How to improve the yield of injection molded parts by using a water chiller?
2025/02/10 By Topstar
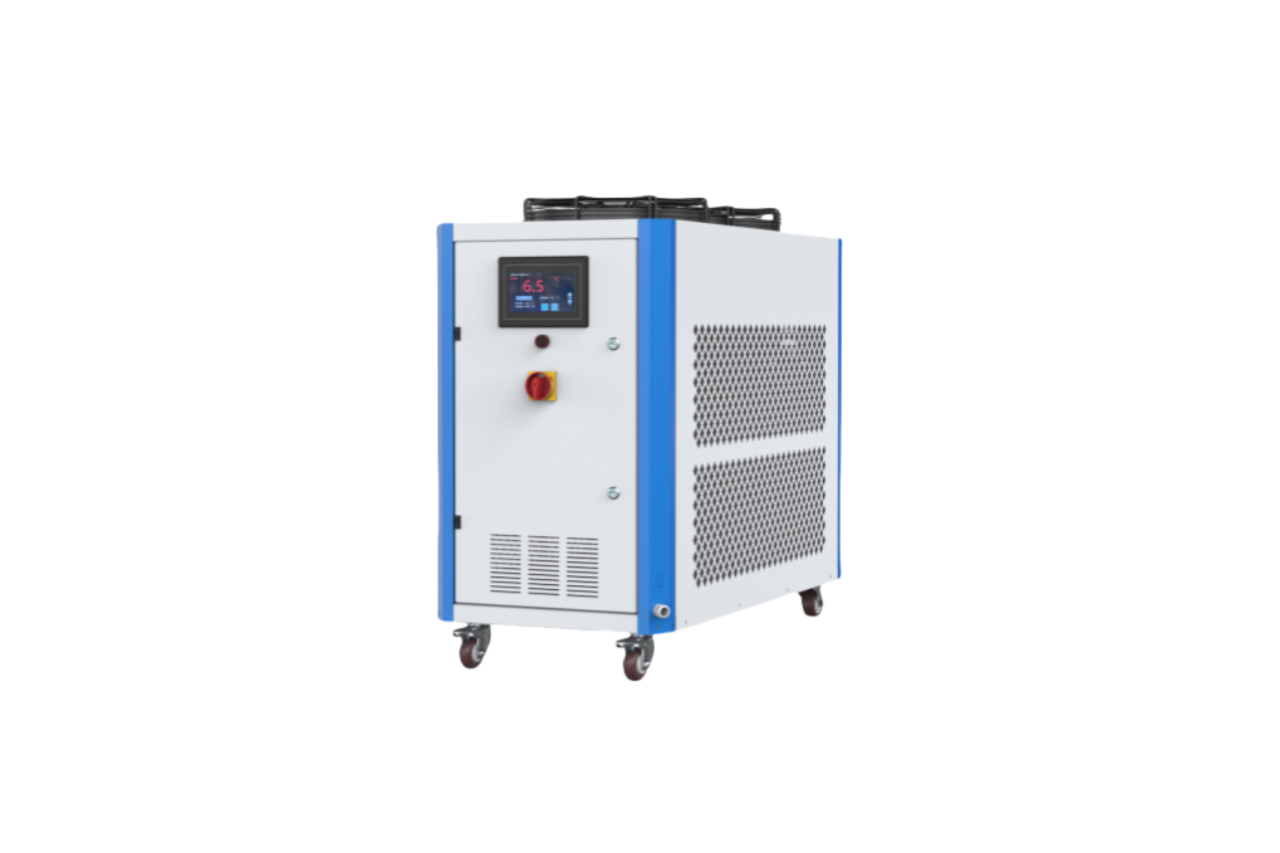
Other auxiliary equipment is also needed to work to ensure a higher yield rate in the production of plastic parts, in addition to using high-efficiency injection molding machines. Injection molding machines generate very high temperatures when working, especially hydraulic injection molding machines, so in addition to mould temperature controllers, a water chiller is also needed to adjust the temperature. By cooling the hydraulic oil and molds to provide precise cooling, water chillers can significantly improve injection molded parts’ efficiency, quality, and durability, which is where water coolers come into play. In this article, we will explore how to use chillers to improve the yield rate of injection molded parts.
