How Plastic Molding Machines Improve the Quality of Plastic Toys?
2024/12/06 By Topstar
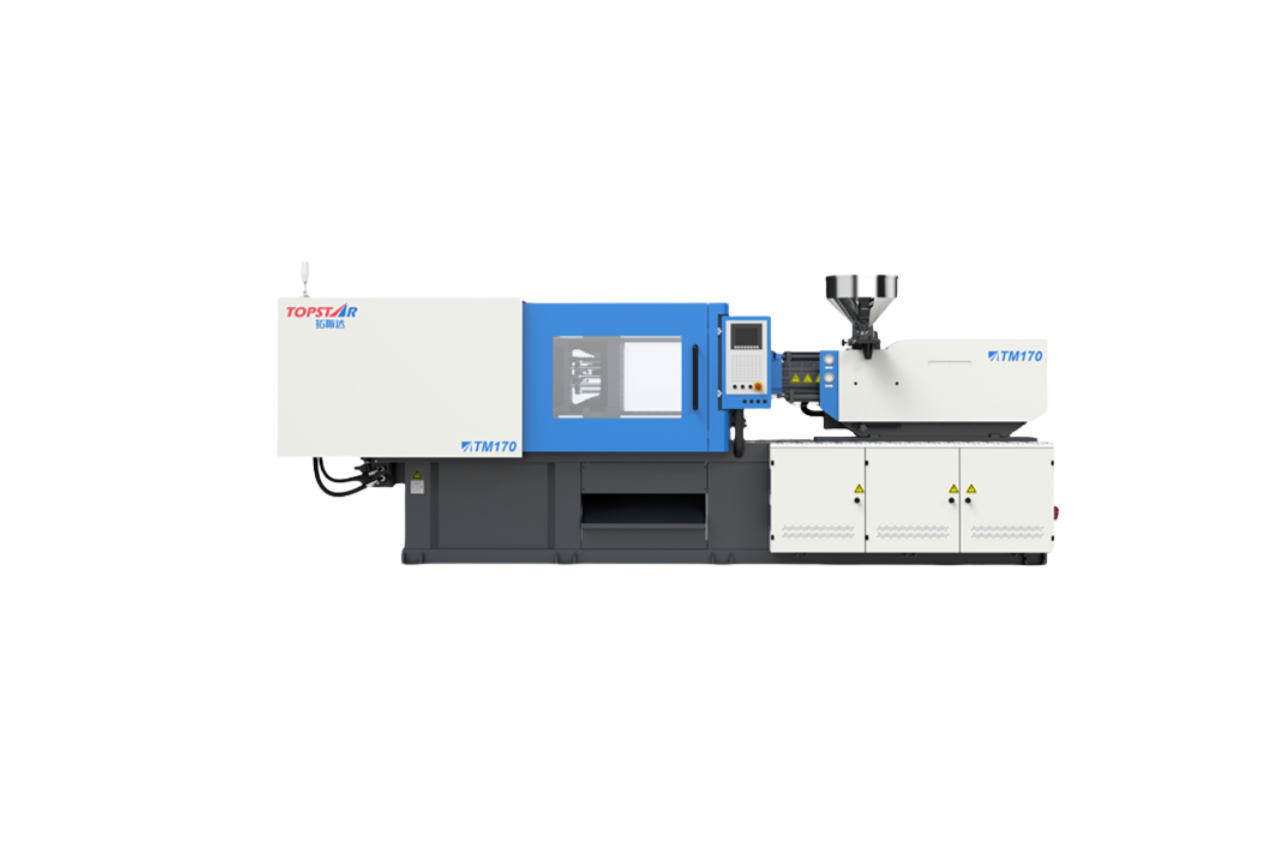
Plastic toys still occupy a large part of the global toy market. If these large and small plastic toy companies want to stand out, in addition to unique designs, they must also improve quality to make their products last longer. Their quality can vary greatly due to factors such as material consistency, mold design, and injection molding process. One of the most critical factors affecting overall quality is the plastic molding machine. The parameter settings of the plastic molding machine, the performance level, and other factors will affect the final toy quality. Therefore, in this guide, we will briefly introduce you to the common problems of plastic toys, the factors that cause these problems, and how Topstar’s plastic molding machines can deal with and solve these problems.
