How to achieve rapid response and stable temperature control of mould temperature controller?
2025/03/28 By Topstar
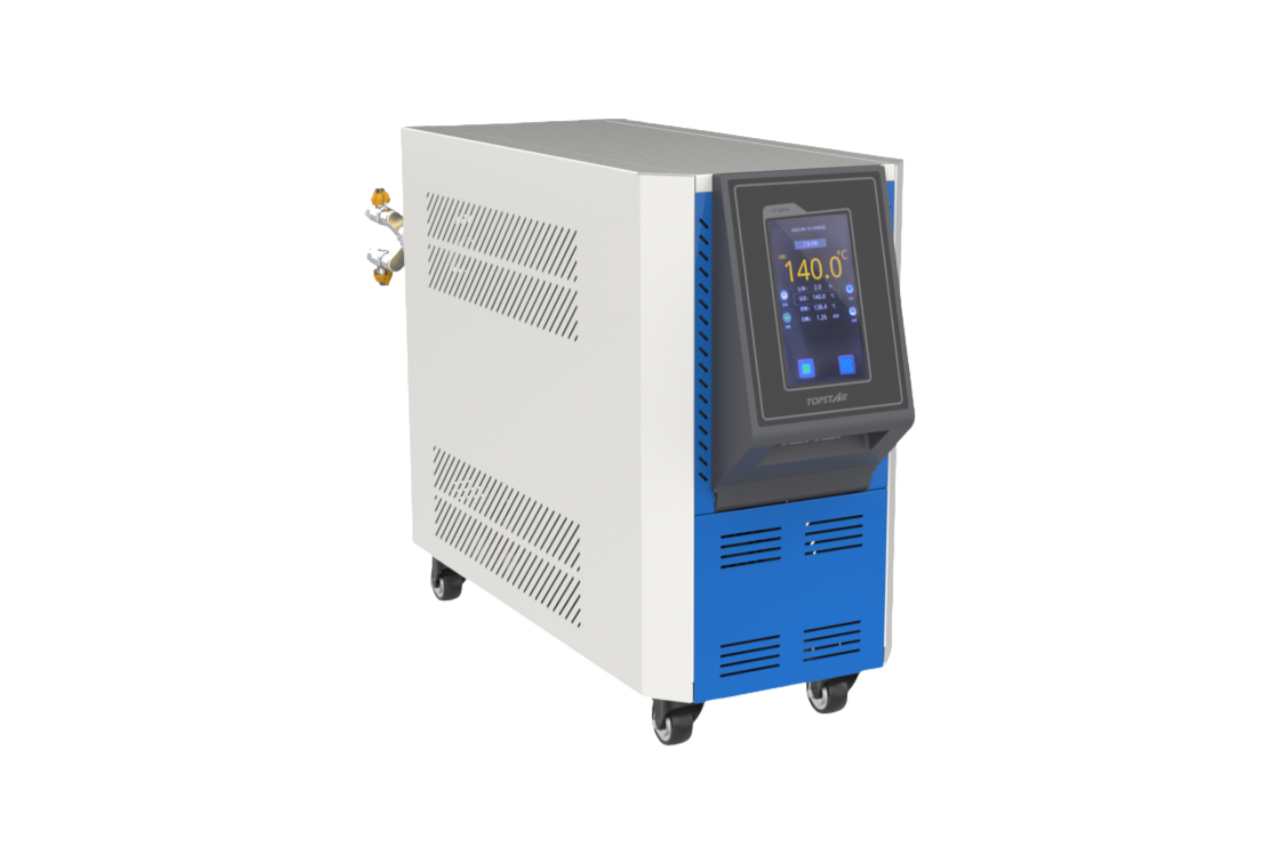
In industrial manufacturing, the performance of the mould temperature controller directly affects production efficiency and product quality. Two key indicators determine its effectiveness: speed (how quickly it reaches the target temperature) and accuracy (how accurately it maintains that temperature). Slow response times delay production cycles, while unstable temperatures can lead to defects such as inconsistent material properties. In addition, mould temperature controllers that heat or cool slowly force the machine to consume additional electricity to make up for the delay, increasing operating costs and carbon footprint. Similarly, unstable temperature profiles can increase material waste.
