How to improve the stability of horizontal injection molding machine?
2024/11/06 By Topstar
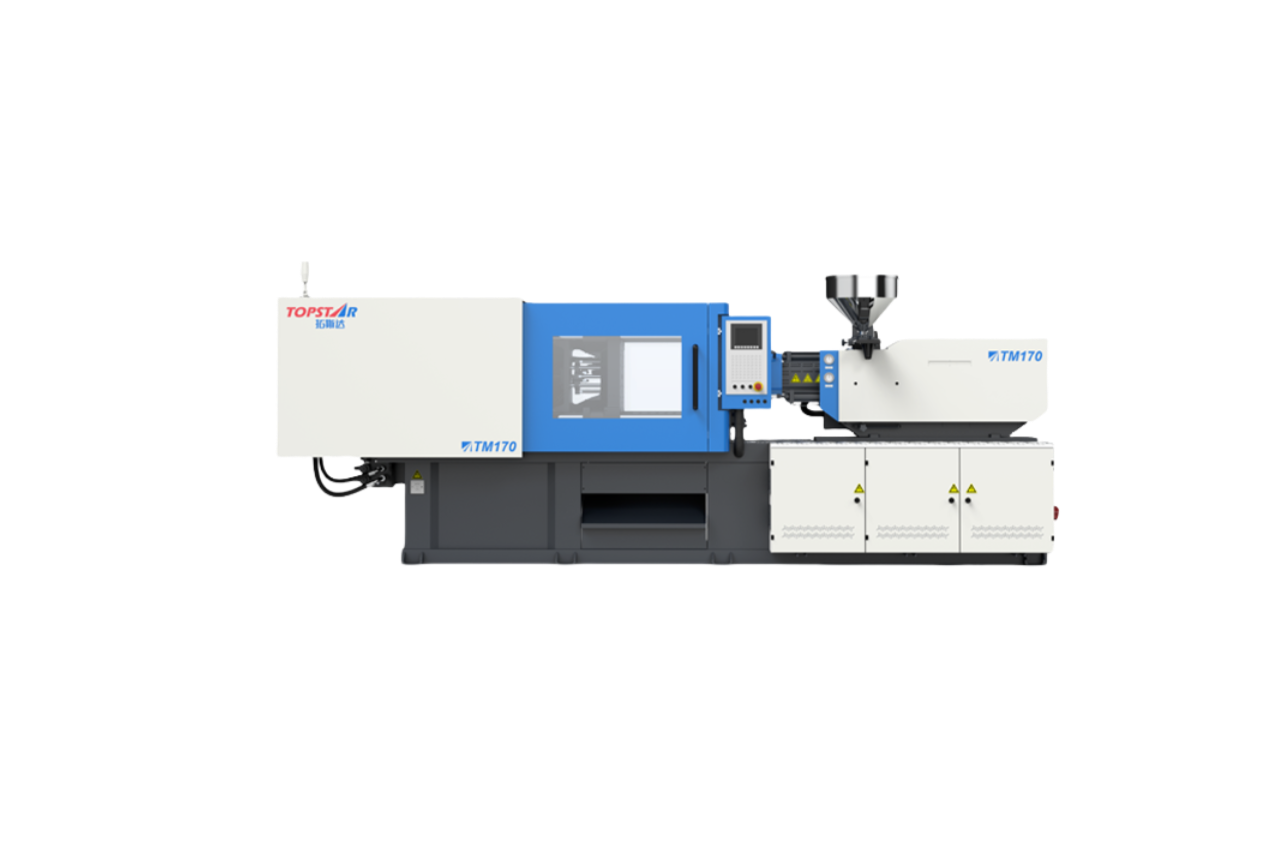
Horizontal injection molding machine is one of the core equipment of many injection molding factories. Different types of horizontal injection molding machines will bring different precision and efficiency. When using some traditional injection molding machines, you may face the situation of the injection molding process not being stable enough and having a high defective rate. Stability is essential to achieve high-quality product output and extend the service life of the machine. Therefore, based on Topstar’s technical core and product philosophy, this guide will tell you how we use different technologies to improve the stability of the injection molding process and bring higher product quality.
