How to ensure uniform temperature distribution with a mold temperature controller?
2024/08/21 By Topstar
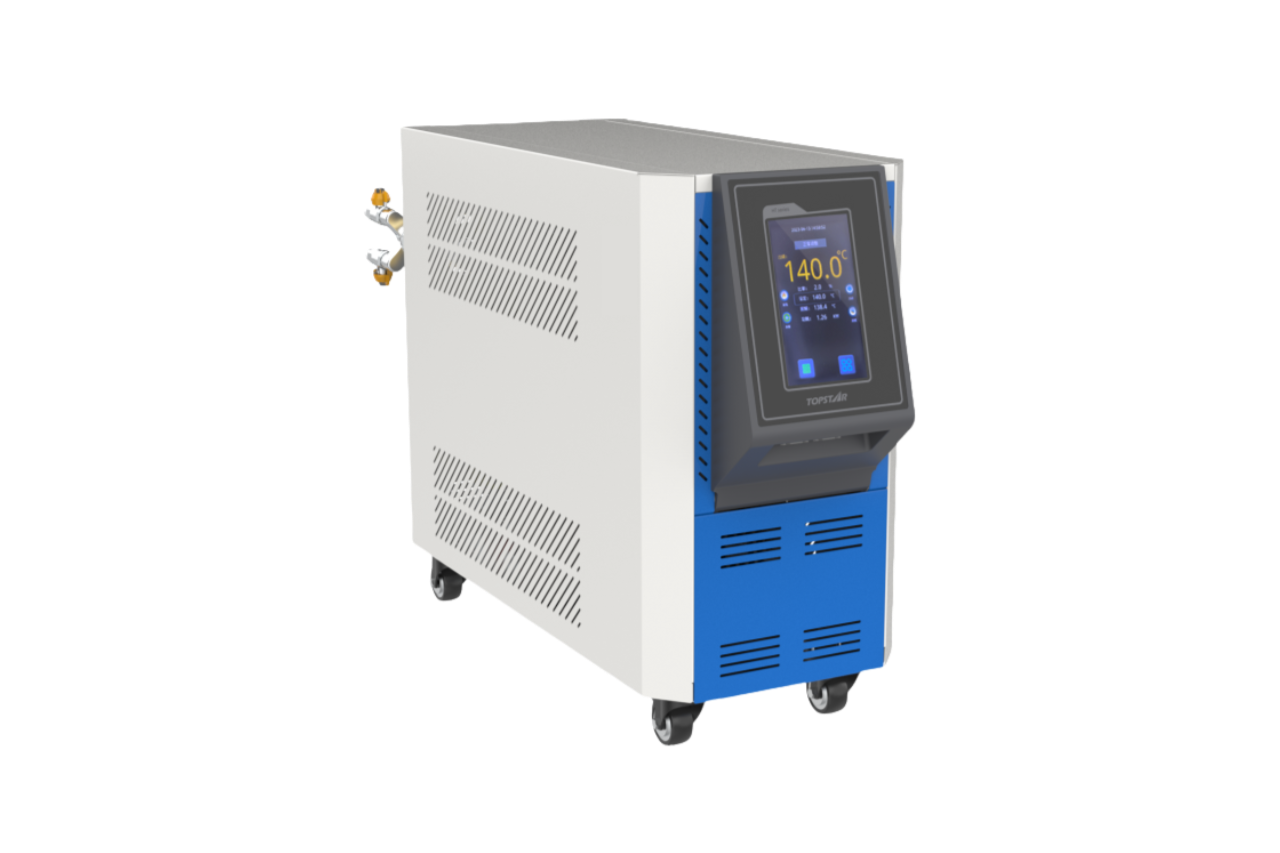
Temperature changes in the mould during injection moulding can lead to part defects, such as warping, dents, and dimensional inconsistencies that compromise the integrity of the final product. Mold temperature controllers, as injection molding auxiliary equipment, are indispensable devices in a complete production line. This ensures that the mold maintains the desired temperature throughout the production process, thereby maintaining temperature uniformity and reducing the risk of defects. Topstar’s mold temperature controllers are based on a temperature PID algorithm with a temperature control accuracy of up to ±0.1°C, ensuring temperature uniformity and having an over-temperature protection mechanism, which is a good solution to the problem of uneven temperature during operation of the mold temperature controller. Below, we will briefly introduce how they achieve uniform temperature distribution.
The role of mold temperature controller
Mold temperature controllers regulate the mold temperature by circulating a heat transfer fluid (usually water or oil) through the mold cooling channel, helping keep the mold surface temperature consistent. Their main function is to minimize temperature fluctuations due to changes in the surrounding environment, differences in material thermal properties, or differences in mold design. By providing precise temperature control, mold temperature controllers help ensure that the mold remains within the required temperature range, ensuring that the parts produced have consistent quality and dimensional consistency. Typically, they will be equipped with sensors and control systems that monitor the temperature of the heat transfer fluid and adjust the heating or cooling output as needed to maintain the target temperature.