Common Problems with Plastic Toys
Common problems with plastic toys include burrs, warping, surface defects, poor color consistency, and even health hazards caused by substandard plastic materials. These problems usually occur due to outdated machines, inefficient molding processes, and poor quality control. Flash is one of the most common problems faced by plastic toy manufacturers. Flash refers to excess plastic overflowing the mold cavity, creating rough edges or excess material, which affects the appearance and safety of the toy. Warping refers to uneven cooling of the plastic, causing the toy to lose its original shape or deform. Surface defects can also make toys less visually appealing, reducing their overall market value.
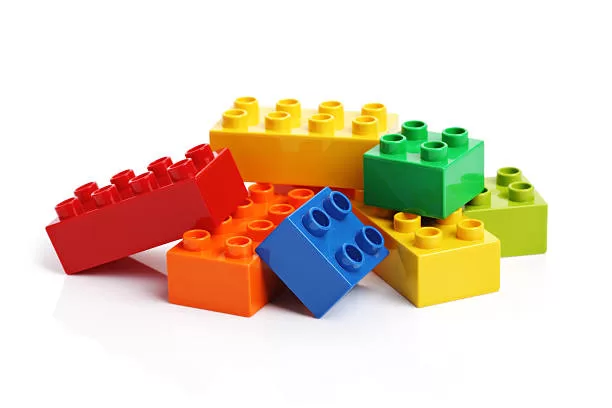
What causes quality problems in plastic toys?
Quality problems in plastic toys often stem from issues in the injection molding process. Conventional plastic molding machines can be subject to various limitations. For example, inconsistent temperature control, pressure fluctuations, and poor mold design can all lead to defects in the final product. If temperature control is not precise, it can cause uneven cooling, which can cause distorted or defective toy shapes. Inconsistent pressure during an injection can cause voids or incomplete filling of the mold, creating weak points that compromise the structural integrity of the toy.
In addition, the type of material used in the molding process and the consistency of the original plastic also determine the durability and overall quality of the finished toy. Of course, old or outdated plastic molding machines may not have the latest technology required to produce high-precision molds or process modern, high-quality plastics. This leads to a need for more consistency and quality issues in the finished product.
How do plastic molding machines solve these problems?
In the face of inconsistent temperature control, Topstar’s plastic molding machines can be integrated with mold temperature controllers for equipment interconnection. Through self-developed system integration, the primary and auxiliary machines are combined, and sensor technology is used to achieve optimal temperature control. The PID temperature control algorithm used in the mold temperature controller can improve the temperature control efficiency by 10% and ensure the uniformity of the mold temperature. Accurate temperature regulation ensures uniform cooling of the plastic and reduces the occurrence of problems such as warping. In terms of pressure control, the system adopts proportional back pressure control to achieve a multi-stage back pressure setting, which increases precision and improves the plasticization quality. When facing different plastics, we use three small parts of precision PVD alloy and a standard electroplated screw to control better the temperature of the feed port, suitable for a broader range of rubber materials.
