How to Improve the Yield Rate of Injection Molded Parts by Cooling with a water chiller
2025/02/21 By Topstar
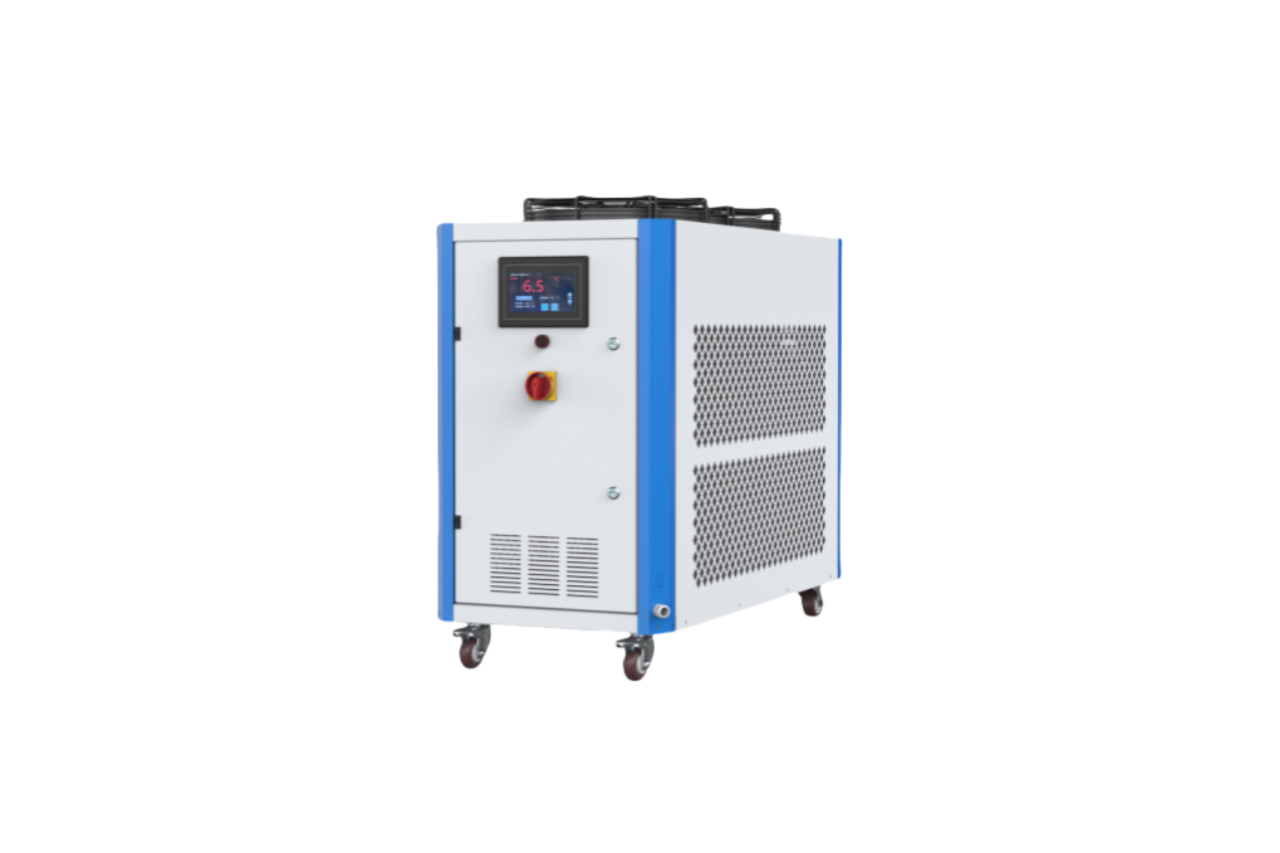
Maintaining high yields and ensuring the quality of molded parts during injection molding can be challenging, as injection molding machines generate high temperatures when operating, which can lead to problems such as overheating, warping, or material defects. In this article, we will explore how using a water chiller for cooling can significantly improve the yield of injection molded parts and how the low-temperature cold water produced by the water chiller can optimize the cooling of hydraulic oil and molds, reduce internal stress, improve mechanical properties, and enhance surface finish. At the same time, it helps improve overall efficiency, product quality, and productivity.
