How to avoid the strain on the plastic injection molding machine?
2025/03/12 By Topstar
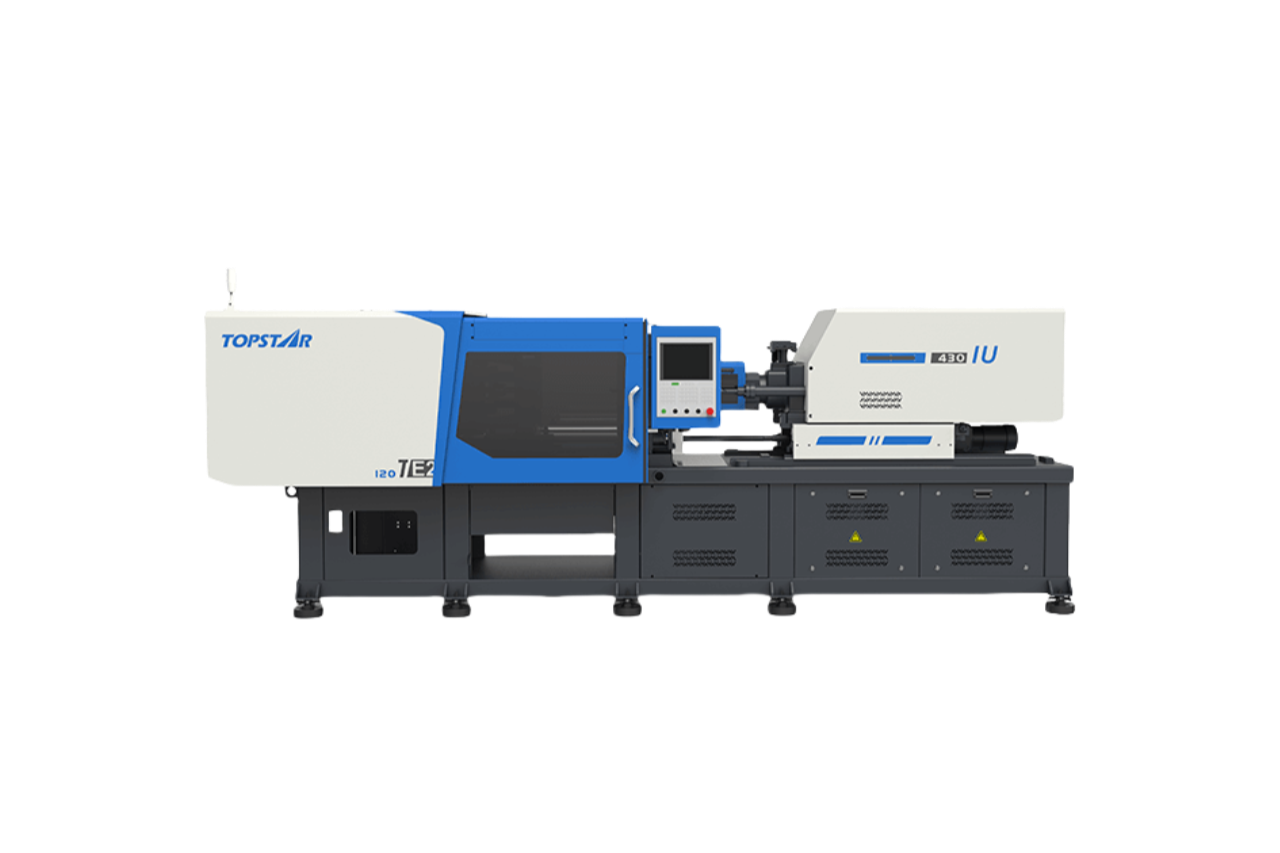
In the clamping unit of a plastic injection molding machine, tie rods are responsible for holding the two halves of the mold together under high clamping forces. However, the friction generated by continuous motion and the necessity for lubrication can cause the coring rods to be overstressed and eventually fail, which occurs when excessive friction or misalignment damages the tie rod strain (also known as coring rods) during the clamping process. This phenomenon not only compromises the mechanical integrity of the plastic injection molding machine but also adversely affects the final product’s dimensional accuracy. To this end, Topstar’s approach is to rethink the design by eliminating direct contact between the tie rods and the moving mold components. Topstar uses a non-contact tie rod with advanced engineering technology to maintain alignment and secure clamping without friction or dependence on lubrication.