The role of water chiller in injection molding
The low-temperature cold water produced by the water chiller can cool the hydraulic oil and molds of the injection molding machine. With its assistance, it can cool quickly, improve efficiency, and enable the physical strength and internal stress of the injection molded parts to reach the optimal state, thereby improving the mechanical properties and durability of the product. At the same time, the cooling process can also significantly improve the product’s surface finish, avoid defects caused by overheating of the material, and thus improve product quality. Topstar’s chillers utilize a more efficient refrigeration circuit design, accelerating cooling and maintaining a stable, low-temperature environment during the injection molding process, enhancing product quality and production efficiency.
Using a water chiller to enhance hydraulic oil cooling in injection molding machines
Injection molding machines rely on hydraulic systems to generate the pressure required for the molding process. However, these systems create heat, leading to overheating and reduced efficiency if not appropriately managed. The cooling process provided by the chiller reduces the temperature and improves energy efficiency. When the system effectively cools the hydraulic oil, it reduces the overall energy consumption of the injection molding machine. By keeping the hydraulic oil at a constant temperature, the water cooler helps prevent thermal degradation of the oil, which can cause increased viscosity and reduced lubrication efficiency. This reduces wear on hydraulic components, extends their service life, and minimizes downtime. Topstar’s water chillers, with their advanced refrigeration circuits, ensure that cooling is both fast and consistent, providing a stable environment for hydraulic oil management.
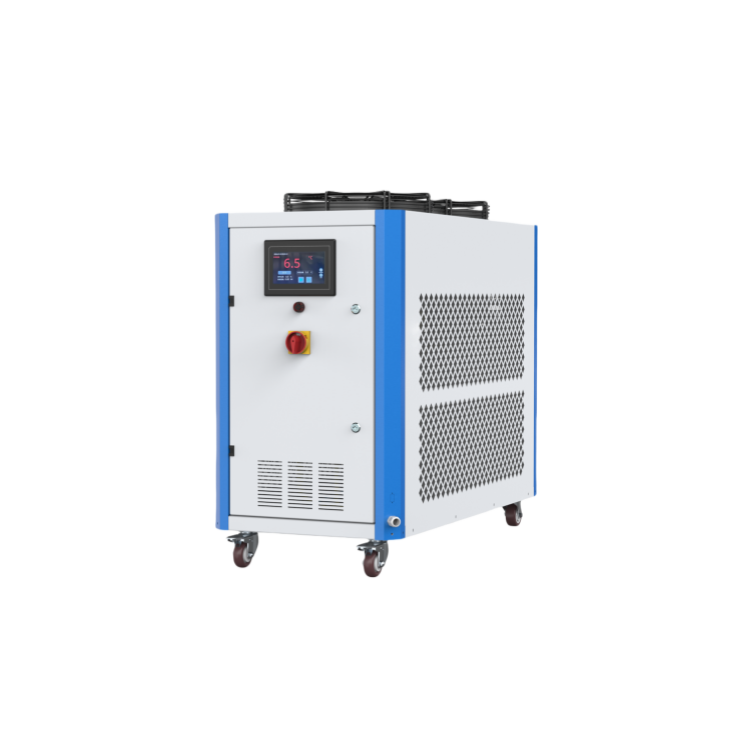
Better optimization of mold temperature
The mold is one of the most critical components in the injection molding process, directly affecting the final product’s quality, dimensional accuracy, and surface finish. Temperature control of the mold is vital. Overheating or uneven cooling can lead to defects, dimensional inaccuracies, and even compromised mechanical properties of the molded part. Water chillers are great for maintaining stable and controlled mold temperatures, ensuring consistent quality output. They provide a steady supply of low-temperature water circling through the mold’s cooling channels. This rapid cooling helps quickly and evenly solidify the molten material so that the resulting part will exhibit minimal internal stress and optimal physical properties. In addition, Topstar’s water chillers feature a fully computerized temperature control system that precisely adjusts the water temperature within a range of 5-35°C, ensuring the mold always maintains optimal performance.