Optimizing Injection Molding Machine Hydraulic Oil Temperature Using a water chiller
The hydraulic system in an injection molding machine generates much heat during operation. Excessive heat can thicken the hydraulic oil, reduce lubrication efficiency, and increase wear on pumps and valves. Over time, this can lead to downtime maintenance and expensive component replacement. The water chiller’s cooling system can solve this problem by keeping the hydraulic oil temperature within the optimal range (usually 35°C–45°C). In injection molding, cooling is one of the key factors that determine molded part quality and yield. Cooling of the hydraulic oil is also critical to keeping the injection molding machine running correctly. Overheated hydraulic oil can reduce machine performance and affect injection molding accuracy. Topstar’s water chillers feature an intelligent refrigeration circuit design. In one case involving a medical device manufacturer, the stable oil temperature after cooling reduced hydraulic system failures by 40% and extended pump life by 2-3 years.
Improve part strength and reduce internal stress with a water chiller.
Internal stress in injection molded parts often stems from uneven cooling. When some parts of a part cool faster than others, residual stress weakens the structure, causing cracks or deformation under load. The chillers provided by Topstar feature fully computerized thermostats that maintain precise mold temperatures for uniform heat dissipation. The resulting ±1°C temperature stability allows for slow, controlled cooling of thick-walled parts and fast cooling of thin-walled parts. The low-temperature cold water produced by the water chiller helps alleviate this problem, ensuring uniform cooling of the mold. By cooling parts faster and more evenly, the water chiller reduces the formation of internal stresses, thereby improving dimensional stability and reducing the risk of warping. This not only improves the yield of the injection molded parts but also enhances their overall mechanical properties.
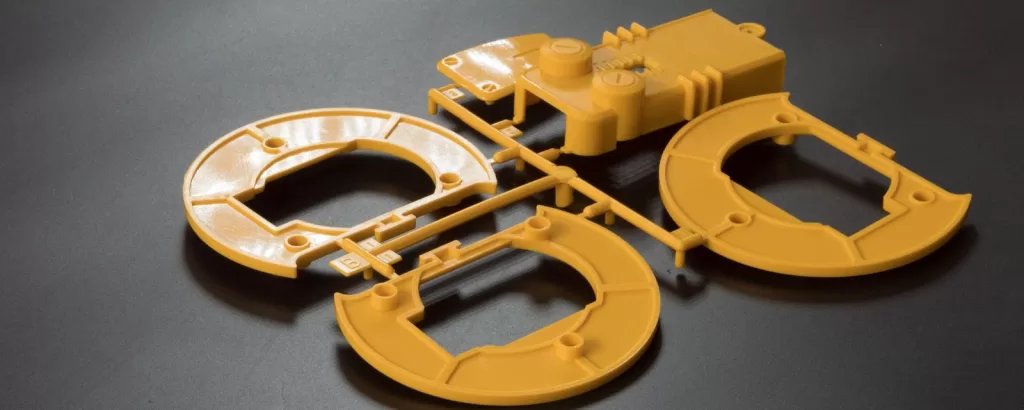
Achieve Superior Surface Finish
Surface defects such as flow lines, jetting or orange peel textures are often caused by inconsistent material flow or premature cooling. Water chillers solve this problem by ensuring that the mold surface maintains a stable temperature during the injection process. For surfaces that require a high finish, such as consumer electronics housings, the mold is kept at a lower temperature (10°C–15°C) to solidify the outer layer and lock in the smoothness quickly. Topstar’s water chillers feature fully computerized temperature controllers with adaptive temperature profiles. During trials for a cosmetic packaging customer, the team gradually increased the mold temperature from 15°C to 25°C during the filling process to eliminate flow marks. Then, they quickly cooled it after packaging.