Upgrade to a new horizontal injection molding machine control system
Due to communication delays in the control system, there will be problems with unstable product quality on traditional horizontal injection molding machines. This situation often occurs on electric injection molding machines. In response to this, Topstar sends the molding process data to the servo drive through the upper controller central controller, and the servo drive generates the operation curve by itself to form an intelligent drive control mode. This mode reduces the impact of communication delay on the high-speed operation of the servo motor and realizes real-time control of the servo motor. Therefore, the accuracy and stability of position, speed, and pressure control are improved, and the response speed is increased by 8-16 times.
High stability template
Wide support feet, stable dynamic support, smooth mold opening and closing, and better protection of molds and machines. Regarding software, we have upgraded to use a self-developed control system. In terms of hardware, the core of the stability of the horizontal injection molding machine is the use of a high-stability template. Especially in electric injection molding machines, high-stability pressure plates can ensure smooth, reliable, and safe operation, especially during high-speed mold opening and closing cycles. The pressure plate adopts a sturdy and wide support foot design to enhance dynamic support, minimizing vibration and ensuring uniform load distribution throughout the machine. This stability reduces the possibility of mechanical stress and ultimately extends the life of the mold and the machine itself. Through smooth mold opening and closing, the pressure plate helps prevent misalignment or uneven pressure that reduces the quality of molded parts, thereby improving production consistency and reducing defects.
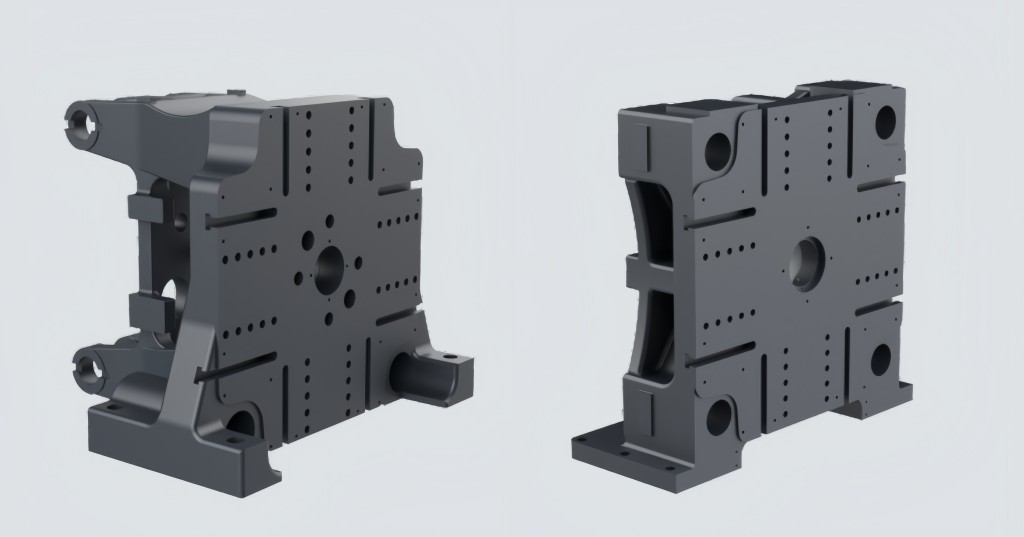
Comprehensive upgrade of the oil circuit system of horizontal injection molding machines
For horizontal hydraulic injection molding machines, the comprehensive upgrade of the oil circuit system has achieved a major leap in operational safety, stability, and performance. The enhanced oil circuit makes the machine more fluid-dynamically efficient, which means smoother transitions and more controlled movements in each cycle. Therefore, it can ensure that the high-pressure clamping and injection processes are handled precisely, reducing the risk of hydraulic fluctuations.
With faster and more sensitive clamping, the machine can switch between clamping states efficiently, significantly reducing cycle time. This differential speed control optimizes productivity and minimizes energy consumption by adjusting the flow rate at any time according to the machine’s specific needs. In addition, the upgraded oil circuit system also integrates a full-featured hydraulic control device, enhancing the machine’s versatility and stability.