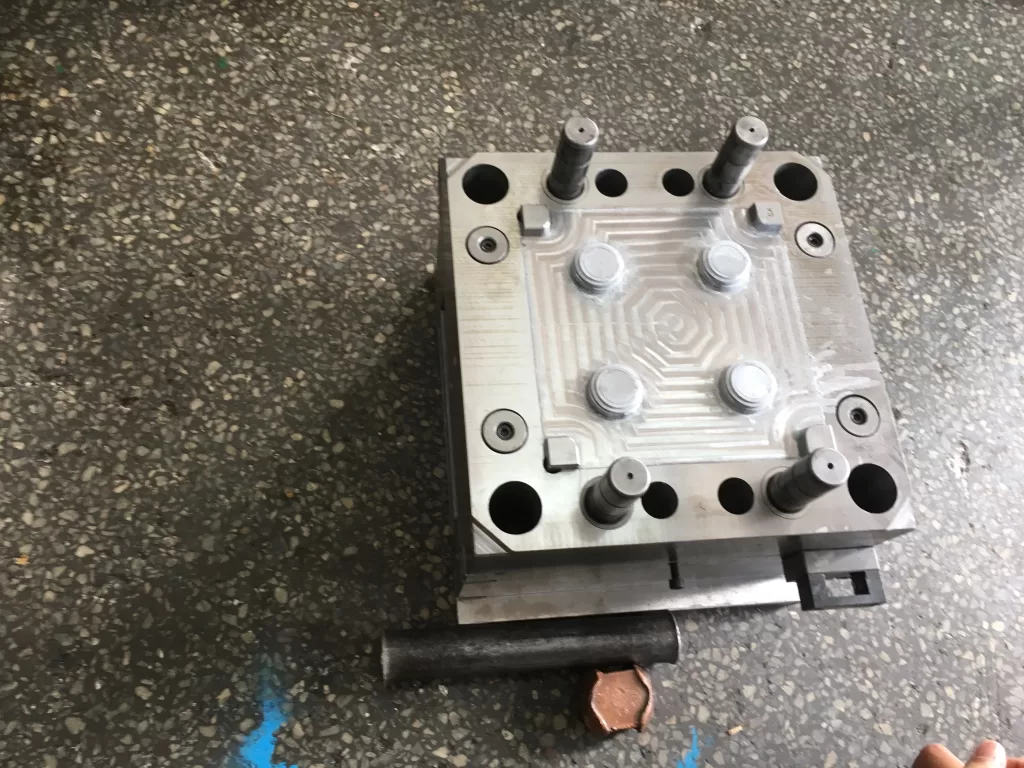
Achieve Optimal Physical Properties of Injection Molded Parts
The cooling process in injection molding also directly impacts the final product’s physical strength and internal stress. Rapid or uneven cooling can lead to internal stresses that weaken the part and make it more susceptible to cracking or failure under load.
By using a water chiller, manufacturers can achieve a controlled, gradual cooling process, which helps minimize internal stress and improve the part’s mechanical properties. In addition, reducing stress inside the material can improve mechanical properties and increase the overall service life of the part. Parts produced under controlled cooling conditions are less likely to develop microcracks or defects over time, so their service life is extended. Ensure that the plastic is cooled evenly so that the parts have higher tensile strength, impact resistance, and overall durability.
