How to ensure uniform wall thickness in plastic bottle making machine?
2024/07/01 By Topstar
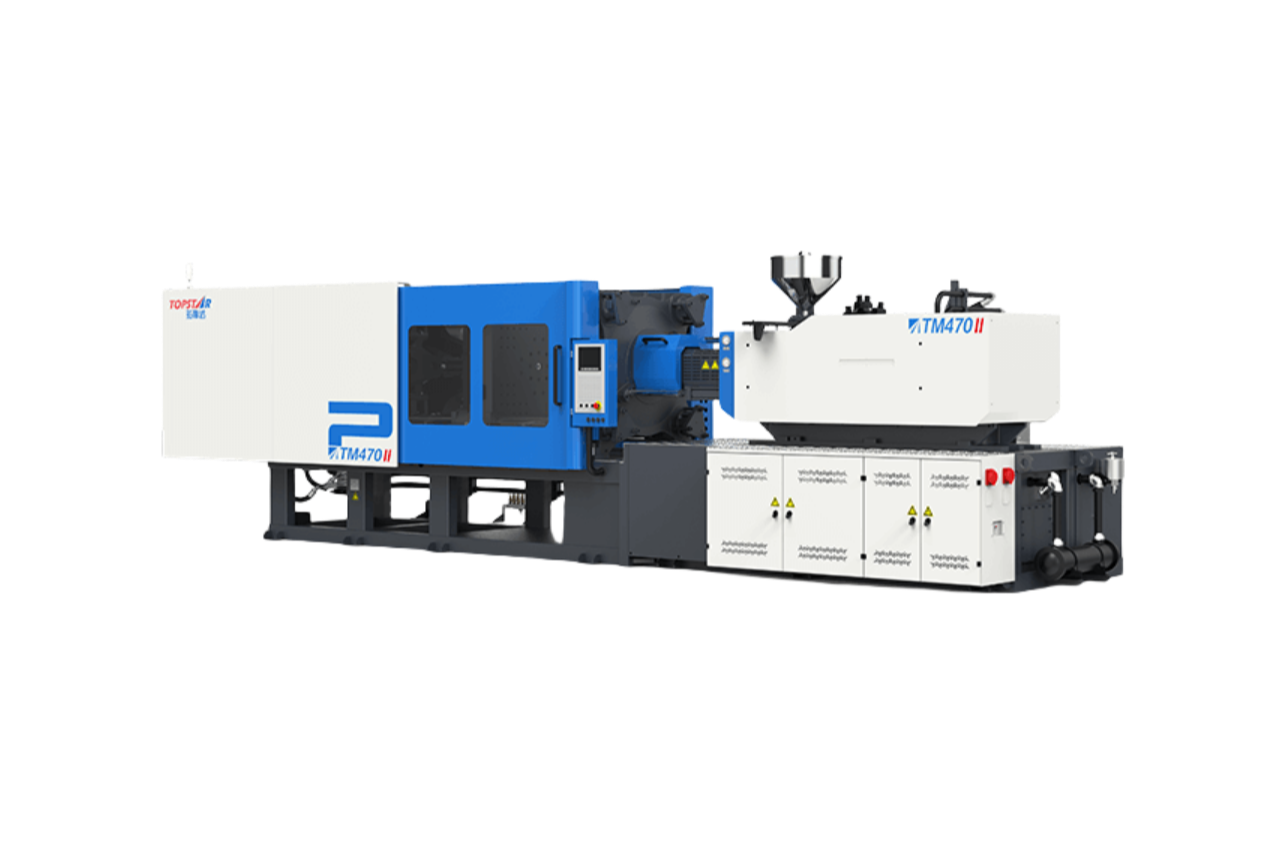
In the plastic bottle manufacturing process, uniform wall thickness can be ensured to maintain the quality and function of the bottle. If the wall thickness is inconsistent, it will lead to structural defects, product failure, and increased material costs, affecting bottle use. This guide will share practical insights on achieving and maintaining uniform wall thickness in the production process for plastic bottle making machine users through 5 aspects.
Importance of material selection for plastic bottle making machine
First, the choice of materials plays a vital role in achieving uniform wall thickness for plastic bottle making machines. On the one hand, different plastics, such as PET, HDPE, and PP, have unique properties that affect their behavior during molding. The melt flow index, viscosity, and thermal stability affect how the material fills the mold and cools. Therefore, selecting the suitable material for your specific application and setting the corresponding parameters is necessary. On the other hand, ensuring the quality consistency of plastic materials, if there are impurities, moisture content, and batch differences, can all lead to inconsistent wall thickness.