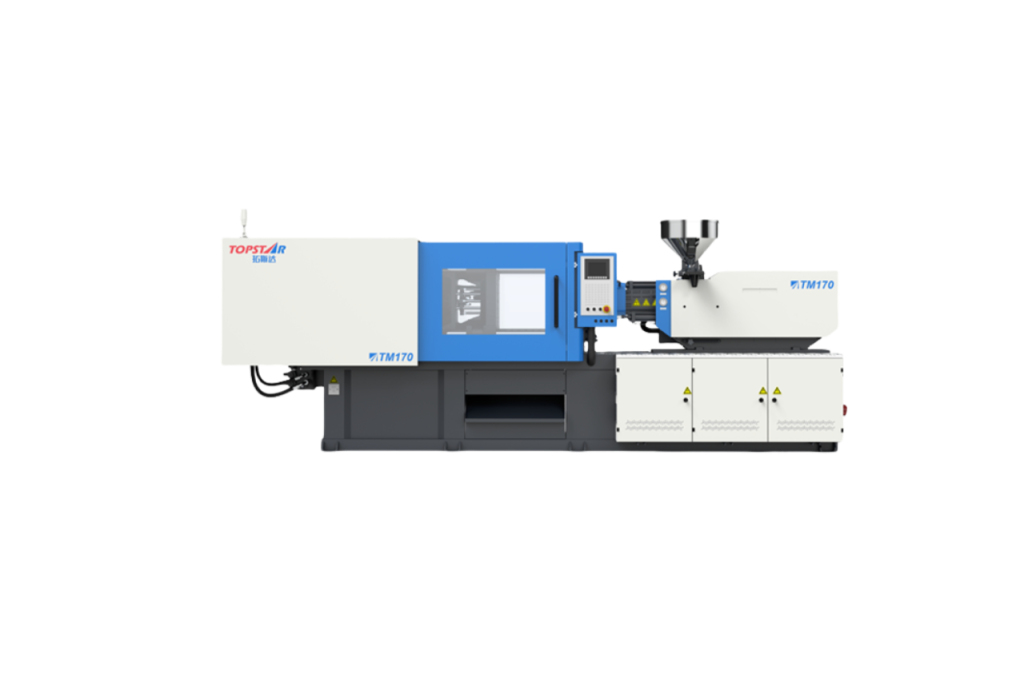
Improve safety
For manufacturers in the toy industry, the children’s toys produced must comply with strict safety regulations to ensure that they do not contain harmful chemicals, sharp edges, or small parts that may cause suffocation hazards, for some customers who have high-end production and high requirements for safety and cleanliness, electric plastic molding machines can be used for production. The “electric drive injection molding process integration” design they adopt can monitor key parameters such as temperature, pressure, and material flow in real-time to ensure that the molding process operates within a predefined safety range. The electric injection molding method is also cleaner in oil pressure, ensuring that the molded toys are pollution-free and healthier for children.
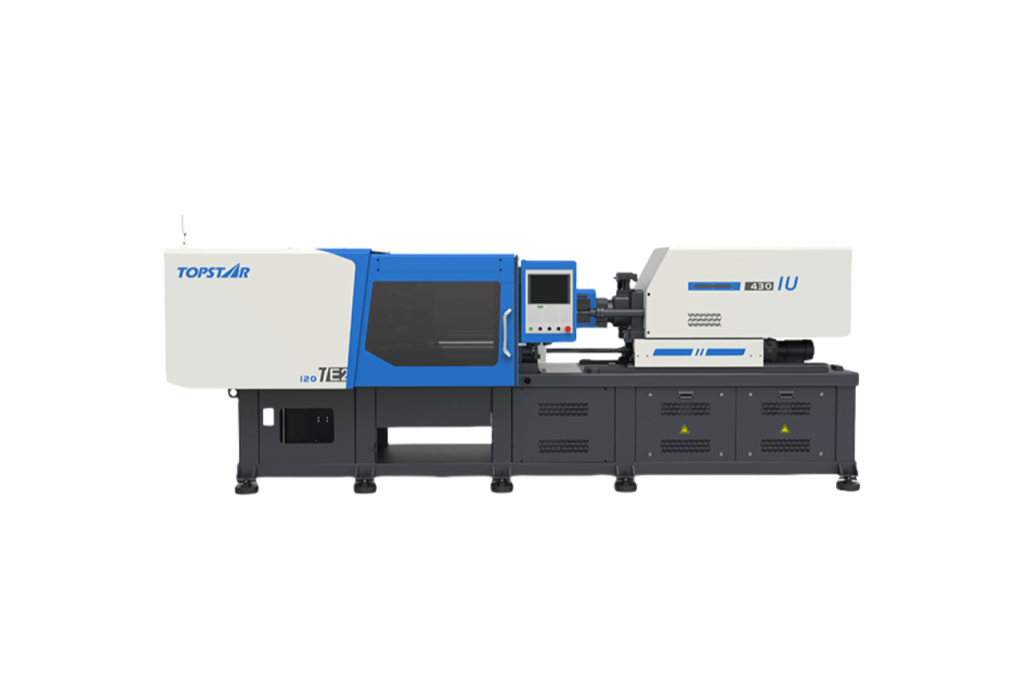
Providing plastic molding machine solutions according to your needs
At Topstar, we will provide you with plastic molding machine solutions based on the unique production requirements and problems faced by each manufacturer, making your factory more intelligent and digital. The complete product TM/TH/TE series can meet the different needs of customers. By combining a unified system language and other auxiliary equipment, you can integrate the parameter setting and working condition monitoring of all peripheral equipment into the plastic molding controller. One operator can operate multiple devices, improve injection molding efficiency, and reduce labor costs. Whether you are manufacturing plastic toys or other products, Topstar’s customized injection molding solutions can solve your problems appropriately.