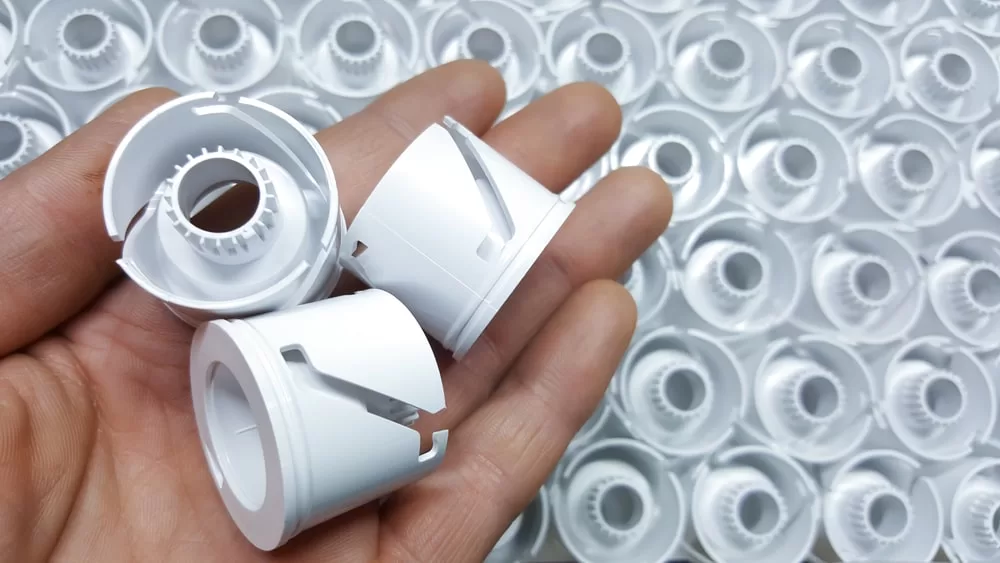
Realize real-time monitoring and scheduling advantages
The real-time monitoring and equipment control capabilities of injection molding equipment can bring high production quality and improve efficiency. In addition to precise temperature control, the self-developed control system used by Topstar’s Water Chille supports the injection molding machine to adjust the chiller and automatically adjust it to ensure optimal performance. At the same time, it supports real-time monitoring of equipment status and records operation and alarm logs. In addition, this scheduling function allows users to program the equipment to turn on and off a week in advance, providing operational flexibility rarely seen in traditional cooling systems.
Maximize production and quality
Providing precise and efficient cooling helps optimize the molding process to produce parts with excellent mechanical properties, perfect surface finish, and consistent dimensions. Topstar’s Water Chilles has advanced cooling and intelligent control systems, providing reliable and effective solutions for manufacturers wanting to increase production capacity.
TRENDING POSTS
- What factors can cause delays in the injection molding process of plastic molding machine? 2025/02/10
- Exhibition Review| Topstar participates in InterPlas Thailand 2024 2025/02/10
- Star Case | Topstar helps Santong upgrade its intelligent plant 2025/02/10
- Topstar Special | National Science and Technology Workers Day 2025/02/10
HOT TOPIC
- 3 in 1 Compact Dehumidifying Dryer
- 5-axis CNC machine
- accuracy
- Air Chillers
- all electric injection molding machine
- All-electric injection molding machines
- and overall production quality. Therefore
- AP-RubberPlas
- automated injection molding machine
- Automation changed engineering
- automation of injection molding robots
- auxiliary machine
- Bench Injection Molding Machine
- Cabinet dryer manufacturers
- Cabinet dryers
- chiller
- CNC Drilling Machine
- CNC Drilling Machines
- cnc engraving machine manufacturer
- cnc laser cutting machine manufacturer
- CNC machine
- CNC Machine Center
- CNC Machine for Sale
- CNC Machine Manufacturing
- CNC Machine Tool
- CNC machine tool product
- CNC Machining Center
- CNC wood carving machine
- Cooling system
- Cross-Walking Single Axis Servo Cylinder Robot
- Cross-Walking Single-Axis Servo Cylinder Robot
- Cross-Walking Three-Axis/Five-Axis Servo Driven Robot
- cross-walking three-axis/five-axis servo-driven robot
- Dehumidifier Dryer
- Dehumidifying Dryer
- delta parallel robot
- Desktop Injection Molding Machine
- Desktop injection molding machines
- Desktop Molding Machine
- desktop plastic injection machine
- Desktop Plastic Injection Molding Machine
- direct clamp injection molding machine
- Direct clamp injection molding machines
- Dosing & mixing system
- Drilling Centers
- Drying and dehumidification system
- drying and dehumidifying equipment
- Drying and Dehumidifying System
- drying system
- effective and efficient. Cabinet dryers are also used in other industries where large quantities of material need to be dried
- efficient injection molding machine
- elbow hydraulic injection molding machines
- electric injection molding machine
- electric injection molding machines
- etc. Among injection molding robots
- exhibition
- features of CNC machine
- Feeding And Conveying System
- Five Axis Machine Center
- Fully automatic injection molding machine
- Gathering Topstar
- giant injection molding machine
- GMU-600 5-Axis Machining Center
- Granulating & Recycling System
- Heavy duty injection molding machine
- Honeycomb rotor dehumidifier
- horizontal injection molding machine
- Horizontal Injection Molding Machines
- Horizontal Injection Moulding Machine
- Horizontal Mixer manufacturer
- How The CNC Machine Works
- hybrid injection molding machine
- hydraulic injection molding machine
- Hydraulic Injection Molding Machines
- in this article
- Industrial robot
- Industrial Robot Chinese brand
- industrial robot parts
- industrial robot supplier
- Industrial robots
- Industry Chain
- Injection Manipulator
- injection mold machines