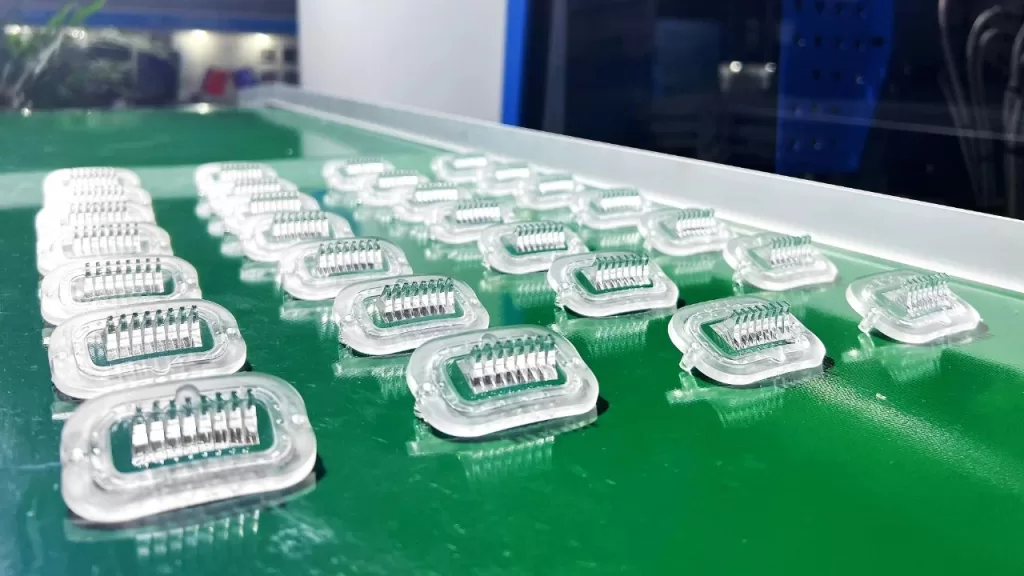
Intelligent Engineering for Fast Cooling and Flexibility
Unlike other water chillers, Topstar’s water chiller systems feature scroll compressors (5HP-50HP), which cool 30% faster than conventional piston compressors. The refrigeration circuit is optimized for minimal energy consumption even at full load. For example, a 20HP chiller consumes only 6.5 kW/h when cooling a 300-ton injection molding machine, equivalent to running two domestic air conditioners. The water chiller also supports multi-zone temperature control. A single unit can manage different cooling needs: 5°C water for the mold, 30°C for the hydraulic oil, and ambient cooling for the hopper dryer. This versatility makes Topstar water chillers ideal for complex applications.
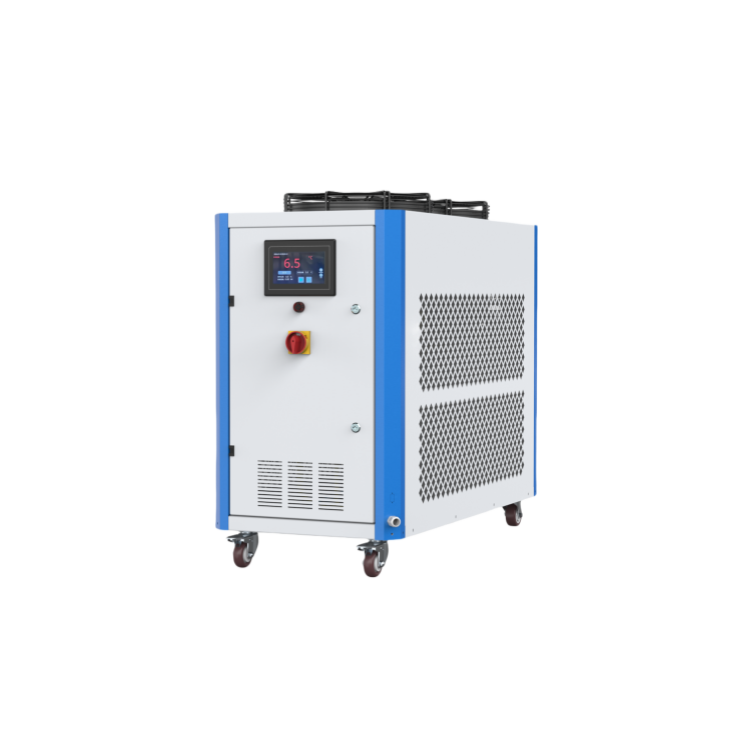
Benefits of Sustainable Manufacturing
With the growing demand for more sustainable and energy-efficient manufacturing processes, the use of water chillers in injection molding operations can also bring multiple environmental benefits. By optimizing the cooling process and reducing cycle times, water chillers help reduce energy consumption, thereby reducing operating costs and reducing environmental impact. In addition to improving the energy efficiency of the production process, Topstar’s water chiller solutions also promote sustainable development by reducing material waste. The ability to more precisely control the cooling process minimizes the possibility of defects, rework and waste, ultimately improving production efficiency and reducing resource use.
