How to choose a chiller according to the actual injection molding situation?
2025/03/21 By Topstar
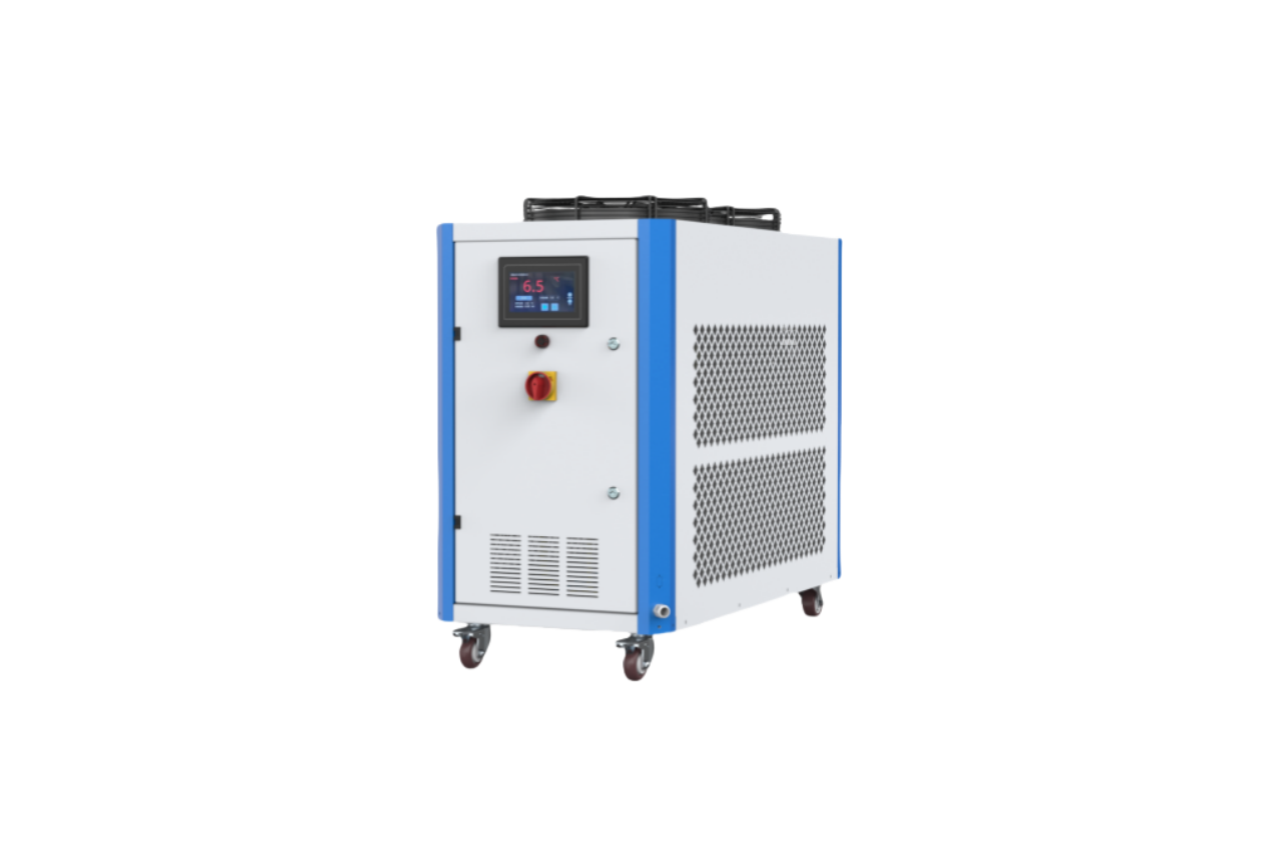
Chillers can remove excess heat from the injection molding system, ensuring the mold and material maintain optimal processing conditions. For injection molding production, the decision of the chiller is not only about cooking but also about ensuring the stability of the entire manufacturing process. An efficient chiller system can prevent common problems caused by thermal fluctuations, such as warping, incomplete curing, or defects in molded products. For injection molding users, choosing a chiller requires careful consideration of several factors, including production volume, specific materials processed, and available infrastructure. If you are a user with a stable water supply, you may prefer a water-cooled chiller because of its energy-saving characteristics and efficient cooling performance. In contrast, air-cooled chillers are more suitable for you in places with limited water resources or installation space.
