How to evaluate the energy consumption of a plastic injection machine?
2023/12/25 By Topstar
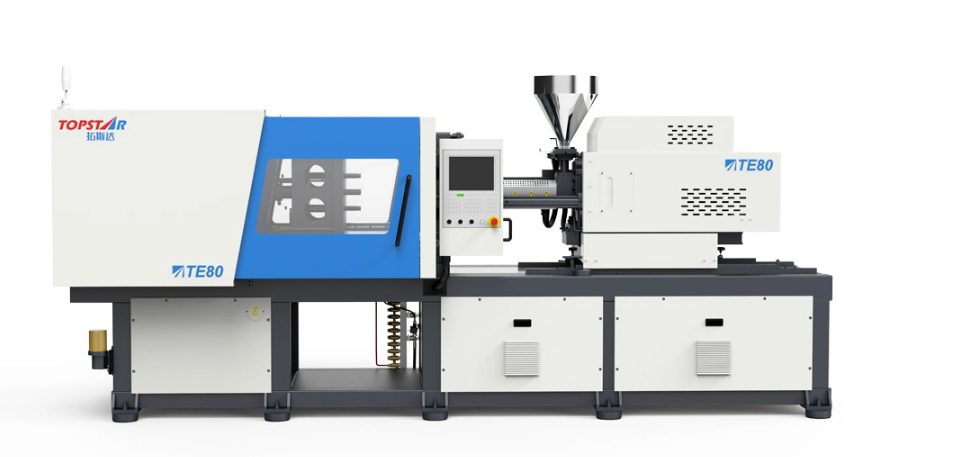
Many buyers in the plastic manufacturing industry will consider many aspects of plastic injection machine when purchasing injection molding machines. In this guide, we’ll tell you how to evaluate the energy consumption of a plastic injection machine, identify key indicators, and implement practical strategies so you can choose a device that can improve efficiency and reduce operating costs.
plastic injection machine energy consumption indicators
A key metric is specific energy consumption (SEC), representing the energy consumed per kilogram of melted plastic. Lower SEC values indicate higher efficiency. Cycle time is another critical metric representing the time required to complete an injection molding cycle. Efficient machines with shorter cycle times minimize energy consumption, helping to increase productivity and cost-effectiveness. The overall efficiency of a plastic injection machine is evaluated by the energy efficiency ratio (EER). This ratio measures a machine’s output relative to its energy input. Higher EER values mean more energy-efficient operations consistent with sustainable manufacturing practices.
Choose energy-saving plastic injection machine to reduce energy consumption.
One way to reduce energy consumption is to choose energy-efficient plastic injection molding machines with variable frequency drives (VFD) integrated into the machine’s motor system. VFDs can precisely control motor speed, reducing energy consumption during periods of lower demand. This dynamic adjustment increases efficiency, especially in processes with different production requirements. Energy-efficient plastic injection molding machines often use advanced heating methods, such as induction heating or advanced insulation materials, to minimize heat loss, optimize the melting process, reduce energy consumption, and shorten cycle time. Energy-saving models often have automatic shut-off or standby features during idle periods, minimizing unnecessary power use.
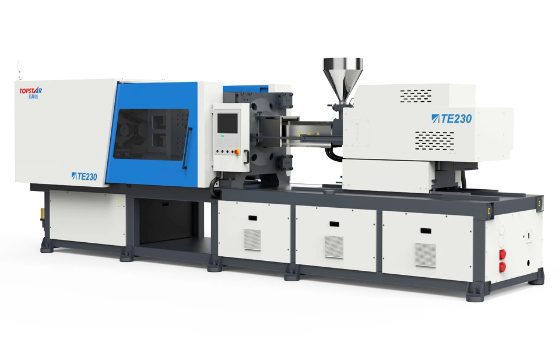
Advanced control systems assess energy losses!
Assessment of the energy consumption of a plastic injection molding machine involves a rigorous examination of its control system. Advanced control systems are vital in minimizing energy losses during the injection molding and increasing overall efficiency. Using a servo-drive system can improve accuracy and responsiveness. Unlike traditional hydraulic systems, servo-drive systems can precisely control the movement of the machine and reduce wasted energy during idle or low-demand periods. This adaptability ensures power is only used when needed, resulting in significant energy savings. Advanced control systems have energy recovery technology, which helps capture and reuse excess energy generated during deceleration or braking phases.
From heating and cooling
We can reduce the energy consumption of plastic injection machines in terms of heating and cooling. Plastic injection molding machines usually use advanced heating technology, such as induction or infrared heating. These technologies target specific areas, minimizing heat loss and ensuring the melting process is more energy efficient. The choice of an efficient heating method directly affects the overall energy consumption during the molding cycle. Efficient cooling minimizes cycle times and ensures consistent part quality. Utilizing cooling technologies such as water-cooling systems can quickly dissipate heat from the molding material, thereby increasing efficiency. Intelligent control systems that adjust cooling rates based on real-time feedback help further save energy.