The role of PID algorithms in optimizing mould temperature controllers
At the heart of Topstar’s mould temperature controllers is the PID algorithm, a mathematical framework that adjusts heating/cooling output based on real-time feedback. Improperly adjusted PID parameters can lead to overshoot, oscillation, or sluggish response. For example, excessive integral action can lead to extended settling times, while insufficient derivative control cannot offset sudden heat loads. Topstar’s engineers focus on dynamic PID adjustments to accommodate different mould loads and environmental conditions, ensuring seamless transitions between heating and cooling stages. However, traditional PID systems face limitations in today’s complex production environments, where fixed PID settings struggle to adapt to materials with widely varying geometric complexity and often require manual recalibration for each new project.
To address this problem, Topstar proposes mould load adaptive temperature intelligent control and feeds this information into the PID algorithm. The result is that the controller can “learn” the unique thermal behaviour of the mould, whether it is a high-inertia system that needs to be gradually heated or a fast-cycling application that requires aggressive cooling.
Key indicators of mould temperature controllers – speed and accuracy
When evaluating the performance of any mould temperature controller, two indicators stand out: speed and accuracy. Speed refers to the controller’s ability to react quickly to temperature changes. Accuracy refers to how accurately the controller maintains the temperature at the set point. These two indicators work together to ensure that the mould temperature controller can provide a fast corrective response and a continuously stable operating environment.
Fast response is an important factor, especially in a high-volume production environment. The faster the mould temperature controller detects deviations from the target temperature and makes corresponding adjustments, the less downtime and waste there will be. With multiple moulds or production lines running simultaneously, the cumulative benefits of fast response can translate into significant time and energy savings.
The accuracy of temperature control is equally important. In many manufacturing processes, even slight deviations from the target temperature can affect the quality of the final product. Plastic properties can change dramatically with temperature fluctuations. Accurate mould temperature controllers minimize these changes by maintaining a stable temperature, thereby reducing the risk of defects and ensuring consistent product quality. This stability is achieved by fine-tuning PID parameters, which directly affects how the controller responds to temperature deviations.
Adaptive Load Intelligent Control
Traditional mould temperature controllers rely on fixed PID settings that struggle with unpredictable variables such as mould complexity, material variations, or ambient temperature changes. Topstar’s R&D team developed the Mold Load Adaptive Intelligent Temperature Control.
What makes this intelligent temperature control different is its ability to handle many different scenarios, namely situations where mould specifications are incomplete or environmental factors are unstable. Traditional controllers may overcompensate during the temperature control process, flooding the entire system with coolant, wasting energy and causing temperature fluctuations. However, Mold Load Adaptive Intelligent Temperature Control identifies these anomalies through pattern recognition and applies targeted adjustments. By utilizing sensors and feedback mechanisms, the mould temperature controller continuously evaluates the condition of the mould and adjusts its operating parameters accordingly. It ensures a quick reaction to any temperature deviations and also maintains the level of precision necessary for high-quality production.
20% faster convergence: How to improve mould temperature controller efficiency
Compared with traditional PID systems, the mould temperature controller with “mould load adaptive temperature intelligent control” reduces the temperature convergence time by 20%. For example, using traditional methods, it may take 8 minutes for a PET preform mould to reach 180°C, while it only takes 6 minutes with the Topstar mould temperature controller.
This acceleration is due to:
- Instant load detection: The sensor identifies the mould characteristics within seconds after startup.
- Aggressive preheating: Maximize energy input in the initial stage without overshooting.
- Predictive cooling: Anticipate cooling needs to minimize lag.
Efficiency gains are not limited to raw speed. In beverage packaging production, faster temperature convergence enables manufacturers to switch between different bottle designs. The mould temperature controller’s adaptive logic automatically recalibrates the settings for each mould type. After this intelligent control system, mould maintenance costs are reduced by 30%, resulting in smoother temperature transitions.
Simplify operation and improve user experience.
User-friendly design is essential for mould temperature controllers – especially in manufacturing environments where downtime and complexity can affect productivity.
One of the outstanding features of Topstar mould temperature controllers is a one-button start operation. This innovation greatly simplifies the setup process, allowing operators to start the control system with just one press. Such a design shortens the learning curve and minimizes the risk of operator error. Thanks to the combination of PID tuning and adaptive control, users can focus on monitoring the process. At the same time, the intuitive user interface provides real-time feedback on temperature status, system alarms, and operating parameters, and it is easy to access, ensuring that operators can quickly diagnose and solve any problems that may arise during production.