Key Considerations for Selecting a Chiller
The first thing to consider is the heat load of the injection molding process. Facilities with large production volumes and materials that are particularly sensitive to temperature fluctuations may be better suited to using water chillers. These systems’ advanced multi-compressor staged control ensures they can effectively handle large heat loads, maintain consistent mold temperatures, and prevent problems such as part warping or incomplete curing. In contrast, air chillers may be a more practical choice for operations with moderate heat demands or limited water resources. Their ease of installation and low maintenance requirements can reduce overall operating costs. In addition, air-cooled systems are less dependent on external water quality and circulation systems, which can be a significant advantage in areas where water treatment and supply are brutal.
Another key factor is the installation environment. Available workshop space, the layout of the production facility, and the existing infrastructure all play a role in determining which chiller type is more suitable. Water-cooled chillers require additional components such as cooling towers, water pumps, and filtration systems. On the other hand, air chillers feature a compact and self-contained design that can be easily integrated into existing production lines without extensive modifications.
Performance of water chillers in injection molding
Water chillers mainly rely on external water sources. Water reflects its performance, which provides a more stable and efficient heat exchange medium than air. Using water as a coolant enables these chillers to achieve lower operating temperatures and maintain a high degree of temperature uniformity across the mold surface. To better reflect the cooling performance in injection molding, Topstar’s water-cooled chiller models use a multi-compressor hierarchical control system that adjusts the operation of each compressor according to real-time thermal demand, optimizing the cooling process and improving cooling performance.
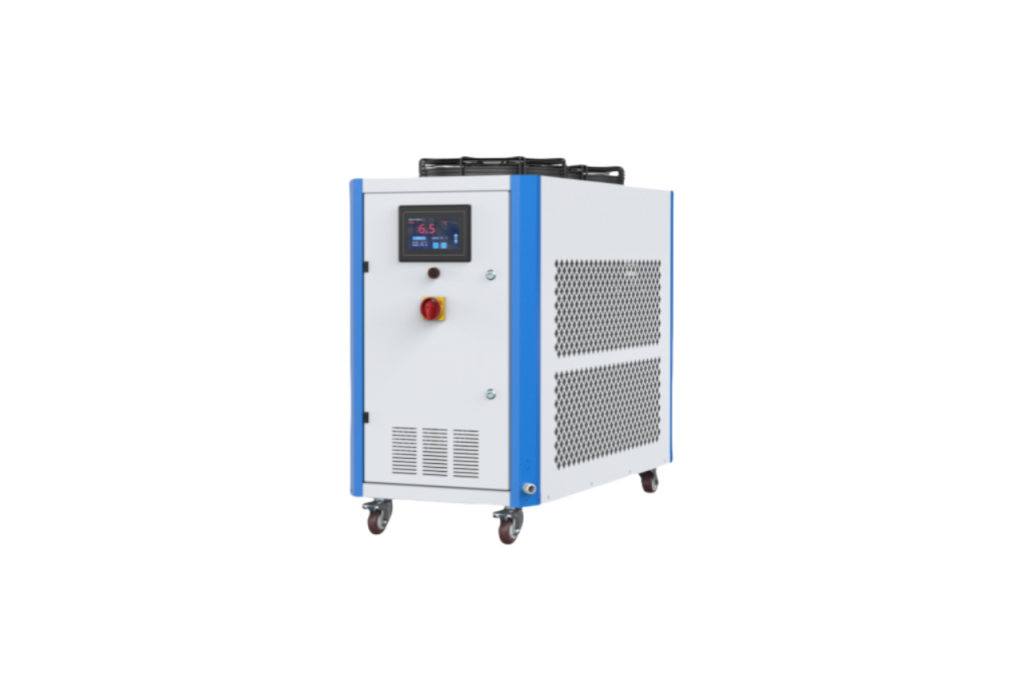
The multi-compressor hierarchical control mechanism can adapt to changing load conditions during the injection molding cycle. During high heat loads, the system will add compressors to provide fast and consistent cooling to ensure the mold maintains a stable temperature. Under low load conditions, the system will reduce compressor activity, reducing energy consumption without affecting performance, thereby achieving comprehensive efficiency and energy-saving effects.