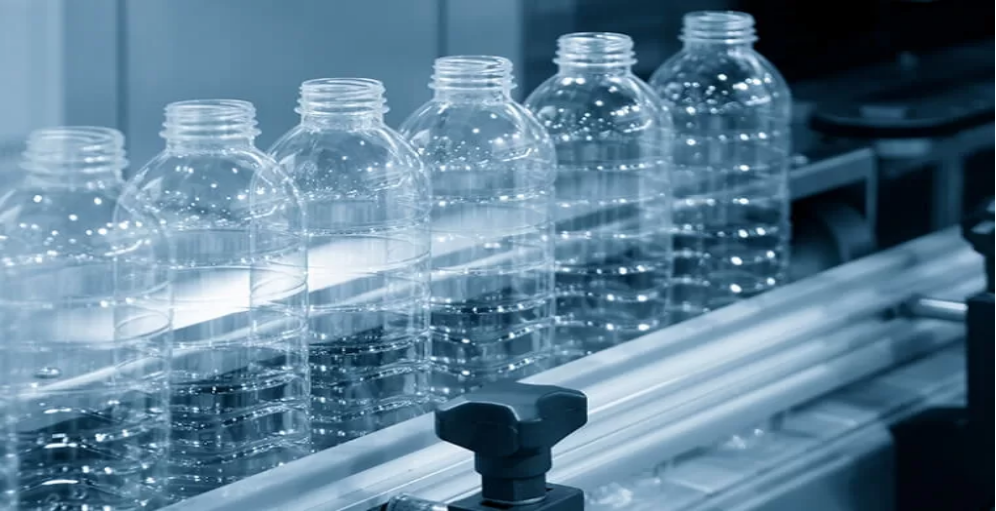
The role of mold design in plastic bottle making machine
During the mold design stage, it is necessary to ensure that the shape of the bottle is uniform. Therefore, the injection molding machine must use its super template design to make each bottle perform and bear the force evenly. In addition, the mould design will directly affect the stretch blow moulding process and ensure that the cavity allows uniform airflow and material distribution during the blow moulding process. Generally speaking, the mould is equipped with cooling channels to regulate the temperature of the entire mould cavity. Uniform cooling helps to evenly solidify the plastic and prevent wall thickness variations due to differences in cooling rates. Maintaining proper ventilation in the mould is essential to eliminate air pockets and ensure uniform moulding of the preform. Adequate ventilation can prevent defects such as bubbles or thin spots, which may affect wall thickness uniformity.
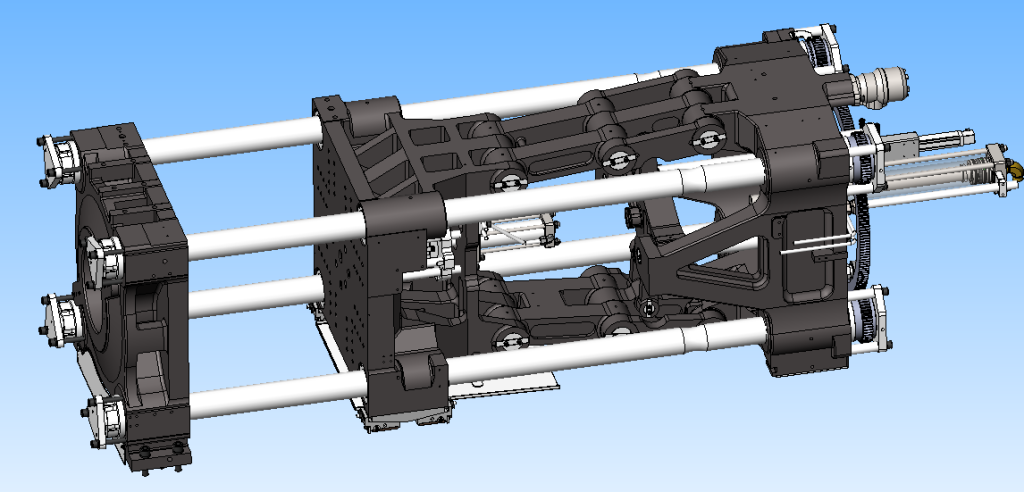
Control of process parameters
In addition to mold design and material selection, we also need to control process parameters. Temperature control is crucial throughout the plastic bottle manufacturing process. Injection molding machines, molds, etc. must maintain precise temperatures. Therefore, mould temperature controllers are used to ensure proper material flow and mold filling. If the temperature is inconsistent, it will cause changes in wall thickness and material properties. Therefore, it is necessary to use mold temperature controllers. Pressure and time also need to be controlled in the control panel of the plastic bottle making machine to ensure that the pressure applied during the inflation of the preform is guaranteed to ensure uniform material distribution. In addition, the time of each stage from forming the preform to the closure and cooling of the mold must be precisely managed.