Problems with Traditional Lubricated Tie Rods in Plastic Injection Molding Machine
Traditional tie rods require oil to reduce friction between the rod and the moving platen. However, lubricants attract contaminants such as dust, metal chips, and plastic particles, forming an abrasive slurry that accelerates wear. The lubricant emulsifies, loses effectiveness, and causes unstable clamping force in a humid environment. The expected effect is not achieved. Variations in lubricant application, temperature fluctuations, and chemical degradation can all lead to uneven stress distribution. Many North American plastics manufacturers report that tie rod replacement costs have increased by 40% due to lubricant contamination. In addition, excess grease often drips onto the mold or finished product, causing cosmetic defects and violating FDA standards for medical or food-grade products.
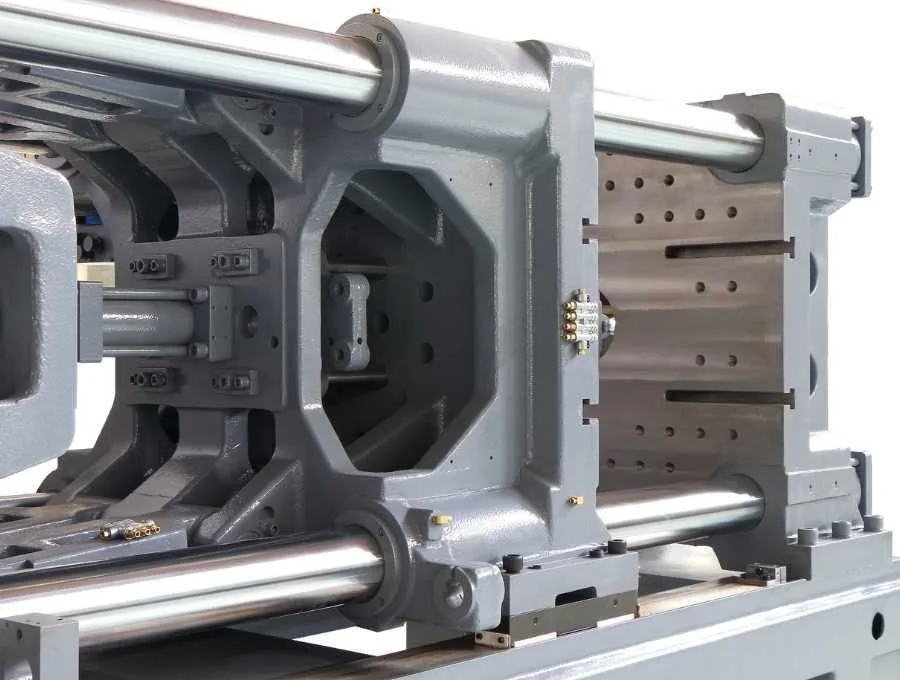
Topstar’s non-contact tie rod system: Eliminating lubrication in plastic injection molding machine
Topstar’s innovative non-contact tie rod system integrates an unpowered roller equipped with a hinge mechanism directly connected to the coring material output. This ingenious arrangement allows the clamping force to transmit evenly to the mold without physical contact with the coring rod. As a result, traditional friction and wear are significantly reduced, and the need for continuous lubrication is eliminated. The absence of lubrication also lowers maintenance costs by 30%.
In the actual production process, preventing direct friction between the tie rod and the coring rod can reduce mechanical strain and coring rod strain. This reduces the wear rate of key mold components and extends their service life, thereby shortening maintenance intervals and improving the uptime of plastic injection molding machines.