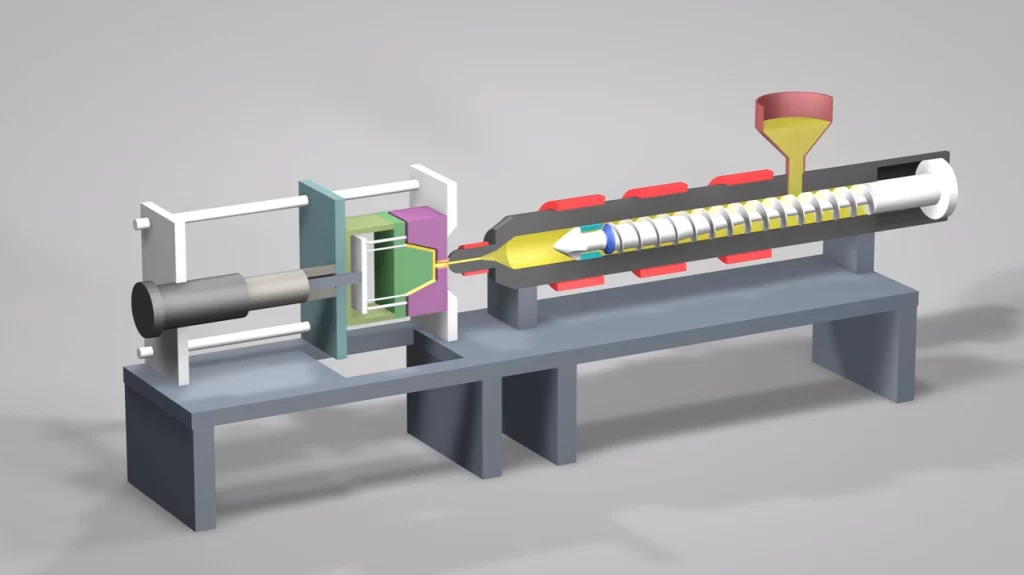
Reduce idle time and standby mode
We can also assess energy consumption by reducing idle times and optimizing standby modes in various industrial processes. Idle time is the period when the machine is not actively involved in the molding process. Taking steps to reduce sedentary time is critical to energy efficiency. Finding out whether the plastic injection molding machine can implement standby mode can help save a lot of energy during downtime. Modern plastic injection molding machines often have an automatic standby function that activates during inactivity. This ensures a quick transition to a low-energy state, minimizing unnecessary power consumption without affecting the machine’s readiness for immediate use.
In short
Assessing the energy consumption of plastic injection machines is a critical step in making our manufacturing processes sustainable and cost-effective. When considering energy consumption when purchasing, we can start from these aspects to assess and evaluate the energy consumption of plastic injection machines to minimize the energy consumption of your overall production process.
TRENDING POSTS
- What factors can cause delays in the injection molding process of plastic molding machine? 2023/12/25
- Exhibition Review| Topstar participates in InterPlas Thailand 2024 2023/12/25
- Star Case | Topstar helps Santong upgrade its intelligent plant 2023/12/25
- Topstar Special | National Science and Technology Workers Day 2023/12/25
HOT TOPIC
- .ervo motor-driven linear robots
- 3 axis robot
- 3 axis robots
- 3 in 1 Compact Dehumidifying Dryer
- 3-axis robot
- 3-axis robots
- 5-axis CNC machine
- accuracy
- Air Chillers
- all electric injection molding machine
- all electric injection molding machines
- All-electric injection molding machines
- and overall production quality. Therefore
- AP-RubberPlas
- automated injection molding machine
- Automation changed engineering
- automation of injection molding robots
- auxiliary machine
- Bench Injection Molding Machine
- Cabinet dryer manufacturers
- Cabinet dryers
- chiller
- CNC Drilling Machine
- CNC Drilling Machines
- cnc engraving machine manufacturer
- cnc laser cutting machine manufacturer
- CNC machine
- CNC Machine Center
- CNC Machine for Sale
- CNC Machine Manufacturing
- CNC Machine Tool
- CNC machine tool product
- CNC Machining Center
- CNC wood carving machine
- Cooling system
- Cross-Walking Single Axis Servo Cylinder Robot
- Cross-Walking Single-Axis Servo Cylinder Robot
- Cross-Walking Three-Axis/Five-Axis Servo Driven Robot
- cross-walking three-axis/five-axis servo-driven robot
- Dehumidifier Dryer
- Dehumidifying Dryer
- delta parallel robot
- Desktop Injection Molding Machine
- Desktop injection molding machines
- Desktop Molding Machine
- desktop plastic injection machine
- Desktop Plastic Injection Molding Machine
- direct clamp injection molding machine
- Direct clamp injection molding machines
- Dosing & mixing system
- Drilling Centers
- Drying and dehumidification system
- drying and dehumidifying equipment
- Drying and Dehumidifying System
- drying system
- effective and efficient. Cabinet dryers are also used in other industries where large quantities of material need to be dried
- efficient injection molding machine
- elbow hydraulic injection molding machines
- electric injection molding machine
- electric injection molding machines
- energy-efficient injection molding robot
- energy-saving injection molding machine
- etc. Among injection molding robots
- exhibition
- features of CNC machine
- Feeding And Conveying System
- Five Axis Machine Center
- Fully automatic injection molding machine
- Gathering Topstar
- giant injection molding machine
- GMU-600 5-Axis Machining Center
- Granulating & Recycling System
- Heavy duty injection molding machine
- High-precision electric molding machines
- high-precision plastic molding machines
- high-speed all electric injection molding machine
- Honeycomb rotor dehumidifier
- horizontal injection molding machine
- Horizontal Injection Molding Machines
- Horizontal Injection Moulding Machine
- Horizontal Mixer manufacturer
- How The CNC Machine Works
- hybrid injection molding machine
- hydraulic injection molding machine
- Hydraulic Injection Molding Machines
- in this article
- Industrial robot
- Industrial Robot Chinese brand
- industrial robot parts
- industrial robot supplier
- Industrial robots
- Industry Chain
- Injection Manipulator
- injection manipulator robot
- injection mold machines
- Injection molding
- Injection molding automation
- Injection Molding Automation Solution