The concept of a process-integrated injection molding machine
We have mentioned this concept in many articles and guides in the past. Traditional horizontal injection molding machines cannot achieve the interconnection between every device in the entire injection molding system because it will cause unstable molding. Therefore, Topstar defines the process-integrated injection molding machine as a fusion of software and hardware and continuously improves the intelligence of the equipment through communication, control, optimization, and perception. Today, the control interface links multiple devices to optimize the entire injection molding process, covering injection material pretreatment, plasticization, molding control, and removal process coordination. Through system integration, combining main and auxiliary machines, and using sensor technology, operators control key injection molding factors like temperature, speed, position, pressure, and time, ensuring a highly stable molding process.
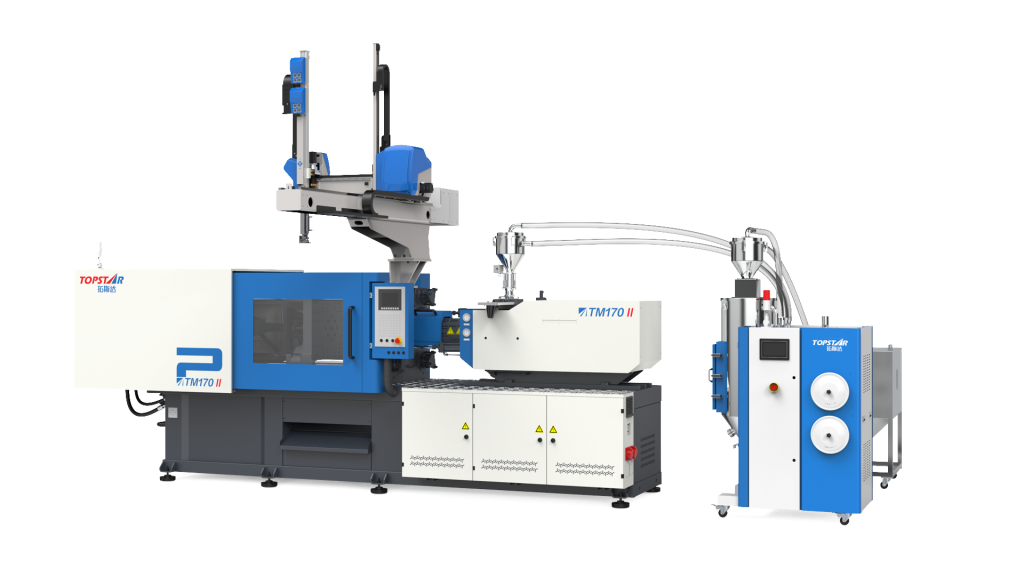
Optimize temperature control to achieve stability
Temperature control is a critical factor in maintaining the stability of horizontal injection molding machines. Temperature fluctuations can cause inconsistent material flow, resulting in changes in part quality and excessive stress on machine components. Stable temperature settings ensure that material viscosity remains constant, resulting in a smooth and predictable injection cycle. To improve temperature stability, Topstar’s mold temperature controller is based on temperature PID algorithm control, with a temperature control accuracy of ±0.1℃, ensuring temperature uniformity, and has an over-temperature protection mechanism to ensure the yield of plastic products. Meanwhile, Topstar uses stainless steel casting and welding in hardware for the main pipeline to reduce leakage. They can also select water quality filters to minimize pipeline blockages and shutdown failures caused by water quality issues, thus ensuring continuous production.