Improve the quality of plastic toys with Topstar plastic molding machines.
Topstar’s plastic molding machines help plastic toy manufacturers produce high-quality, safe, and durable toys. By precisely controlling temperature, pressure, and material flow, these machines ensure consistency, reduce defects, and improve the efficiency of toy production. For high-end plastic toy manufacturers, choosing intelligent and digital injection molding solutions can directly affect product quality and competitiveness. Topstar’s molding machines not only meet the reliability, precision, and flexibility required by the toy market but also ensure that plastic toys meet safety standards and aesthetics.
TRENDING POSTS
- What factors can cause delays in the injection molding process of plastic molding machine? 2024/12/06
- Exhibition Review| Topstar participates in InterPlas Thailand 2024 2024/12/06
- Star Case | Topstar helps Santong upgrade its intelligent plant 2024/12/06
- Topstar Special | National Science and Technology Workers Day 2024/12/06
HOT TOPIC
- 3 in 1 Compact Dehumidifying Dryer
- 5-axis CNC machine
- accuracy
- Air Chillers
- all electric injection molding machine
- all electric injection molding machines
- All-electric injection molding machines
- and overall production quality. Therefore
- AP-RubberPlas
- automated injection molding machine
- Automation changed engineering
- automation of injection molding robots
- auxiliary machine
- Bench Injection Molding Machine
- Cabinet dryer manufacturers
- Cabinet dryers
- chiller
- CNC Drilling Machine
- CNC Drilling Machines
- cnc engraving machine manufacturer
- cnc laser cutting machine manufacturer
- CNC machine
- CNC Machine Center
- CNC Machine for Sale
- CNC Machine Manufacturing
- CNC Machine Tool
- CNC machine tool product
- CNC Machining Center
- CNC wood carving machine
- Cooling system
- Cross-Walking Single Axis Servo Cylinder Robot
- Cross-Walking Single-Axis Servo Cylinder Robot
- Cross-Walking Three-Axis/Five-Axis Servo Driven Robot
- cross-walking three-axis/five-axis servo-driven robot
- Dehumidifier Dryer
- Dehumidifying Dryer
- delta parallel robot
- Desktop Injection Molding Machine
- Desktop injection molding machines
- Desktop Molding Machine
- desktop plastic injection machine
- Desktop Plastic Injection Molding Machine
- direct clamp injection molding machine
- Direct clamp injection molding machines
- Dosing & mixing system
- Drilling Centers
- Drying and dehumidification system
- drying and dehumidifying equipment
- Drying and Dehumidifying System
- drying system
- effective and efficient. Cabinet dryers are also used in other industries where large quantities of material need to be dried
- efficient injection molding machine
- elbow hydraulic injection molding machines
- electric injection molding machine
- electric injection molding machines
- energy-saving injection molding machine
- etc. Among injection molding robots
- exhibition
- features of CNC machine
- Feeding And Conveying System
- Five Axis Machine Center
- Fully automatic injection molding machine
- Gathering Topstar
- giant injection molding machine
- GMU-600 5-Axis Machining Center
- Granulating & Recycling System
- Heavy duty injection molding machine
- Honeycomb rotor dehumidifier
- horizontal injection molding machine
- Horizontal Injection Molding Machines
- Horizontal Injection Moulding Machine
- Horizontal Mixer manufacturer
- How The CNC Machine Works
- hybrid injection molding machine
- hydraulic injection molding machine
- Hydraulic Injection Molding Machines
- in this article
- Industrial robot
- Industrial Robot Chinese brand
- industrial robot parts
- industrial robot supplier
- Industrial robots
- Industry Chain
- Injection Manipulator
- injection mold machines
- Injection molding
- Injection molding automation
- Injection Molding Automation Solution
- injection molding dryer
- Injection molding equipment
- injection molding hopper dryer