Benefits of air chillers for injection molding
Air chillers have become a practical alternative for injection molding applications where external water sources are unavailable or cannot be used. Their main advantage is that they are easy to install. In a small number of injection molding workshop environments, the space is relatively small, and there is no ability to connect to external water resources. Topstar’s air-cooled models are designed to maximize installation efficiency while minimizing footprint, making them ideal for facilities where space constraints are an essential consideration.
With no external water source required, they can be installed quickly with minimal disruption to existing production lines. At the same time, we use nut-to-lock on the coils, achieving no welds in contact with water, which is more corrosion-resistant. This simplifies maintenance and reduces the possibility of water-related problems such as scaling or corrosion. This is a relatively easy-to-implement versatile cooling solution for injection molding plants in areas with limited water resources.
Comparative Analysis and Selection of the Two Chillers
The multi-compressor staged control of water-cooled chillers excels in energy efficiency and temperature regulation. Therefore, it is particularly suitable for high-demand applications with large heat loads and the need for precise temperature control to avoid defects in molded products. The robust performance of water chillers makes them an ideal choice for workshops with water infrastructure.
In contrast, air chillers have low installation and maintenance requirements and a compact design, making them the choice of facilities in areas with limited space or scarce or unstable water resources. While they may be slightly less energy efficient than water chillers, their simplicity of operation often makes up for this shortcoming, especially in applications with lower cooling loads. They place a greater emphasis on convenience and quick setup in the injection molding shop.
Optimizing Energy Efficiency for Injection Molding
In addition to the inherent energy efficiency of both chiller types, Topstar’s chillers can integrate with the injection molding machine and other auxiliary equipment around it, allowing for continuous optimization through unified monitoring and control capabilities. Operators can track energy consumption in real-time and adjust system settings to reduce waste further. This level of control is critical in today’s manufacturing industry, where even minor improvements in energy efficiency can significantly impact operating costs. In addition, energy efficiency not only reduces costs but also increases the reliability and lifespan of the system. An efficiently operating chiller is less likely to experience wear and tear due to overworked components, resulting in fewer failures and lower maintenance costs.
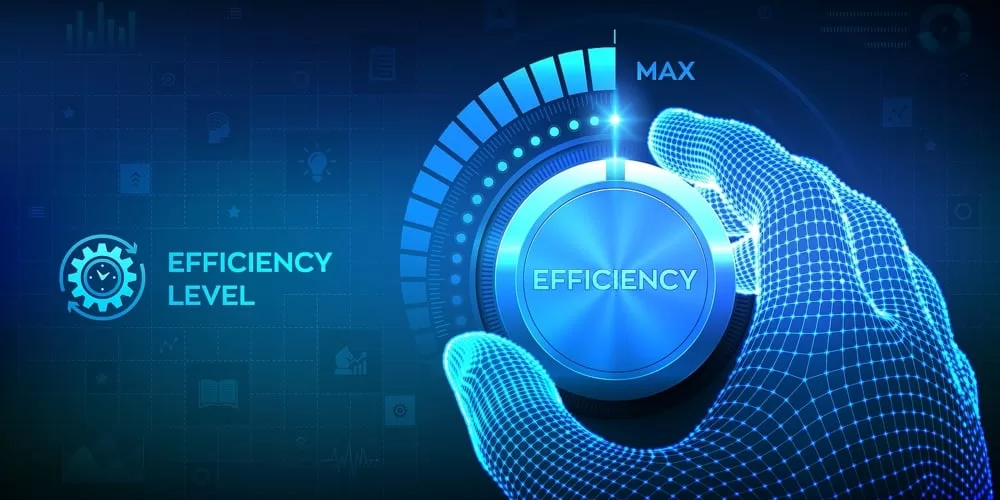
Providing customized chiller solutions for injection molding
When selecting a chiller, we will comprehensively assess your injection molding process, including heat load, available infrastructure, and energy management goals. In addition, we consider the immediate cooling needs and the long-term impact of its selection, such as operating costs, maintenance requirements, and potential scalability. By balancing these factors, we provide users with a suitable chiller to ensure optimal temperature control and improve overall production efficiency and product quality.
