controllers, and effectively planning the integration process, you can achieve the best results in temperature management and ensure product quality.
TRENDING POSTS
- What factors can cause delays in the injection molding process of plastic molding machine? 2024/10/30
- Exhibition Review| Topstar participates in InterPlas Thailand 2024 2024/10/30
- Star Case | Topstar helps Santong upgrade its intelligent plant 2024/10/30
- Topstar Special | National Science and Technology Workers Day 2024/10/30
HOT TOPIC
- 3 in 1 Compact Dehumidifying Dryer
- 5-axis CNC machine
- accuracy
- Air Chillers
- all electric injection molding machine
- All-electric injection molding machines
- and overall production quality. Therefore
- AP-RubberPlas
- automated injection molding machine
- Automation changed engineering
- automation of injection molding robots
- auxiliary machine
- Bench Injection Molding Machine
- Cabinet dryer manufacturers
- Cabinet dryers
- chiller
- CNC Drilling Machine
- CNC Drilling Machines
- cnc engraving machine manufacturer
- cnc laser cutting machine manufacturer
- CNC machine
- CNC Machine Center
- CNC Machine for Sale
- CNC Machine Manufacturing
- CNC Machine Tool
- CNC machine tool product
- CNC Machining Center
- CNC wood carving machine
- Cooling system
- Cross-Walking Single Axis Servo Cylinder Robot
- Cross-Walking Single-Axis Servo Cylinder Robot
- Cross-Walking Three-Axis/Five-Axis Servo Driven Robot
- cross-walking three-axis/five-axis servo-driven robot
- Dehumidifier Dryer
- Dehumidifying Dryer
- delta parallel robot
- Desktop Injection Molding Machine
- Desktop injection molding machines
- Desktop Molding Machine
- desktop plastic injection machine
- Desktop Plastic Injection Molding Machine
- direct clamp injection molding machine
- Direct clamp injection molding machines
- Dosing & mixing system
- Drilling Centers
- Drying and dehumidification system
- drying and dehumidifying equipment
- Drying and Dehumidifying System
- drying system
- effective and efficient. Cabinet dryers are also used in other industries where large quantities of material need to be dried
- efficient injection molding machine
- elbow hydraulic injection molding machines
- electric injection molding machine
- electric injection molding machines
- etc. Among injection molding robots
- exhibition
- features of CNC machine
- Feeding And Conveying System
- Five Axis Machine Center
- Fully automatic injection molding machine
- Gathering Topstar
- giant injection molding machine
- GMU-600 5-Axis Machining Center
- Granulating & Recycling System
- Heavy duty injection molding machine
- Honeycomb rotor dehumidifier
- horizontal injection molding machine
- Horizontal Injection Molding Machines
- Horizontal Injection Moulding Machine
- Horizontal Mixer manufacturer
- How The CNC Machine Works
- hybrid injection molding machine
- hydraulic injection molding machine
- Hydraulic Injection Molding Machines
- in this article
- Industrial robot
- Industrial Robot Chinese brand
- industrial robot parts
- industrial robot supplier
- Industrial robots
- Industry Chain
- Injection Manipulator
- injection mold machines
- Injection molding
- Injection molding automation
- Injection Molding Automation Solution
- injection molding dryer
- Injection molding equipment
- injection molding hopper dryer
- Injection molding machine
- injection molding machine brand
- Injection Molding Machine Factory
- Injection Molding Machine Manufacture
- Injection molding machine manufacturer
- injection molding machine manufacturers
- Injection molding machine procurement
- injection molding machine robotic arm
- injection molding machine with a robot
- Injection molding machines
- injection molding material dehumidifying
- injection molding plant
- Injection Molding Robot
- injection molding robot arm
- Injection molding robot automation
- Injection molding robotic arm
- injection molding robots
- Injection Moulding Robots
- Injection Robot
- Injection robot arm
- Injection robot manufacturer
- Injection robot wholesale
- injection robots
- intelligent injection molding machines
- Introducing Injection Robot
- It is the best choice for drying large quantities of material at once. Cabinetmakers use these machines because they are fast
- large injection molding machine
- Learn what industrial automation and robotics is
- low speed sound-proof granulator
- machine plastic molding
- make sure to add some! Improvements (2) Keyphrase in introduction: Your keyphrase or its synonyms appear in the first paragraph of the copy
- manipulator machine
- manufacturing
- micro injection molding machine
- middle speed granulator
- Mini CNC machine manufacturers.
- Mold Temperature Control System
- mold temperature controller
- molding material Dehumidifying System
- mould temperature controller
- mould temperature controllers
- New electric injection molding machine
- nitrogen dryer manufacturer
- nitrogen dryer system manufacturer
- Oil type mold temperature controller
- open day
- Outbound links: No outbound links appear in this page. Add some! Images: No images appear on this page. Add some! Internal links: No internal links appear in this page
- PET Preform injection molding
- phone case maker machine
- phone case making machine
- plastic bottle making machine
- plastic bottle manufacturing
- plastic bucket making machine
- plastic bucket manufacturing
- Plastic chair making machine
- plastic forming equipment
- plastic hopper dryer
- plastic injection machine
- plastic injection machines
- plastic injection molding
- Plastic injection molding equipment
- Plastic injection molding machine
- Plastic Injection Molding Machines
- plastic injection robot
- Plastic Molding machine
- Plastic Molding Machines
- plastic molding press
- plastic phone case making machine
- plastic-molding machine
- powerful granulator
- Powerful Type Sound-Proof Granulator
- production of plastic seats
- Robot injection molding
- robot injection molding machine
- robot manufacturing companies
- Robotic arm for injection molding machine
- robotic injection molding machines
- robotics in injection molding
- SCARA robot
- SCARA robots
- Service-oriented manufacturing
- Servo Cylinder Robot
- servo driven robot
- Servo Driven Robots
- servo injection robots
- Servo-Driven Robot
- Setup of injection machine
- Silicone Injection Molding Machine
- six-axis industrial robot
- Stainless Hopper Dryer
- Stainless Hopper Dryers
- star club
- swing arm robot
- the choice between servo-driven robots and hydraulic robots will have a certain impact on efficiency
- the most popular injection molding machine
- the type of injection molding robot
- toggle clamp injection molding machine
- Toggle Hydraulic Injection Molding Machines
- toggle injection molding machine
- Top 10 brands of injection robots
- Topstar
- Topstar Engineering
- Topstar Industrial Robots
- Topstar injection molding intelligent
- Topstar Scara Robots
- Useful Injection molding machine
- Vertical machining centers
- volumetric type blender
- water chiller
- water chillers
- water distributor
- Water Type MoldTemperature Controller
- We often face choices when performing injection molding. We will choose the type of injection molding machine
- wholesale of injection molding machines
- x carve CNC