Key factors affecting mold temperature distribution
Achieving uniform temperature distribution in the mold is affected by several key factors, one of which is the design of the mold itself. The structural design of the Topstar mold temperature controller is more sophisticated, which can better improve space utilization, and the design of the heat dissipation channel can more effectively protect the electronic components to achieve a more uniform temperature distribution.
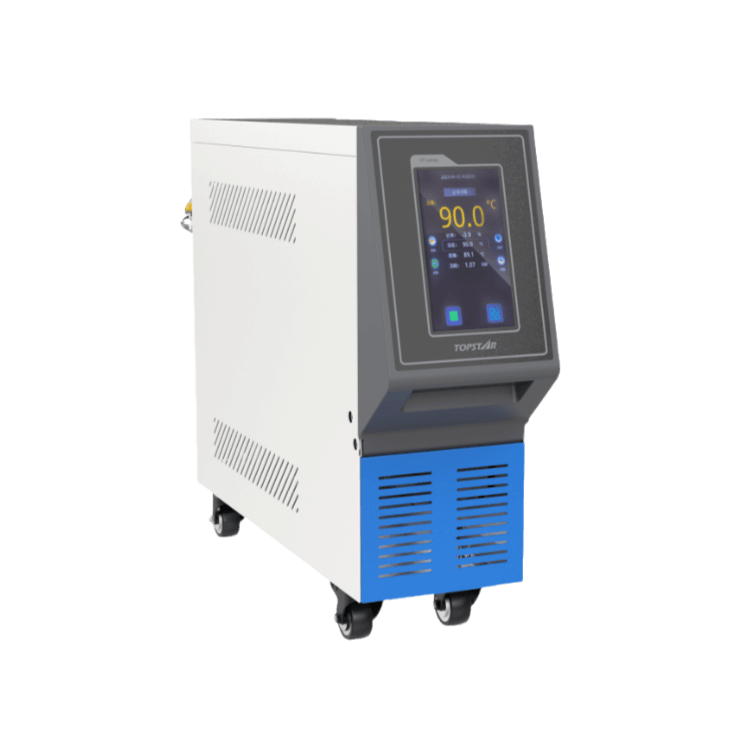
Another key factor is the thermal conductivity of the mold material. The stainless steel casting used in the frame structure of the mold temperature controller has high thermal conductivity, which can achieve rapid heat transfer and more uniform temperature distribution. In addition, the type of heat transfer fluid used also plays an important role in temperature distribution. Water and oil are the most commonly used fluids, each offering its own advantages and limitations. Water is generally ideal for applications that require rapid cooling due to its high thermal conductivity and rapid heat transfer capabilities. On the other hand, you can use oil in applications that require higher temperatures because it has a higher boiling point. Still, its thermal conductivity is lower than that of water, which affects temperature distribution.
Maintaining uniform temperature through temperature PID algorithm
Topstar’s mold temperature controller has more uniform and accurate temperature control based on temperature PID algorithm control, which can achieve a temperature control accuracy of ±0.1℃, ensuring temperature uniformity, and also has an over-temperature protection mechanism to ensure the yield of plastic products. The PID algorithm dynamically adjusts the heating and cooling process by continuously monitoring the mold temperature and making real-time corrections. Balancing these adjustments minimizes temperature fluctuations and ensures mold operates within a narrow range. This precise control is essential for producing high-quality molded products with consistent performance, reducing defects and improving overall production efficiency.
The mold temperature control system is more intelligent.
The open communication interface of the mold temperature controller can realize interconnection with other equipment, which can improve the collaborative efficiency of the entire production process and optimize staffing to the greatest extent. At the same time, the system automatically records the equipment operation status and alarm log, improves fault response speed and maintenance efficiency, and reduces downtime. The 7-inch touch screen on the front of the mold temperature controller makes the display more intuitive, allowing operators to operate through the screen and better control the temperature parameters to make the temperature more uniform. Through real-time data collection and analysis, they can autonomously predict temperature changes and make precise adjustments. This self-control capability continuously optimizes to ensure the system maintains the mold temperature at the desired set point.