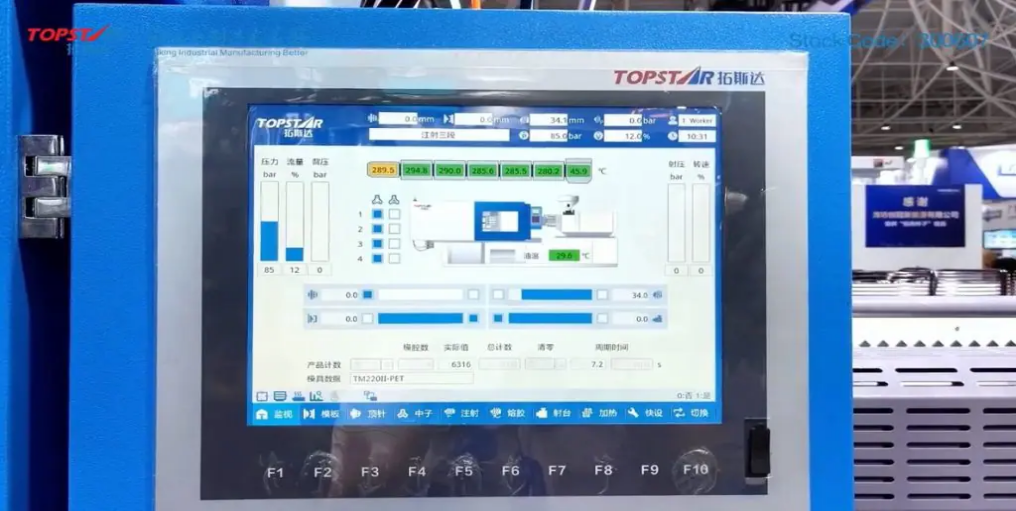
Perform regular calibrations
Regular calibration of plastic bottle making machines is also crucial to ensuring the wall thickness of the bottles. Calibration involves precise adjustment and maintenance of various parts of the machine. The calibration process usually involves the following steps:
Set up the machine according to the manufacturer’s specifications. Establish baseline parameters for temperature, pressure, and material feed rate. Regularly check the extruder, die, and die controller, and implement a monitoring system to record data continuously during production. Regular sample bottle tests measure the wall thickness at different points. Perform regular maintenance and clean machine parts to prevent any material buildup or wear that may affect calibration.
Achieve uniform wall thickness
Ensuring uniform wall thickness of plastic bottles can ensure the production of high-quality, durable and safe products. By controlling the key factors that affect wall thickness, selecting the right materials, and controlling temperature and regular calibration mentioned in the article, manufacturers can achieve and maintain uniform wall thickness of their products.
TRENDING POSTS
- What factors can cause delays in the injection molding process of plastic molding machine? 2024/07/01
- Exhibition Review| Topstar participates in InterPlas Thailand 2024 2024/07/01
- Star Case | Topstar helps Santong upgrade its intelligent plant 2024/07/01
- Topstar Special | National Science and Technology Workers Day 2024/07/01
HOT TOPIC
- 3 in 1 Compact Dehumidifying Dryer
- 5-axis CNC machine
- accuracy
- Air Chillers
- all electric injection molding machine
- all electric injection molding machines
- All-electric injection molding machines
- and overall production quality. Therefore
- AP-RubberPlas
- automated injection molding machine
- Automation changed engineering
- automation of injection molding robots
- auxiliary machine
- Bench Injection Molding Machine
- Cabinet dryer manufacturers
- Cabinet dryers
- chiller
- CNC Drilling Machine
- CNC Drilling Machines
- cnc engraving machine manufacturer
- cnc laser cutting machine manufacturer
- CNC machine
- CNC Machine Center
- CNC Machine for Sale
- CNC Machine Manufacturing
- CNC Machine Tool
- CNC machine tool product
- CNC Machining Center
- CNC wood carving machine
- Cooling system
- Cross-Walking Single Axis Servo Cylinder Robot
- Cross-Walking Single-Axis Servo Cylinder Robot
- Cross-Walking Three-Axis/Five-Axis Servo Driven Robot
- cross-walking three-axis/five-axis servo-driven robot
- Dehumidifier Dryer
- Dehumidifying Dryer
- delta parallel robot
- Desktop Injection Molding Machine
- Desktop injection molding machines
- Desktop Molding Machine
- desktop plastic injection machine
- Desktop Plastic Injection Molding Machine
- direct clamp injection molding machine
- Direct clamp injection molding machines
- Dosing & mixing system
- Drilling Centers
- Drying and dehumidification system
- drying and dehumidifying equipment
- Drying and Dehumidifying System
- drying system
- effective and efficient. Cabinet dryers are also used in other industries where large quantities of material need to be dried
- efficient injection molding machine
- elbow hydraulic injection molding machines
- electric injection molding machine
- electric injection molding machines
- energy-saving injection molding machine
- etc. Among injection molding robots
- exhibition
- features of CNC machine
- Feeding And Conveying System
- Five Axis Machine Center
- Fully automatic injection molding machine
- Gathering Topstar
- giant injection molding machine
- GMU-600 5-Axis Machining Center
- Granulating & Recycling System
- Heavy duty injection molding machine
- Honeycomb rotor dehumidifier
- horizontal injection molding machine
- Horizontal Injection Molding Machines
- Horizontal Injection Moulding Machine
- Horizontal Mixer manufacturer
- How The CNC Machine Works
- hybrid injection molding machine
- hydraulic injection molding machine
- Hydraulic Injection Molding Machines
- in this article
- Industrial robot
- Industrial Robot Chinese brand
- industrial robot parts
- industrial robot supplier
- Industrial robots