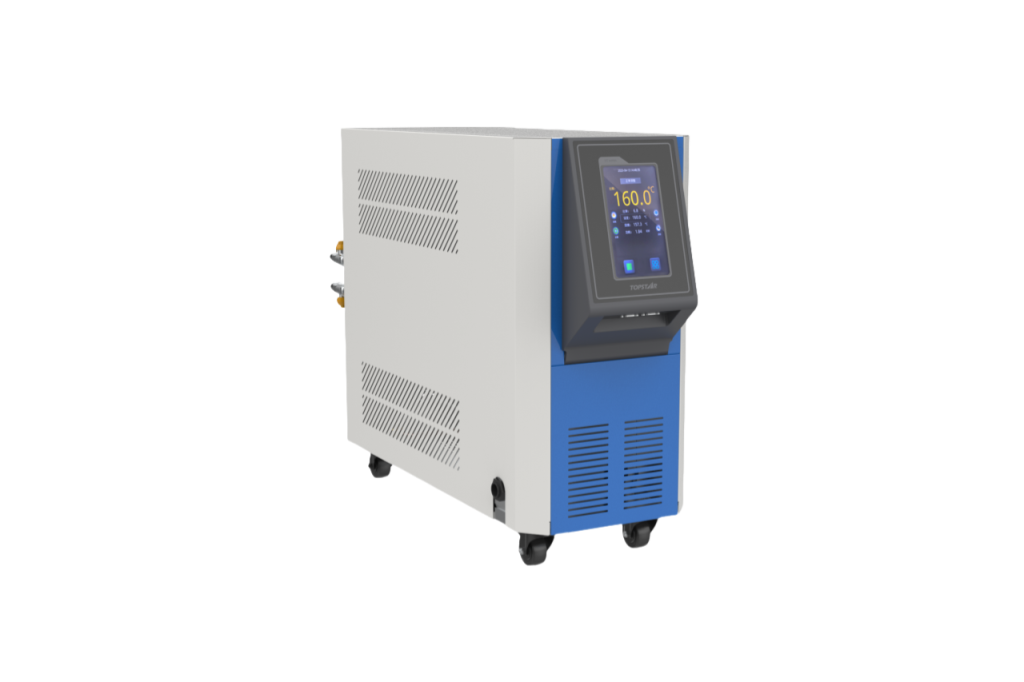
Bring you a more stable injection molding process
Comprehensive measures are needed to improve the stability of horizontal injection molding machines, including independent research and development of control systems, temperature control, and intelligent upgrades of software and hardware. Therefore, by targeting these factors, the stability of the machine can be gradually improved, downtime can be reduced, and product quality can be improved.
TRENDING POSTS
- What factors can cause delays in the injection molding process of plastic molding machine? 2024/11/06
- Exhibition Review| Topstar participates in InterPlas Thailand 2024 2024/11/06
- Star Case | Topstar helps Santong upgrade its intelligent plant 2024/11/06
- Topstar Special | National Science and Technology Workers Day 2024/11/06
HOT TOPIC
- 3 in 1 Compact Dehumidifying Dryer
- 5-axis CNC machine
- accuracy
- Air Chillers
- all electric injection molding machine
- all electric injection molding machines
- All-electric injection molding machines
- and overall production quality. Therefore
- AP-RubberPlas
- automated injection molding machine
- Automation changed engineering
- automation of injection molding robots
- auxiliary machine
- Bench Injection Molding Machine
- Cabinet dryer manufacturers
- Cabinet dryers
- chiller
- CNC Drilling Machine
- CNC Drilling Machines
- cnc engraving machine manufacturer
- cnc laser cutting machine manufacturer
- CNC machine
- CNC Machine Center
- CNC Machine for Sale
- CNC Machine Manufacturing
- CNC Machine Tool
- CNC machine tool product
- CNC Machining Center
- CNC wood carving machine
- Cooling system
- Cross-Walking Single Axis Servo Cylinder Robot
- Cross-Walking Single-Axis Servo Cylinder Robot
- Cross-Walking Three-Axis/Five-Axis Servo Driven Robot
- cross-walking three-axis/five-axis servo-driven robot
- Dehumidifier Dryer
- Dehumidifying Dryer
- delta parallel robot
- Desktop Injection Molding Machine
- Desktop injection molding machines
- Desktop Molding Machine
- desktop plastic injection machine
- Desktop Plastic Injection Molding Machine
- direct clamp injection molding machine
- Direct clamp injection molding machines
- Dosing & mixing system
- Drilling Centers
- Drying and dehumidification system
- drying and dehumidifying equipment
- Drying and Dehumidifying System
- drying system
- effective and efficient. Cabinet dryers are also used in other industries where large quantities of material need to be dried
- efficient injection molding machine
- elbow hydraulic injection molding machines
- electric injection molding machine
- electric injection molding machines
- energy-saving injection molding machine
- etc. Among injection molding robots
- exhibition
- features of CNC machine
- Feeding And Conveying System
- Five Axis Machine Center
- Fully automatic injection molding machine
- Gathering Topstar
- giant injection molding machine
- GMU-600 5-Axis Machining Center
- Granulating & Recycling System
- Heavy duty injection molding machine
- Honeycomb rotor dehumidifier
- horizontal injection molding machine
- Horizontal Injection Molding Machines
- Horizontal Injection Moulding Machine
- Horizontal Mixer manufacturer
- How The CNC Machine Works
- hybrid injection molding machine
- hydraulic injection molding machine
- Hydraulic Injection Molding Machines
- in this article
- Industrial robot
- Industrial Robot Chinese brand
- industrial robot parts
- industrial robot supplier
- Industrial robots
- Industry Chain
- Injection Manipulator
- injection mold machines
- Injection molding
- Injection molding automation
- Injection Molding Automation Solution
- injection molding dryer
- Injection molding equipment
- injection molding hopper dryer
- Injection molding machine
- injection molding machine brand
- Injection Molding Machine Factory