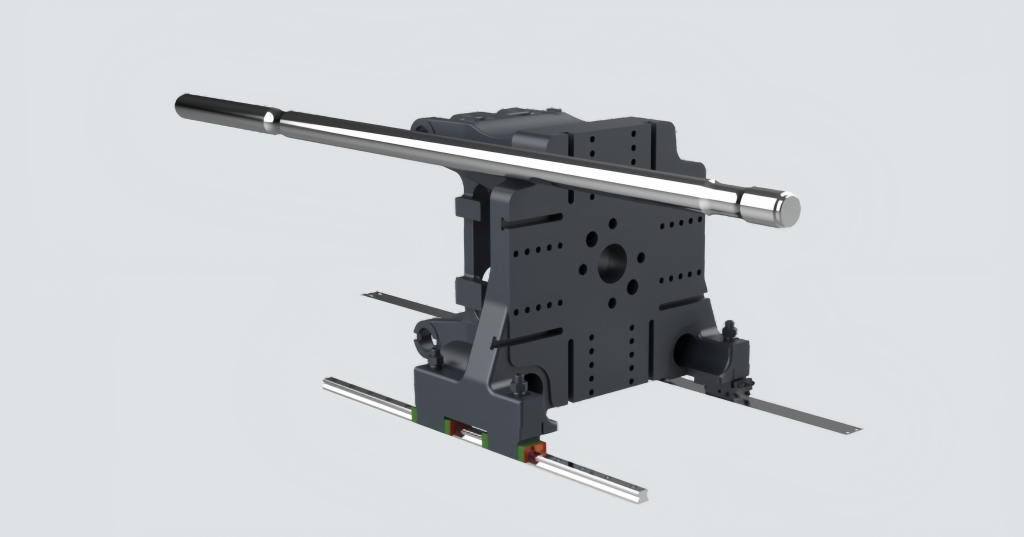
Operational Benefits of Non-Contact Tie-Bar Systems
Traditional injection molding machine tie-bar systems require periodic lubrication and are prone to inconsistencies due to uneven lubricant application, temperature variations, and performance degradation caused by friction. In contrast, our non-contact tie bars eliminate these issues, resulting in a more stable clamping force and evenly distributing pressure across the mold. Another benefit lies in improved product quality. In injection molding, even minor deviations in clamping force can lead to defects such as burrs, warping, or incomplete filling. By maintaining consistent force without the interference of variable lubrication, our plastic injection molding machines can produce parts that are dimensionally accurate and free of common molding defects. In addition, the non-contact design simplifies the entire injection molding production process, eliminating the need for operators to monitor and adjust lubricant levels, thereby reducing the complexity of daily maintenance tasks.
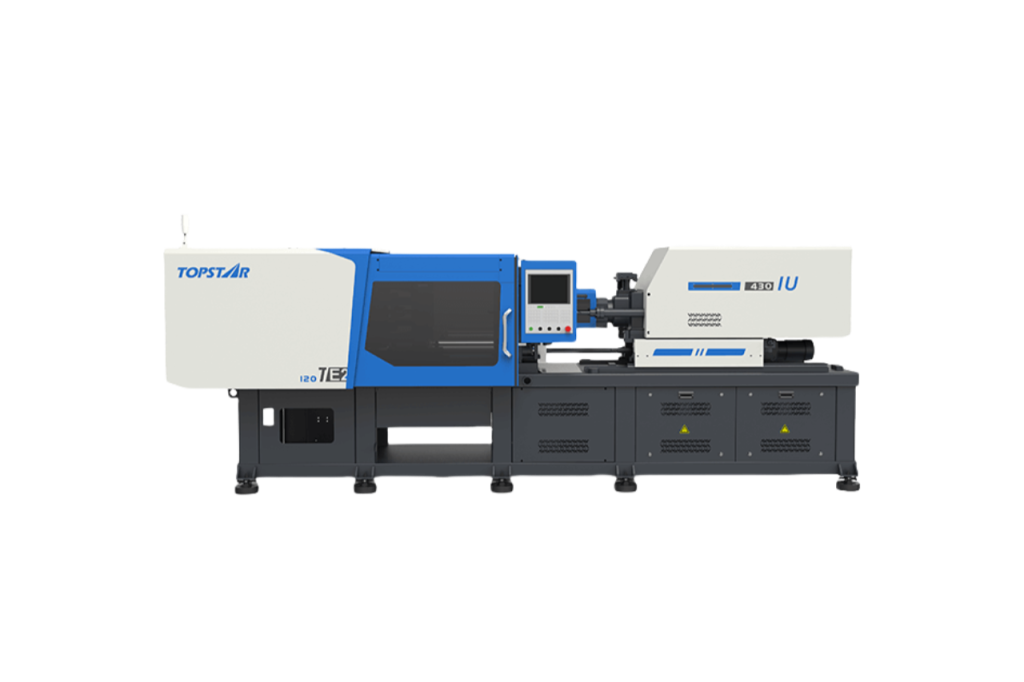
How Non-Contact Tie-Bars Protect Plastic Injection Molding Machines?