- Industry Chain
- Injection Manipulator
- injection mold machines
- Injection molding
- Injection molding automation
- Injection Molding Automation Solution
- injection molding dryer
- Injection molding equipment
- injection molding hopper dryer
- Injection molding machine
- injection molding machine brand
- Injection Molding Machine Factory
- Injection Molding Machine Manufacture
- Injection molding machine manufacturer
- injection molding machine manufacturers
- Injection molding machine procurement
- injection molding machine robotic arm
- injection molding machine with a robot
- Injection molding machines
- injection molding material dehumidifying
- injection molding plant
- Injection Molding Robot
- injection molding robot arm
- Injection molding robot automation
- Injection molding robotic arm
- injection molding robots
- Injection Moulding Robots
- Injection Robot
- Injection robot arm
- Injection robot manufacturer
- Injection robot wholesale
- injection robots
- intelligent injection molding machines
- Introducing Injection Robot
- It is the best choice for drying large quantities of material at once. Cabinetmakers use these machines because they are fast
- large injection molding machine
- Learn what industrial automation and robotics is
- low speed sound-proof granulator
- machine plastic molding
- make sure to add some! Improvements (2) Keyphrase in introduction: Your keyphrase or its synonyms appear in the first paragraph of the copy
- manipulator machine
- manufacturing
- micro injection molding machine
- middle speed granulator
- Mini CNC machine manufacturers.
- Mold Temperature Control System
- mold temperature controller
- molding material Dehumidifying System
- mould temperature controller
- mould temperature controllers
- New electric injection molding machine
- nitrogen dryer manufacturer
- nitrogen dryer system manufacturer
- Oil type mold temperature controller
- open day
- Outbound links: No outbound links appear in this page. Add some! Images: No images appear on this page. Add some! Internal links: No internal links appear in this page
- PET Preform injection molding
- phone case maker machine
- phone case making machine
- plastic bottle making machine
- plastic bottle manufacturing
- plastic bucket making machine
- plastic bucket manufacturing
- Plastic chair making machine
- plastic forming equipment
- plastic hopper dryer
- plastic injection machine
- plastic injection machines
- plastic injection molding
- Plastic injection molding equipment
- Plastic injection molding machine
- Plastic Injection Molding Machines
- plastic injection robot
- Plastic Molding machine
- Plastic Molding Machines
- plastic molding press
- plastic phone case making machine
- plastic-molding machine
- powerful granulator
- Powerful Type Sound-Proof Granulator
- production of plastic seats
- Robot injection molding
- robot injection molding machine
- robot manufacturing companies
- Robotic arm for injection molding machine
- robotic injection molding machines
- robotics in injection molding
- SCARA robot
- SCARA robots
- Service-oriented manufacturing
- Servo Cylinder Robot
- servo driven robot
- Servo Driven Robots
- servo injection robots
- Servo-Driven Robot
- Setup of injection machine
- Silicone Injection Molding Machine
- six-axis industrial robot
- Stainless Hopper Dryer
- Stainless Hopper Dryers
- star club
- swing arm robot
- the choice between servo-driven robots and hydraulic robots will have a certain impact on efficiency
- the most popular injection molding machine
- the type of injection molding robot
- toggle clamp injection molding machine
- Toggle Hydraulic Injection Molding Machines
- toggle injection molding machine
- Top 10 brands of injection robots
- Topstar
- Topstar Engineering
- Topstar Industrial Robots
- Topstar injection molding intelligent
- Topstar Scara Robots
- Useful Injection molding machine
- Vertical machining centers
- volumetric type blender
- water chiller
- water chillers
- water distributor
- Water Type MoldTemperature Controller
- We often face choices when performing injection molding. We will choose the type of injection molding machine
- wholesale of injection molding machines
- x carve CNC