- Injection Molding Machine Manufacture
- Injection molding machine manufacturer
- injection molding machine manufacturers
- Injection molding machine procurement
- injection molding machine robotic arm
- injection molding machine with a robot
- Injection molding machines
- injection molding material dehumidifying
- injection molding plant
- Injection Molding Robot
- injection molding robot arm
- Injection molding robot automation
- Injection molding robotic arm
- injection molding robots
- Injection Moulding Robots
- Injection Robot
- Injection robot arm
- Injection robot manufacturer
- Injection robot wholesale
- injection robots
- intelligent injection molding machines
- Introducing Injection Robot
- It is the best choice for drying large quantities of material at once. Cabinetmakers use these machines because they are fast
- large injection molding machine
- Learn what industrial automation and robotics is
- low speed sound-proof granulator
- machine plastic molding
- make sure to add some! Improvements (2) Keyphrase in introduction: Your keyphrase or its synonyms appear in the first paragraph of the copy
- manipulator machine
- manufacturing
- micro injection molding machine
- middle speed granulator
- Mini CNC machine manufacturers.
- Mold Temperature Control System
- mold temperature controller
- molding material Dehumidifying System
- mould temperature controller
- mould temperature controllers
- New electric injection molding machine
- nitrogen dryer manufacturer
- nitrogen dryer system manufacturer
- Oil type mold temperature controller
- open day
- Outbound links: No outbound links appear in this page. Add some! Images: No images appear on this page. Add some! Internal links: No internal links appear in this page
- PET Preform injection molding
- phone case maker machine
- phone case making machine
- plastic bottle making machine
- plastic bottle manufacturing
- plastic bucket making machine
- plastic bucket manufacturing
- Plastic chair making machine
- plastic forming equipment
- plastic hopper dryer
- plastic injection machine
- plastic injection machines
- plastic injection molding
- Plastic injection molding equipment
- Plastic injection molding machine
- Plastic Injection Molding Machines
- plastic injection robot
- Plastic Molding machine
- Plastic Molding Machines
- plastic molding press
- plastic phone case making machine
- plastic-molding machine
- powerful granulator
- Powerful Type Sound-Proof Granulator
- production of plastic seats
- Robot injection molding
- robot injection molding machine
- robot manufacturing companies
- Robotic arm for injection molding machine
- robotic injection molding machines
- robotics in injection molding
- SCARA robot
- SCARA robots
- Service-oriented manufacturing
- Servo Cylinder Robot
- servo driven robot
- Servo Driven Robots
- servo injection robots
- Servo-Driven Robot
- Setup of injection machine
- Silicone Injection Molding Machine
- six-axis industrial robot
- Stainless Hopper Dryer
- Stainless Hopper Dryers
- star club
- swing arm robot
- the choice between servo-driven robots and hydraulic robots will have a certain impact on efficiency
- the most popular injection molding machine
- the type of injection molding robot
- toggle clamp injection molding machine
- Toggle Hydraulic Injection Molding Machines
- toggle injection molding machine
- Top 10 brands of injection robots
- Topstar
- Topstar Engineering
- Topstar Industrial Robots
- Topstar injection molding intelligent
- Topstar Scara Robots
- Useful Injection molding machine
- Vertical machining centers
- volumetric type blender
- water chiller
- water chillers
- water distributor
- Water Type MoldTemperature Controller
- We often face choices when performing injection molding. We will choose the type of injection molding machine
- wholesale of injection molding machines
- x carve CNC