Achieve fast response and stable accuracy.
The fast response and accuracy of mould temperature controllers are no longer optional – they are competitive necessities. By combining adaptive PID adjustment, machine learning and powerful engineering design, Topstar’s mould temperature controllers have a temperature rise convergence speed that is 20% faster than traditional control methods and a temperature control accuracy of ±0.1℃. Manufacturers can now achieve higher quality and efficient production through intelligent, self-adjusting temperature control systems.
TRENDING POSTS
- What factors can cause delays in the injection molding process of plastic molding machine? 2025/03/28
- Exhibition Review| Topstar participates in InterPlas Thailand 2024 2025/03/28
- Star Case | Topstar helps Santong upgrade its intelligent plant 2025/03/28
- Topstar Special | National Science and Technology Workers Day 2025/03/28
HOT TOPIC
- .ervo motor-driven linear robots
- 1.0 guangdong topstar technology co. ltd
- 1.0 topstar china
- 1.0 topstar robot
- 11
- 2
- 21
- 23
- 3 axis robot
- 3 axis robots
- 3 in 1 Compact Dehumidifying Dryer
- 3-axis robot
- 3-axis robots
- 39
- 41
- 5-axis CNC machine
- 62
- accuracy
- Air Chillers
- all electric injection molding machine
- all electric injection molding machines
- All-electric injection molding machines
- and overall production quality. Therefore
- AP-RubberPlas
- automated injection molding machine
- Automation changed engineering
- automation of injection molding robots
- auxiliary machine
- Bench Injection Molding Machine
- Cabinet dryer manufacturers
- Cabinet dryers
- chiller
- CNC Drilling Machine
- CNC Drilling Machines
- cnc engraving machine manufacturer
- cnc laser cutting machine manufacturer
- CNC machine
- CNC Machine Center
- CNC Machine for Sale
- CNC Machine Manufacturing
- CNC Machine Tool
- CNC machine tool product
- CNC Machining Center
- CNC wood carving machine
- Cooling system
- Cross-Walking Single Axis Servo Cylinder Robot
- Cross-Walking Single-Axis Servo Cylinder Robot
- Cross-Walking Three-Axis/Five-Axis Servo Driven Robot
- cross-walking three-axis/five-axis servo-driven robot
- Dehumidifier Dryer
- Dehumidifying Dryer
- delta parallel robot
- Desktop Injection Molding Machine
- Desktop injection molding machines
- Desktop Molding Machine
- desktop plastic injection machine
- Desktop Plastic Injection Molding Machine
- direct clamp injection molding machine
- Direct clamp injection molding machines
- Dosing & mixing system
- Drilling Centers
- Drying and dehumidification system
- drying and dehumidifying equipment
- Drying and Dehumidifying System
- drying system
- effective and efficient. Cabinet dryers are also used in other industries where large quantities of material need to be dried
- efficient injection molding machine
- elbow hydraulic injection molding machines
- electric injection molding machine
- electric injection molding machines
- energy-efficient injection molding robot
- energy-efficient water chiller
- energy-efficient water chillers
- energy-saving injection molding machine
- etc. Among injection molding robots
- exhibition
- features of CNC machine
- Feeding And Conveying System
- Five Axis Machine Center
- Fully automatic injection molding machine
- Gathering Topstar
- giant injection molding machine
- GMU-600 5-Axis Machining Center
- Granulating & Recycling System
- Heavy duty injection molding machine
- High-precision electric molding machines
- high-precision plastic molding machines
- high-speed all electric injection molding machine
- Honeycomb rotor dehumidifier
- horizontal injection molding machine
- Horizontal Injection Molding Machines
- Horizontal Injection Moulding Machine
- Horizontal Mixer manufacturer
- How The CNC Machine Works
- hybrid injection molding machine
- hydraulic injection molding machine
- Hydraulic Injection Molding Machines
- in this article
- Industrial robot
- Industrial Robot Chinese brand
- industrial robot parts
- industrial robot supplier
- Industrial robots
- Industry Chain
- Injection Manipulator
- injection manipulator robot
- injection mold machines
- Injection molding
- Injection molding automation
- Injection Molding Automation Solution
- injection molding dryer
- Injection molding equipment
- injection molding hopper dryer
- Injection molding machine
- injection molding machine brand
- Injection Molding Machine Factory
- Injection Molding Machine Manufacture
- Injection molding machine manufacturer
- injection molding machine manufacturers
- Injection molding machine procurement