Tie-bar strain can shorten the life of critical components such as platens, molds, and hydraulic systems. Topstar’s non-contact design minimizes mechanical stress and extends the machine’s life by 25-40%. Among customer feedback, a Thai packaging company using Topstar plastic injection molding machines reported 95% original part functionality, while competitor equipment required a complete overhaul after 6 years. Reduced vibration also maintains mold integrity, saving tens of thousands of dollars in replacement costs annually.
Maintenance, Environmental Advantages
Because traditional tie rod systems produce wear and tear, coring rods appear. The need for constant lubrication leads to unstable performance and increases the risk of contamination. Over time, this can lead to expensive repairs, extended downtime, and increased waste from spent lubricants. In contrast, the non-contact tie rod design eliminates the need for such maintenance. Since constant lubrication is not required, the machine runs cleaner, and the risk of oil-induced contamination is virtually eliminated.
Lubricants, while essential in traditional systems, can become a source of contamination if not appropriately managed. They often require special handling and disposal procedures to prevent environmental harm. Topstar’s electric plastic injection molding machines support a cleaner production process. This complies with modern ecological regulations and is suitable for industries such as medicine, precision optics, etc.
Avoid Tie rod strain.
Tie rod strain no longer plagues plastic injection molding machines. Topstar’s non-contact system eliminates the need for lubrication, reduces contamination, and extends equipment life, combining reliability and sustainability. By adopting this technology, manufacturers can focus on production rather than maintenance while meeting stringent environmental standards.
TRENDING POSTS
- What factors can cause delays in the injection molding process of plastic molding machine? 2025/03/12
- Exhibition Review| Topstar participates in InterPlas Thailand 2024 2025/03/12
- Star Case | Topstar helps Santong upgrade its intelligent plant 2025/03/12
- Topstar Special | National Science and Technology Workers Day 2025/03/12
HOT TOPIC
- 3 in 1 Compact Dehumidifying Dryer
- 5-axis CNC machine
- accuracy
- Air Chillers
- all electric injection molding machine
- All-electric injection molding machines
- and overall production quality. Therefore
- AP-RubberPlas
- automated injection molding machine
- Automation changed engineering
- automation of injection molding robots
- auxiliary machine
- Bench Injection Molding Machine
- Cabinet dryer manufacturers
- Cabinet dryers
- chiller
- CNC Drilling Machine
- CNC Drilling Machines
- cnc engraving machine manufacturer
- cnc laser cutting machine manufacturer
- CNC machine
- CNC Machine Center
- CNC Machine for Sale
- CNC Machine Manufacturing
- CNC Machine Tool
- CNC machine tool product
- CNC Machining Center
- CNC wood carving machine
- Cooling system
- Cross-Walking Single Axis Servo Cylinder Robot
- Cross-Walking Single-Axis Servo Cylinder Robot
- Cross-Walking Three-Axis/Five-Axis Servo Driven Robot
- cross-walking three-axis/five-axis servo-driven robot
- Dehumidifier Dryer
- Dehumidifying Dryer
- delta parallel robot
- Desktop Injection Molding Machine
- Desktop injection molding machines
- Desktop Molding Machine
- desktop plastic injection machine
- Desktop Plastic Injection Molding Machine
- direct clamp injection molding machine
- Direct clamp injection molding machines
- Dosing & mixing system
- Drilling Centers
- Drying and dehumidification system
- drying and dehumidifying equipment
- Drying and Dehumidifying System
- drying system
- effective and efficient. Cabinet dryers are also used in other industries where large quantities of material need to be dried
- efficient injection molding machine
- elbow hydraulic injection molding machines
- electric injection molding machine
- electric injection molding machines
- etc. Among injection molding robots
- exhibition
- features of CNC machine
- Feeding And Conveying System
- Five Axis Machine Center
- Fully automatic injection molding machine
- Gathering Topstar
- giant injection molding machine
- GMU-600 5-Axis Machining Center
- Granulating & Recycling System
- Heavy duty injection molding machine
- Honeycomb rotor dehumidifier
- horizontal injection molding machine
- Horizontal Injection Molding Machines
- Horizontal Injection Moulding Machine