- injection molding dryer
- Injection molding equipment
- injection molding hopper dryer
- Injection molding machine
- injection molding machine brand
- Injection Molding Machine Factory
- Injection Molding Machine Manufacture
- Injection molding machine manufacturer
- injection molding machine manufacturers
- Injection molding machine procurement
- injection molding machine robotic arm
- injection molding machine with a robot
- Injection molding machines
- injection molding material dehumidifying
- injection molding plant
- Injection Molding Robot
- injection molding robot arm
- Injection molding robot automation
- Injection molding robotic arm
- injection molding robots
- Injection moulding machine
- Injection Moulding Robots
- Injection Robot
- Injection robot arm
- Injection robot manufacturer
- Injection robot wholesale
- injection robots
- intelligent injection molding machines
- Introducing Injection Robot
- It is the best choice for drying large quantities of material at once. Cabinetmakers use these machines because they are fast
- large injection molding machine
- Learn what industrial automation and robotics is
- linear robot
- linear robots
- low speed sound-proof granulator
- machine plastic molding
- make sure to add some! Improvements (2) Keyphrase in introduction: Your keyphrase or its synonyms appear in the first paragraph of the copy
- manipulator machine
- manufacturing
- medical grade injection molding machines
- medical injection molding machine
- medical injection molding machines
- micro injection molding machine
- middle speed granulator
- Mini CNC machine manufacturers.
- Mold Temperature Control System
- mold temperature controller
- mold temperature controllers
- molding material Dehumidifying System
- mould temperature control system
- mould temperature controller
- mould temperature controllers
- New electric injection molding machine
- nitrogen dryer manufacturer
- nitrogen dryer system manufacturer
- Oil type mold temperature controller
- Oil type mold temperature controllers
- open day
- Outbound links: No outbound links appear in this page. Add some! Images: No images appear on this page. Add some! Internal links: No internal links appear in this page
- PET Preform injection molding
- phone case maker machine
- phone case making machine
- plastic bottle making machine
- plastic bottle manufacturing
- plastic bucket making machine
- plastic bucket manufacturing
- Plastic chair making machine
- plastic forming equipment
- plastic hopper dryer
- plastic injection machine
- plastic injection machines
- plastic injection molding
- Plastic injection molding equipment
- Plastic injection molding machine
- Plastic Injection Molding Machines
- plastic injection moulding machine
- plastic injection robot
- Plastic Molding machine
- Plastic Molding Machines
- plastic molding press
- plastic moulding machine
- plastic phone case making machine
- plastic-molding machine
- powerful granulator
- Powerful Type Sound-Proof Granulator
- precision injection molding
- production of plastic seats
- pure water mould temperature controller
- Robot injection molding
- robot injection molding machine
- robot manufacturing companies
- Robotic arm for injection molding machine
- robotic injection molding machines
- robotics in injection molding
- SCARA robot
- SCARA robots
- Service-oriented manufacturing
- Servo Cylinder Robot
- servo driven robot
- Servo Driven Robots
- servo injection robots
- servo motor-driven linear robots
- servo-driven 3-axis robot
- Servo-Driven Robot
- Setup of injection machine
- Silicone Injection Molding Machine
- six-axis industrial robot
- Stainless Hopper Dryer
- Stainless Hopper Dryers
- star club
- swing arm robot
- take-out robots
- the choice between servo-driven robots and hydraulic robots will have a certain impact on efficiency
- the most popular injection molding machine
- the type of injection molding robot
- toggle clamp injection molding machine
- Toggle Hydraulic Injection Molding Machines
- toggle injection molding machine
- Top 10 brands of injection robots
- Topstar
- Topstar Engineering
- Topstar Industrial Robots
- Topstar injection molding intelligent
- Topstar Scara Robots
- Useful Injection molding machine
- Vertical machining centers
- volumetric type blender
- water chiller
- water chillers
- water distributor
- water type mold temperature controller
- Water Type MoldTemperature Controller
- Water-Type Mould Temperature Controllers
- We often face choices when performing injection molding. We will choose the type of injection molding machine
- wholesale of injection molding machines
- x carve CNC