Comprehensive Optimized Injection Molding Performance
Using a water chiller in the injection molding process is one of the most effective ways to increase the yield of injection molded parts. By optimizing the cooling of hydraulic oil and molds, water chillers help reduce internal stress, improve part mechanical properties, enhance surface finish and speed up production cycles. Topstar’s water chiller solutions provide manufacturers with the injection molding auxiliary equipment they need to achieve faster cooling, higher efficiency and more consistent results.
TRENDING POSTS
- What factors can cause delays in the injection molding process of plastic molding machine? 2025/02/21
- Exhibition Review| Topstar participates in InterPlas Thailand 2024 2025/02/21
- Star Case | Topstar helps Santong upgrade its intelligent plant 2025/02/21
- Topstar Special | National Science and Technology Workers Day 2025/02/21
HOT TOPIC
- 3 in 1 Compact Dehumidifying Dryer
- 5-axis CNC machine
- accuracy
- Air Chillers
- all electric injection molding machine
- all electric injection molding machines
- All-electric injection molding machines
- and overall production quality. Therefore
- AP-RubberPlas
- automated injection molding machine
- Automation changed engineering
- automation of injection molding robots
- auxiliary machine
- Bench Injection Molding Machine
- Cabinet dryer manufacturers
- Cabinet dryers
- chiller
- CNC Drilling Machine
- CNC Drilling Machines
- cnc engraving machine manufacturer
- cnc laser cutting machine manufacturer
- CNC machine
- CNC Machine Center
- CNC Machine for Sale
- CNC Machine Manufacturing
- CNC Machine Tool
- CNC machine tool product
- CNC Machining Center
- CNC wood carving machine
- Cooling system
- Cross-Walking Single Axis Servo Cylinder Robot
- Cross-Walking Single-Axis Servo Cylinder Robot
- Cross-Walking Three-Axis/Five-Axis Servo Driven Robot
- cross-walking three-axis/five-axis servo-driven robot
- Dehumidifier Dryer
- Dehumidifying Dryer
- delta parallel robot
- Desktop Injection Molding Machine
- Desktop injection molding machines
- Desktop Molding Machine
- desktop plastic injection machine
- Desktop Plastic Injection Molding Machine
- direct clamp injection molding machine
- Direct clamp injection molding machines
- Dosing & mixing system
- Drilling Centers
- Drying and dehumidification system
- drying and dehumidifying equipment
- Drying and Dehumidifying System
- drying system
- effective and efficient. Cabinet dryers are also used in other industries where large quantities of material need to be dried
- efficient injection molding machine
- elbow hydraulic injection molding machines
- electric injection molding machine
- electric injection molding machines
- energy-saving injection molding machine
- etc. Among injection molding robots
- exhibition
- features of CNC machine
- Feeding And Conveying System
- Five Axis Machine Center
- Fully automatic injection molding machine
- Gathering Topstar
- giant injection molding machine
- GMU-600 5-Axis Machining Center
- Granulating & Recycling System
- Heavy duty injection molding machine
- Honeycomb rotor dehumidifier
- horizontal injection molding machine
- Horizontal Injection Molding Machines
- Horizontal Injection Moulding Machine
- Horizontal Mixer manufacturer
- How The CNC Machine Works
- hybrid injection molding machine
- hydraulic injection molding machine
- Hydraulic Injection Molding Machines
- in this article
- Industrial robot
- Industrial Robot Chinese brand
- industrial robot parts
- industrial robot supplier
- Industrial robots
- Industry Chain
- Injection Manipulator
- injection mold machines
- Injection molding
- Injection molding automation
- Injection Molding Automation Solution
- injection molding dryer
- Injection molding equipment
- injection molding hopper dryer
- Injection molding machine
- injection molding machine brand