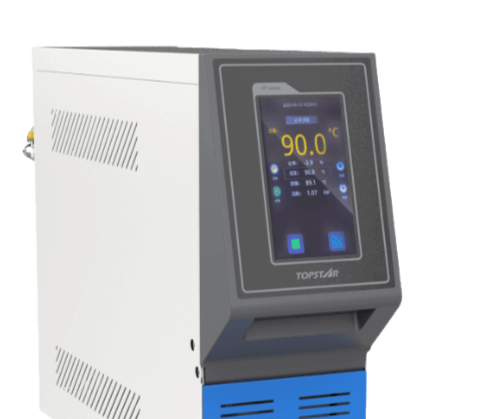
The impact of uniform temperature distribution on product quality
If the temperature changes in the mold, a series of defects and inconsistencies will occur, damaging the integrity, appearance and performance of the molded parts. One of the most common defects is warping. Warping occurs when different areas of the part cool at different rates, and the material shrinks unevenly. This distorts the shape of the part, making it difficult to fit or assemble with other parts. Another defect may also occur. When the part’s surface cools and solidifies faster than the material below, dents will appear, causing the surface to sink inward, forming unsightly depressions and affecting its appearance and structural integrity.
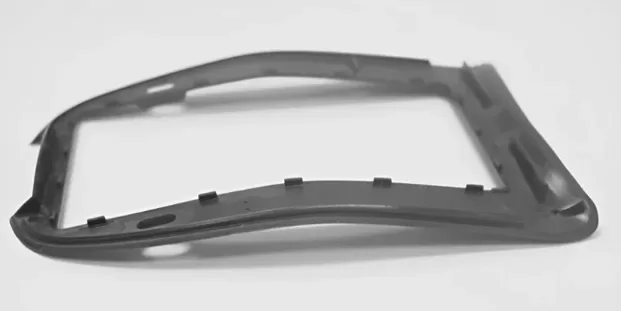
Inconsistent temperature distribution can also cause changes in the mechanical properties of the part. Different areas of the part may cool and solidify at different rates, resulting in changes in the crystallinity and molecular structure of the material. The final product’s appearance will also be affected by temperature changes in the mold. Inconsistent temperatures can lead to color variations, surface defects, and poor texture.
Achieve uniform temperature distribution.
Topstar’s mold temperature controller can achieve uniform temperature distribution through the PID algorithm and intelligent system settings. In addition, manufacturers can improve temperature uniformity and overall production efficiency by solving common challenges such as ambient temperature fluctuations, material thermal properties, and flow rate imbalance.
TRENDING POSTS
- What factors can cause delays in the injection molding process of plastic molding machine? 2024/08/21
- Exhibition Review| Topstar participates in InterPlas Thailand 2024 2024/08/21
- Star Case | Topstar helps Santong upgrade its intelligent plant 2024/08/21
- Topstar Special | National Science and Technology Workers Day 2024/08/21
HOT TOPIC
- .ervo motor-driven linear robots
- 3 axis robot
- 3 axis robots
- 3 in 1 Compact Dehumidifying Dryer
- 3-axis robot
- 3-axis robots
- 5-axis CNC machine
- accuracy
- Air Chillers
- all electric injection molding machine
- all electric injection molding machines
- All-electric injection molding machines
- and overall production quality. Therefore
- AP-RubberPlas
- automated injection molding machine
- Automation changed engineering
- automation of injection molding robots
- auxiliary machine
- Bench Injection Molding Machine
- Cabinet dryer manufacturers
- Cabinet dryers
- chiller
- CNC Drilling Machine
- CNC Drilling Machines
- cnc engraving machine manufacturer
- cnc laser cutting machine manufacturer
- CNC machine
- CNC Machine Center
- CNC Machine for Sale
- CNC Machine Manufacturing
- CNC Machine Tool
- CNC machine tool product
- CNC Machining Center
- CNC wood carving machine
- Cooling system
- Cross-Walking Single Axis Servo Cylinder Robot
- Cross-Walking Single-Axis Servo Cylinder Robot
- Cross-Walking Three-Axis/Five-Axis Servo Driven Robot
- cross-walking three-axis/five-axis servo-driven robot
- Dehumidifier Dryer
- Dehumidifying Dryer
- delta parallel robot
- Desktop Injection Molding Machine
- Desktop injection molding machines
- Desktop Molding Machine
- desktop plastic injection machine
- Desktop Plastic Injection Molding Machine
- direct clamp injection molding machine
- Direct clamp injection molding machines
- Dosing & mixing system
- Drilling Centers
- Drying and dehumidification system
- drying and dehumidifying equipment
- Drying and Dehumidifying System
- drying system
- effective and efficient. Cabinet dryers are also used in other industries where large quantities of material need to be dried
- efficient injection molding machine
- elbow hydraulic injection molding machines
- electric injection molding machine
- electric injection molding machines
- energy-efficient injection molding robot
- energy-saving injection molding machine
- etc. Among injection molding robots
- exhibition
- features of CNC machine
- Feeding And Conveying System
- Five Axis Machine Center
- Fully automatic injection molding machine
- Gathering Topstar
- giant injection molding machine
- GMU-600 5-Axis Machining Center
- Granulating & Recycling System
- Heavy duty injection molding machine
- High-precision electric molding machines
- high-precision plastic molding machines
- high-speed all electric injection molding machine
- Honeycomb rotor dehumidifier
- horizontal injection molding machine
- Horizontal Injection Molding Machines
- Horizontal Injection Moulding Machine
- Horizontal Mixer manufacturer
- How The CNC Machine Works
- hybrid injection molding machine
- hydraulic injection molding machine
- Hydraulic Injection Molding Machines
- in this article
- Industrial robot
- Industrial Robot Chinese brand
- industrial robot parts