TRENDING POSTS
- What factors can cause delays in the injection molding process of plastic molding machine? 2025/03/21
- Exhibition Review| Topstar participates in InterPlas Thailand 2024 2025/03/21
- Star Case | Topstar helps Santong upgrade its intelligent plant 2025/03/21
- Topstar Special | National Science and Technology Workers Day 2025/03/21
HOT TOPIC
- .ervo motor-driven linear robots
- 1.0 guangdong topstar technology co. ltd
- 1.0 topstar china
- 1.0 topstar robot
- 11
- 2
- 21
- 23
- 3 axis robot
- 3 axis robots
- 3 in 1 Compact Dehumidifying Dryer
- 3-axis robot
- 3-axis robots
- 39
- 41
- 5-axis CNC machine
- 62
- accuracy
- Air Chillers
- all electric injection molding machine
- all electric injection molding machines
- All-electric injection molding machines
- and overall production quality. Therefore
- AP-RubberPlas
- automated injection molding machine
- Automation changed engineering
- automation of injection molding robots
- auxiliary machine
- Bench Injection Molding Machine
- Cabinet dryer manufacturers
- Cabinet dryers
- chiller
- CNC Drilling Machine
- CNC Drilling Machines
- cnc engraving machine manufacturer
- cnc laser cutting machine manufacturer
- CNC machine
- CNC Machine Center
- CNC Machine for Sale
- CNC Machine Manufacturing
- CNC Machine Tool
- CNC machine tool product
- CNC Machining Center
- CNC wood carving machine
- Cooling system
- Cross-Walking Single Axis Servo Cylinder Robot
- Cross-Walking Single-Axis Servo Cylinder Robot
- Cross-Walking Three-Axis/Five-Axis Servo Driven Robot
- cross-walking three-axis/five-axis servo-driven robot
- Dehumidifier Dryer
- Dehumidifying Dryer
- delta parallel robot
- Desktop Injection Molding Machine
- Desktop injection molding machines
- Desktop Molding Machine
- desktop plastic injection machine
- Desktop Plastic Injection Molding Machine
- direct clamp injection molding machine
- Direct clamp injection molding machines
- Dosing & mixing system
- Drilling Centers
- Drying and dehumidification system
- drying and dehumidifying equipment
- Drying and Dehumidifying System
- drying system
- effective and efficient. Cabinet dryers are also used in other industries where large quantities of material need to be dried
- efficient injection molding machine
- elbow hydraulic injection molding machines
- electric injection molding machine
- electric injection molding machines
- energy-efficient injection molding robot
- energy-efficient water chiller
- energy-efficient water chillers
- energy-saving injection molding machine
- etc. Among injection molding robots
- exhibition
- features of CNC machine
- Feeding And Conveying System
- Five Axis Machine Center
- Fully automatic injection molding machine
- Gathering Topstar
- giant injection molding machine
- GMU-600 5-Axis Machining Center
- Granulating & Recycling System
- Heavy duty injection molding machine
- High-precision electric molding machines
- high-precision plastic molding machines
- high-speed all electric injection molding machine
- Honeycomb rotor dehumidifier
- horizontal injection molding machine
- Horizontal Injection Molding Machines
- Horizontal Injection Moulding Machine
- Horizontal Mixer manufacturer
- How The CNC Machine Works
- hybrid injection molding machine
- hydraulic injection molding machine
- Hydraulic Injection Molding Machines
- in this article
- Industrial robot
- Industrial Robot Chinese brand
- industrial robot parts
- industrial robot supplier
- Industrial robots
- Industry Chain
- Injection Manipulator
- injection manipulator robot
- injection mold machines
- Injection molding
- Injection molding automation
- Injection Molding Automation Solution
- injection molding dryer
- Injection molding equipment
- injection molding hopper dryer
- Injection molding machine
- injection molding machine brand
- Injection Molding Machine Factory
- Injection Molding Machine Manufacture
- Injection molding machine manufacturer
- injection molding machine manufacturers
- Injection molding machine procurement
- injection molding machine robotic arm
- injection molding machine with a robot
- Injection molding machines
- injection molding material dehumidifying
- injection molding plant
- Injection Molding Robot
- injection molding robot arm
- Injection molding robot automation