- injection molding machine robotic arm
- injection molding machine with a robot
- Injection molding machines
- injection molding material dehumidifying
- injection molding plant
- Injection Molding Robot
- injection molding robot arm
- Injection molding robot automation
- Injection molding robotic arm
- injection molding robots
- Injection moulding machine
- injection moulding machines
- Injection Moulding Robots
- Injection Robot
- Injection robot arm
- Injection robot manufacturer
- Injection robot wholesale
- injection robots
- intelligent injection molding machines
- Introducing Injection Robot
- It is the best choice for drying large quantities of material at once. Cabinetmakers use these machines because they are fast
- Large flow water type mold temperature controller
- large injection molding machine
- large injection molding machines
- Learn what industrial automation and robotics is
- linear robot
- linear robots
- low speed sound-proof granulator
- machine plastic molding
- make sure to add some! Improvements (2) Keyphrase in introduction: Your keyphrase or its synonyms appear in the first paragraph of the copy
- manipulator machine
- manufacturing
- medical grade injection molding machines
- medical injection molding machine
- medical injection molding machines
- micro injection molding machine
- middle speed granulator
- Mini CNC machine manufacturers.
- Mold Temperature Control System
- mold temperature controller
- mold temperature controllers
- molding material Dehumidifying System
- mould temperature control system
- mould temperature controller
- mould temperature controllers
- New electric injection molding machine
- nitrogen dryer manufacturer
- nitrogen dryer system manufacturer
- Oil type mold temperature controller
- Oil type mold temperature controllers
- open day
- Outbound links: No outbound links appear in this page. Add some! Images: No images appear on this page. Add some! Internal links: No internal links appear in this page
- PET Preform injection molding
- phone case maker machine
- phone case making machine
- plastic bottle making machine
- plastic bottle manufacturing
- plastic bucket making machine
- plastic bucket manufacturing
- Plastic chair making machine
- plastic forming equipment
- plastic hopper dryer
- plastic injection machine
- plastic injection machines
- plastic injection molding
- Plastic injection molding equipment
- Plastic injection molding machine
- Plastic Injection Molding Machines
- plastic injection moulding machine
- plastic injection moulding machines
- plastic injection robot
- Plastic Molding machine
- Plastic Molding Machines
- plastic molding press
- plastic moulding machine
- plastic phone case making machine
- plastic-molding machine
- powerful granulator
- Powerful Type Sound-Proof Granulator
- precision injection molding
- precision injection molding machines
- production of plastic seats
- pure water mould temperature controller
- Robot injection molding
- robot injection molding machine
- robot manufacturing companies
- Robotic arm for injection molding machine
- robotic injection molding machines
- robotics in injection molding
- SCARA robot
- SCARA robots
- Service-oriented manufacturing
- Servo Cylinder Robot
- servo driven robot
- Servo Driven Robots
- servo injection molding machine
- servo injection robots
- servo motor-driven linear robots
- servo-driven 3-axis robot
- Servo-Driven Robot
- Setup of injection machine
- Silicone Injection Molding Machine
- six-axis industrial robot
- Stainless Hopper Dryer
- Stainless Hopper Dryers
- star club
- swing arm robot
- take-out robot
- take-out robots
- the choice between servo-driven robots and hydraulic robots will have a certain impact on efficiency
- the most popular injection molding machine
- the type of injection molding robot
- toggle clamp injection molding machine
- Toggle Hydraulic Injection Molding Machines
- toggle injection molding machine
- Top 10 brands of injection robots
- Topstar
- Topstar Engineering
- Topstar Industrial Robots
- Topstar injection molding intelligent
- Topstar Scara Robots
- Useful Injection molding machine
- Vertical machining centers
- volumetric type blender
- water chiller
- water chillers
- water distributor
- water type mold temperature controller
- Water Type MoldTemperature Controller
- Water-Type Mould Temperature Controllers
- We often face choices when performing injection molding. We will choose the type of injection molding machine
- wholesale of injection molding machines
- x carve CNC
- 热门查询 点击次数 展示 排名 topstar