- Horizontal Mixer manufacturer
- How The CNC Machine Works
- hybrid injection molding machine
- hydraulic injection molding machine
- Hydraulic Injection Molding Machines
- in this article
- Industrial robot
- Industrial Robot Chinese brand
- industrial robot parts
- industrial robot supplier
- Industrial robots
- Industry Chain
- Injection Manipulator
- injection mold machines
- Injection molding
- Injection molding automation
- Injection Molding Automation Solution
- injection molding dryer
- Injection molding equipment
- injection molding hopper dryer
- Injection molding machine
- injection molding machine brand
- Injection Molding Machine Factory
- Injection Molding Machine Manufacture
- Injection molding machine manufacturer
- injection molding machine manufacturers
- Injection molding machine procurement
- injection molding machine robotic arm
- injection molding machine with a robot
- Injection molding machines
- injection molding material dehumidifying
- injection molding plant
- Injection Molding Robot
- injection molding robot arm
- Injection molding robot automation
- Injection molding robotic arm
- injection molding robots
- Injection Moulding Robots
- Injection Robot
- Injection robot arm
- Injection robot manufacturer
- Injection robot wholesale
- injection robots
- intelligent injection molding machines
- Introducing Injection Robot
- It is the best choice for drying large quantities of material at once. Cabinetmakers use these machines because they are fast
- large injection molding machine
- Learn what industrial automation and robotics is
- low speed sound-proof granulator
- machine plastic molding
- make sure to add some! Improvements (2) Keyphrase in introduction: Your keyphrase or its synonyms appear in the first paragraph of the copy
- manipulator machine
- manufacturing
- micro injection molding machine
- middle speed granulator
- Mini CNC machine manufacturers.
- Mold Temperature Control System
- mold temperature controller
- molding material Dehumidifying System
- mould temperature controller
- mould temperature controllers
- New electric injection molding machine
- nitrogen dryer manufacturer
- nitrogen dryer system manufacturer
- Oil type mold temperature controller
- open day
- Outbound links: No outbound links appear in this page. Add some! Images: No images appear on this page. Add some! Internal links: No internal links appear in this page
- PET Preform injection molding
- phone case maker machine
- phone case making machine
- plastic bottle making machine
- plastic bottle manufacturing
- plastic bucket making machine
- plastic bucket manufacturing
- Plastic chair making machine
- plastic forming equipment
- plastic hopper dryer
- plastic injection machine
- plastic injection machines
- plastic injection molding
- Plastic injection molding equipment
- Plastic injection molding machine
- Plastic Injection Molding Machines
- plastic injection robot
- Plastic Molding machine
- Plastic Molding Machines
- plastic molding press
- plastic phone case making machine
- plastic-molding machine
- powerful granulator
- Powerful Type Sound-Proof Granulator
- production of plastic seats
- Robot injection molding
- robot injection molding machine
- robot manufacturing companies
- Robotic arm for injection molding machine
- robotic injection molding machines
- robotics in injection molding
- SCARA robot
- SCARA robots
- Service-oriented manufacturing
- Servo Cylinder Robot
- servo driven robot
- Servo Driven Robots
- servo injection robots
- Servo-Driven Robot
- Setup of injection machine
- Silicone Injection Molding Machine
- six-axis industrial robot
- Stainless Hopper Dryer
- Stainless Hopper Dryers
- star club
- swing arm robot
- the choice between servo-driven robots and hydraulic robots will have a certain impact on efficiency
- the most popular injection molding machine
- the type of injection molding robot
- toggle clamp injection molding machine
- Toggle Hydraulic Injection Molding Machines
- toggle injection molding machine
- Top 10 brands of injection robots
- Topstar
- Topstar Engineering
- Topstar Industrial Robots
- Topstar injection molding intelligent
- Topstar Scara Robots
- Useful Injection molding machine
- Vertical machining centers
- volumetric type blender
- water chiller
- water chillers
- water distributor
- Water Type MoldTemperature Controller
- We often face choices when performing injection molding. We will choose the type of injection molding machine
- wholesale of injection molding machines
- x carve CNC