- Injection molding
- Injection molding automation
- Injection Molding Automation Solution
- injection molding dryer
- Injection molding equipment
- injection molding hopper dryer
- Injection molding machine
- injection molding machine brand
- Injection Molding Machine Factory
- Injection Molding Machine Manufacture
- Injection molding machine manufacturer
- injection molding machine manufacturers
- Injection molding machine procurement
- injection molding machine robotic arm
- injection molding machine with a robot
- Injection molding machines
- injection molding material dehumidifying
- injection molding plant
- Injection Molding Robot
- injection molding robot arm
- Injection molding robot automation
- Injection molding robotic arm
- injection molding robots
- Injection Moulding Robots
- Injection Robot
- Injection robot arm
- Injection robot manufacturer
- Injection robot wholesale
- injection robots
- intelligent injection molding machines
- Introducing Injection Robot
- It is the best choice for drying large quantities of material at once. Cabinetmakers use these machines because they are fast
- large injection molding machine
- Learn what industrial automation and robotics is
- low speed sound-proof granulator
- machine plastic molding
- make sure to add some! Improvements (2) Keyphrase in introduction: Your keyphrase or its synonyms appear in the first paragraph of the copy
- manipulator machine
- manufacturing
- micro injection molding machine
- middle speed granulator
- Mini CNC machine manufacturers.
- Mold Temperature Control System
- mold temperature controller
- molding material Dehumidifying System
- mould temperature controller
- mould temperature controllers
- New electric injection molding machine
- nitrogen dryer manufacturer
- nitrogen dryer system manufacturer
- Oil type mold temperature controller
- open day
- Outbound links: No outbound links appear in this page. Add some! Images: No images appear on this page. Add some! Internal links: No internal links appear in this page
- PET Preform injection molding
- phone case maker machine
- phone case making machine
- plastic bottle making machine
- plastic bottle manufacturing
- plastic bucket making machine
- plastic bucket manufacturing
- Plastic chair making machine
- plastic forming equipment
- plastic hopper dryer
- plastic injection machine
- plastic injection machines
- plastic injection molding
- Plastic injection molding equipment
- Plastic injection molding machine
- Plastic Injection Molding Machines
- plastic injection robot
- Plastic Molding machine
- Plastic Molding Machines
- plastic molding press
- plastic phone case making machine
- plastic-molding machine
- powerful granulator
- Powerful Type Sound-Proof Granulator
- production of plastic seats
- Robot injection molding
- robot injection molding machine
- robot manufacturing companies
- Robotic arm for injection molding machine
- robotic injection molding machines
- robotics in injection molding
- SCARA robot
- SCARA robots
- Service-oriented manufacturing
- Servo Cylinder Robot
- servo driven robot
- Servo Driven Robots
- servo injection robots
- Servo-Driven Robot
- Setup of injection machine
- Silicone Injection Molding Machine
- six-axis industrial robot
- Stainless Hopper Dryer
- Stainless Hopper Dryers
- star club
- swing arm robot
- the choice between servo-driven robots and hydraulic robots will have a certain impact on efficiency
- the most popular injection molding machine
- the type of injection molding robot
- toggle clamp injection molding machine
- Toggle Hydraulic Injection Molding Machines
- toggle injection molding machine
- Top 10 brands of injection robots
- Topstar
- Topstar Engineering
- Topstar Industrial Robots
- Topstar injection molding intelligent
- Topstar Scara Robots
- Useful Injection molding machine
- Vertical machining centers
- volumetric type blender
- water chiller
- water chillers
- water distributor
- Water Type MoldTemperature Controller
- We often face choices when performing injection molding. We will choose the type of injection molding machine
- wholesale of injection molding machines
- x carve CNC