- Injection molding robotic arm
- injection molding robots
- Injection moulding machine
- injection moulding machines
- Injection Moulding Robots
- Injection Robot
- Injection robot arm
- Injection robot manufacturer
- Injection robot wholesale
- injection robots
- intelligent injection molding machines
- Introducing Injection Robot
- It is the best choice for drying large quantities of material at once. Cabinetmakers use these machines because they are fast
- Large flow water type mold temperature controller
- large injection molding machine
- large injection molding machines
- Learn what industrial automation and robotics is
- linear robot
- linear robots
- low speed sound-proof granulator
- machine plastic molding
- make sure to add some! Improvements (2) Keyphrase in introduction: Your keyphrase or its synonyms appear in the first paragraph of the copy
- manipulator machine
- manufacturing
- medical grade injection molding machines
- medical injection molding machine
- medical injection molding machines
- micro injection molding machine
- middle speed granulator
- Mini CNC machine manufacturers.
- Mold Temperature Control System
- mold temperature controller
- mold temperature controllers
- molding material Dehumidifying System
- mould temperature control system
- mould temperature controller
- mould temperature controllers
- New electric injection molding machine
- nitrogen dryer manufacturer
- nitrogen dryer system manufacturer
- Oil type mold temperature controller
- Oil type mold temperature controllers
- open day
- Outbound links: No outbound links appear in this page. Add some! Images: No images appear on this page. Add some! Internal links: No internal links appear in this page
- PET Preform injection molding
- phone case maker machine
- phone case making machine
- plastic bottle making machine
- plastic bottle manufacturing
- plastic bucket making machine
- plastic bucket manufacturing
- Plastic chair making machine
- plastic forming equipment
- plastic hopper dryer
- plastic injection machine
- plastic injection machines
- plastic injection molding
- Plastic injection molding equipment
- Plastic injection molding machine
- Plastic Injection Molding Machines
- plastic injection moulding machine
- plastic injection moulding machines
- plastic injection robot
- Plastic Molding machine
- Plastic Molding Machines
- plastic molding press
- plastic moulding machine
- plastic phone case making machine
- plastic-molding machine
- powerful granulator
- Powerful Type Sound-Proof Granulator
- precision injection molding
- precision injection molding machines
- production of plastic seats
- pure water mould temperature controller
- Robot injection molding
- robot injection molding machine
- robot manufacturing companies
- Robotic arm for injection molding machine
- robotic injection molding machines
- robotics in injection molding
- SCARA robot
- SCARA robots
- Service-oriented manufacturing
- Servo Cylinder Robot
- servo driven robot
- Servo Driven Robots
- servo injection molding machine
- servo injection robots
- servo motor-driven linear robots
- servo-driven 3-axis robot
- Servo-Driven Robot
- Setup of injection machine
- Silicone Injection Molding Machine
- six-axis industrial robot
- Stainless Hopper Dryer
- Stainless Hopper Dryers
- star club
- swing arm robot
- take-out robot
- take-out robots
- the choice between servo-driven robots and hydraulic robots will have a certain impact on efficiency
- the most popular injection molding machine
- the type of injection molding robot
- toggle clamp injection molding machine
- Toggle Hydraulic Injection Molding Machines
- toggle injection molding machine
- Top 10 brands of injection robots
- Topstar
- Topstar Engineering
- Topstar Industrial Robots
- Topstar injection molding intelligent
- Topstar Scara Robots
- Useful Injection molding machine
- Vertical machining centers
- volumetric type blender
- water chiller
- water chillers
- water distributor
- water type mold temperature controller
- Water Type MoldTemperature Controller
- Water-Type Mould Temperature Controllers
- We often face choices when performing injection molding. We will choose the type of injection molding machine
- wholesale of injection molding machines
- x carve CNC
- 热门查询 点击次数 展示 排名 topstar