- Injection molding machine
- injection molding machine brand
- Injection Molding Machine Factory
- Injection Molding Machine Manufacture
- Injection molding machine manufacturer
- injection molding machine manufacturers
- Injection molding machine procurement
- injection molding machine robotic arm
- injection molding machine with a robot
- Injection molding machines
- injection molding material dehumidifying
- injection molding plant
- Injection Molding Robot
- injection molding robot arm
- Injection molding robot automation
- Injection molding robotic arm
- injection molding robots
- Injection Moulding Robots
- Injection Robot
- Injection robot arm
- Injection robot manufacturer
- Injection robot wholesale
- injection robots
- intelligent injection molding machines
- Introducing Injection Robot
- It is the best choice for drying large quantities of material at once. Cabinetmakers use these machines because they are fast
- large injection molding machine
- Learn what industrial automation and robotics is
- low speed sound-proof granulator
- machine plastic molding
- make sure to add some! Improvements (2) Keyphrase in introduction: Your keyphrase or its synonyms appear in the first paragraph of the copy
- manipulator machine
- manufacturing
- micro injection molding machine
- middle speed granulator
- Mini CNC machine manufacturers.
- Mold Temperature Control System
- mold temperature controller
- molding material Dehumidifying System
- mould temperature controller
- mould temperature controllers
- New electric injection molding machine
- nitrogen dryer manufacturer
- nitrogen dryer system manufacturer
- Oil type mold temperature controller
- open day
- Outbound links: No outbound links appear in this page. Add some! Images: No images appear on this page. Add some! Internal links: No internal links appear in this page
- PET Preform injection molding
- phone case maker machine
- phone case making machine
- plastic bottle making machine
- plastic bottle manufacturing
- plastic bucket making machine
- plastic bucket manufacturing
- Plastic chair making machine
- plastic forming equipment
- plastic hopper dryer
- plastic injection machine
- plastic injection machines
- plastic injection molding
- Plastic injection molding equipment
- Plastic injection molding machine
- Plastic Injection Molding Machines
- plastic injection robot
- Plastic Molding machine
- Plastic Molding Machines
- plastic molding press
- plastic phone case making machine
- plastic-molding machine
- powerful granulator
- Powerful Type Sound-Proof Granulator
- production of plastic seats
- Robot injection molding
- robot injection molding machine
- robot manufacturing companies
- Robotic arm for injection molding machine
- robotic injection molding machines
- robotics in injection molding
- SCARA robot
- SCARA robots
- Service-oriented manufacturing
- Servo Cylinder Robot
- servo driven robot
- Servo Driven Robots
- servo injection robots
- Servo-Driven Robot
- Setup of injection machine
- Silicone Injection Molding Machine
- six-axis industrial robot
- Stainless Hopper Dryer
- Stainless Hopper Dryers
- star club
- swing arm robot
- the choice between servo-driven robots and hydraulic robots will have a certain impact on efficiency
- the most popular injection molding machine
- the type of injection molding robot
- toggle clamp injection molding machine
- Toggle Hydraulic Injection Molding Machines
- toggle injection molding machine
- Top 10 brands of injection robots
- Topstar
- Topstar Engineering
- Topstar Industrial Robots
- Topstar injection molding intelligent
- Topstar Scara Robots
- Useful Injection molding machine
- Vertical machining centers
- volumetric type blender
- water chiller
- water chillers
- water distributor
- Water Type MoldTemperature Controller
- We often face choices when performing injection molding. We will choose the type of injection molding machine
- wholesale of injection molding machines
- x carve CNC