- Injection Molding Machine Factory
- Injection Molding Machine Manufacture
- Injection molding machine manufacturer
- injection molding machine manufacturers
- Injection molding machine procurement
- injection molding machine robotic arm
- injection molding machine with a robot
- Injection molding machines
- injection molding material dehumidifying
- injection molding plant
- Injection Molding Robot
- injection molding robot arm
- Injection molding robot automation
- Injection molding robotic arm
- injection molding robots
- Injection Moulding Robots
- Injection Robot
- Injection robot arm
- Injection robot manufacturer
- Injection robot wholesale
- injection robots
- intelligent injection molding machines
- Introducing Injection Robot
- It is the best choice for drying large quantities of material at once. Cabinetmakers use these machines because they are fast
- large injection molding machine
- Learn what industrial automation and robotics is
- linear robot
- low speed sound-proof granulator
- machine plastic molding
- make sure to add some! Improvements (2) Keyphrase in introduction: Your keyphrase or its synonyms appear in the first paragraph of the copy
- manipulator machine
- manufacturing
- micro injection molding machine
- middle speed granulator
- Mini CNC machine manufacturers.
- Mold Temperature Control System
- mold temperature controller
- molding material Dehumidifying System
- mould temperature controller
- mould temperature controllers
- New electric injection molding machine
- nitrogen dryer manufacturer
- nitrogen dryer system manufacturer
- Oil type mold temperature controller
- open day
- Outbound links: No outbound links appear in this page. Add some! Images: No images appear on this page. Add some! Internal links: No internal links appear in this page
- PET Preform injection molding
- phone case maker machine
- phone case making machine
- plastic bottle making machine
- plastic bottle manufacturing
- plastic bucket making machine
- plastic bucket manufacturing
- Plastic chair making machine
- plastic forming equipment
- plastic hopper dryer
- plastic injection machine
- plastic injection machines
- plastic injection molding
- Plastic injection molding equipment
- Plastic injection molding machine
- Plastic Injection Molding Machines
- plastic injection robot
- Plastic Molding machine
- Plastic Molding Machines
- plastic molding press
- plastic phone case making machine
- plastic-molding machine
- powerful granulator
- Powerful Type Sound-Proof Granulator
- production of plastic seats
- Robot injection molding
- robot injection molding machine
- robot manufacturing companies
- Robotic arm for injection molding machine
- robotic injection molding machines
- robotics in injection molding
- SCARA robot
- SCARA robots
- Service-oriented manufacturing
- Servo Cylinder Robot
- servo driven robot
- Servo Driven Robots
- servo injection robots
- Servo-Driven Robot
- Setup of injection machine
- Silicone Injection Molding Machine
- six-axis industrial robot
- Stainless Hopper Dryer
- Stainless Hopper Dryers
- star club
- swing arm robot
- the choice between servo-driven robots and hydraulic robots will have a certain impact on efficiency
- the most popular injection molding machine
- the type of injection molding robot
- toggle clamp injection molding machine
- Toggle Hydraulic Injection Molding Machines
- toggle injection molding machine
- Top 10 brands of injection robots
- Topstar
- Topstar Engineering
- Topstar Industrial Robots
- Topstar injection molding intelligent
- Topstar Scara Robots
- Useful Injection molding machine
- Vertical machining centers
- volumetric type blender
- water chiller
- water chillers
- water distributor
- Water Type MoldTemperature Controller
- We often face choices when performing injection molding. We will choose the type of injection molding machine
- wholesale of injection molding machines
- x carve CNC