- industrial robot supplier
- Industrial robots
- Industry Chain
- Injection Manipulator
- injection manipulator robot
- injection mold machines
- Injection molding
- Injection molding automation
- Injection Molding Automation Solution
- injection molding dryer
- Injection molding equipment
- injection molding hopper dryer
- Injection molding machine
- injection molding machine brand
- Injection Molding Machine Factory
- Injection Molding Machine Manufacture
- Injection molding machine manufacturer
- injection molding machine manufacturers
- Injection molding machine procurement
- injection molding machine robotic arm
- injection molding machine with a robot
- Injection molding machines
- injection molding material dehumidifying
- injection molding plant
- Injection Molding Robot
- injection molding robot arm
- Injection molding robot automation
- Injection molding robotic arm
- injection molding robots
- Injection moulding machine
- Injection Moulding Robots
- Injection Robot
- Injection robot arm
- Injection robot manufacturer
- Injection robot wholesale
- injection robots
- intelligent injection molding machines
- Introducing Injection Robot
- It is the best choice for drying large quantities of material at once. Cabinetmakers use these machines because they are fast
- large injection molding machine
- Learn what industrial automation and robotics is
- linear robot
- linear robots
- low speed sound-proof granulator
- machine plastic molding
- make sure to add some! Improvements (2) Keyphrase in introduction: Your keyphrase or its synonyms appear in the first paragraph of the copy
- manipulator machine
- manufacturing
- medical grade injection molding machines
- medical injection molding machine
- medical injection molding machines
- micro injection molding machine
- middle speed granulator
- Mini CNC machine manufacturers.
- Mold Temperature Control System
- mold temperature controller
- mold temperature controllers
- molding material Dehumidifying System
- mould temperature control system
- mould temperature controller
- mould temperature controllers
- New electric injection molding machine
- nitrogen dryer manufacturer
- nitrogen dryer system manufacturer
- Oil type mold temperature controller
- Oil type mold temperature controllers
- open day
- Outbound links: No outbound links appear in this page. Add some! Images: No images appear on this page. Add some! Internal links: No internal links appear in this page
- PET Preform injection molding
- phone case maker machine
- phone case making machine
- plastic bottle making machine
- plastic bottle manufacturing
- plastic bucket making machine
- plastic bucket manufacturing
- Plastic chair making machine
- plastic forming equipment
- plastic hopper dryer
- plastic injection machine
- plastic injection machines
- plastic injection molding
- Plastic injection molding equipment
- Plastic injection molding machine
- Plastic Injection Molding Machines
- plastic injection moulding machine
- plastic injection robot
- Plastic Molding machine
- Plastic Molding Machines
- plastic molding press
- plastic moulding machine
- plastic phone case making machine
- plastic-molding machine
- powerful granulator
- Powerful Type Sound-Proof Granulator
- precision injection molding
- production of plastic seats
- pure water mould temperature controller
- Robot injection molding
- robot injection molding machine
- robot manufacturing companies
- Robotic arm for injection molding machine
- robotic injection molding machines
- robotics in injection molding
- SCARA robot
- SCARA robots
- Service-oriented manufacturing
- Servo Cylinder Robot
- servo driven robot
- Servo Driven Robots
- servo injection robots
- servo motor-driven linear robots
- servo-driven 3-axis robot
- Servo-Driven Robot
- Setup of injection machine
- Silicone Injection Molding Machine
- six-axis industrial robot
- Stainless Hopper Dryer
- Stainless Hopper Dryers
- star club
- swing arm robot
- take-out robots
- the choice between servo-driven robots and hydraulic robots will have a certain impact on efficiency
- the most popular injection molding machine
- the type of injection molding robot
- toggle clamp injection molding machine
- Toggle Hydraulic Injection Molding Machines
- toggle injection molding machine
- Top 10 brands of injection robots
- Topstar
- Topstar Engineering
- Topstar Industrial Robots
- Topstar injection molding intelligent
- Topstar Scara Robots
- Useful Injection molding machine
- Vertical machining centers
- volumetric type blender
- water chiller
- water chillers
- water distributor
- water type mold temperature controller
- Water Type MoldTemperature Controller
- Water-Type Mould Temperature Controllers
- We often face choices when performing injection molding. We will choose the type of injection molding machine
- wholesale of injection molding machines
- x carve CNC